To conceal the rough ends of the rails, I covered them with printed end caps, which also act as belt tensioners. The belt brackets are fastened to the end caps and tightened using M3 screws. Afterwards, I fixed them to the rails with more M3 screws to take some of the stress off the caps.
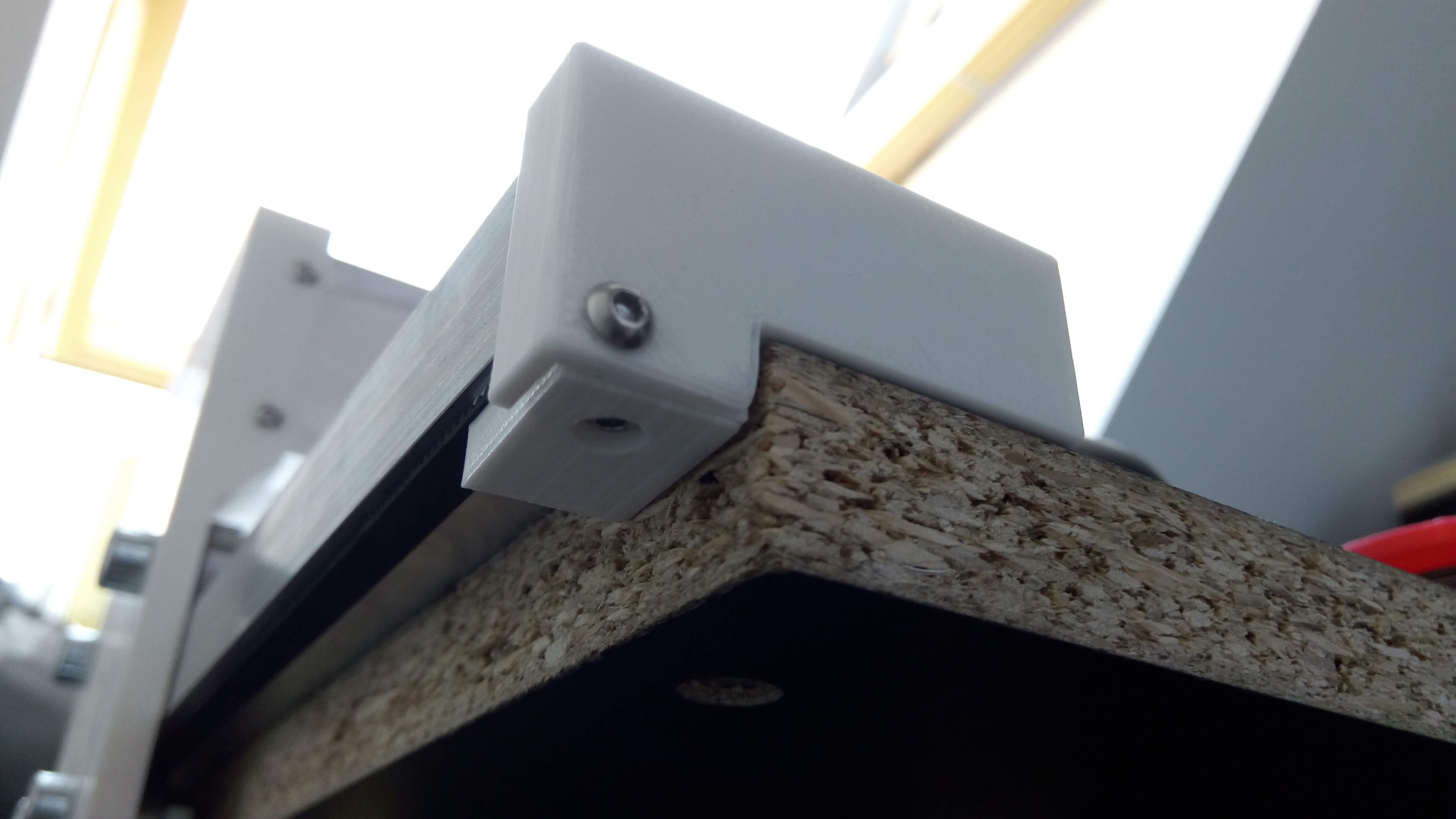
For testing, I connected the stepper motors to an Arduino CNC shield and tested out different speeds and accelerations. Sadly, the limit seems to be around 100mm/s, which is really, really slow for a PnP machine. Changing the Y axis to servo drive will be one of the first upgrades after everything else is working.
I'm already thinking about building my own BLDC servo using a standard 2212 motor with a printed encoder. If it works, it should allow the heads to move up and down fast enough. I need to continue with the head design now before going any further with this build, because the head will determine which motors I can use on the X axis.
Discussions
Become a Hackaday.io Member
Create an account to leave a comment. Already have an account? Log In.