This is not an single instrument but a concept: to produce techno - with robots! I prodiced electronic music for many years with computers and synths. But I realized that something was missing: being a classically trained clarinetist, I needed some physical context. I still wanted the repetitive character of techno: Born was the idea of Techno Music Robots!
"Each sound is played by robots. Small motors beat on metal, 3D-printed robo-kalimbas vibrate with deep bass sounds, salvaged parts from old hard drives click and cut. Over several years Moritz Simon Geist committed to build, tweak, test and play all of his DIY robotic instruments.
Geist’s ‘Sonic Robots’ push the boundaries of the imaginable and invent a new plurality in music creation. In electronic music, many imagine humans playing machines. Few imagined these music machines being actual robots. In 2012, Geist ventured into this exploration with the invention of his well-known oversized 808 robot. The MR-808 robot is an iconic drum machine gone physical, no longer dwelling in the confines of circuitry alone. In the form of a 4 by 2 meter music box, filled with mechanical parts which play the instruments live, a new idea in electro and human-machine interaction was born. Now, he goes even further to pioneer the unknown and futuristic sound world of ‘Robotic Electronic Music’.
In this quest, Geist teamed up with the Berliner sound alchemists ‘Mouse On Mars ‘ to dig deep into the history of mechanical music and experiments of early electronic music. What Moritz Simon Geist came up with is a stunning record of what is possible today – to explore the sound of mechanics that continually describe our world. Geist creates a smashing soundtrack for both the precise automation and physical fragility that shapes today‘s society."
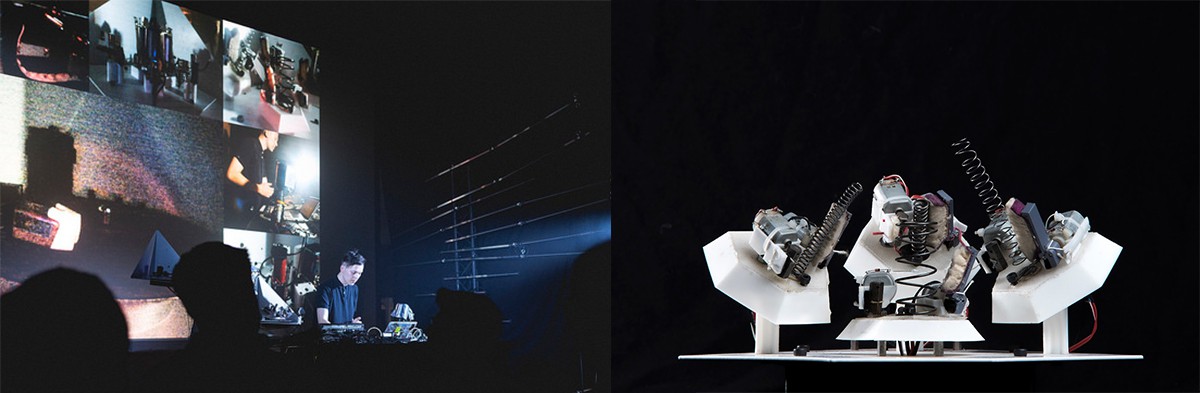
I am just about to release my first debut album with help from Mouse On Mars, Kompakt and many many other wonderful people. Its the worlds first techno record made only with robot! You can find it here
That is way cool :-D