Example of such potentiometer is the RV112FF from Taiwan Alpha, and basically consist of two potentiometers with no end-stops and with a 90 degree phase difference.
Finally I calculate the change in value based on the direction, difference in ADC measurement (to make sure a fast turn increase value more than a slow turn) and a constant representing the sensitivity desired from the potentiometer, i.e. how many turns is needed to go from min to max value.
For my application I want to adjust the value based on relative position, so the absolute position is of no interest. If you knew what direction the shaft is being turned you could use the change in ADC value to caluclate a relative position change. But one challenge is that when the value reaches the top it goes back down again, which it also will do if you change direction exactly at the top. So you need to use the phase difference to determine if the value decrease due to change in shaft direction, or due to passing the top point. And same for the bottom point.
Additional practical challenges is that the resistance value is not linear at the top and bottom points, but have a small section of flat value, and also the noise on the signals and inaccuracies in the ADC will have the signal jump back and forth.
The algorithm I deviced first decides for each tap on the pot, lets call them tap A and tap B, what the direction of signal is (up = 1, down = -1 or unchanged = 0), and then look at the combination of the two taps' directions and the values/phase to determine actual direction for the shaft rotation. The following diagram show the relationship between direction of the signal of tap A and tap B for shaft direction Up/Increase and Down/Decrease. It also shows the relationship for the phase, i.e. if signal A is higher or lower than signal B, and if signal A/B both are is at higher end or lower end. With all this information combined I can correctly determine the rotation direction of the shaft.
Finally I calculate the change in value based on the shaft direction, difference in ADC measurement (to make sure a fast turn increase value more than a slow turn) and a constant representing the sensitivity desired from the potentiometer, i.e. how many turns is needed to go from min to max value. I primarily use signal A for this calculation, but if signal A is within the upper or lower 20% it is too close to the flat sections at top and bottom, so I change to signal B instead.
This algorithm gives a very good and stable result, and the plot below is a direct plot of the tap A (red) and tap B (blue) values, and the corresponding output value (green).
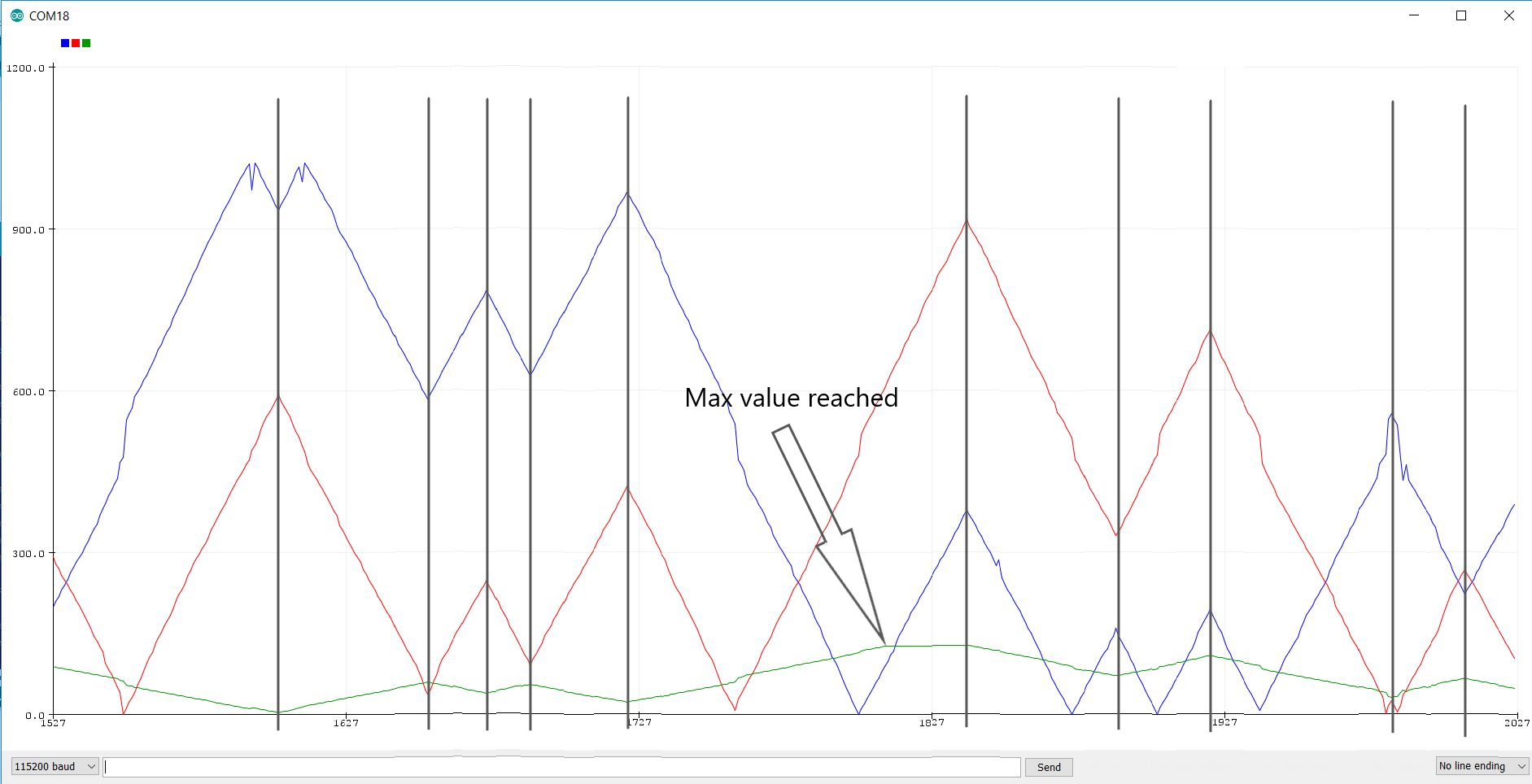
I have however observed that when the value is at zero, if I keep turning left (i.e. "decrease value") very fast, sometimes the direction will change to "increase / 1" for one cycle resulting in a small jump up in value before going back down to zero. From my debugging this seem to be due to noise on the ADC measurements, but I have not been able to fully debug it yet. The following plot is the signal when one of my fingers touched the signal B pin, and as you can see that introduce a lot of noise.
I have attached the arduino scetch for this decoding algorithm, and hopefully with the comments it should be possible to fully undnerstand its operation.
If any of you have any ideas to improvements please comment and maybe we can together refine this algorithm to be even better.
Hi Bjorn, I'm a bit late here, and maybe you've already figured it out by now. There is a simple algorithm that makes this whole process just a few lines of code. It's called atan2.
I created extensive documentation about these potentiometers on my website. It includes example code for Arduino, as well as a Max for Live device for testing.
https://connorshafran.com/endless-potentiometers
Hope this helps!