As mentioned, the schematic is taken straight out of datasheets so I didn't expect any problems, nor did I encounter any. It was insanely easy to get working.
After putting the components on a breadboard, and doing an anti-smoke accident check, I connected it up to an Arduino Uno to test it.
Except for one LED plugged in backwards, which I corrected, the test program worked first time. Here it is:
/*
Test shift register display
*/
#define DATA 2
#define CLOCK 3
#define LOAD 4
void setup() {
// put your setup code here, to run once:
pinMode(DATA, OUTPUT);
pinMode(CLOCK, OUTPUT);
pinMode(LOAD, OUTPUT);
digitalWrite(DATA, LOW);
digitalWrite(CLOCK, LOW);
digitalWrite(LOAD, LOW);
}
void writebyte(unsigned int i) {
for (byte mask = 0x80; mask != 0; mask >>= 1) {
digitalWrite(DATA, i & mask ? HIGH : LOW);
delayMicroseconds(10);
digitalWrite(CLOCK, HIGH);
delayMicroseconds(10);
digitalWrite(CLOCK, LOW);
delayMicroseconds(10);
}
}
void load() {
digitalWrite(LOAD, HIGH);
delayMicroseconds(10);
digitalWrite(LOAD, LOW);
delayMicroseconds(10);
}
void write2bytes(unsigned int i, unsigned int j) {
writebyte(i); // MSB
writebyte(j); // LSB
load();
}
void loop() {
// put your main code here, to run repeatedly:
for (unsigned int i = 0; i < 256; i++) {
write2bytes(i, i);
delay(250);
}
}
All that the program does is repeatedly display an 8-bit counter as binary on the two columns of LEDs in parallel, at the rate of 4 per second. This rather than display one 16-bit counter as I don't want to wait 5 hours to see the whole cycle.
The CLOCK and LOAD lines are pulsed for 10 microseconds. This implies a maximum data rate of 50,000 bits/second, far more than adequate for this kind of display. I limit the rate so that the wiring isn't critical as it might be at a higher rate.
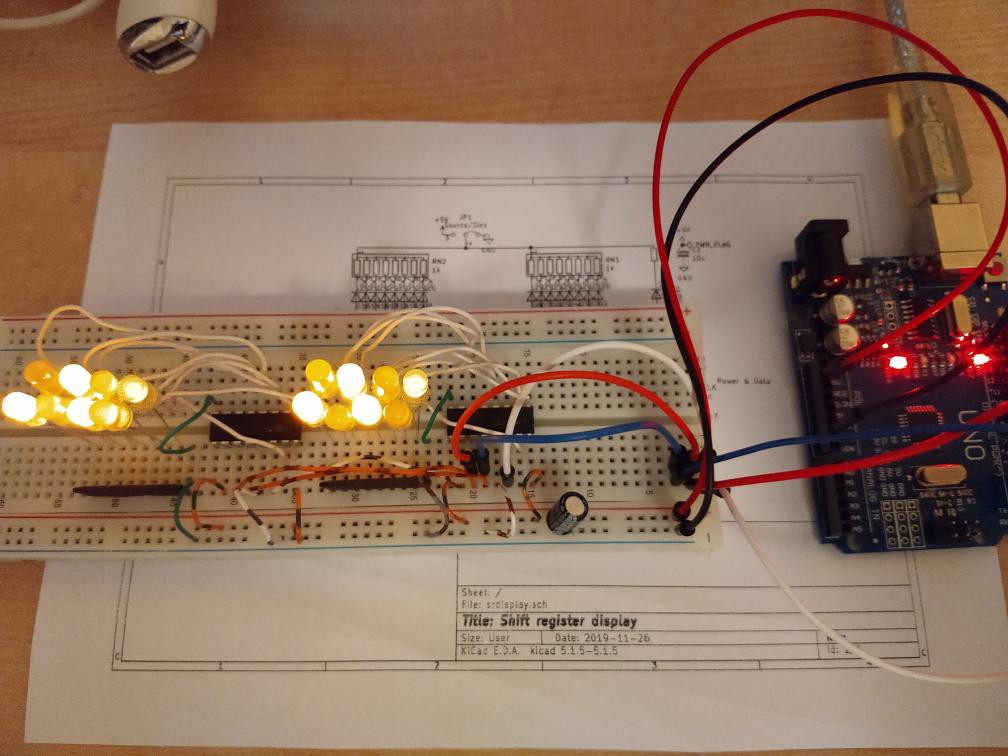
Next step will be to get the board fabricated.
Discussions
Become a Hackaday.io Member
Create an account to leave a comment. Already have an account? Log In.