What I have Learned
Okay, I have not built anything yet but here are some observations:
- Although the path is longer it was good to start with what can be cut with a laser cutter (2D) and then regroup the layers for a CNC milling (2.5D). Keeping both options open gives flexibility.
- I would question building an open races when similar dimension roller bearings are available of a very reasonable price?
- It it probably easier to match the bearing thickness to the sheet thickness than not.
- In my designs I have both dowel (i.e. 1.25 mm diameter nails) alignment and bolt alignment. If the layers are glued, then the dowels can be removed).
- Permanent dowels and split dowels are an option where disassemble is not required.
- For wood (MDF) PVA glue is fine, for acrylic #16 acrylic glue is fine (but use safety precautions as it contains very nasty chemicals (methyl chloride)).
- Full thread bolts are available in lengths up to about 80 mm and studs even longer. I am no longer relying on the bolts for alignment.
- Not hard to design steps to use allow the use of shorter bolts or the use a mix of bolts, glued lamination and permanent dowels.
- There is a trade off between thicker sheets and manufacturing. It is not easy to cut thick sheets (i.e. greater than 12 mm). It may be better to laminate (glue) sheets (i.e. 6 mm) for thicker sheets.
- The size of my CNC machine limit the size of my project.
- Although expensive, commercial laser cutting services can cut pieces beyond the size limits of my CNC machine.
Some slew ring design concepts using roller bearings.
Double open race #1:
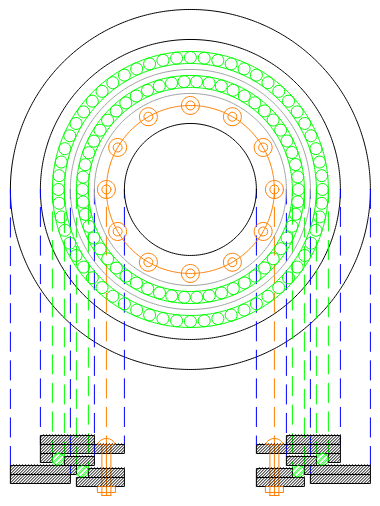
Double open race #2:
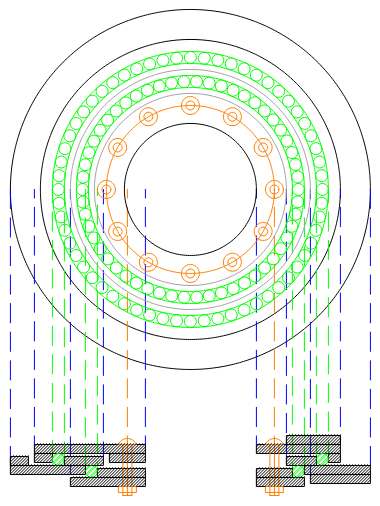
Single roller bearing #1:
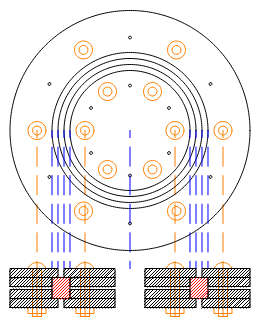
A double roller bearing (with gaskets) #4
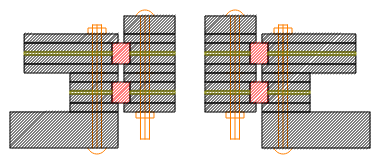
If the roller bearing thickness matches the sheet thickness then a single roller bearing design #5:
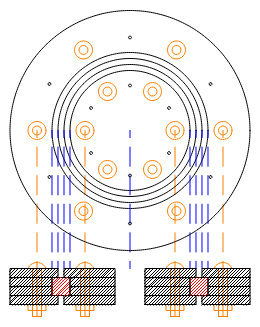
An finally a 2.5D CNC double version of #5:
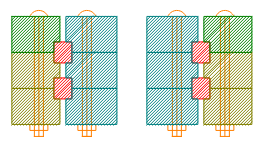
Looking at #6 I wish I could just weld a flange with holes on the inside and outside of the roller bearing.
Anyway, I think I should build a couple to see what they are like in practice.
Here is the 2.5D CNC layout of design #1 but with gaskets:
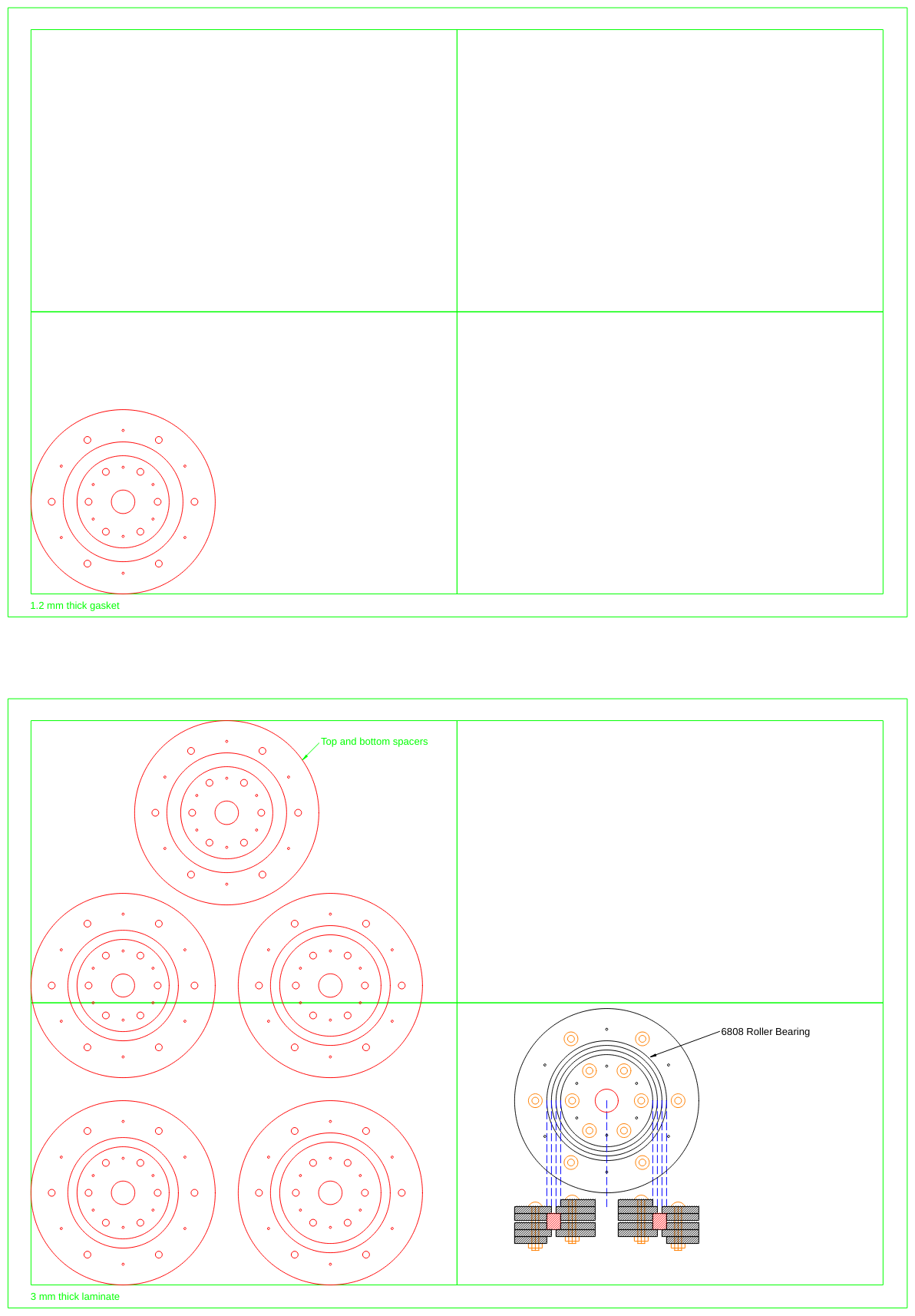
AlanX
Discussions
Become a Hackaday.io Member
Create an account to leave a comment. Already have an account? Log In.