Today was all focused on testing out the braking effects of a pulsed rectified sine wave on a motor. But to do such a test, we needed a circuit which would be able to switch fully rectified mains at a frequency several times higher than 60Hz. Our first circuit was composed of a power MOSFET for switching the power on and off, a bridge rectifier to give us a full wave rectification of AC power, an Arduino to give us a cheap and easily configured square wave, and an optocoupler to protect the Arduino from accidents. We used a bar-style 50 ohm resistor for the load to just start testing, to be replaced with the grinder once the circuit was doing the basics correctly.
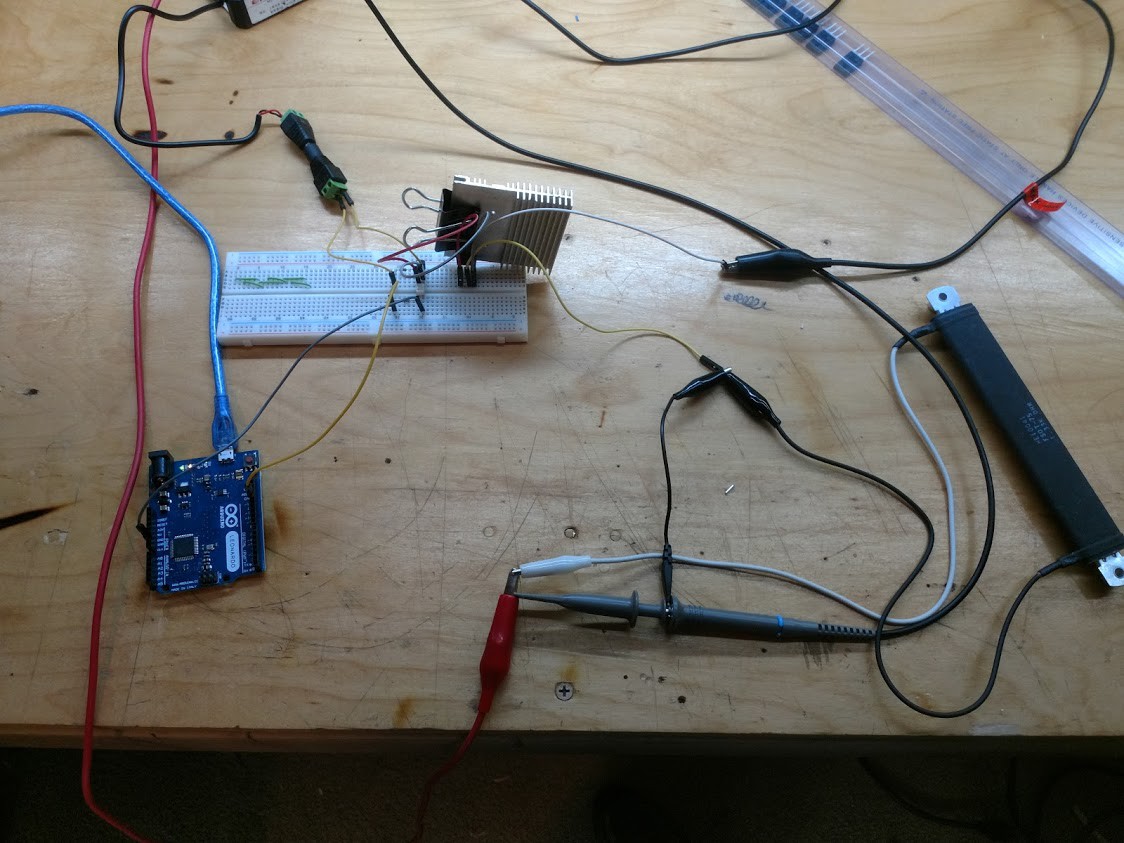
We configured the Arduino to produce a roughly 500Hz square wave with 50% duty cycle, and kicked on the power. Our first test went off without issue, producing a very nicely chopped up sine wave, and a little heat from the resistor.
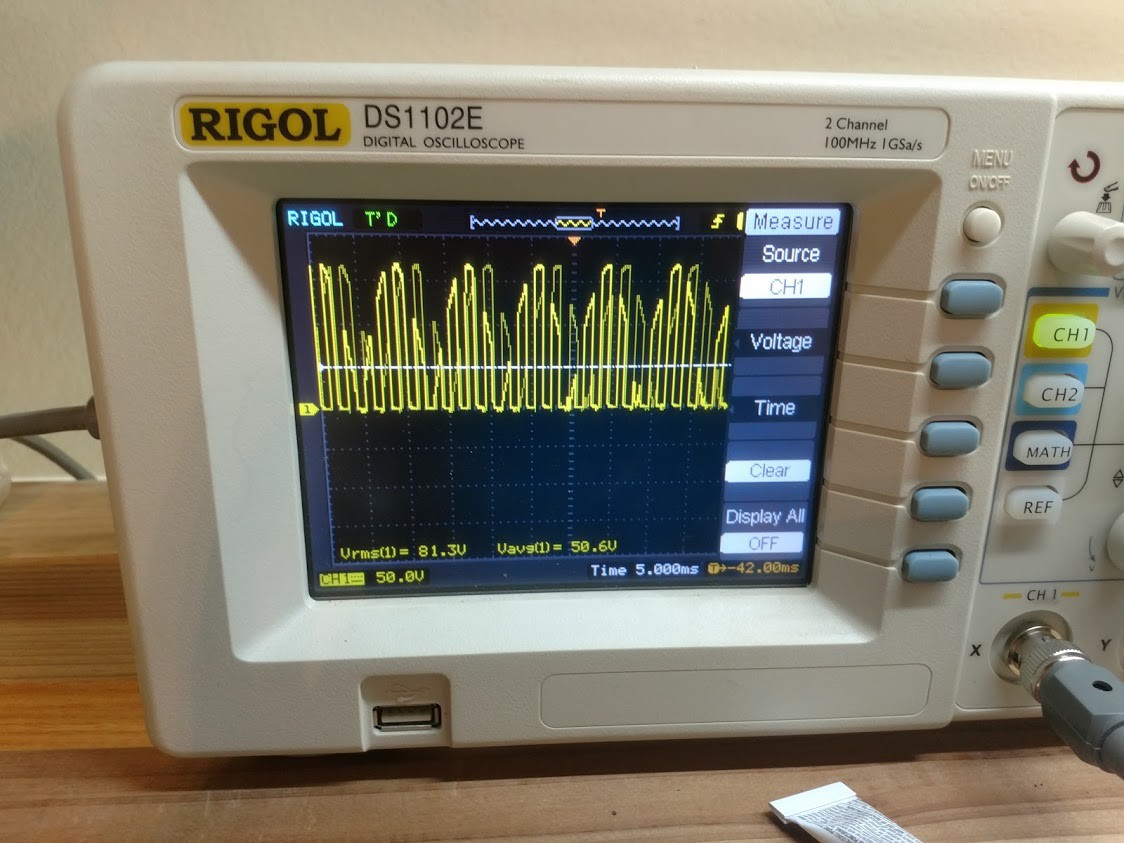
We wanted our later motor tests to have a wider envelope in terms of tested frequencies (upwards of 5kHz), so we configured the arduino to send out a faster signal. At this point, we just started seeing the fully rectified wave from the rectifier. We tested to ensure the optocoupler hadn't failed closed, and found no fault. Then we double checked it's timing limitations. Unfortunately, the time to turn on was ~10μs, while the time to turn off was ~50μs, which gives us a frequency limitation of 1.6kHz. So, we thought hard about the actual need of the optocoupler, and decided to do without it.
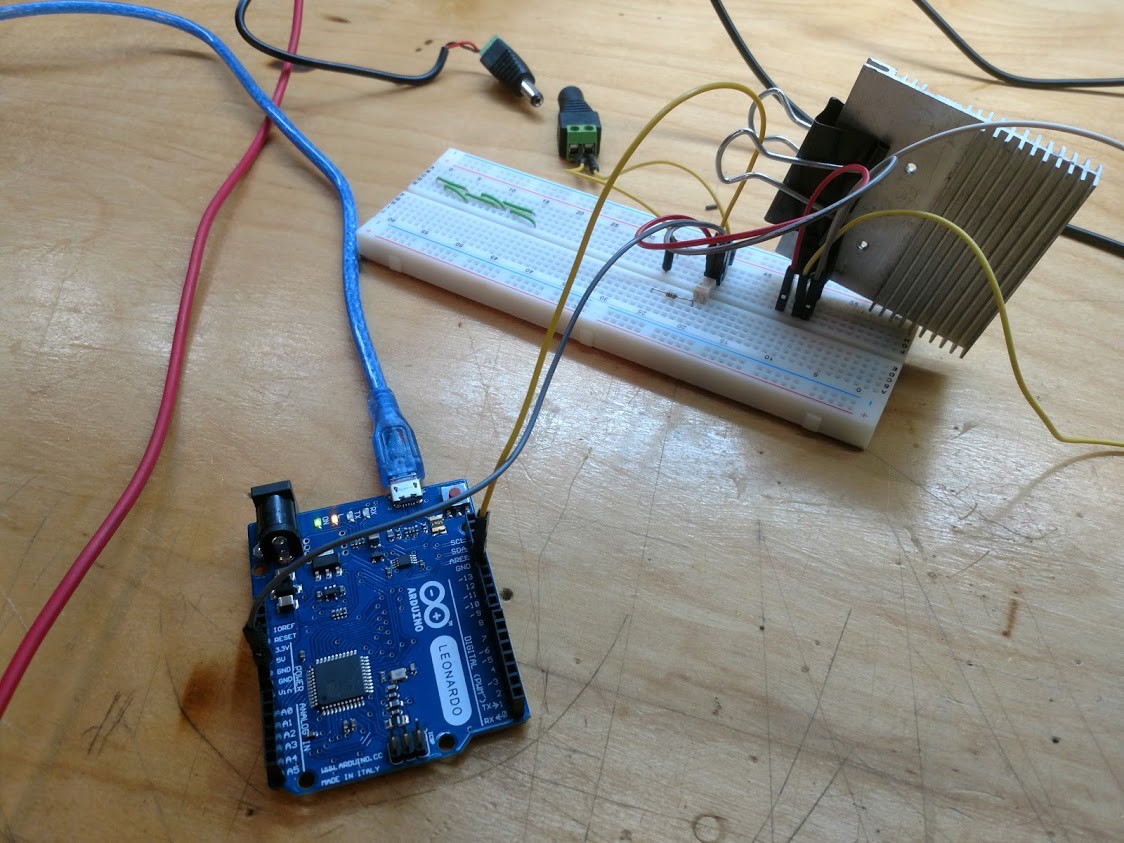
Having bypassed the optocoupler, we ran the test again, and sure enough, we landed a very nice higher frequency chopping of the sine wave.
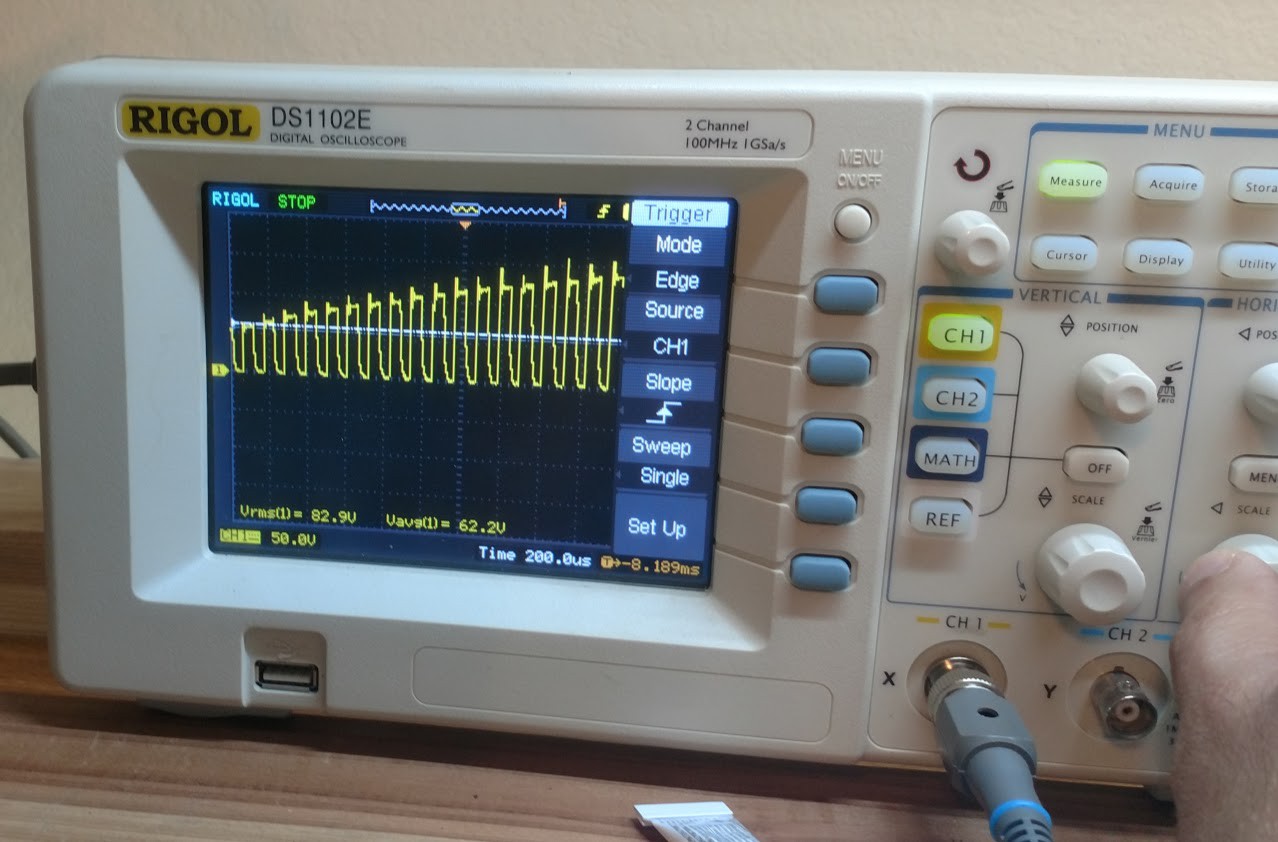
With our basic test completed, it was time to hook up the Grinder and see what happened.
It actually worked quite nicely, altogether. Sure, we had a lot of inductive kickback whenever we turned the MOSFET back off, and the flywheel diode we had got a little toasty from dropping that current on it's return trip, but altogether, it was at step in the right direction. This is where we started having a few issues.
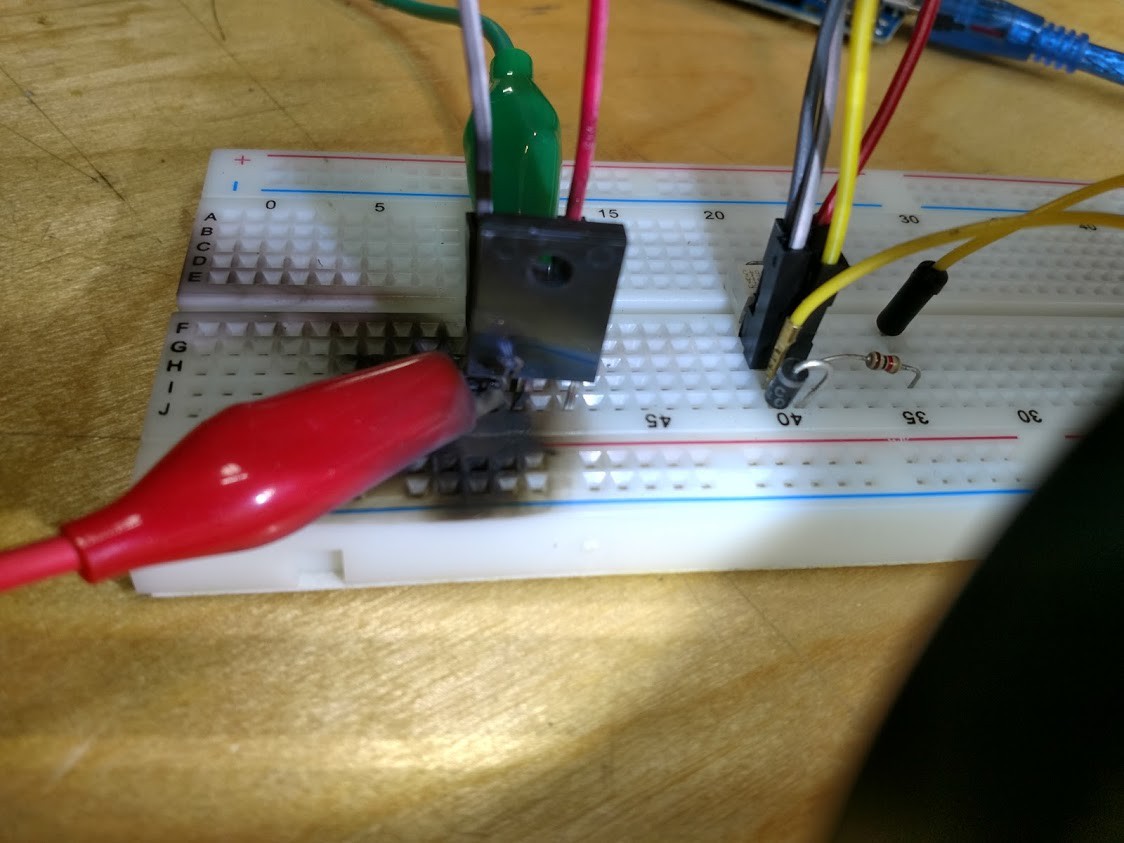
To start, our flywheel diode broke down from heat on the second test. We were treated to some arcing and charred breadboard before we shut it back down. We found that the diode, the mosfet, and the Arduino were shot (Blew the cap right off the FTDI chip). We replaced the smoked parts, went to a larger protection diode, added a optocoupler with a faster response time, and directly soldered the connections to the pins of the MOSFET.
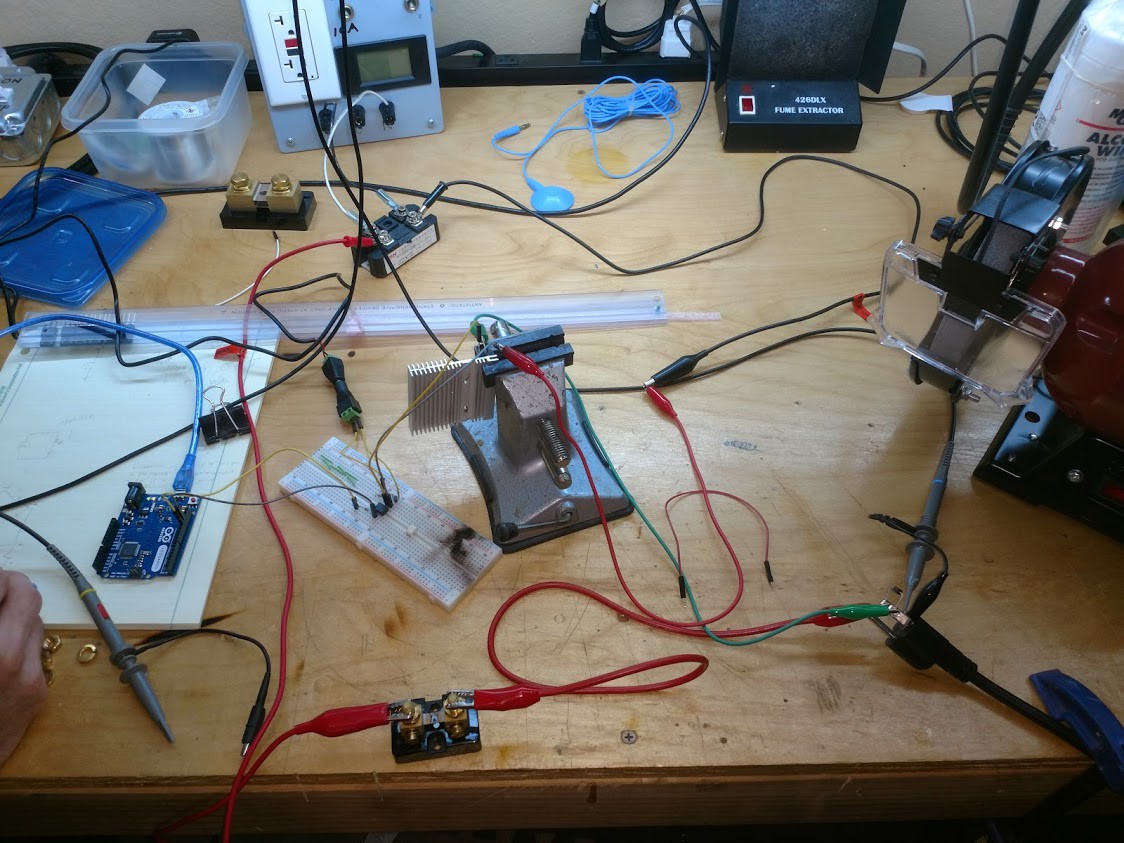
Again ready to proceed, we kicked on the power, and immediately blew the MOSFET and charred the heck out of the pulldown resistor on the MOSFET gate. Whoops.
Discussions
Become a Hackaday.io Member
Create an account to leave a comment. Already have an account? Log In.