At the same time that I ordered my rivet and taper samples I got a quote on the cost of enough parts for my H-500:
- 350 Flange Head Eyelet - $19.32 (CDN)
- 200 Steel Milled Taper Pin - $59.32 (CDN)
So 80 bucks if I make 100 jumper cables (the number that shipped with the original Computer Lab). But even if I only make say 50 jumper cables that's still $50. So while I was waiting for the samples to arrive, I played around with a rivet alternative idea.
Here is what I came up with:
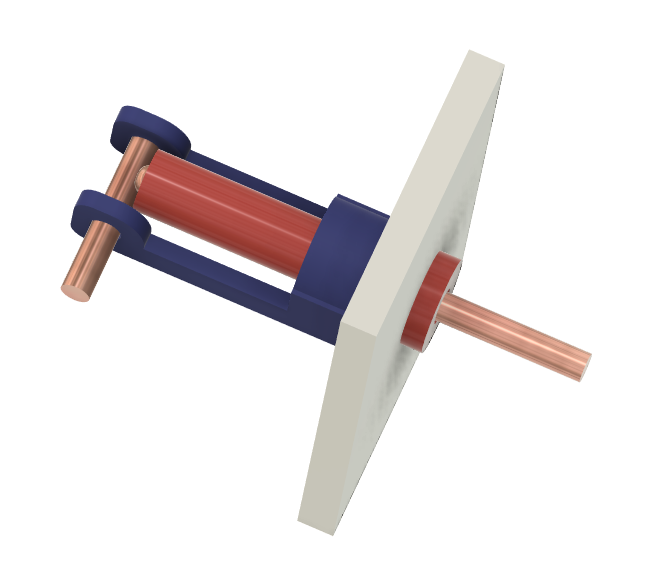
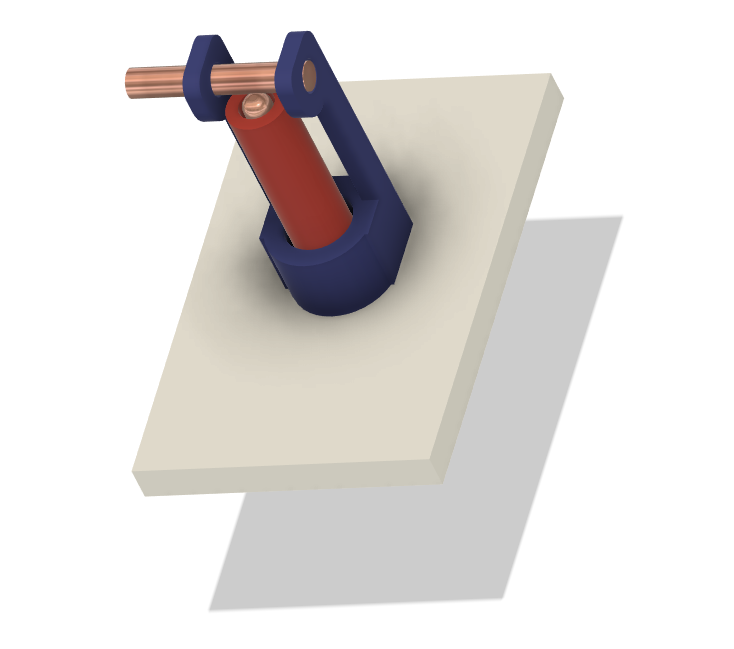
The design uses standard 14 AWG wire for both the jumper cable ends and the connector inside the terminal jack. As the jumper wire is pushed into the jack and comes in contact with the connector wire (which is offset from the center of the hole) the uprights (in blue) will bend slightly allowing the jumper wire to pass and keeping the two wires in firm contact.
I printed a few.
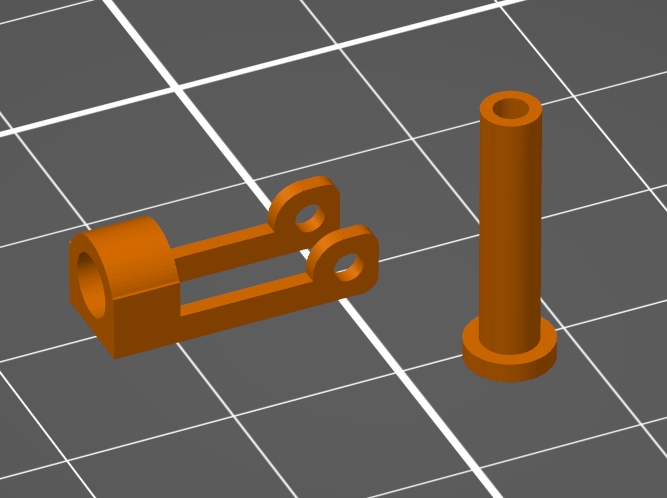
It's especially important to print the part that holds the connector wire in this orientation for strength. No supports required, but since the actual parts are so small I did need a small brim.
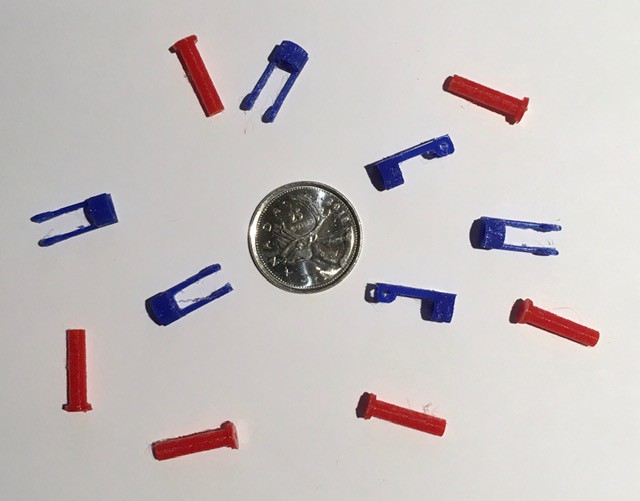
They are pretty small. I tried one out.
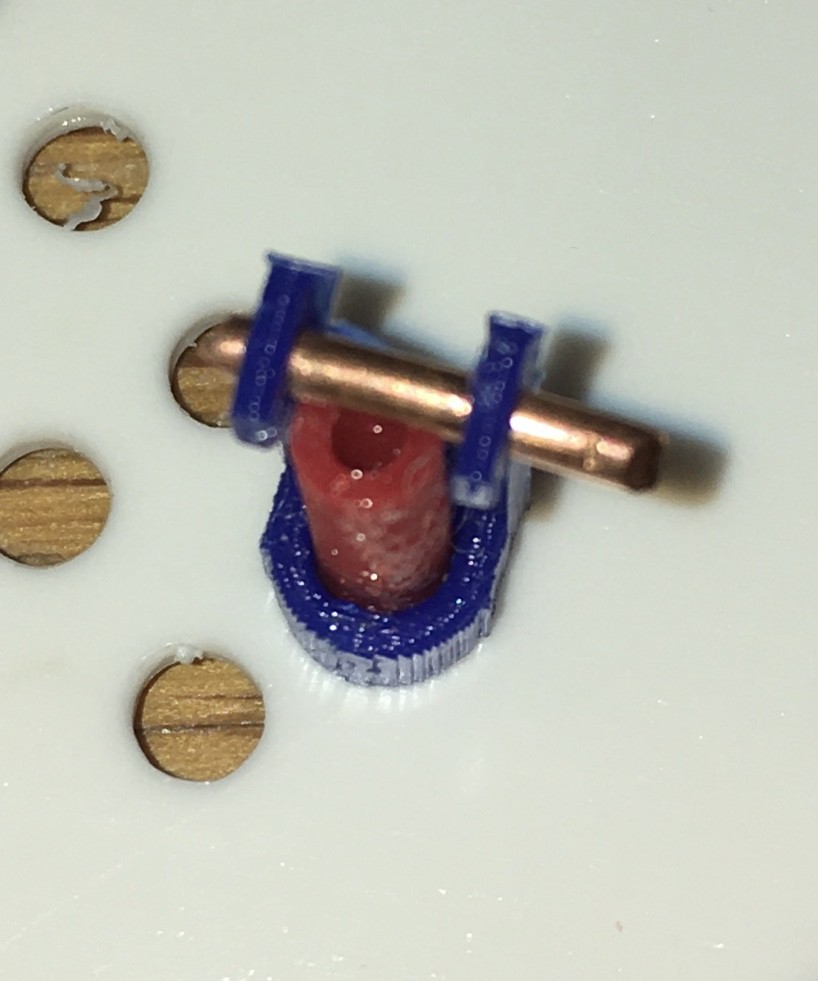
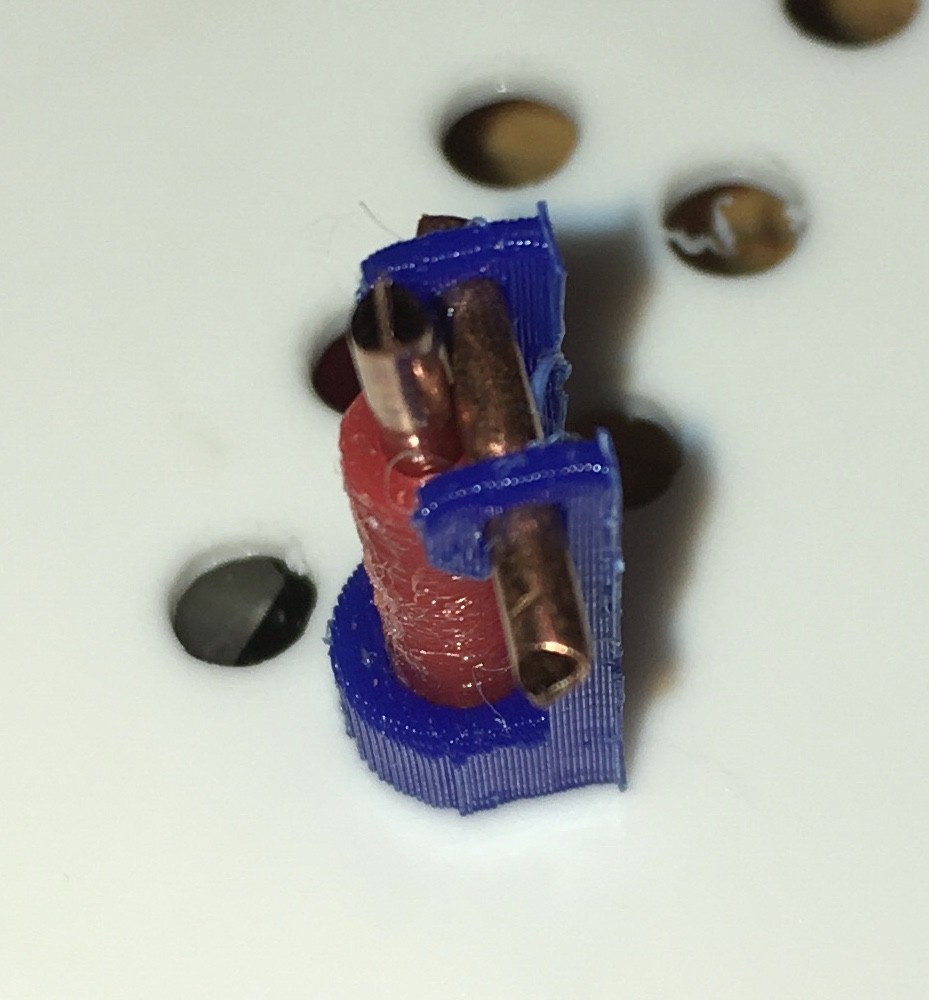
And it actually worked pretty well. One of the reasons for this design is that the terminals have to be grouped together pretty tightly in places so I had to check if this would be a problem.
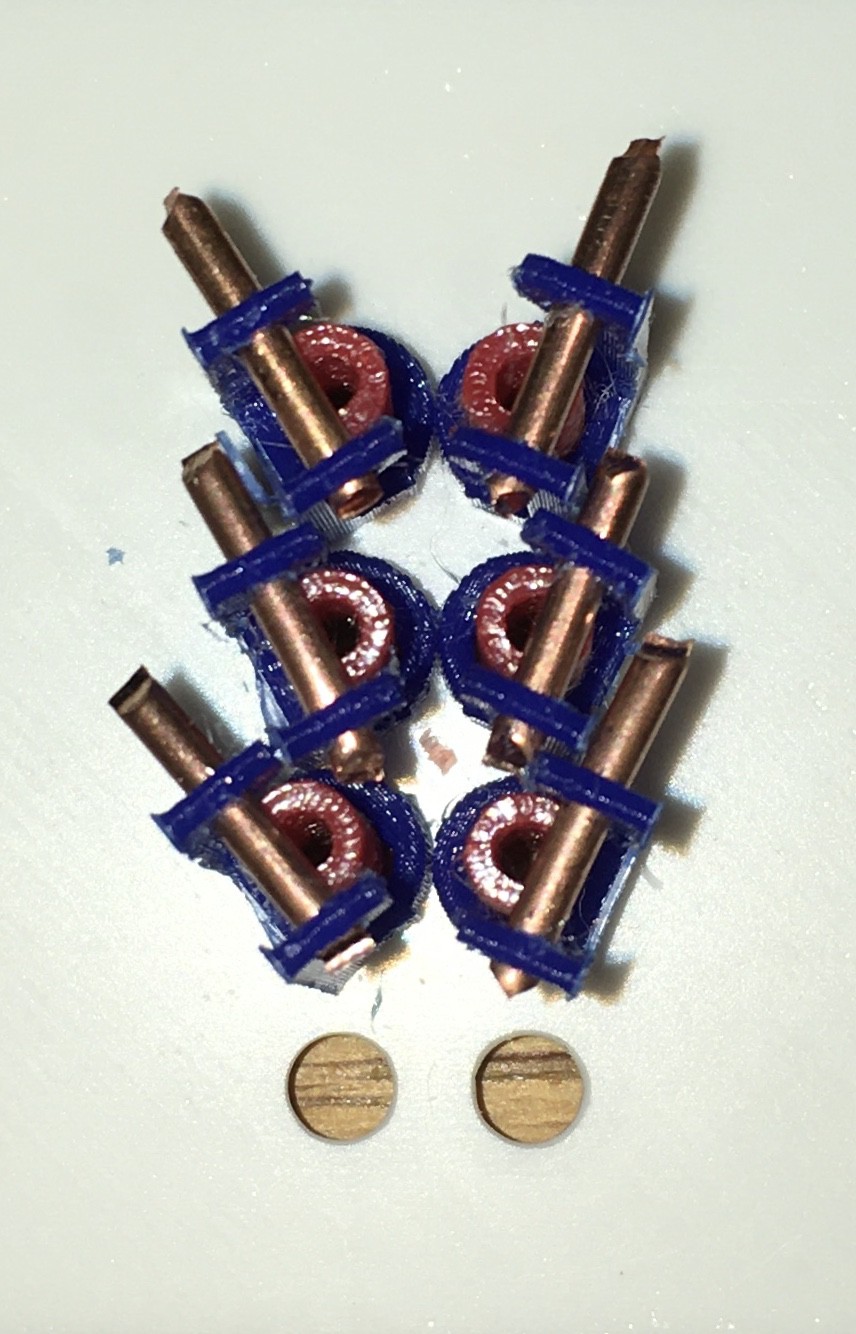
A little tight but it looks like it will work.
All in all a pretty successful exercise. So will I use this alternative? Probably not, even thought the total cost for these terminals and jumper cables would only be a couple of bucks.
There are a few reasons for this:
- This solution is pretty labor intensive. Because the small parts require brims to print there is a fair amount of post processing to get them ready for use (x 335 remember). In addition the parts will have to be glued in place and again due to the small size will be hard to position. Soldering the connection wires and securing them in place will also be an issue. I'm not afraid of the work, but it feels like I would be asking for trouble in the long run.
- I worry about the long term viability of this solution. As the plastic becomes brittle over time it may not provide the amount of force necessary to maintain good contact between the wires, or may in fact break.
- The plastic "rivets" even if printed with copper colored filament won't look as authentic as the brass equivalents on the original H-500.
Would I ever use this technique? Sure would. In a situation where there were far fewer terminals required, and where the terminals were spaced a little further apart allowing for slightly more robust parts I wouldn't hesitate.
Discussions
Become a Hackaday.io Member
Create an account to leave a comment. Already have an account? Log In.