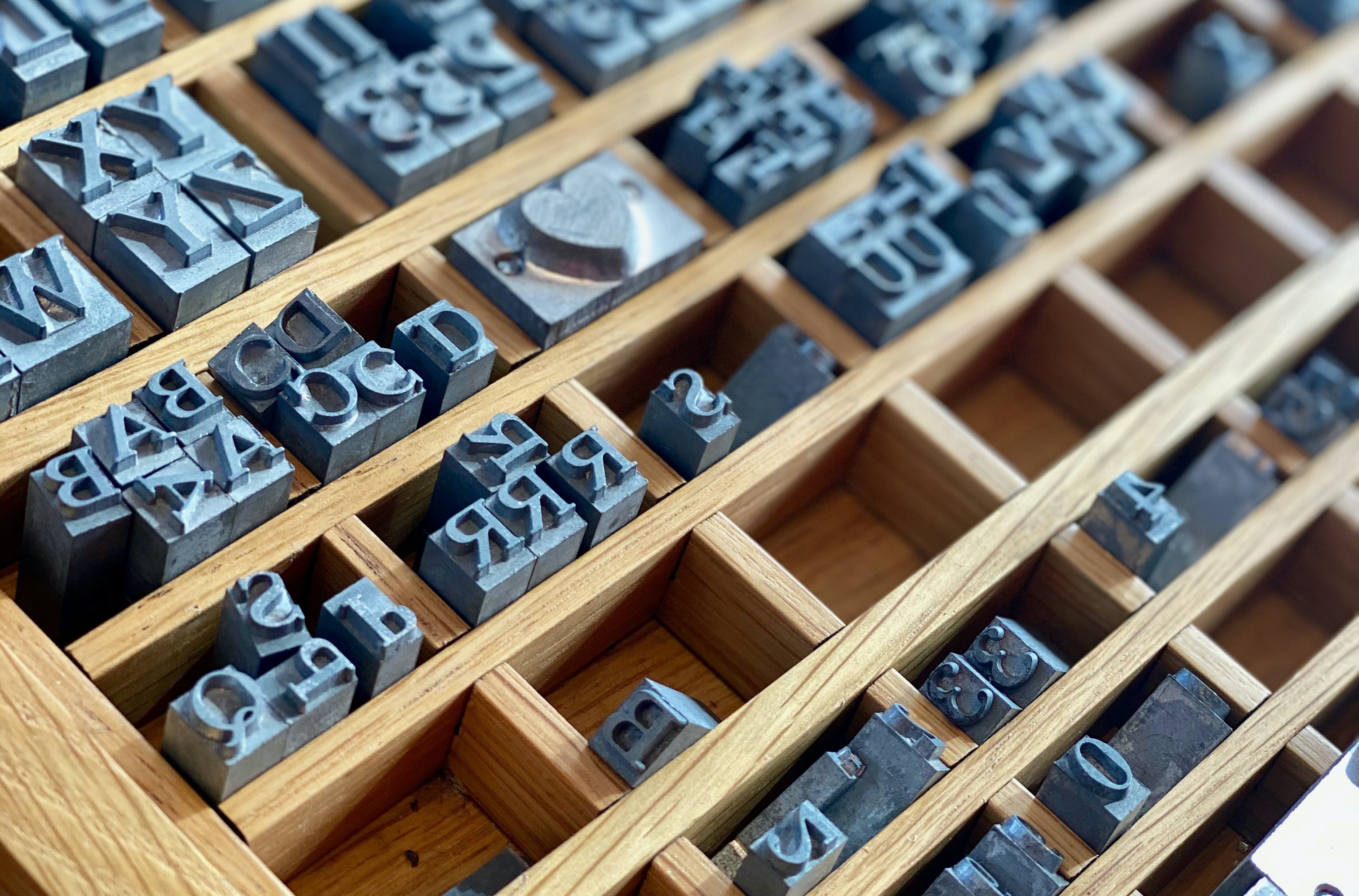
At the end of last week, we presented a selection of different options for further development under several different categories: labelling, testing, and user feedback. Today, I want to talk a bit more about one of our labelling solutions, using recycled aluminium cans for the creation of embossed metal plates and tags for machines.
To fully understand some of the ideas we’ve been having around this, I think it’s worth taking a look back in history. There are countless modern ways to mark aluminium at extremely high speed with high precision, but it’s always worth exploring simpler options in parallel to ensure that we provide the best value for our NGO, Field Ready.
With that in mind, I want to tell you all about the printing process called letterpress. In an earlier time, before digital print, letterpress formed the basis of almost all printing - way back to Gutenberg's press in 1440. So, how did it work? Well, it’s surprisingly simple. You have a bunch of physical small metal or wood blocks, each of which has a single raised letter on one side of it.
These metal blocks are known as ‘type’. They are stored in cases like the image above - hence the origins of the word lower case and upper case - the capital letters are stored higher up, as they harder to use, and the small letters are stored lower down! By taking these placing these snugly together in a frame, you can form words and, with the help of some blank spaces, full sentences or even pages!
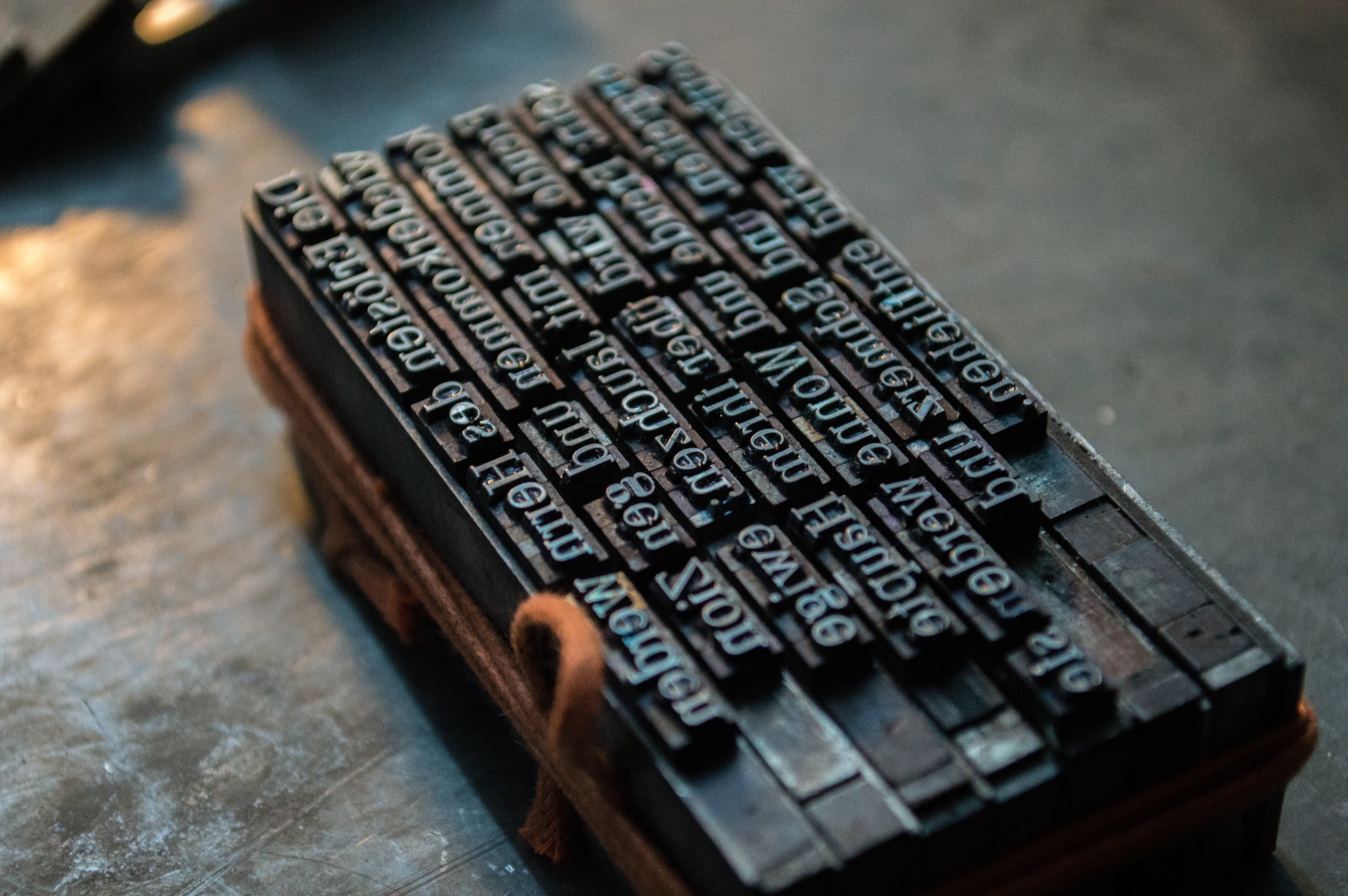
Once you have these letters aligned in a frame, you can pop them, bumpy side up, into a printing press (just a roller on top of a flat bed). Roll some ink on the type, then pop a sheet of paper on top. Move the roller over the sheet to press it into the paper, and you’ve got printed words on paper (and probably a couple of typos if you’re new to the process like I was!)
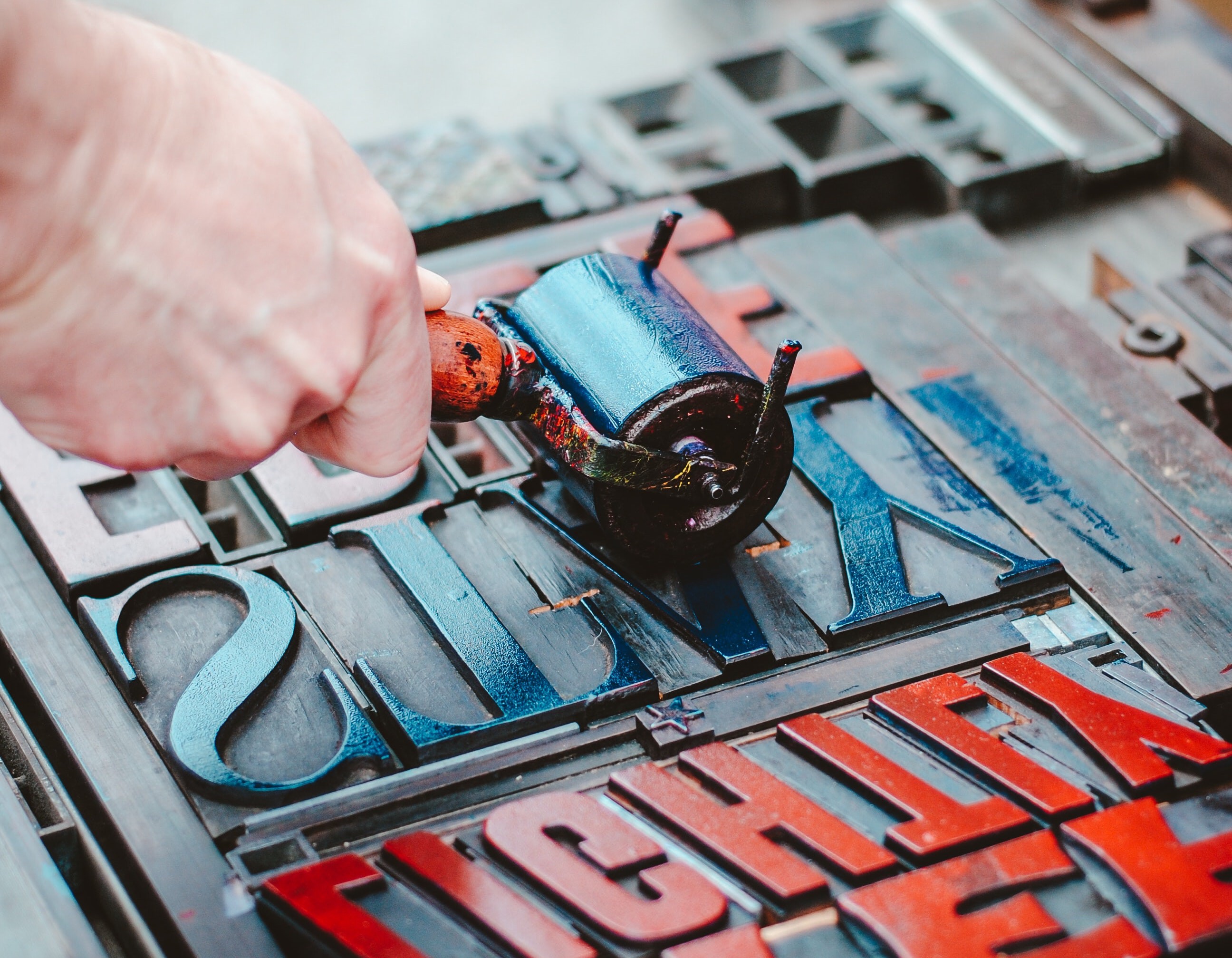
Now, you may be asking - how does this process of printing ink on paper connect to embossing text onto aluminium? Well - sometimes when you’re printing with letterpress, it’s possible to misalign the roller height and physically push the paper into the type. This has the effect of debossing the paper. If you do this without ink, you’ve just made a reasonably visible impression without using any consumables, and there’s no reason to suggest it wouldn’t work with aluminium either. There will be more in my next log on our experiments with this process and others!
Discussions
Become a Hackaday.io Member
Create an account to leave a comment. Already have an account? Log In.
A very interesting article, some of the facts I have not heard. It's amazing how in those ancient times they could develop such a printing technology. Moreover, it is so successful that it is still used today. I used to study old prints in college. I even wrote a small study using this resource https://graduateway.com/essay-examples/technology/ for students. It was a very time-consuming process. At one time, the creation of one book required months of work, special skills, and accuracy. Not like now, everything is done by the machine.
Are you sure? yes | no