tl;dr: 12x
So far I've run the same "feeds and speeds" as the prior project just to get things working. Lately I've tried pushing a little harder.
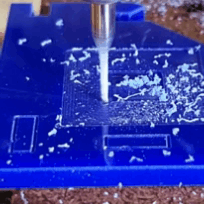
#CDCNC can manage extremely conservative cuts with a 1 mm end mill. Typically 0.15 mm step-down, 40% step-over, and nominally[1] 500 mm/min feed. That yields a material removal rate (MRR) like the material addition rate of grass growing. Numerically, 0.03 cc/min or two seconds per microliter. This machine should be able to do better, but I hadn't tried much beyond an early stab at cutting deeper. Until eventually I got around to trying.
Results
(summary below video)
More briefly:
- 3x feed rate: 500 -> 1500 mm/min
- 2x depth of cut: 0.15 -> 0.3 mm
- 2x stepover: 40% -> 80%
Those gains multiply out to 12x MRR in a straight line.
I think it's fair to call that "faster".
Feed
The X & Y maximum "rapid" motion speed capped the feed rate. In other words, the machine cuts at g0 speed. In other words, "rapid" isn't very.
On one hand, that limit has floated around pretty conservative numbers while sorting other faults and may hide some more available speed. I didn't try.
On the other hand, the 0.5 mm pitch lead screws have to spin pretty rapidly to produce "rapid" motion and the top end of that may be not very tall. That's the trade for useful axial thrust from 15mm can-stack steppers. At 40 steps/mm and 8x microstepping (iirc what worked best when I poked at that a couple years ago), a diagonal 1500 mm/min "rapid" eats 16k step pulses/second. Doubling that would exceed Grbl's nominal max pulse rate (unless that's per axis?). All assuming sufficient torque at whatever speed. So if the motors have potential to make torque faster, the microstepping may need review.
Speed
I've been running the dremeloid rotary tool at minimum speed to avoid rubbing at slow feed rates. Except that's not really how it worked. A major part of the prior project was pushing up the feed rate to escape from rubbing at the minimum spindle speed. Either way: minimum speed. About 10,000 rpm but spontaneously and seemingly randomly variable in some range. Increasing the feed rate made opportunity to try dialing up the spindle speed. About that:
- MRR
- For shallow cuts, the machine can do fast feeds (thicker chips) at minimum spindle speed.
- Faster feed does enable faster spindle speed. Up to maximum spindle speed at maximum feed. The spindle maxed out at 29,000 rpm. Tripling the spindle speed at triple the feed rate seemed like a reasonable thing to try and it did work agreeably well. I didn't look for a minimum feed for maximum speed
- Faster speed enables more aggressive step-down and step-over at high feed rate.
- Surface finish
- tl;dr: better. Prior logs show a history of variably imperfect surface finish quality for flat face cuts, with evidence of vertical oscillation in Z. And the tool never sounds really right at min speed but smooths out at higher speeds. Apparently min speed allows something to rattle axially, apparently somewhat coupled with radial loading, which apparently shows up in the cutter path. That calms down at higher speeds (the internal fan makes enough thrust to preload the bearings?) and cut surfaces look and feel much better.
- Noise noisenoisenoisenoise
- At minimum speed the sound, while qualitatively rough, doesn't overwhelm. While the sound smooths out with increasing speed, it also picks up strong tonal peaks that make it unpleasant if not crazy loud. At max it's just #!%&$☆ loud. Earplugs (you were already wearing eyeball protection, right?), pre-emptive apologies and short runs. Apart from max MRR attempts, mid-range spindle speeds turn out decent results and there may be a sweet spot. tbd.
Depth of cut / step-down
Not a strength. Trying that first (see first log entry) didn't encourage me to try more of this earlier. Doubling the step-down helps MRR but it's still just 300 microns. Subjectively, it seems like the machine has to work a lot harder to cut a little deeper. At this point in development, I don't expect to adopt 0.3 mm step-down as the new routine. Especially if running the spindle at less than max noise.
Deflection
With more aggressive cutting, tool deflection becomes a thing. Especially considering that the first segment of the first loop of an area clearing operation is a 100% full-width slot. At 80% step-over, just 0.2 mm deflection breaks overlap with the returning segment. And since the non-overlapping return becomes it's own slot, just 0.1 mm deflection of each slot breaks overlap. Note the very thin but neatly uniform strip left in the center of the last example in the video.
Also, with conventional milling, the tool deflects "the other way" vs climb milling. So those two paths deflect away from each other instead of into each other. (Now I wonder what evils magically disappear in climb milled operations...)
I think the opposite-handed deflection answers the mystery of the "depressed/offset patches" in the test pockets described a couple of entries back. Those are where the area-clearing operation degenerates into slotting between the central figure and the pocket wall. The tool deflection increases slightly when it becomes fully engaged in the slot. With the switch to conventional milling, the opposite-handed deflection pushed the tool towards the center of the central figure. That and a tollerance stack-up with a slightly thin rod in a slightly big bearing, but that will (may) be another entry.
Also, making the Z axis a 3rd copy of the X & Y axes was simply expedient. It is artificially less stiff than it could be. And I've had some time to think about how to make it more different from the horizontal axes.
[1] I say "nominally" because that's the number I used in CAM to generate toolpaths, but then I adjusted that to find what worked. So CDCNC almost never maintained 500 mm/min but more often 350-400ish. If I remembered what feed I actually ended up using for the better example pieces, I could probably compare with a lower baseline and claim greater speed-up. But for this project I've mostly used 500 mm/min unadjusted so this compares with earlier work on this machine without considering the maybe 20-40% gain that already represented.
Discussions
Become a Hackaday.io Member
Create an account to leave a comment. Already have an account? Log In.