Passive water cooling was one of the innovations I brought in with the Blackbox.
There are three reasons why I prefer water cooling:
- I had only good experiences with water cooling before, the Kraken Hotend which I used for a while never failed me (unlike air cooled v5 or v6 hotends)
- Blackbox was designed with a closed built chamber in mind, and water cooling performs way better in that scenario. Another plus is that it's more resistant to general ambient temperature. I witnessed a few summers (in Germany!!) in which the air cooling of an e3d v5 came to its limits.
- It shortens the distance between drive gear and nozzle. A short distance is especially crucial for soft materials, the smaller the gap between gearwheel and nozzle, the more direct the control. And you can truly feel and see it in practice.
Watercooling a tool changing printer the "classic" way would require many hoses to every single tool, which produces just as many possible leaks. Water cooling in a device which has countless high voltage parts can be very dangerous, so you naturally want to avoid too much unnecessary fittings. With the Blackbox setup, you only need two hoses: one goes to the X-Axis and another one to the tool bank. That way, the tool is cooled when active and inactive without beeing cooled actively by itself.
How it works
The system works like any other water block with the only difference that there is no thermal grease and it is not screwed and therefore removable. The lack of heat conductive paste substantially impairs efficiency, but a hotend produces significantly less waste heat than we are used to from CPU or GPU. And while the conductivity between the two cooling blocks is rather low, the water cooling itself is extremely efficient. Maximilian Arnold was so nice to calculate how much waste heat dissipates at the cooler of an e3d hotend. These are his results:
Q=cp*m*dT
Original E3D Hotend
Sunon fan 3010 Maglev 12V
Fan flow rate 0.154 m3/min
Air density 1,2041 kg/m3
cp Air 1.005 kJ/(kg*K)
Ambient temperature 26 °C
Hotend temperature 250°C
Air temperature upper end of the heatsink 30.5 °C
Air temperature lower end of the heatsink 40.5 °C
Average value 35.5 °C
delta T is thus 9.5 K
Thus 29.5 W should be delivered under perfect conditions.
The lamellas got a higher air resistance, therefore one gets counterairflow from the fans. I think that the heat dissipation lies rather in the range of 20-25 W
Instead of the 100-500 watts we are used to cool our computer chips, only about 20w have to be dissipated. And appearantly pure touch is enough to do that, if paired with a titanium heatbreak there should be plenty of room even for high temp materials.
Simulation
I tried to do a simulation in Fusion 360, but the results do not represent reality. As you could see in the video, the tool cooler reaches around 35°C (250°C), in the simulation the tool cooler stays at 25°C. I guess the reason is that fusion calculates with perfect contact surfaces. If anyone knows how to improve the simulation, you can download the Fusion file. I would love to have a better representation.
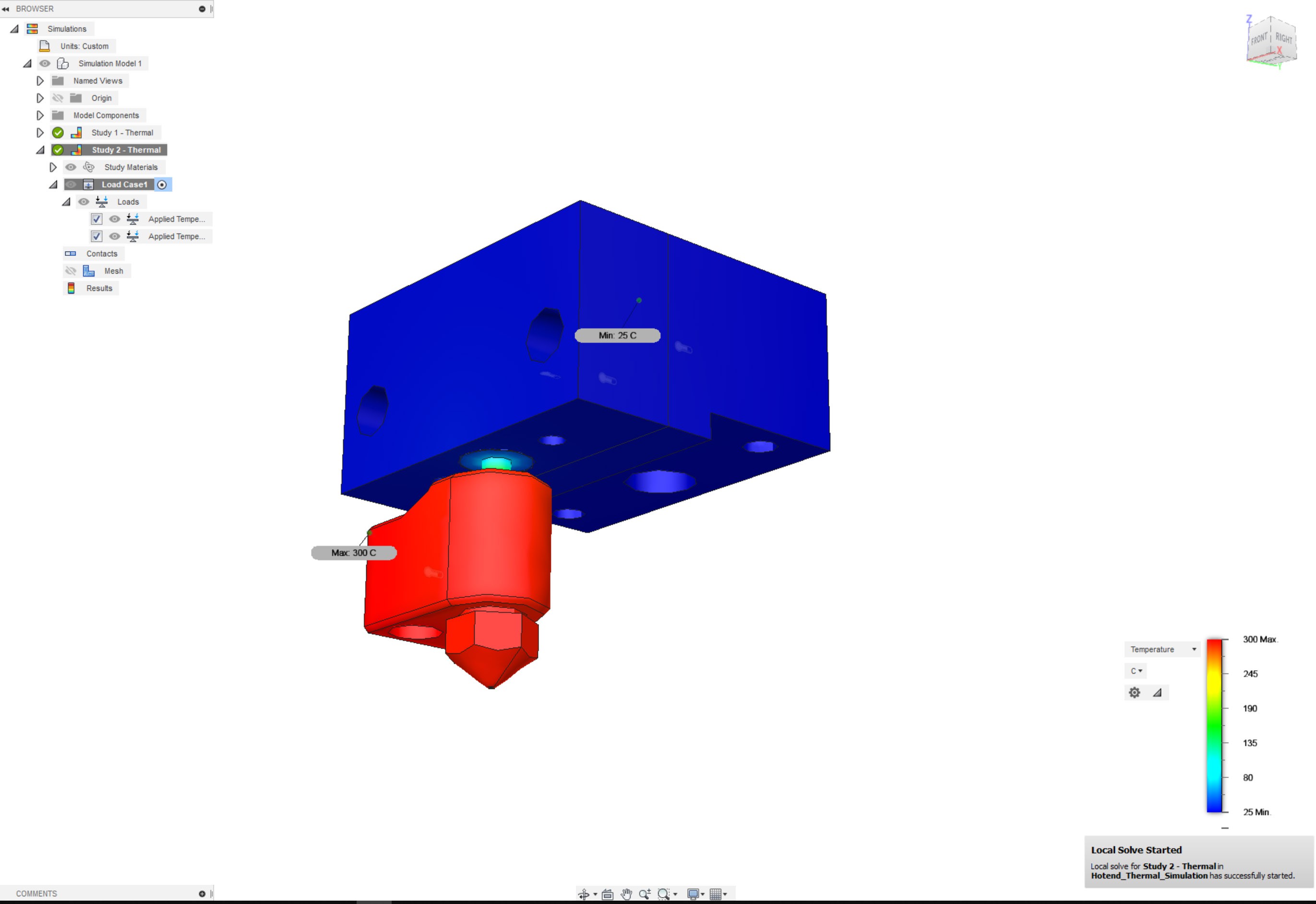
Discussions
Become a Hackaday.io Member
Create an account to leave a comment. Already have an account? Log In.