We've talked about how DC Injection will play a large role in this product but we haven't yet talked about how we'll actually make that DC. We're all used to thinking about a DC Power Supply as a trivial purchase or design, but this is something altogether different. The driving factor that makes this different is our gargantuan power requirements. We're designing our product to work with grinders motors up to 1HP so let's start by looking at the specs for a 1HP induction motor at 120V (based on NEMA MG-1):
- Full Load Current: 11 A (1.3 kW)
- Locked Rotor Current: up to 80 Amps (9.6 kW)
When a motor starts, the initial current hits locked-rotor-current for an instant then settles into a startup current roughly four times it's full load current. That means a 1HP grinder coming up to synchronous speed will draw 44A (5.2 kW) for a few seconds. Just as that 5.2 kW decelerated the motor from stopped to synchronous speed, we'll need roughly the same amount of power to decelerate it from synchronous speed to stopped. That's a ton of juice. For some perspective, a commercially available 5kW DC power supply costs nearly a thousand dollars and measures 17"x7"x6" and weighs over 30 lbs. Our entire product (of which DC supply is only a part) should measure less than 5"x5"x2", weight less than 1 lb, and cost less than $100.
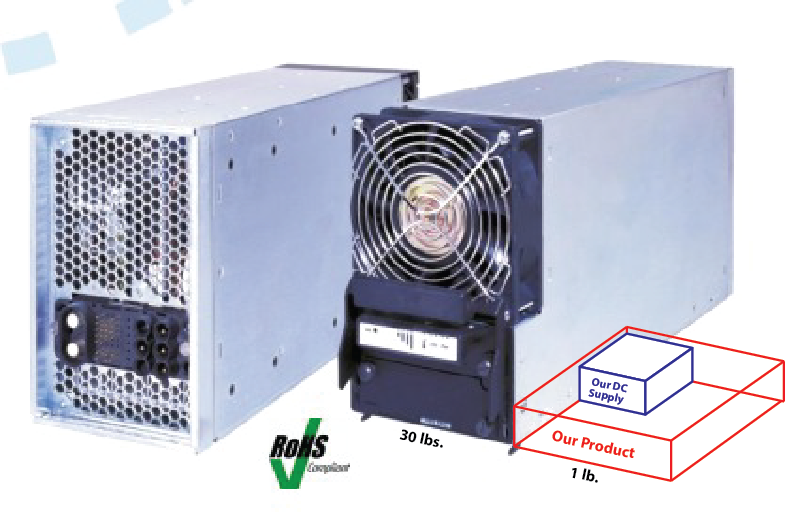
And we haven't even begun to talk about DC output voltage. Most commercially available supplies max out around 24V but we need up to 90V DC to source enough power into the relatively high impedance windings of an induction motor. Wowzers. Now you see why this project is so ambitious. But don't worry, we have some tricks up our sleeve. More soon!
Discussions
Become a Hackaday.io Member
Create an account to leave a comment. Already have an account? Log In.