Abstract
We propose an automated guided vehicle (AGV)-based logistics transportation robot with a fork-type manipulator that are efficient in delivering various and small goods on the shelf. The proposed robot system can be divided into a main server part, a drive control part, and a fork lifter motion control part. The main server part includes the path and task planning algorithm, a communication system for exchanging information, and a database. The drive control part performs navigation control and position recognition through the camera. The fork lifter motion control part contains a control algorithm for transporting the product and basket on the shelf. To evaluate the performance of the proposed transportation robot system, the driving test was performed and a fork lifter working experiment was carried out. The experimental results show that the performance of the proposed robot system is satisfactory and can be applied to the transportation tasks in the distribution centers. Keywords: Logistics transportation robot, Fork-type manipulator, Fork lifter, Position recognition.
Introduction
As the proportion of logistics costs gradually increases, various logistics technologies are being developed to obtain price competitiveness of products through reduction of logistics costs. Especially, due to the successful commercialization of logistics transportation robots such as Amazon’s Kiva System, technology development of logistics robots has attracted great interest. Also, the element technology and robot system that can be applied to various logistics fields are being studied. Many companies are adopting various automation and information systems to increase profits and logistics efficiency.
2. Design of Transportation Robot System
2.1 Design of Transportation Mobile Robot
The transportation robot applied to the logistics center needs driving technology, localization technology and task process technology. Driving technology is to safely transport the objects Table 1. Specification of the transportation robot Contents Values (mm) Width of robot’s frame (d) 600.0 Length of robot’s frame (L) 700.0 Radius of steerable wheel 24.4 Radius of active wheel (R) 50.0 Height of lifter’s frame 1596.0 Length of lifter’s frame 300.0 Width of fork-type element 196.0 Length of fork-type element 503.5 to a target location. The location recognition is required for driving and collision avoidance in the dynamic environment where several robots are operating. The task processing technique is to deliver products to an operator using a pallet, a shelf, or a rack, and the behavior of the robots varies depending on the tasks. The most important consideration in the design of these robots is the internal environment of the logistics center and the type of operation. Logistics transportation robots that perform diverse and precise tasks increase their development costs accordingly.
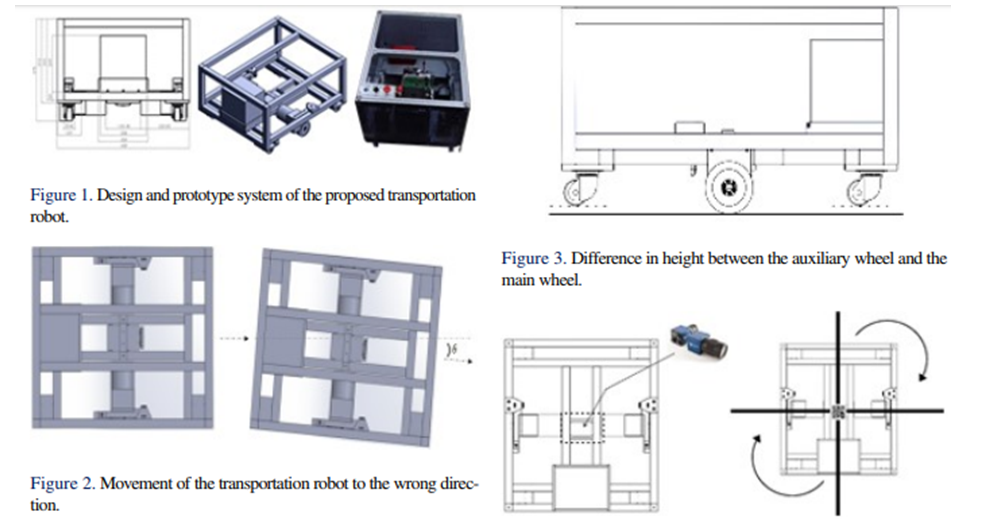
2.3 Design of the Embedded Control System
The control system of the proposed robot can be divided into a main server, a drive controller, and a forklift motion controller as shown in Figure 8. The main server plans the path of the individual transportation robots and the task schedule of the fork lifter. The information’s of paths and schedules are delivered to the robots via Wi-Fi communication. The information of completed tasks are received and stored in the server’s database. Based on the information of the stored database, it continuously calculates the path of the individual transportation robots, and transmits updated path and work plans to the logistics transportation robot in real time. The drive controller controls the drive motor to travel along the correct path to perform straight run and change of direction. The position information of the QR code is acquired through the camera at the robot. The current position is calculated through the image processing algorithm of Raspberry Pi-3 and the motor is controlled according to the path error. The forklift motion controller removes the shelf from the specified shelf support using a fork according to the task schedule and then moves it to the specified position. The sensors for the control use a camera for position recognition, a gyro sensor for direction recognition, and an ultrasonic sensor for obstacle detection. Figure 9 shows the software functions of the embedded controller. The control board shown in Figure 10 was manufactured for control of the transportation robot. The main CPU uses the ELB-REV4 iSCADA and is connected to the motor driver using relays to prevent reverse voltage. The Bluetooth module for shutdown and passive mode test is connected via UART communication to allow remote control by wireless communication and has IMU sensor for correction of rotation or path tracking error. Also, it relates to the acceleration sensor through SPI communication to acquire the attitude information of the robot. The battery uses a 24 V battery. The BLDC motors are individually controlled through the driver.
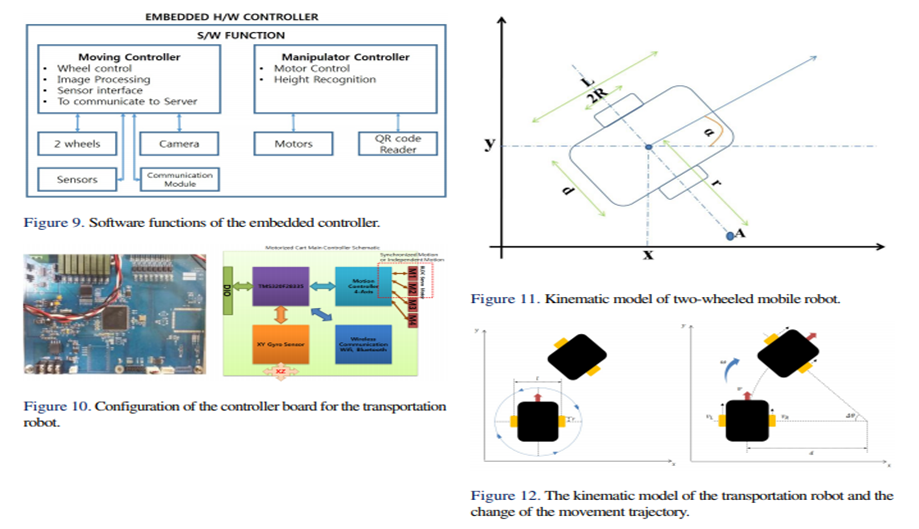
3. Control and Operation System of the Robot
3.1 Kinematic Model of the Mobile Robot
The kinematic model for the driving control of a mobile robot with two wheels is shown in Figure 11 [5–8]. If the non-slipping condition is satisfied to simplify the kinematic model of the robot, the velocity equation of the mobile robot is expressed by Eq. (1)
v = VL + VR 2 = (wL + wR)r 2 ,
w = VR − VL l = (wR − wL)r l ,
where l is the distance between the centers of two wheels, r is the radius of the wheel, v is the linear velocity of the robot, w is the angular velocity of the robot, VL and VR are the linear velocities of the two wheels, wL and wR are the angular velocities of the two wheel.
Figure 12 shows the kinematic model of the transportation robot and the change of the movement trajectory. d is the radius of the circle generated when the robot moves along the radius of rotation, and SL and SR are the movement distances of each wheel for a given time, then the proportional formula according to the movement trajectory can be obtained as shown in Eq. (2). Here, if the angle of the arc drawn by the robot is ∆θ and the moving distance of the center of the robot is S, ∆θ and S are shown in Eq. (3).
SR : d + l 2 = SL : d − l 2 , (2)
∆θ = SR − SL l , S = SR + SL 2 . (3)
3.2 Control Algorithm for the Robot
The main server calculates the route, plan tasks and transmits them to the robot through communication. Based on the transmitted path information, the robot starts to travel and transmits the QR code information of the floor surface to the main server in real time. At each QR code point, a drive controller controls the motor using a PID controller as shown in Figure 13. When power is applied to the main controller, the register is initialized for operation and the controller performs communication initialization using the GPIO. The mode is set in the RX buffer by SCI communication, and it is driven according to the speed and acceleration value of the user initial setting. These values can be calculated and empirically selected according to the user. If the speed and acceleration values are selected, the yaw value of the gyro sensor is processed and displayed. The controller performs forward and reverse in accordance with the angle change of the yaw value and continuously controls by using the PID control. In addition, the controller switches the direction of left and right based on 90 degrees and performs acceleration and deceleration control for precise direction switching. Figure 14 shows the flowchart of the overall driving mode of the transportation robot. The controller has a separate PID controller according to the mode and the PID gain values were empirically tuned.
3.3 Task Planning of the Transportation Robot
The main server plans the path and tasks of the transportation robot. The main server has the location information of the goods including the position of the shelf using the database. Therefore, the main server transmits the optimal driving path and the task sequences of each fork lifter to the transportation robot in order to process the order. The task plan is processed in the fork lifter controller when the robot is completed to reach the target shelf. As shown in Figure 15, the fork lifter controller takes out the basket based on the position information of the Figure 14. Flowchart of the robot control mode. Figure 15. Movement of a basket using a fork lifter of a transportation robot. shelves and delivers the basket to the operator or returns the basket to the work place. The height of each layer can be known through the sensors installed in each layer.
5. Conclusion
In this paper, an efficient logistics transportation robot system with fork lifter is proposed. The proposed system is designed including a mobile robot, a main server, and a fork-type lifter. The mobile robot is designed in consideration of stable and efficient movement, and the fork lifter is designed to pull out the basket on the shelf. The main server calculates the overall path and the task plan of the robots and instructs the operation by communicating with each robot. To evaluate the performance of the proposed transportation robot, the driving test was performed and a fork lifter working experiment was carried out. The experimental results show that the performance of the proposed transportation system is satisfactory.