The most time-consuming part of this project has been to get the arms cast. I spent this summer preparing a 3D printed arm model for making molds. After spending a month on sanding it so that it was perfectly smooth and making a mold, turned out it needed to be split into 4 pieces: 2 of them welded by a wax pen after casting out of wax (otherwise the mold would be impossible to make) and 2 of them welded by a welder after casting out of aluminum (otherwise it would be too large to fit in a kiln).
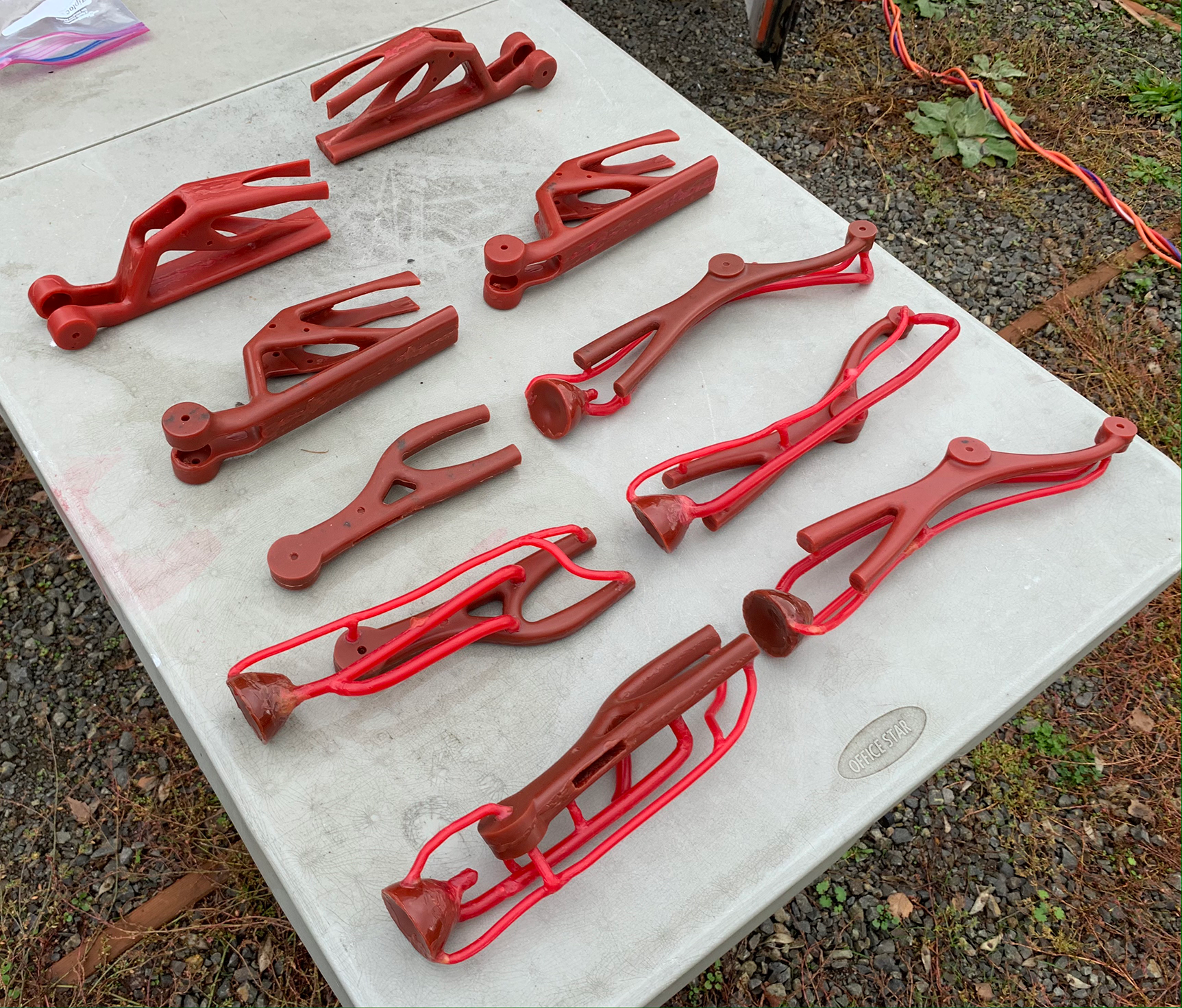
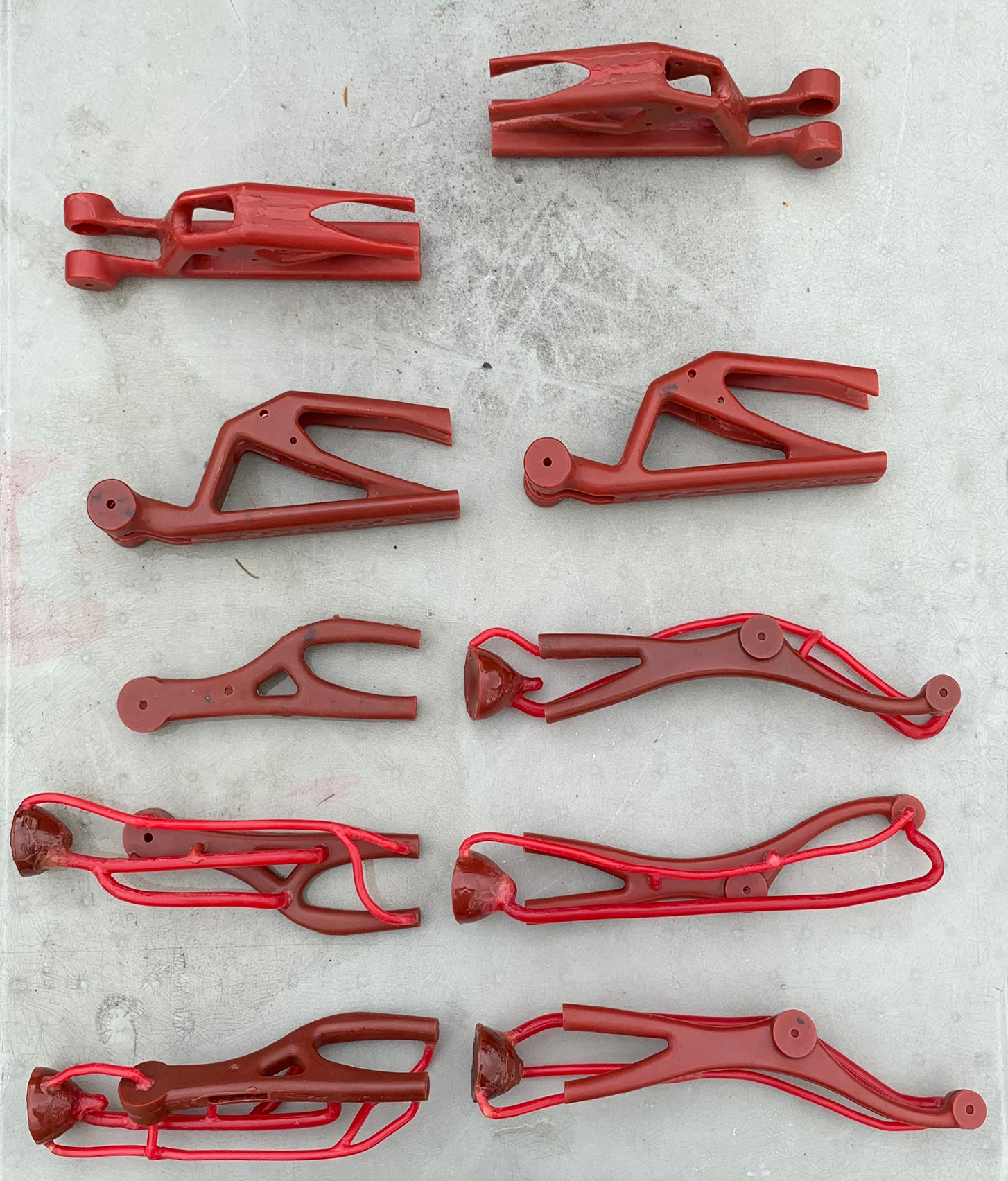
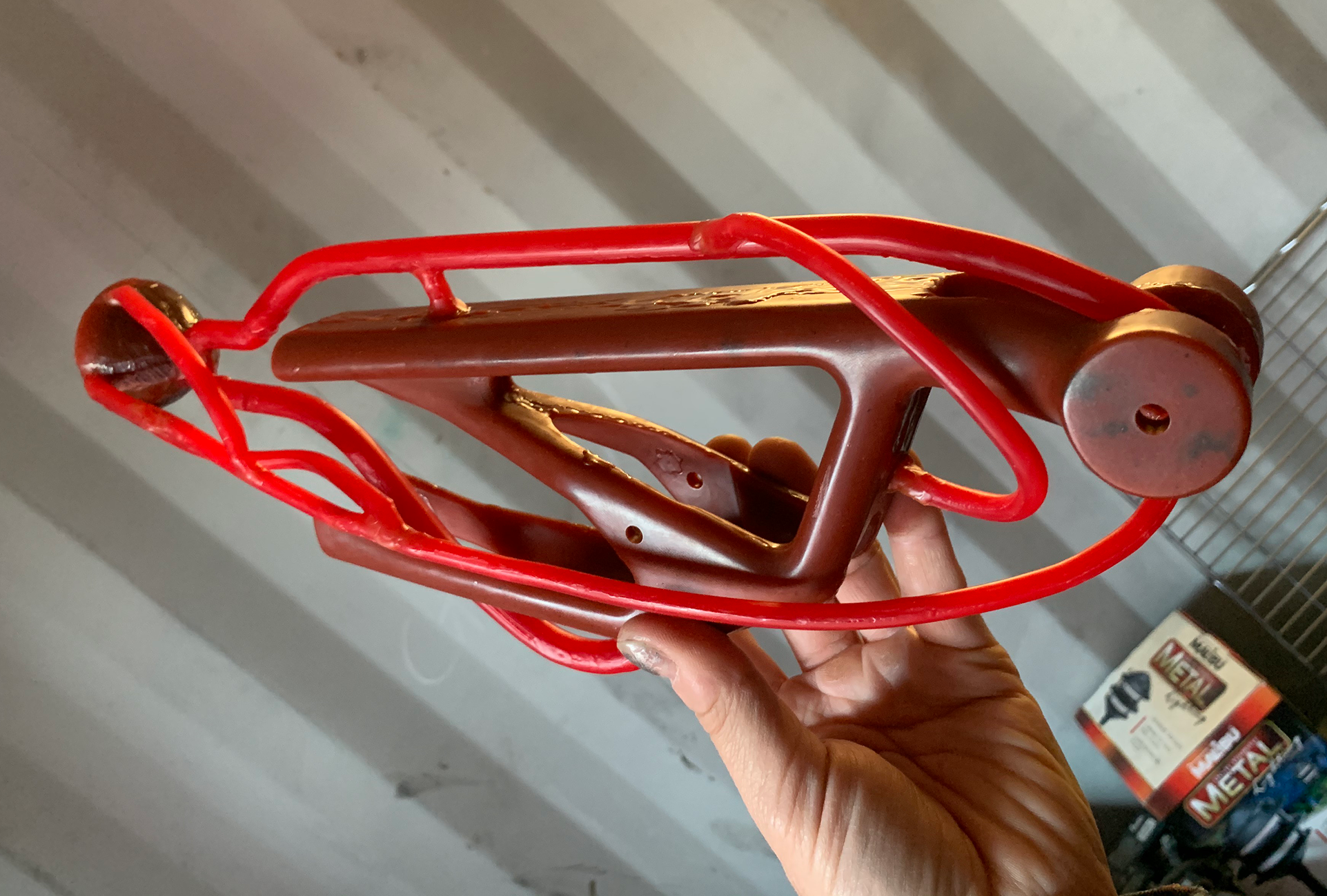
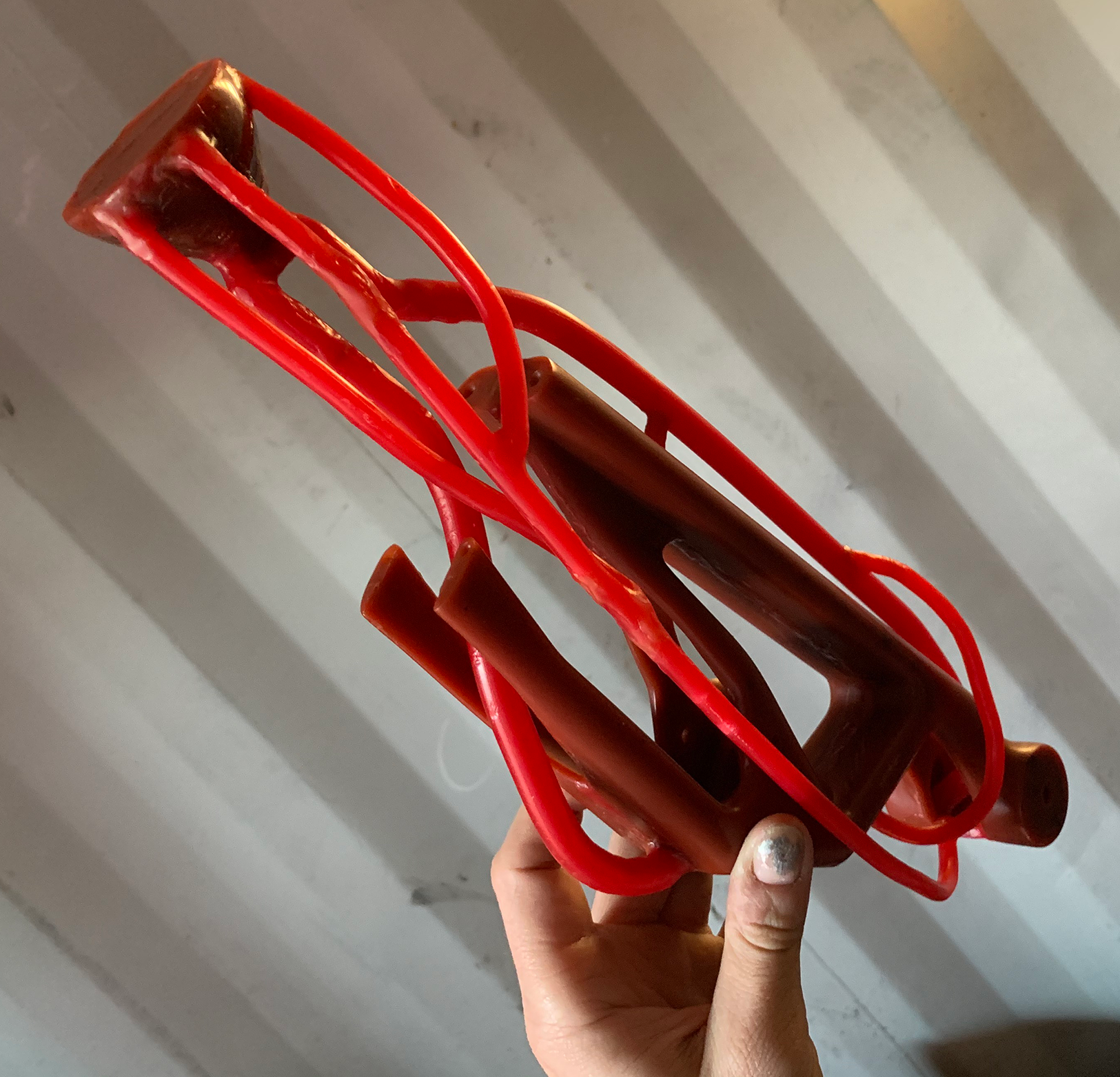
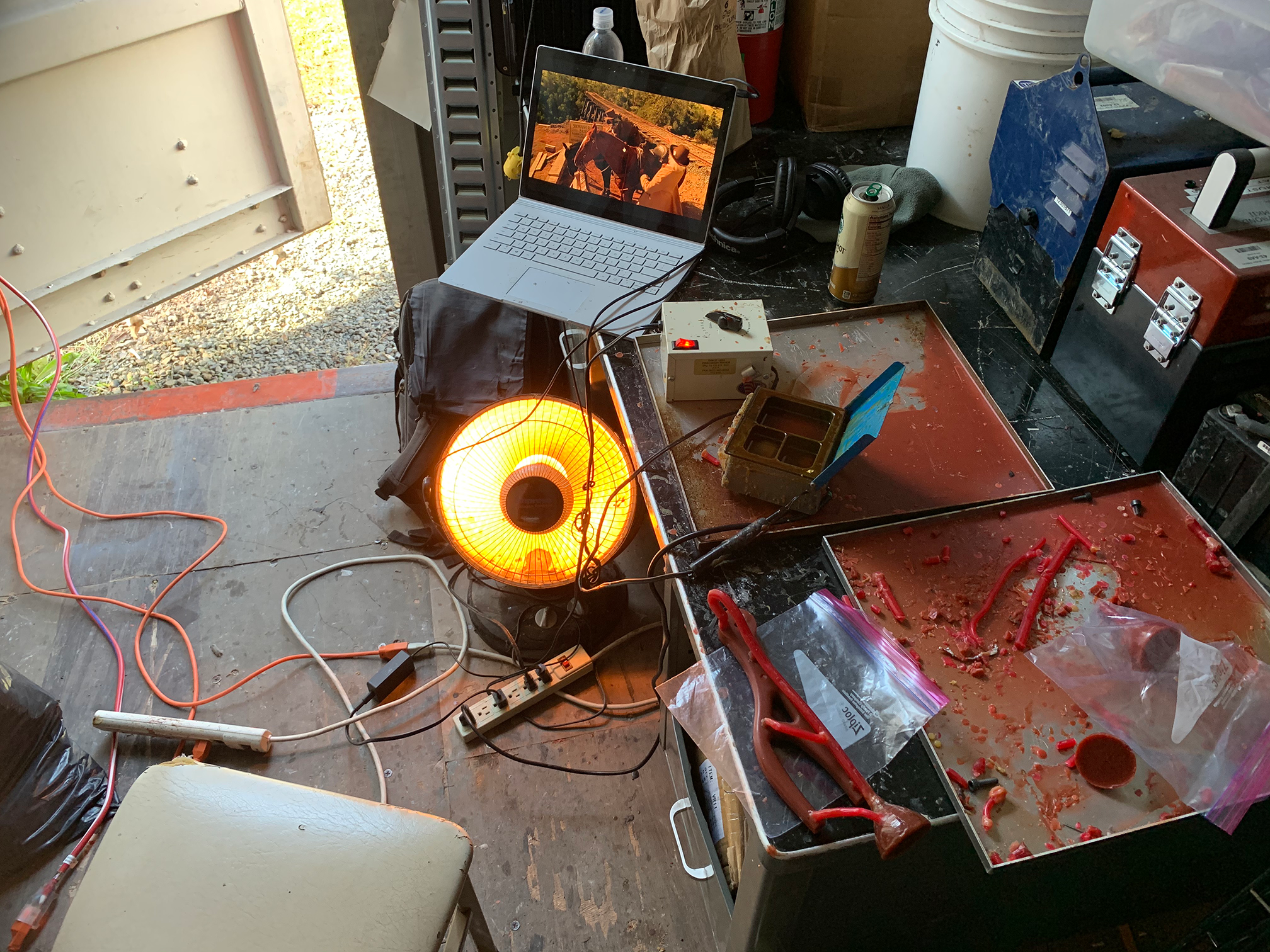
Anyway, a friend helped me prototype and re-print the models so that they were split down two perpendicular axis into quarters, then I spent another month sanding and making molds, and then another month preparing wax positives. I just got done casting 3-4 batches of wax positives for investment casting, put sprues on most of them, and I am ready to start building investment shell layers this week, maybe casting next weekend.
Discussions
Become a Hackaday.io Member
Create an account to leave a comment. Already have an account? Log In.