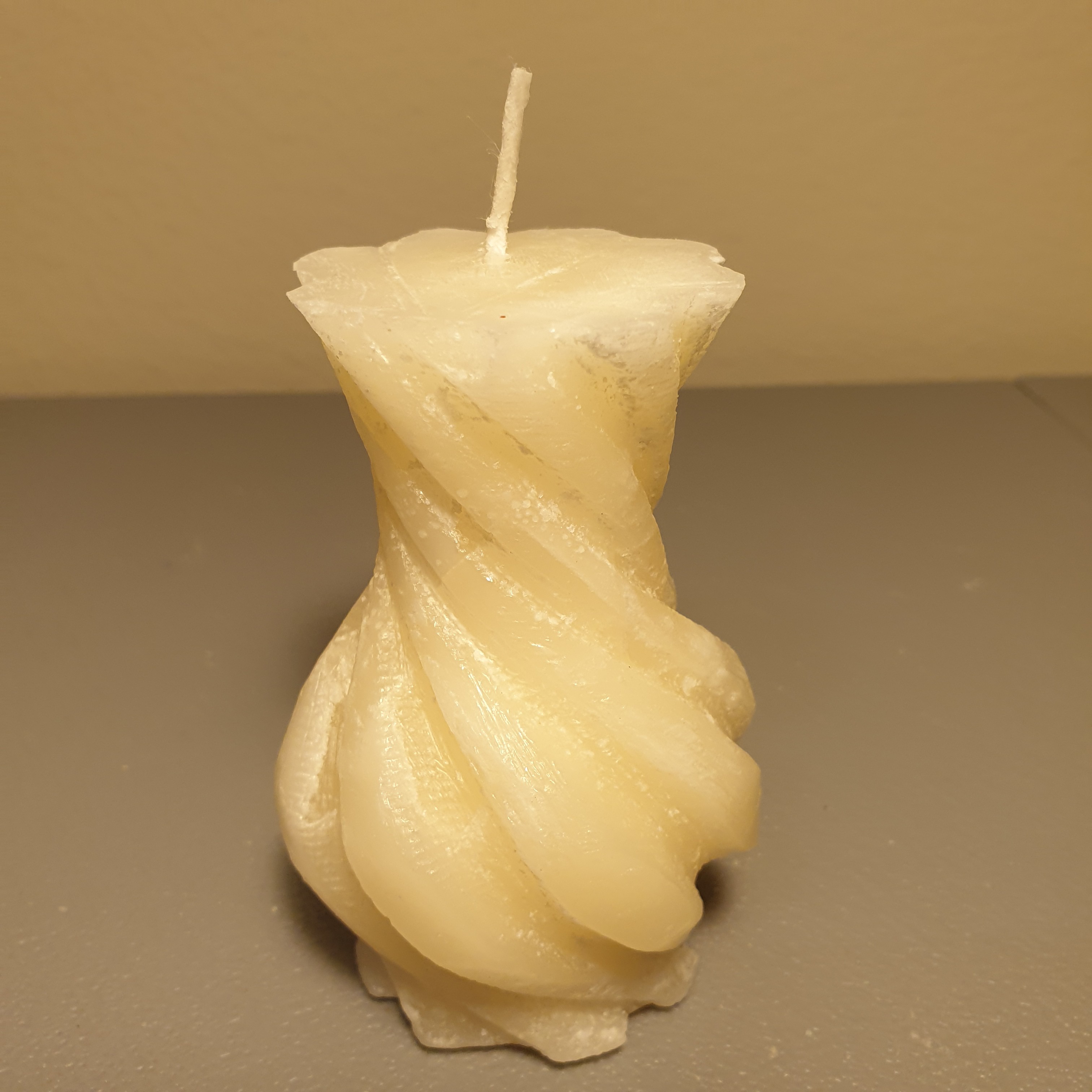
I completed the first successful candle carving this weekend! The carving is approximately 60mm in diameter and 92mm tall. It took 5 hours and 50 minutes to machine the spiral fluted vase design from a pillar candle. Both the roughing and finishing machining operations were performed with a 1/8in diameter router bit.
I generally only post project logs when I have an interesting visual of project progress. All the challenges I had to solve to get to that point often go undocumented. So just for fun here, these are all my previous failed attempts at candle carving with this custom cnc system:
- My computer shut down after 40 minutes per the "power & sleep" settings I forgot to change -> the Arduino stopped receiving g-code and the operation stopped
- I didn't zero the system properly prior to starting the machining operation -> the bit rammed the candle
- I was using wax bur bits and the rotational feed rate was too fast -> the plywood frame flexed and the bit dug into the side of the candle
- I hand tightened the bit into the chuck -> bit came out during the machining operation
- I forgot to set "$1" of the grbl config to 255 -> the motors would "disable" between movements and motor synchronization was lost
- The ground connection on the x-axis enable of the stepper motor driver came loose -> the x-axis stopped moving
- I ran using too high of cut depth per pass -> it pushed the candle out of the longworth chuck
- I input the wrong stock material size in the rotatory machining program that generates the g-code -> the bit rammed the candle
- ... :(
Moving on from all the setbacks. I didn't end up laser cutting a custom electronics enclosure for this first prototype build. Instead, I drilled holes and mounted the electronics to a spare 12x24in plywood sheet I had available.
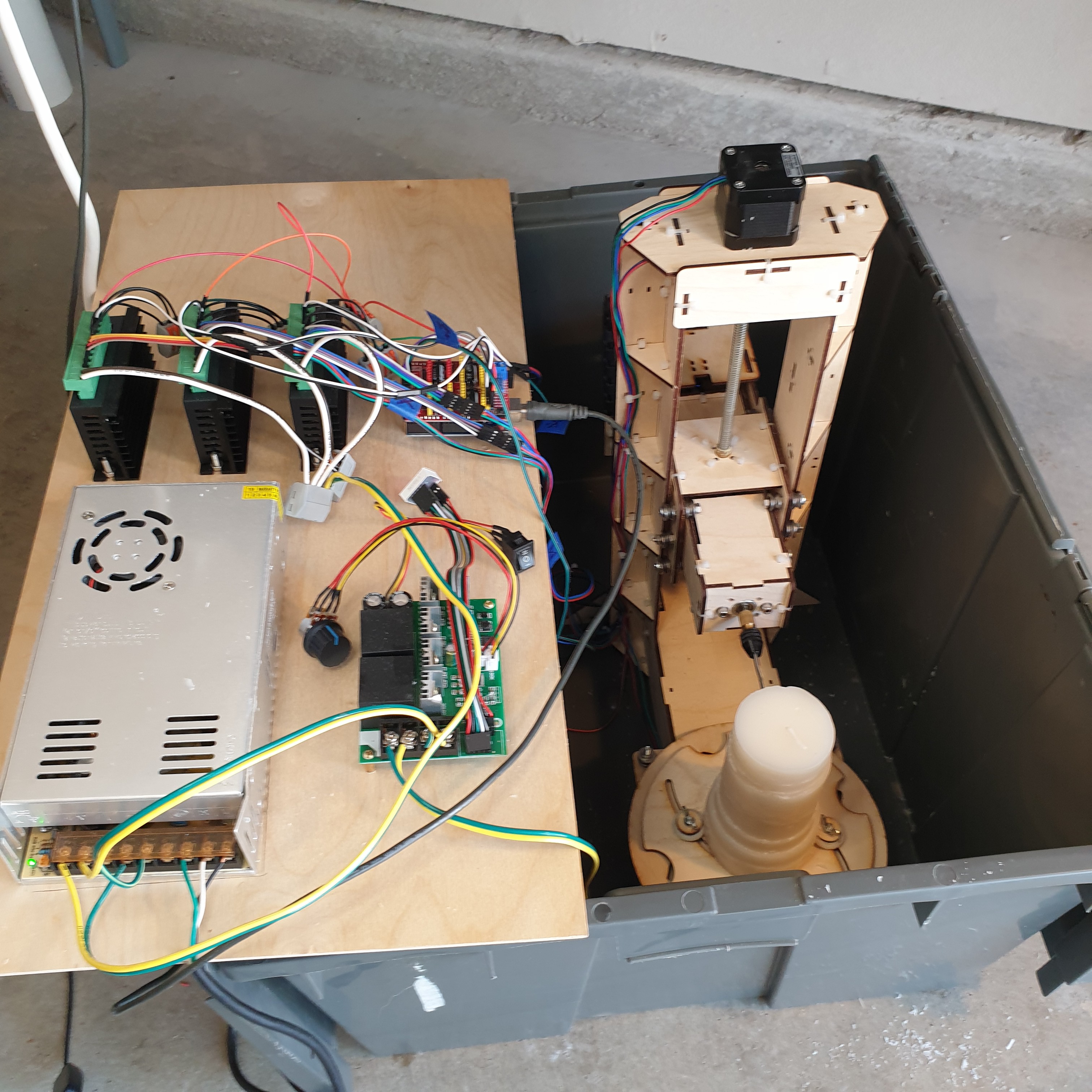
One minute of the roughing operation:
One minute of the finishing operation:
Overall, I was happy with how the first candle carving turned out. The motors stayed synchronized and did not overheat while in operation for almost six hours. The 1/8in router bit was sharper than the wax bur bits that I had been using previously and allowed a much faster feed rate. The dimensions of the final part matched closely to the modeled part dimensions.
Even so, there is still room for improvement. Adding torsional stiffness about the vertical axis would allow higher tool feed rates. The candle chuck can be redesigned to achieve a more rigid connection between the candle and the machine (possibly hold the candle from both top and bottom). The base rotational axis can be redesigned for ease of assembly. Its probably worth exploring alternatives to the v-bearings. Even with six of them on each axis there is still a little play and they tend to vibrate and create noise during operation.
Discussions
Become a Hackaday.io Member
Create an account to leave a comment. Already have an account? Log In.
Looking great. Thanks for sharing.
Are you sure? yes | no