I should start by saying that my CAD skills are mediocre at best. I don't really know how one would properly design an insert for a cavity with curves on every surface but I started with paper and cardboard. Once I got a pretty good initial cardboard template assembled from lots of bits of cardboard taped together, I scanned it and imported it into CAD. From there I laser cut the base out of chip board and refined the shape over a few iterations. Once I had the shape of the base I was able to establish a reference point from which I could make more cardboard templates for the arms that would hold the net. These went back into the scanner and into CAD and then I was able to start the process of designing parts.
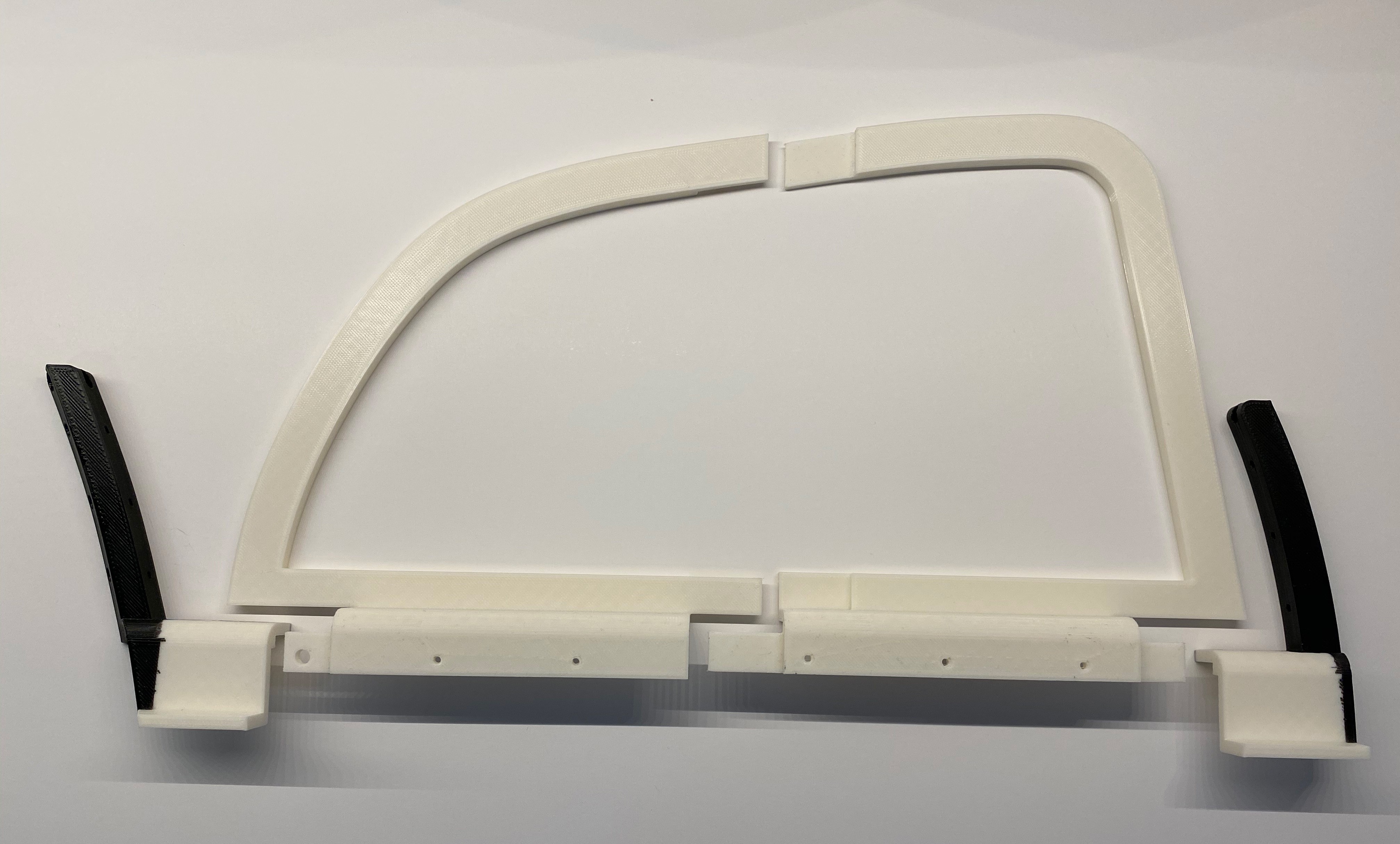
The picture above shows the third revision. The plan was to create an insert that would hang off of the lip of the pocket on the flat side (thus the rollover to catch the lip) and then have the rest just be a tight fit around the edge. Knowing that the arms would be connected by a bungie cord I wanted these to be printed in a different orientation to increase strength so they were designed as separate parts that have interlocks that can be easily glued together. My original plan was to cover the base with felt but leave the arms exposed so I spray painted them black to match the trunk.
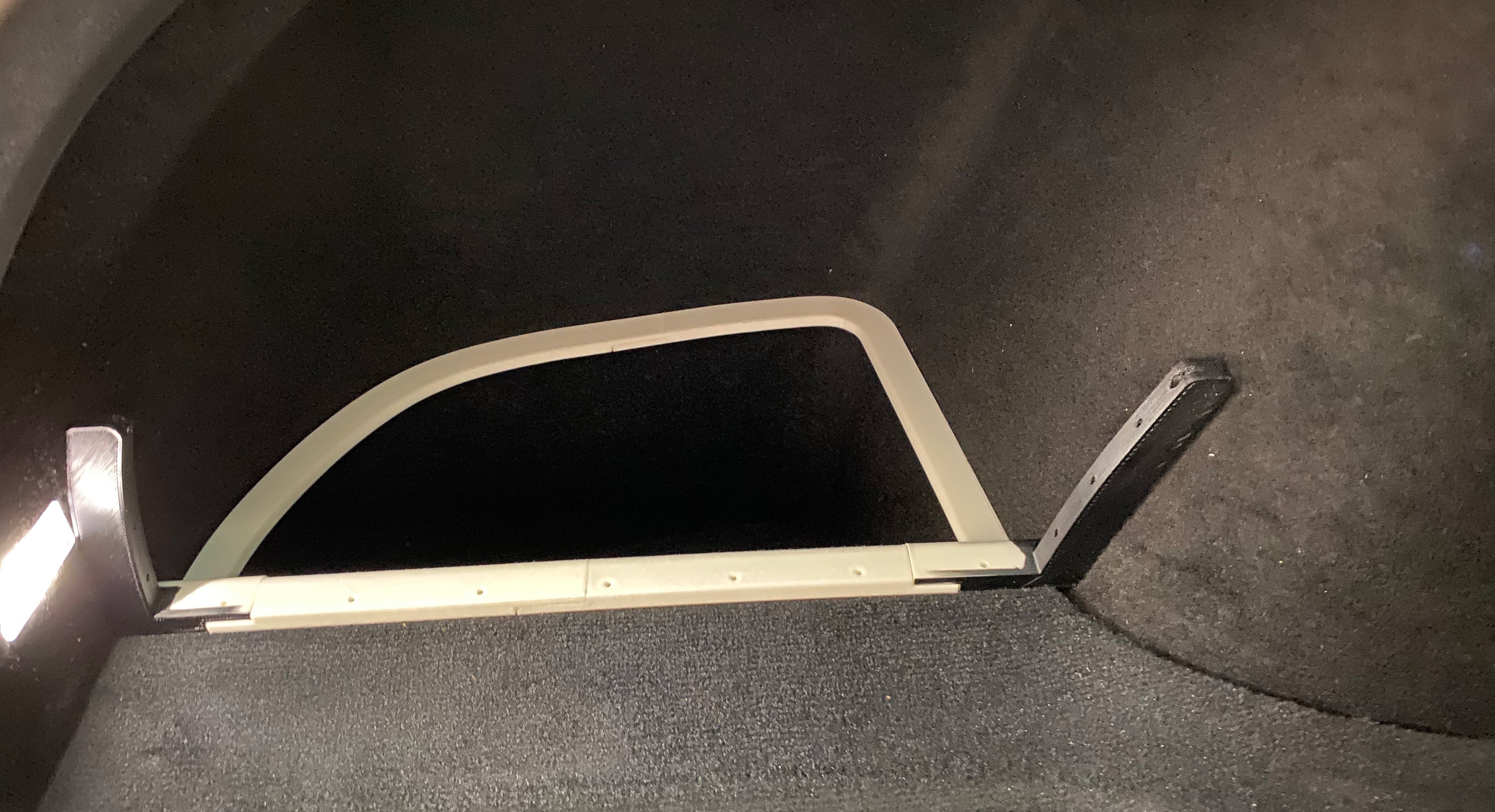
The image above shows the assembly installed in the trunk. Everything fits well and the arms match the curves of the trunk really well. Notice the holes in the arms and the rim of the base. These are for the net. In order to keep things clean, I planned to pull the netting through the holes and glue them from the hidden side.
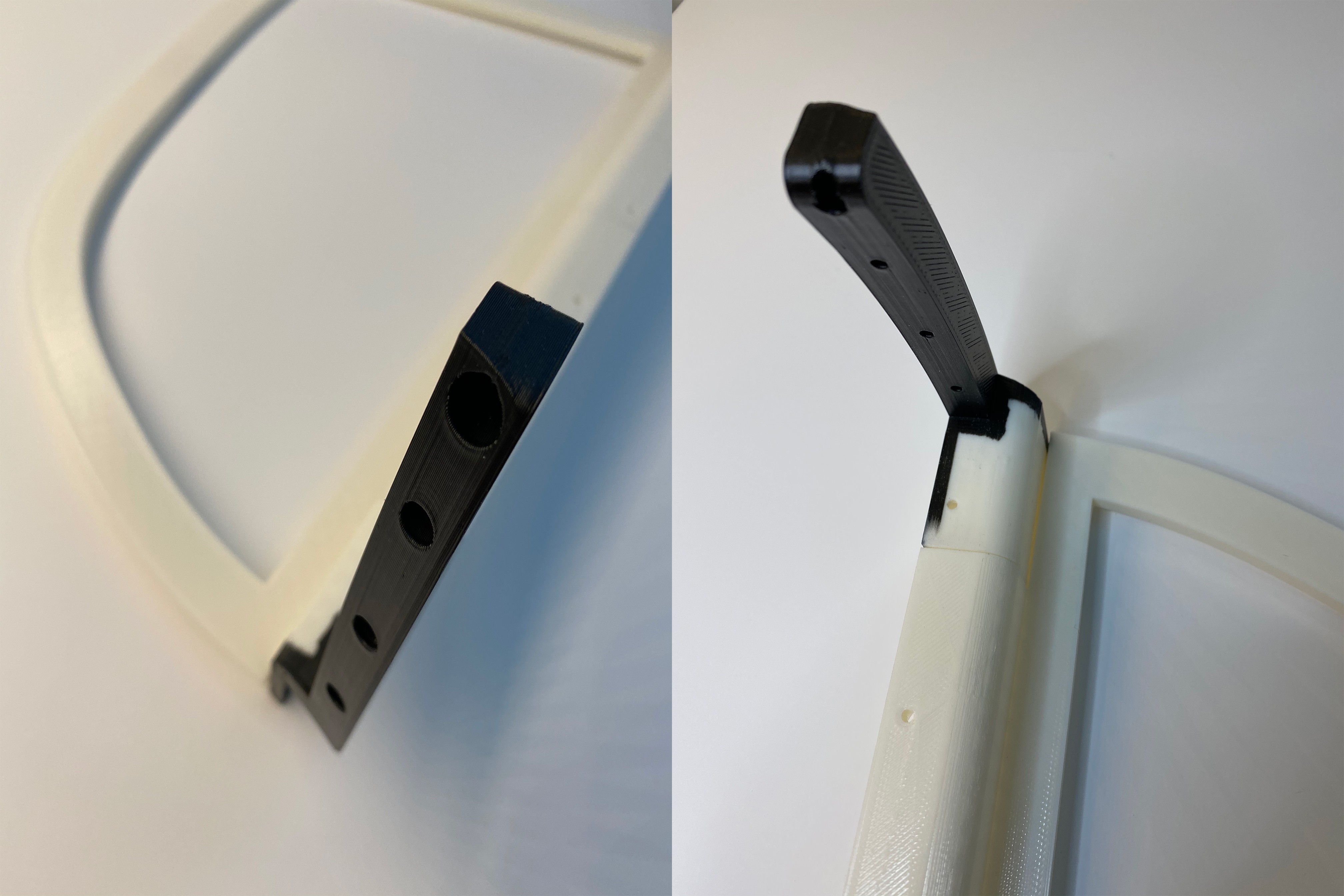
Next step was to finish the base by gluing the laser cut chip board onto the frame and then cover everything with adhesive backed felt.
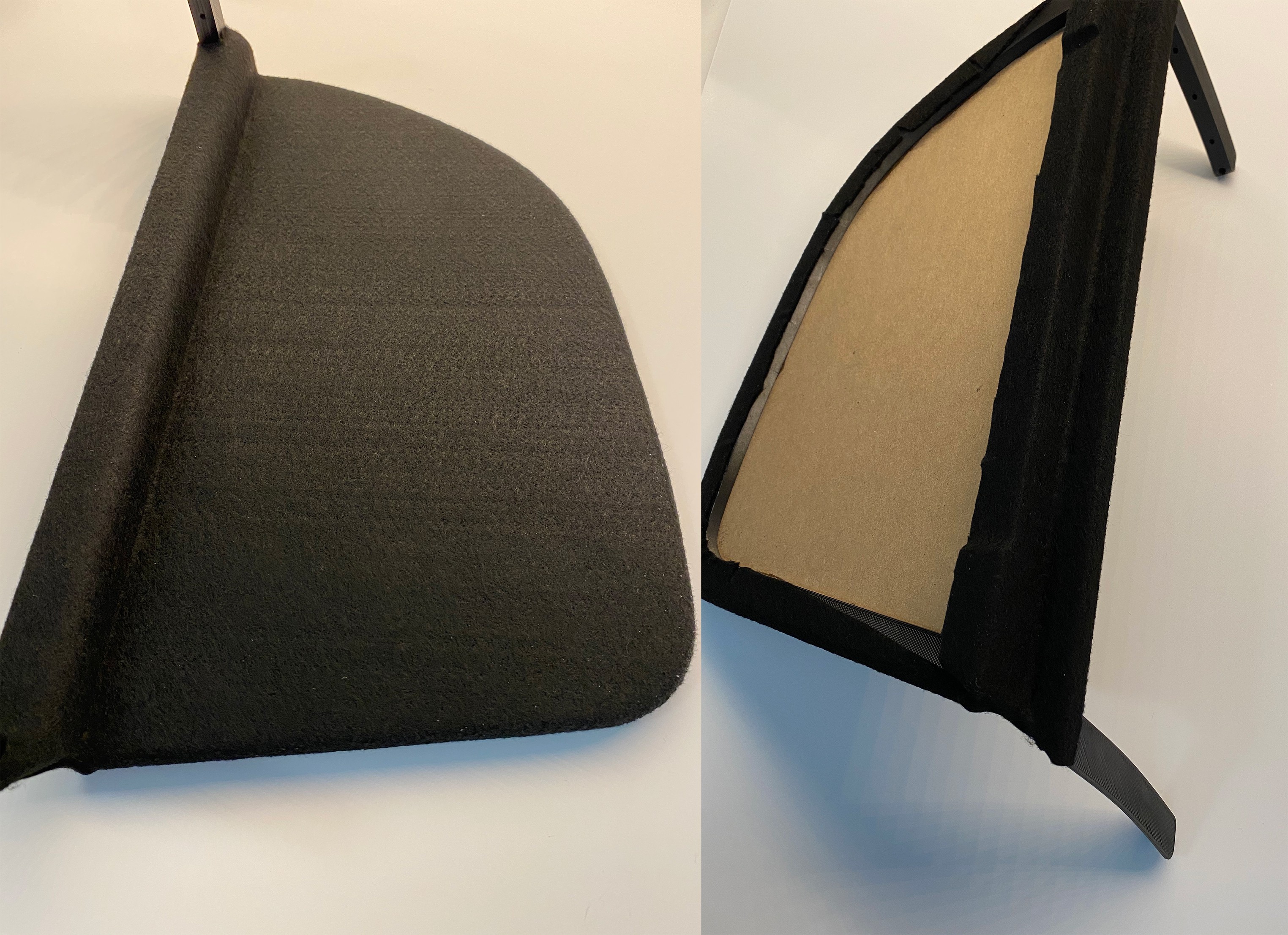
With the felt in place, it was time to attach the net. The net is just a cheap cargo net from Amazon which was cut up for parts.
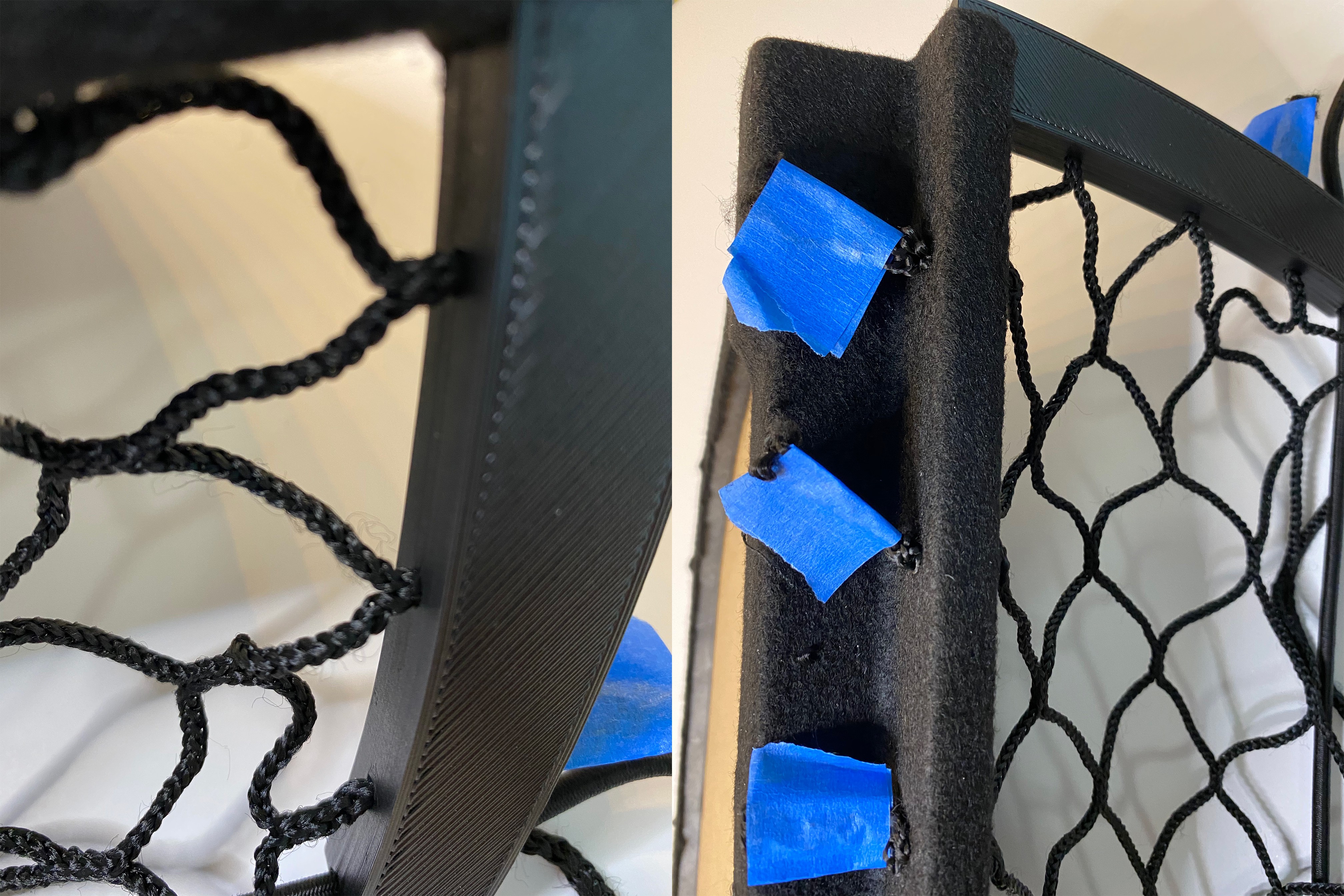
The cut ends of the net were passed through the holes with a needle, sealed off with hot glue and then trimmed. The bungie cord across the top was terminated with a wire wrap to make sure it could handle being pulled without any risk of popping out of the arms.
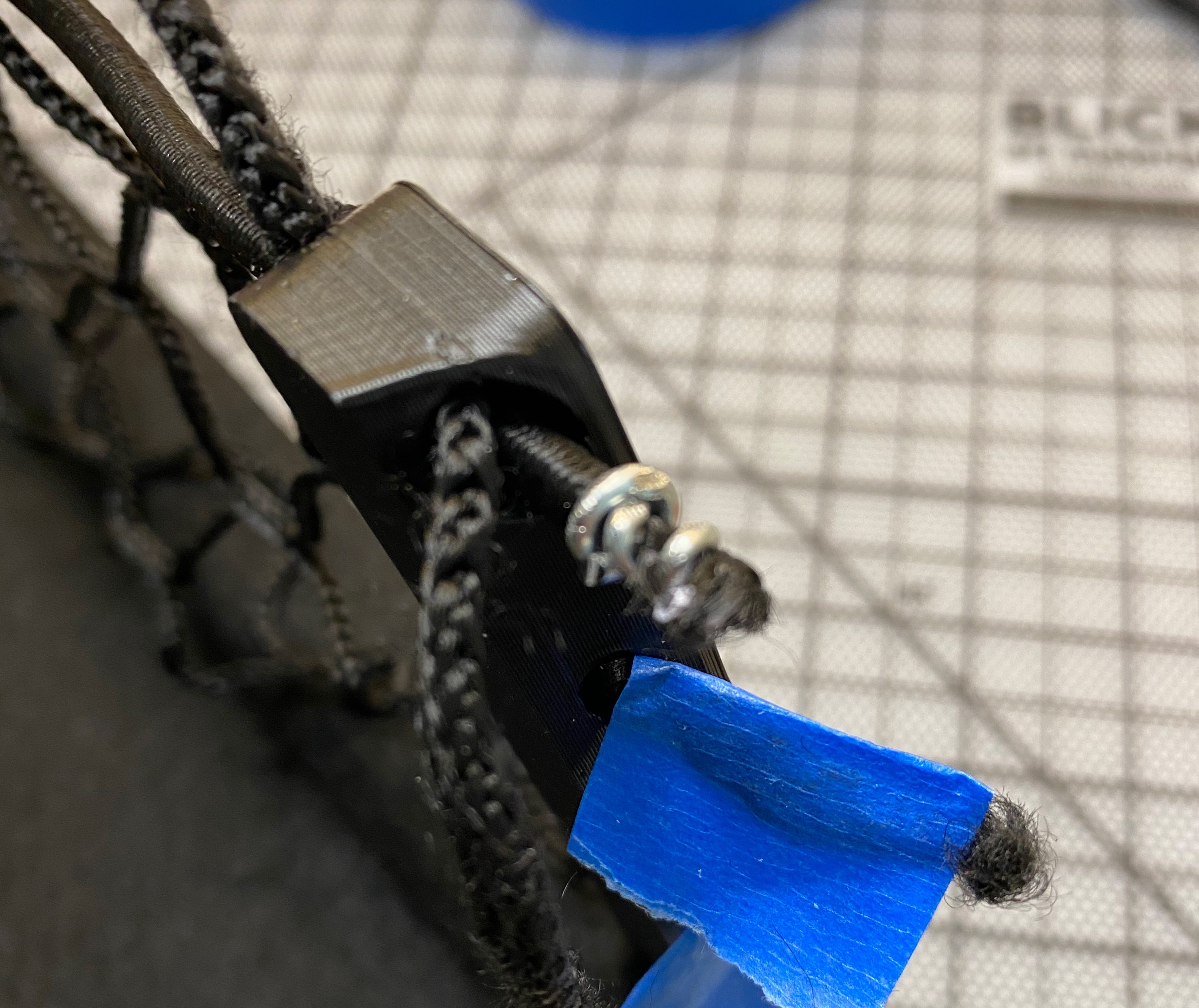
Here is a shot with the net fully attached.
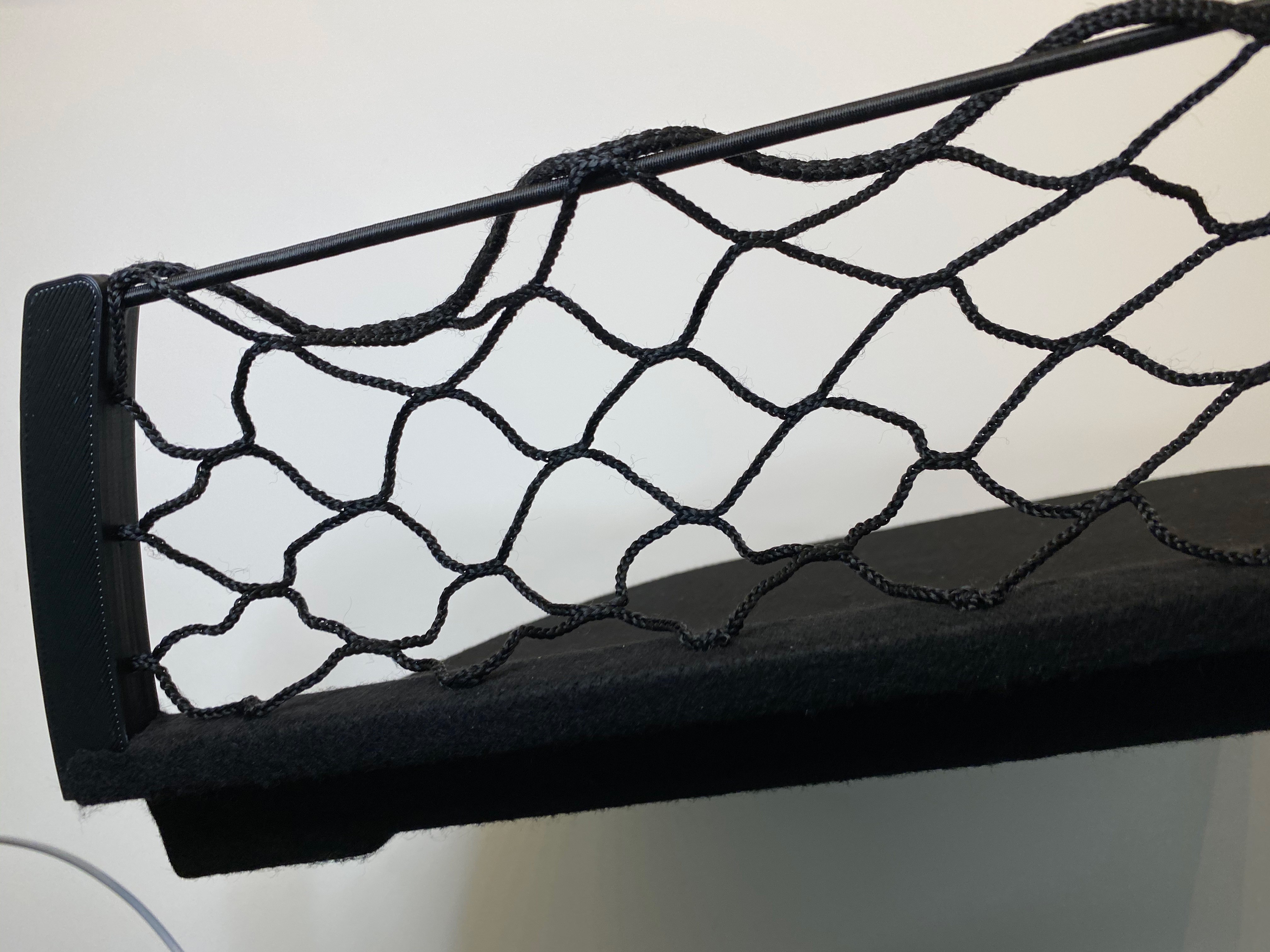
Finally I wrapped the arms with felt and installed it into the trunk. This can easily be inserted and removed but is quite stable when installed. I'll likely add a support to the bottom that will allow it to hold more weight but it's currently very stable just resting against the curved surfaces of the trunk.
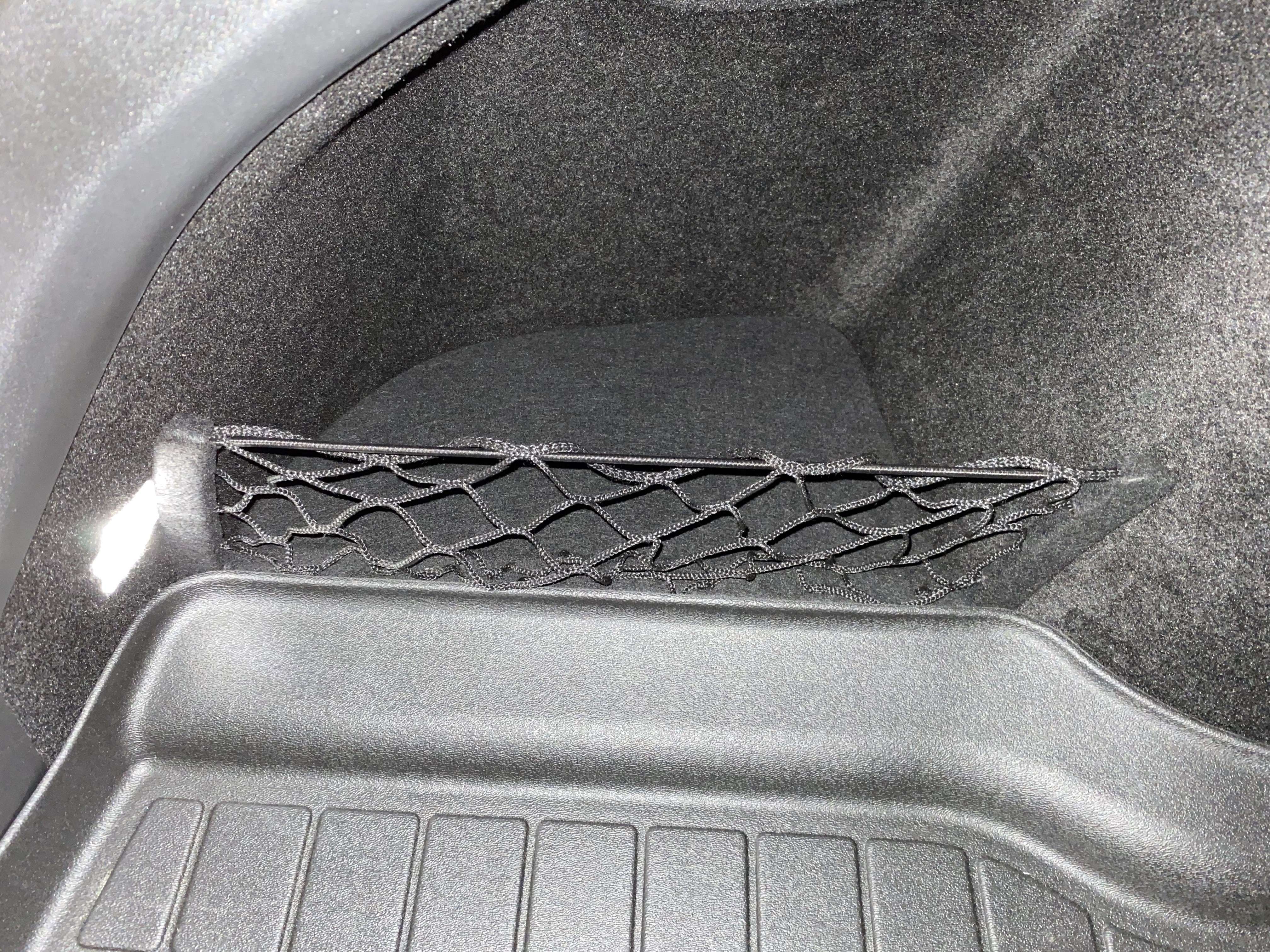
Here are links to the felt and cargo net I used:
Hard to believe that Tesla wouldn't have thought of something so obvious themselves. Nice solution - looks OEM. Good to know that felt is available commercially - could come in handy for a ton of projects.