Testing:
First Trial:
At my first trial to run the pump, the motor's shaft was disconnected from the rotors and as such was rotating independently and the rotors remained stationary as shown below. To overcome this, I used adhesive to stick the shaft and rotor together to be able to run the tests.
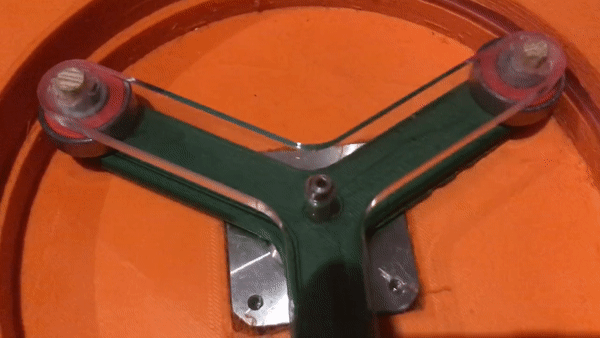
Maximum Speed:
The pump was tested at the maximum speed to see if the rotors are able to rotate through the casing and understand the potential max volume flow rate possible. Once the motor was operated, the rotors started rapidly vibrating in place as shown in link below. I assume this is because the torque supplied by the motor at such speeds is not sufficient to overcome the frictional forces and moments the bearings experience from the casing's raceway.
https://vimeo.com/user110521159/review/400015830/37903e3764
Other Speeds:
However, what I quickly realized is that even at slower speeds the rotor had difficulties rotating smoothly and while this can be due to manufacturing errors causes the rotor and casing to contact, this meant that if a tube was added the rotor will not be able to rotate at all.
Verdict:
Conclusion from testing the prototype is that:
- Size of the pump is too big for the motor to provide a reliable torque
- Larger tolerance needed between rotors and casing
- Need to use more flexible tubing to reduce load required by motor
Discussions
Become a Hackaday.io Member
Create an account to leave a comment. Already have an account? Log In.