[Update 2022-07-05: Replaced older 3-reference/4-voltage design with newer single reference/3-voltage design.
Why am I doing this?:
I'm waiting for delivery of my Keysight 34461A 6.5-digit digital multimeter (DMM). I got to thinking that this would be the perfect time to build a precision voltage reference to check the DMM for parameter drift. This is a bit daunting. The voltage accuracy of the meter is specified as:
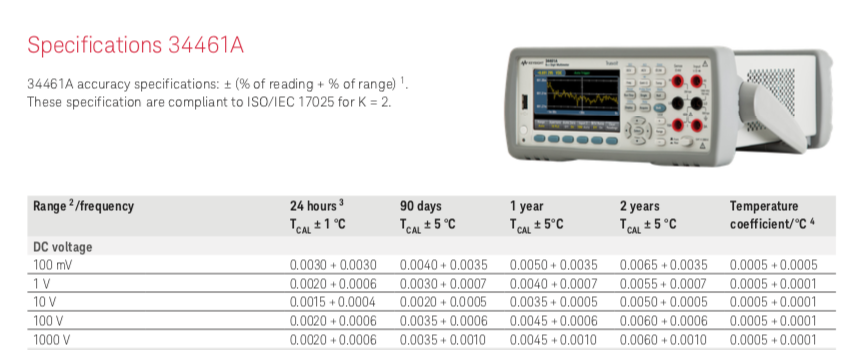
After 1 year the meter should measure a 100mV reference with an error of less than ±8.5µV, 1V±47µV and 10V±1mV. The real question is which is correct -- the meter or the reference?
Wandering through the reference wilderness:
There is a lot of passion about this subject. The absolute best ever reference is a Josephson Voltage Standard, but expect to pay ~$300k for one.
The next best thing is a heated buried zener diode, ala LTZ1000. This voltage output of the diode can hardly be called a reference since it is usually somewhere around 7.1 V. You don’t build one of these for accuracy. Its claim to fame is low temperature drift and incredible stability (i.e. it doesn’t change much with time). But the LTZ1000 is a bit pricey as well — around $60 just for the hermetically sealed metal can that encloses it. And the surrounding circuitry is a nightmare of concern. Not for me with just my lowly 6.5-digit DMM.
After you discard the top two, you’re left with a bazillion choices in a more reasonable price range: $1-$12. The problem is to choose wisely. In order to do that I had to decide what is important for my purposes. Here’s a list of primary specifications:
- Temperature drift. How much is too much? The other factor is how does the drift change when the reference voltage is trimmed, which I intend to to. Really good drift is 1ppm/C, but you pay dearly for it. <10ppm/C is pretty common and cheaper. I figure that the temperature in my shop varies from 50°F (10°C) in winter to not more than 80°F (27°C) in summer, for a total range of 17°C. That’s not a lot, but with 10ppm/C drift the voltages vary 0.017%, or 1.7mV @10V. That’s a bit more than desired.
- Stability (or Aging). This is the biggy. The lower the better. Specifications range from 10ppm/1000hrs to 100ppm/1000hrs. No design tricks to fix this.
- Noise. This is a big deal if you are designing a reference for a data converter (ADC or DAC), but I think this doesn’t matter in this application because the DMM filters the input and averages many readings to obtain a good result. Any noise above 1 Hz should disappear.
- Line regulation. All of the specs are pretty good: usually < 5ppm/V. This translates to an output variation of 5µV of change at the output for every 1V change on the supply.
- Load regulation. Usually in the range of 10-30 ppm/mA. Doesn’t matter. The 34461A has a highZ input that puts a negligible load on the reference output. Even the 10MegΩ input resistance of a lower grade DMM won’t be of any significance.
Other Stuff to Worry About:
- Temperature effects on the other components can destroy the integrity of the reference. Temperature drift of discrete resistors is not guaranteed to match. Discrete resistor tolerances below 0.1% get very expensive, along with tempcos less than 10ppm/C.
- Using an amplifier to generate a separate reference, either higher or lower in value, incurs offset errors and offset drift, resistor matching tolerances and drift. Also possible loading effects on the reference source.
- Thermoelectric noise in electrical connections of dissimilar metals. This is caused by temperature differentials between circuit connections that generate small voltages. The trick is to use metals (like gold) that don't tend to generate much potential, or keep the temperature of the entire circuit the same value.
- Kelvin connection at important junctions to prevent unwanted errors induced into circuit traces.
- I'm sure I'll be adding to this list as the design progresses.
My Bright Idea:
After...
Read more »
Hi. How type of PCB surface was used? HASL or ENIG? You finally used 2oz copper?