While measuring the collets for the collet box build I had this silly idea; why not attempt to measure them as accurately as possible, and then make a 3d printed blank "emergency" collet? Plastic collet blanks are available so this is not a totally insane idea.
I measured the critical dimensions as best as I could with my calipers and put it in a FreeCAD model (dimensions in mm)
The dimension I'm the most unsure about is the included angle of the taper, it does look symmetrical, and it does seem to be 41 degrees, but it is hard to measure accurately with my current tooling. I 3D printed a few copies of that model in PETG and tried it out on the spindle.
It seemed to fit fairly well. If you're wondering what those green dots are, they are pins made of 3mm filament (ABS I think) inside some recesses I modeled in the collet "jaws" to prop them open for machining, otherwise they would be collapsed by the nut and not be able to close any more than the machined dimension when in use.
Then I did a quick test with a drill and 6mm reamer. It would have been better if I had actually bored the hole instead of reaming, as the reamer can wiggle and not make a perfectly concentric hole, but I didn't have the right boring bar at the time.
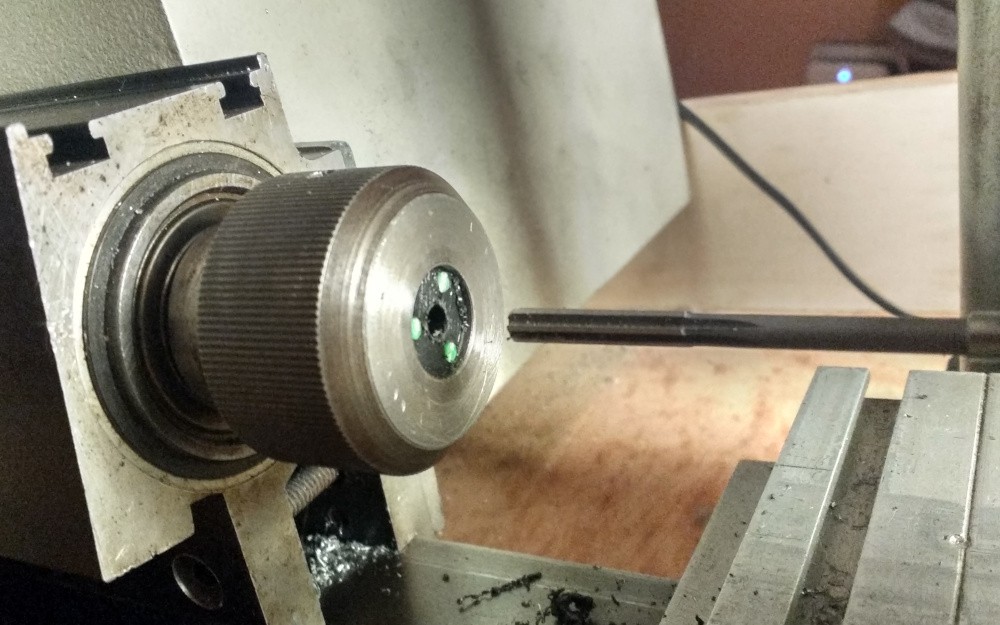
I tried chucking some 6mm bar stock and the reamer itself with it and it has more than acceptable gripping force, whatever is secured with it will not rotate inside the collet with light cutting forces. A quick test with an indicator showed about 0.1-0.15mm (4-6 thou) of TIR which is about 10x higher than a decent collet should be, but it could still be handy for gripping an odd sized drill bit or stock when a regular chuck would be too bulky.
I'm also printing a set in Nylon with a much higher quality printer to do more testing, and also attempt to bore the hole out more accurately. I also plan to confirm the angle as soon as I figure out how to measure it accurately....
Discussions
Become a Hackaday.io Member
Create an account to leave a comment. Already have an account? Log In.