Credit Where Credit is Due
A few months back, maybe even a year ago, I remember seeing these beautiful, delicate, impossible looking electronics projects based around thin brass tubing by Mohit Bhoite. Across his different social media platforms I gathered enough info to try getting creative with the brass rods myself. Please go check out his work, it's very interesting.
What I Used
My first attempt at manipulating the brass tube used these tools.
Measuring in KiCad
I used measurements that I had previously made in KiCad to start figuring out how long the brass tubes needed to be for each individual 'bond-wire'. I did this with KiCad's Measurement tool, placing the measurements on the user drawing layer. I then printed out the sheet you see above.
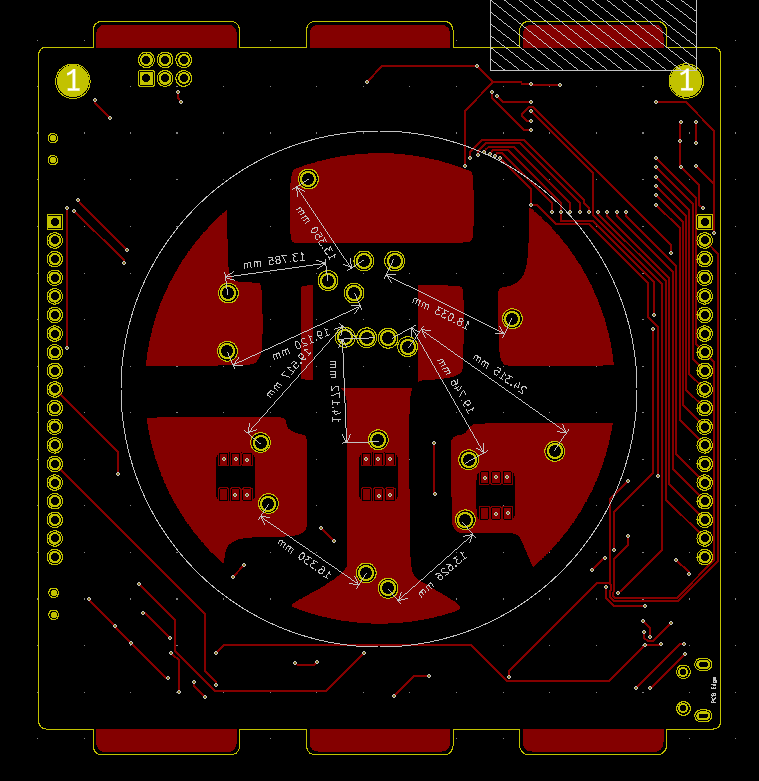
Through trial and error I found that I was adding between 6 and 7mm to the distance between the holes on the PCB to get a length of wire with two 90º-ish bends that would be raised up just a little bit above the surface of the PCB.
After I figured out how long each of the ten individual (and unique) tubes needed to be, I made a list of lengths, measured and scored each length with the caliper, cut them with my flush cutters, and bent them with the needle nose pliers. I did my best to keep the two bends on the same plane and tweaked them into position as needed. I attempted to use the K&S tubing bender, but it's designed for larger diameter rod/tube and it didn't work any better than my hand and the pliers in my opinion.
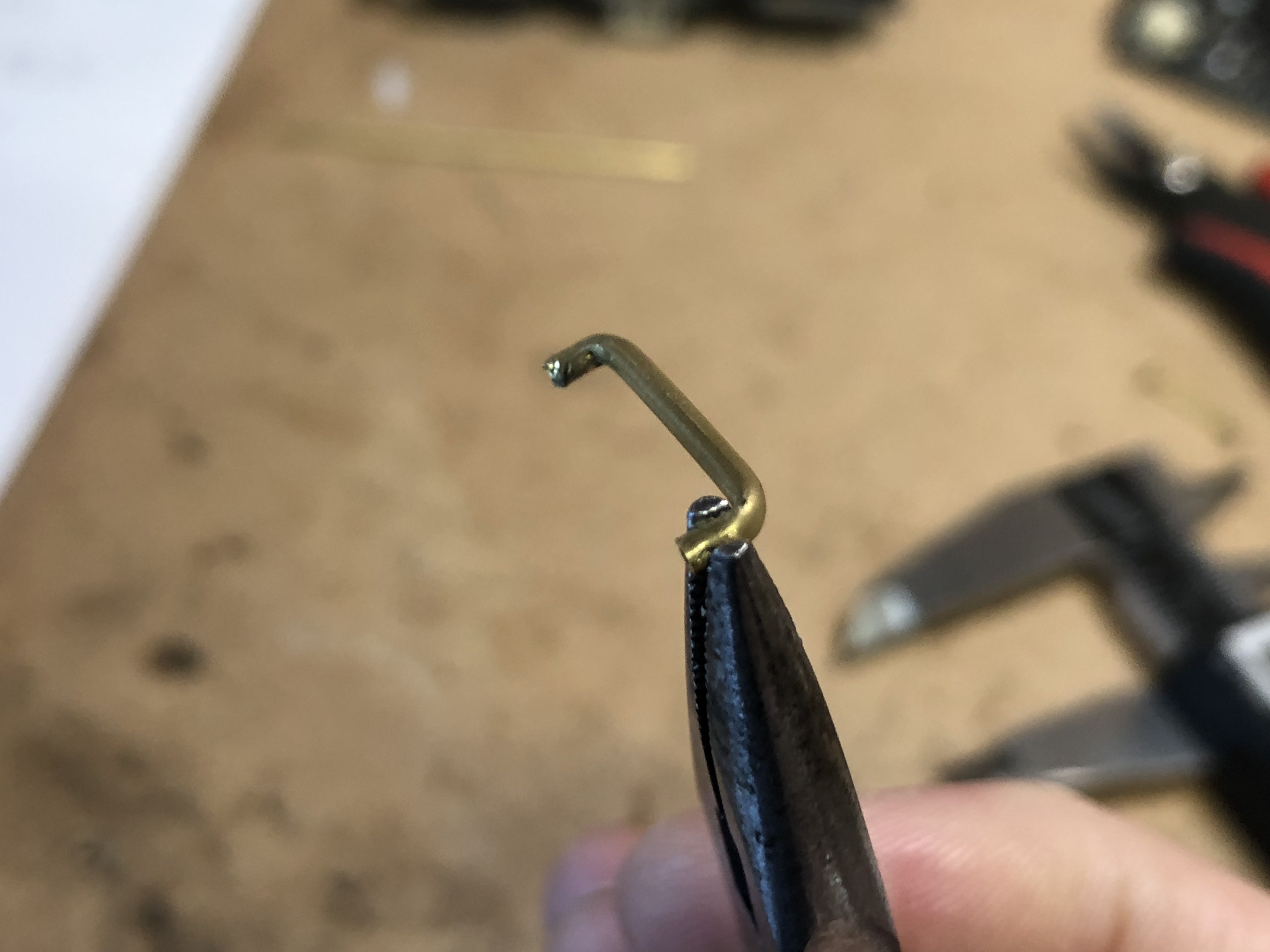
Using the flush cutters flattened out the tube where I cut it, so I used the pliers to force the tube back into a tube-like-shape that would place nicely with the round holes they were meant to mate with. I'm being pretty lenient with the tolerances here so I was able to bend any tubes that didn't land perfectly in their holes until everything seated nicely. I also didn't care too much about marring the ends of the brass tubes as they would be nested within the hole in the PCB and I didn't think you'd be able to see many of the imperfections.
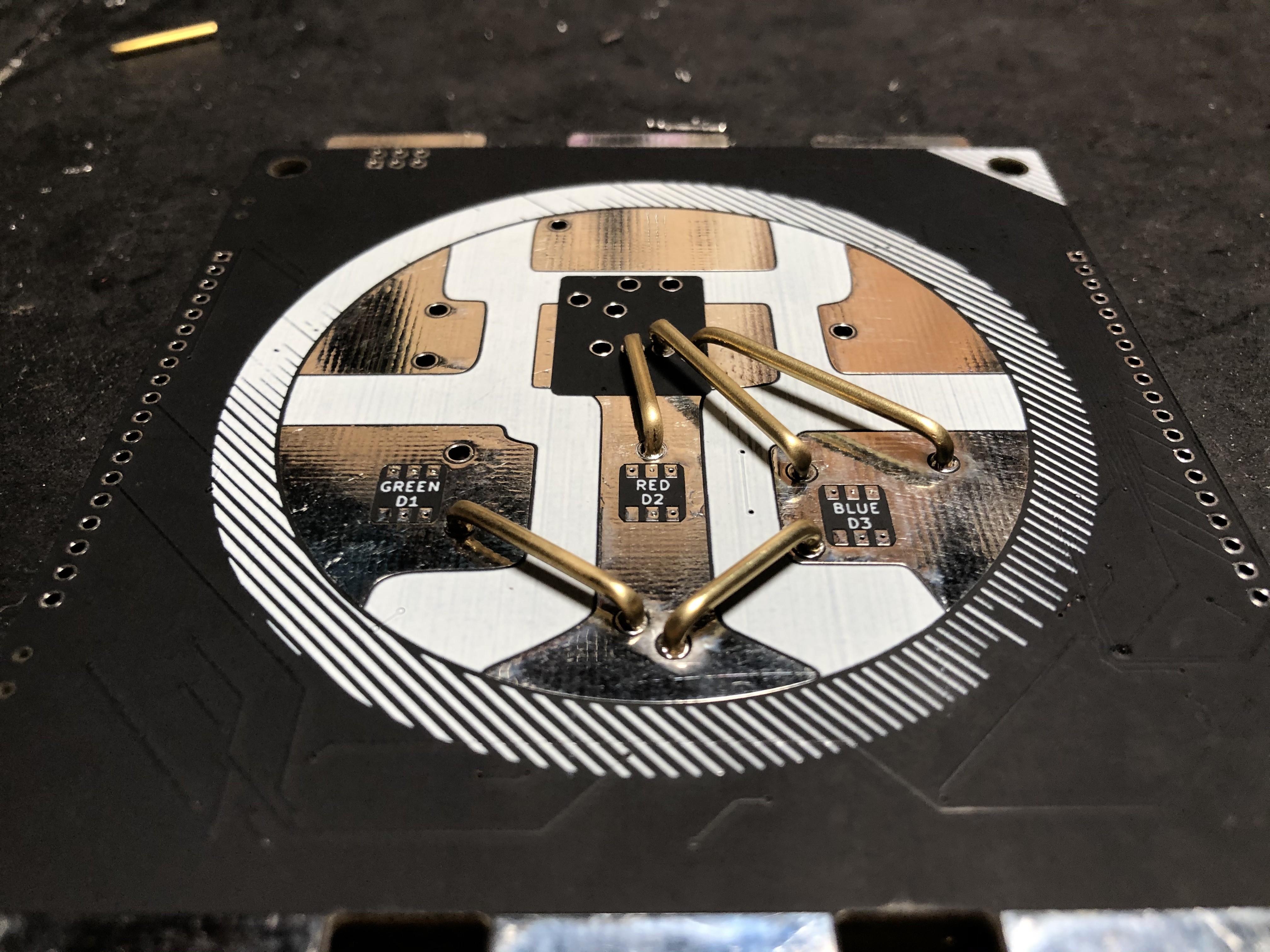
I can get a really nice fit my bending the brass into the exact position I want it, and it snuggly fits into the 1.7mm holes in the PCB. The tension of the bent metal was enough to hold the tubes in place while I flipped over the board and soldered them into place. For the most part they all soldered very nicely save for one tube (H10) that was protruding a little bit. I will be mindful of this in the future.
Overall, the front of the PCB looks extremely clean as far as the attachment of the brass tube, especially in comparison to the first version of this board where I essentially welded the tubes to the large copper pads.
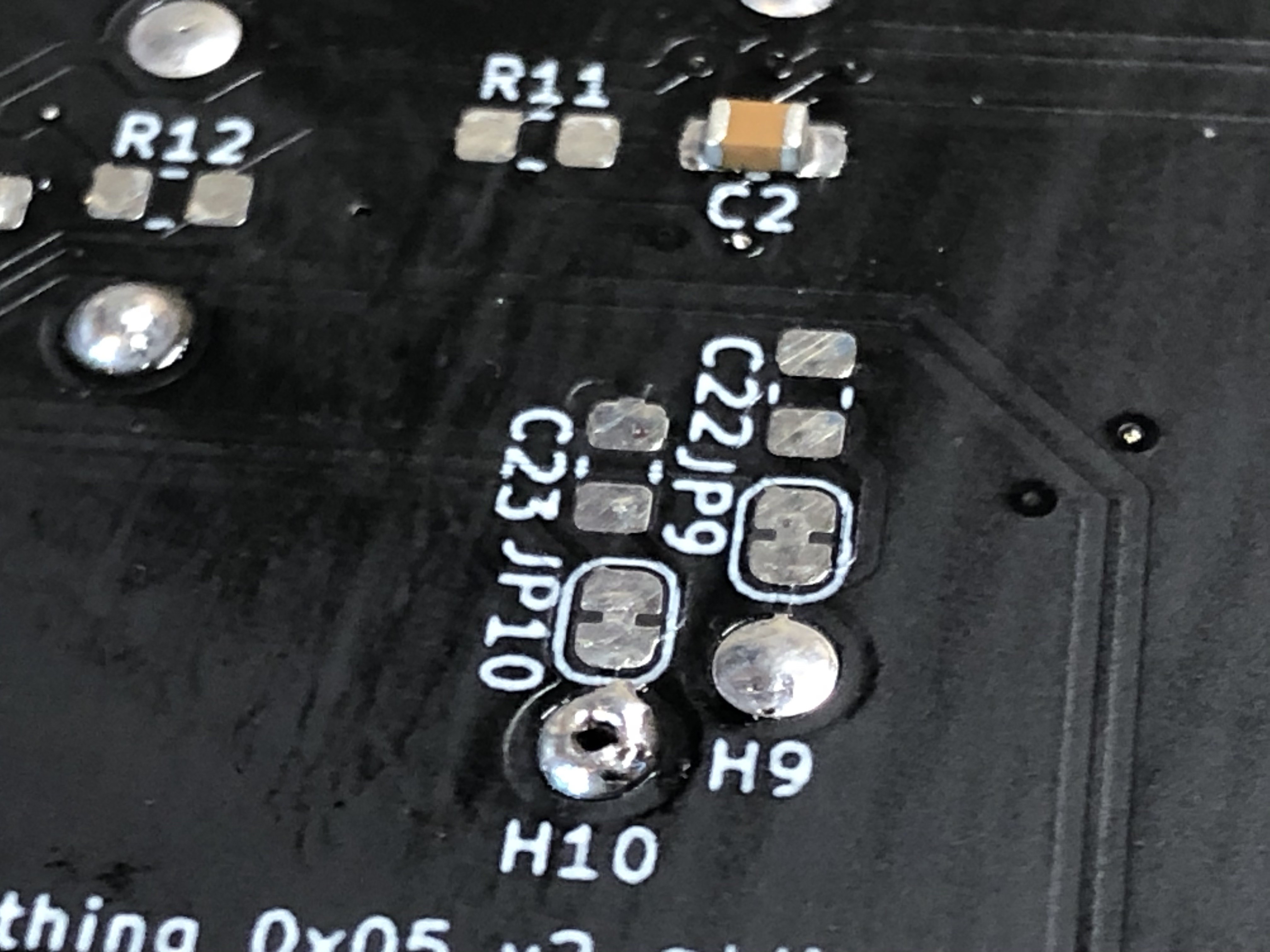
Here's a short clip of me the first bit of code I have running on the first prototype. It's a slight modification to the Adafruit Neopixel strandtest example that allows for touch input.
Discussions
Become a Hackaday.io Member
Create an account to leave a comment. Already have an account? Log In.