Compared with ordinary traditional motors, brushless DC motors have the advantages of high power density, high efficiency, and long life. Brushless DC motors have a simple structure and few components, so they are easy to maintain and have a long service life. They are now widely used in robots, automated production lines, medical equipment, automobiles and other fields.
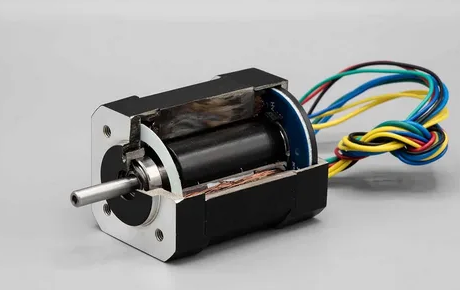
Key factors for choosing brushless DC motors:
1. Rated torque and rated current of the motor
This is one of the most basic parameters of the brushless DC motor. The rated torque and rated current of the motor can reflect the capability and performance of the motor. When selecting, the required torque and current need to be determined according to the specific usage requirements.
2. Motor speed range
Brushless DC motors generally have a wide speed range, generally ranging from a few hundred to tens of thousands of revolutions. Therefore, the speed range needs to be determined according to the specific application scenario when selecting a motor. Generally speaking, it is necessary to ensure that the torque output by the motor at the rated speed reaches the required workload when running, so as to ensure that the motor works stably and reliably.
3. Dimensions and quality of the motor
The overall size and quality are also one of the key factors in the selection of brushless DC motors, which are related to specific usage requirements and scenarios. For some scenarios that require small size and light weight, miniaturized brushless DC motors need to be selected.
4. Motor control method
There are three main control methods for brushless DC motors: Hall control, sensor out-of-step control and inductive feedback control. When selecting, you need to determine which control method to choose based on specific application scenarios and usage requirements.
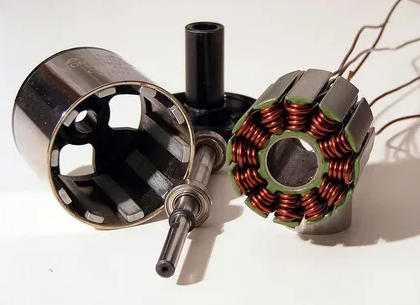
Matching motor drivers and controllers
After selecting a brushless DC motor, you also need to select a suitable motor driver and controller. Generally speaking, the brand and model of the driver and controller should be consistent with the motor to ensure system stability and reliability.
The main parameters to consider when selecting a brushless DC motor are the following:
1. Maximum torque: It can be obtained by adding the load torque, moment of inertia and friction. In addition, there are some additional factors that affect the maximum torque, such as the resistance of the air gap.
2. Square module torque: It can be approximately considered to be the continuous output torque required for practical applications, which is determined by many factors: maximum torque, load torque, moment of inertia, acceleration, deceleration and running time, etc.
3. Speed: This is the speed required by the application. The speed requirement of the motor can be determined based on the motor's speed trapezoidal curve. Usually, a 10% margin should be left in the calculation.
Discussions
Become a Hackaday.io Member
Create an account to leave a comment. Already have an account? Log In.