Funny how things seem to come together all at once. I hadn't worked on this in a while, but today I got it to my desired endpoint.
Solder problem solved:
Worthington Liquid stainless steel flux- contains ammonium bifluoride and hydrocloric acid and zinc chloride. Nasty stuff but can not argue with the results. The 96/4 Sn/Ag solder sealed the deal.
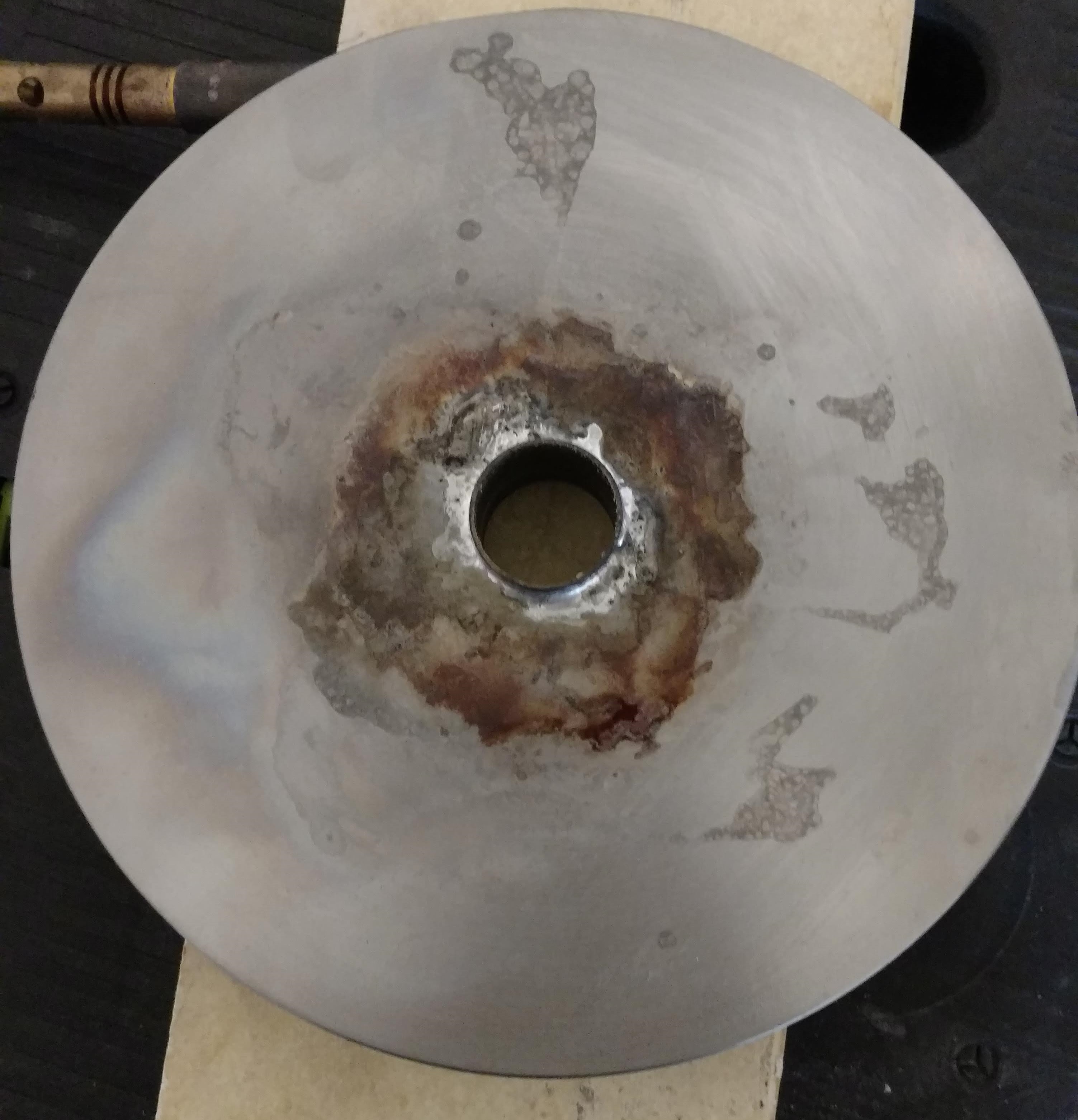
After I Cleaned it up with barkeepers friend and a paper towel.
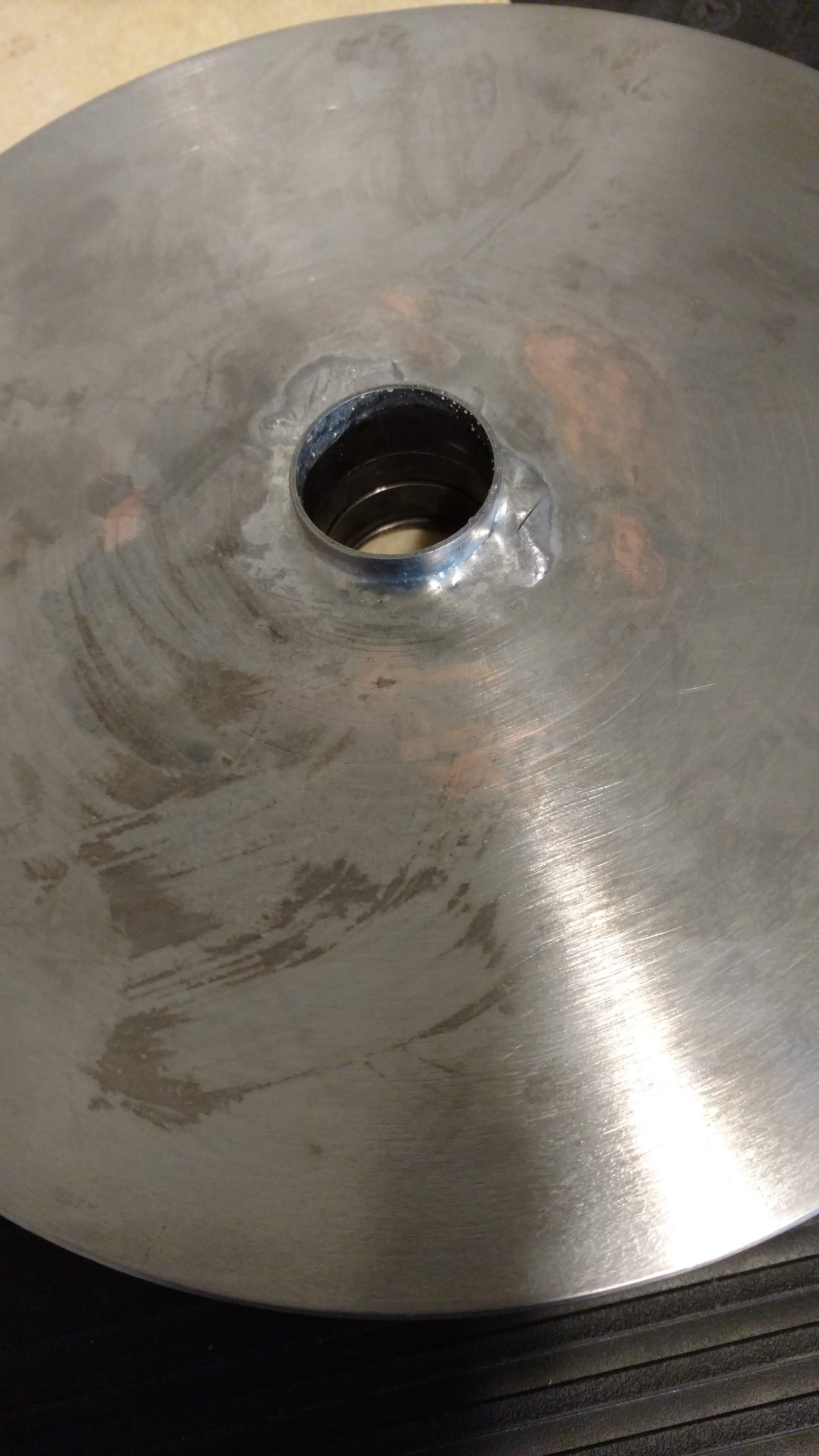
With that done I turn to the glass chamber.
With high vacuum there is a massive danger using glass, due to implosion. Make sure to have a safety cover to place around your chamber.I recommend poly-carbonate. I annealed my broken piece at 560 degrees C for 2 hours. Then I cut it on the diamond saw. The piece was massive so i clamped a marker to my table and rotated the piece gently in saw blade. After that I ground the ends flat with 120 grit carborundum. I used a lapping wheel., But this can be done on flat plate glass. Be sure to rotate to keep even pressure. To check to see if there is a good sealing surface, take a piece of plate glass and wet it. Then place it over the edge of the tube. You will be able to see if there are any gaps in the sealing surface. Here is the finished piece. You can see that the edge is smooth, but the corners are sharp.
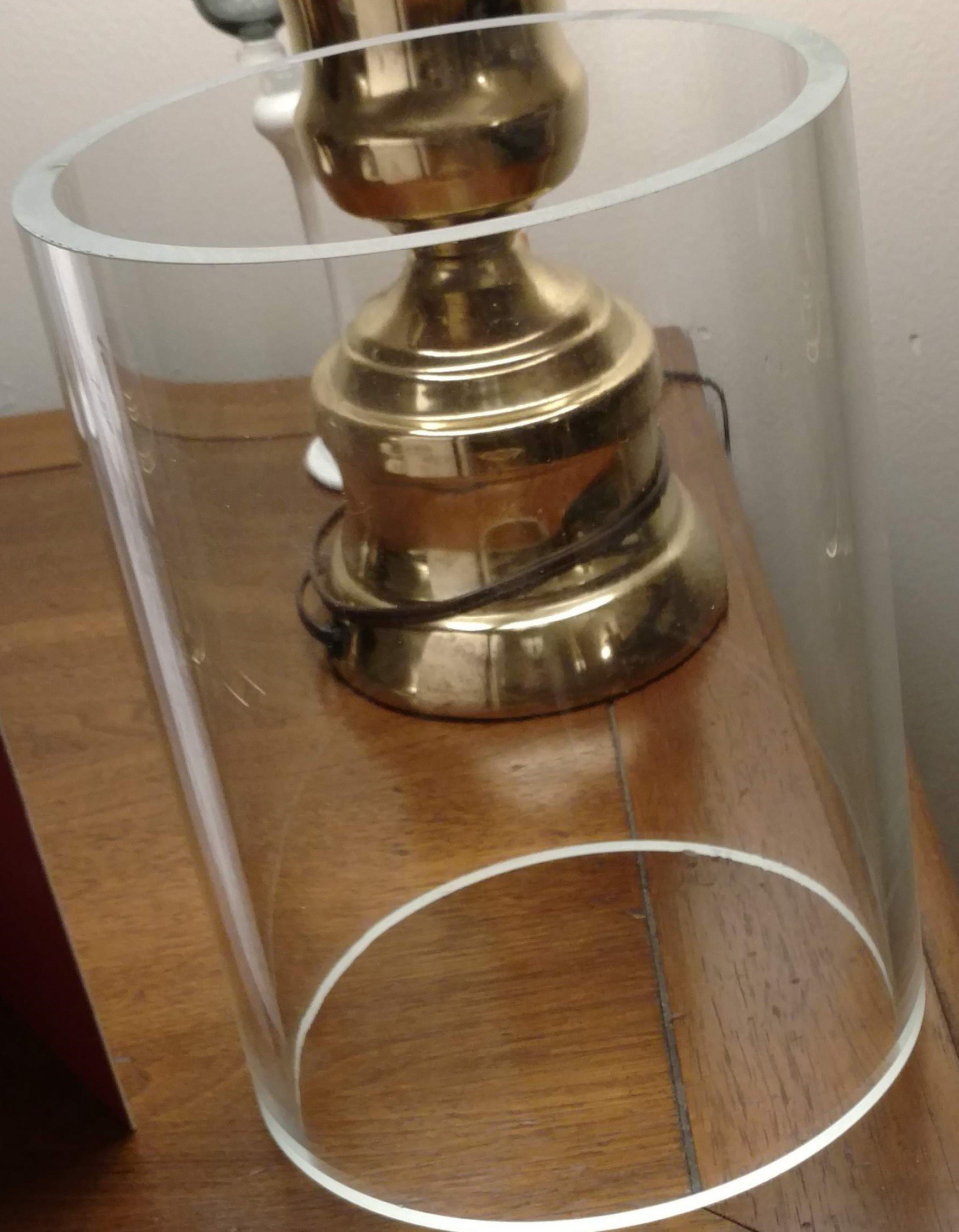
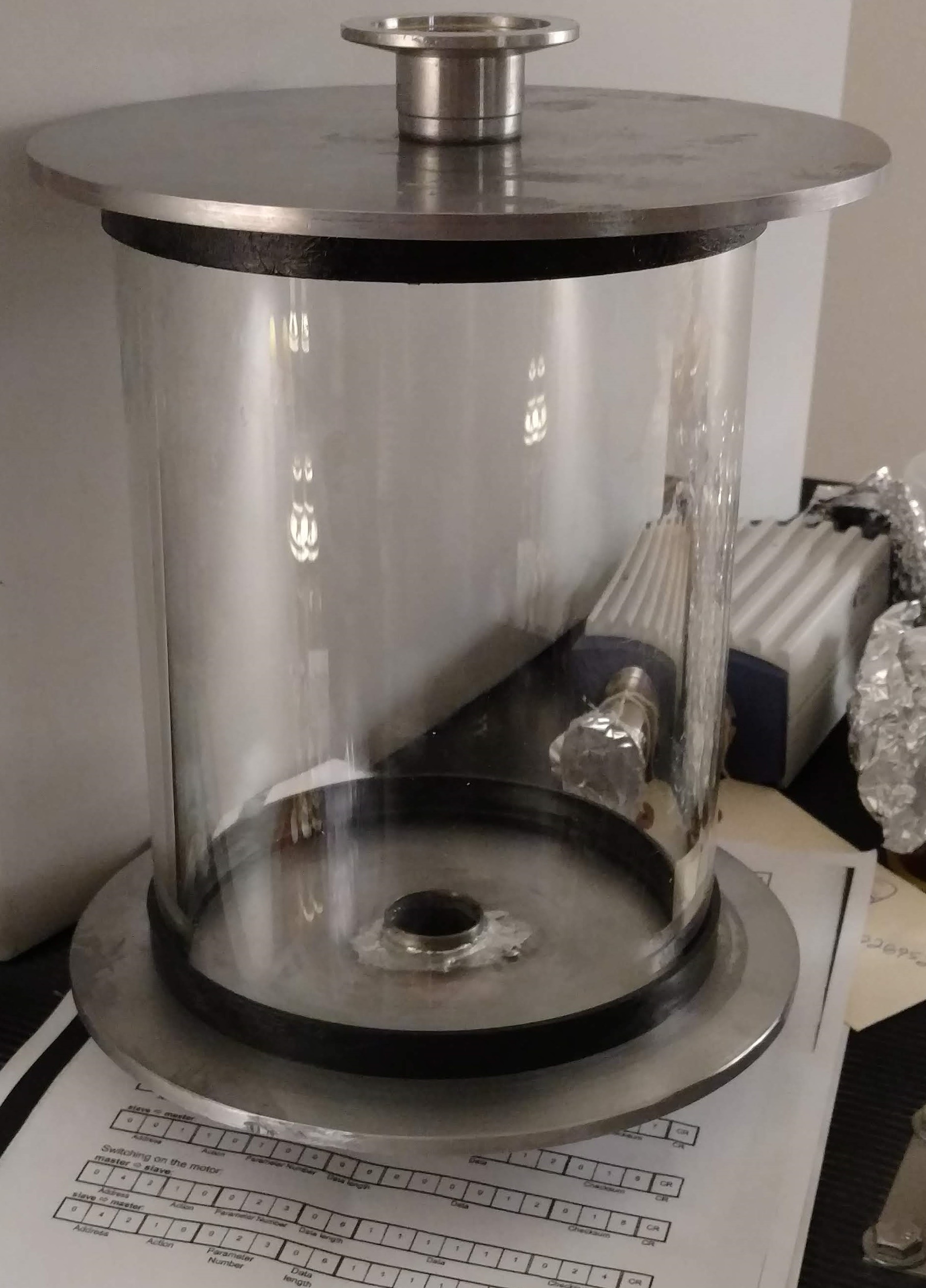
Discussions
Become a Hackaday.io Member
Create an account to leave a comment. Already have an account? Log In.