A trackstar finally began its new life as a 360 stepper motor.
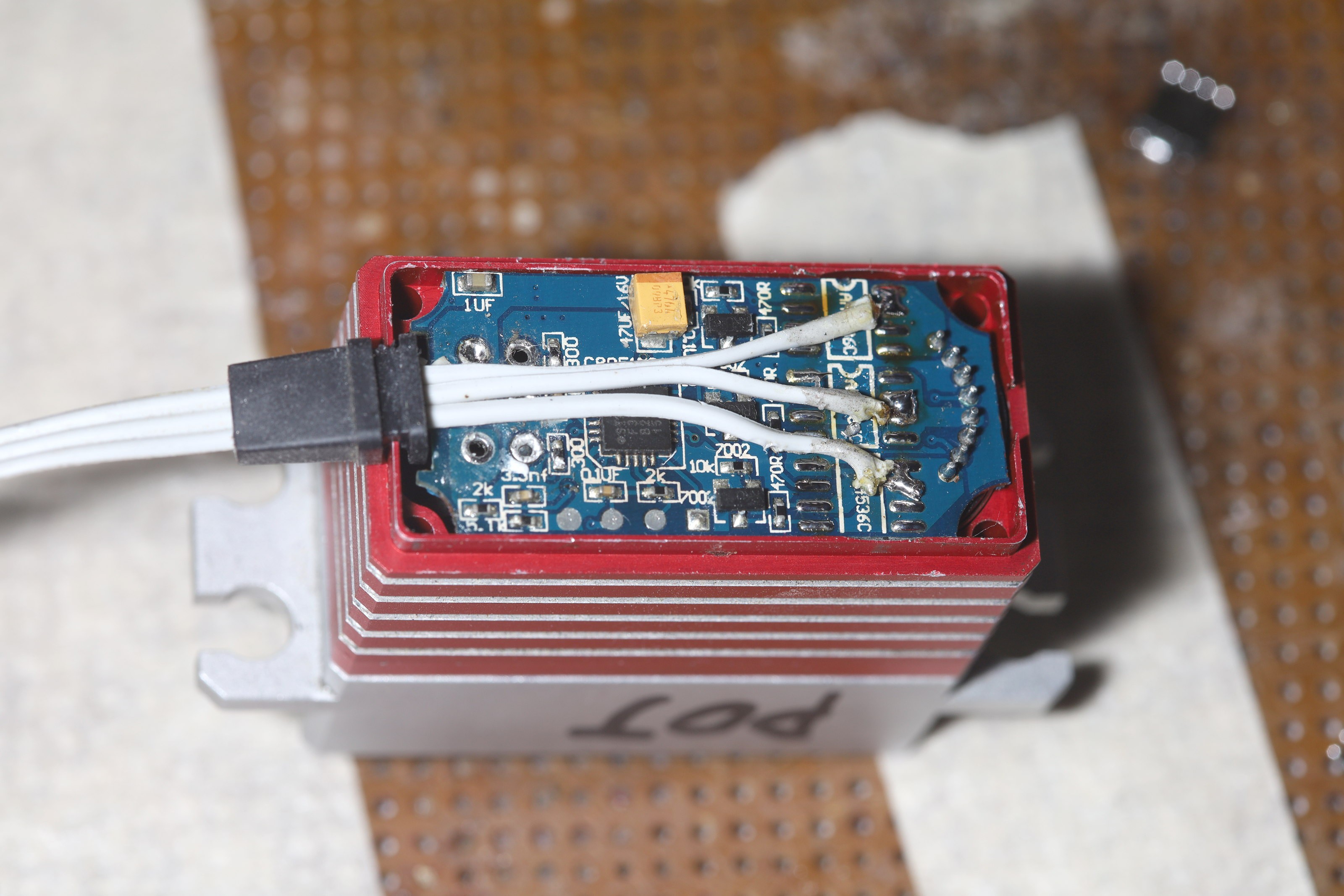
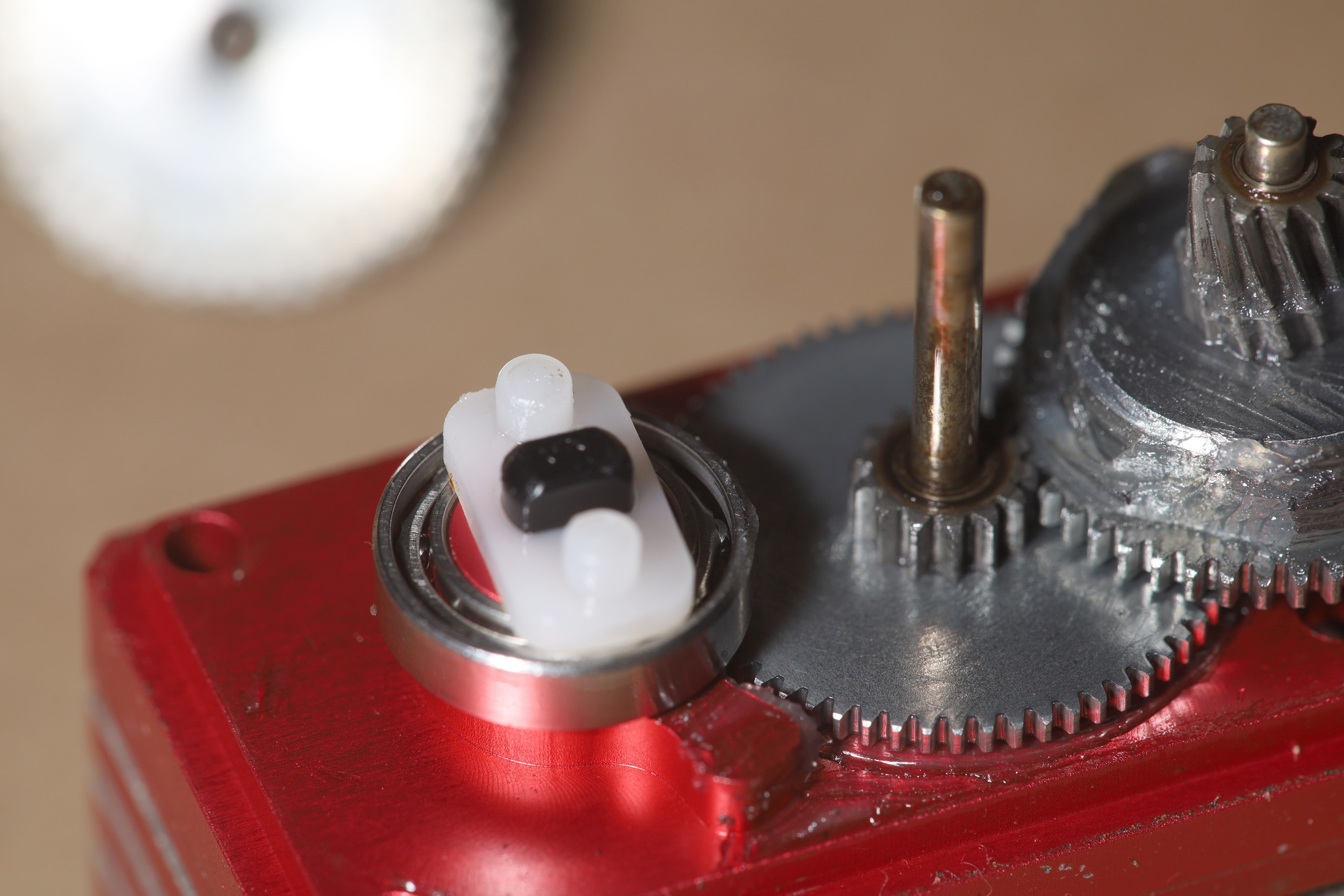
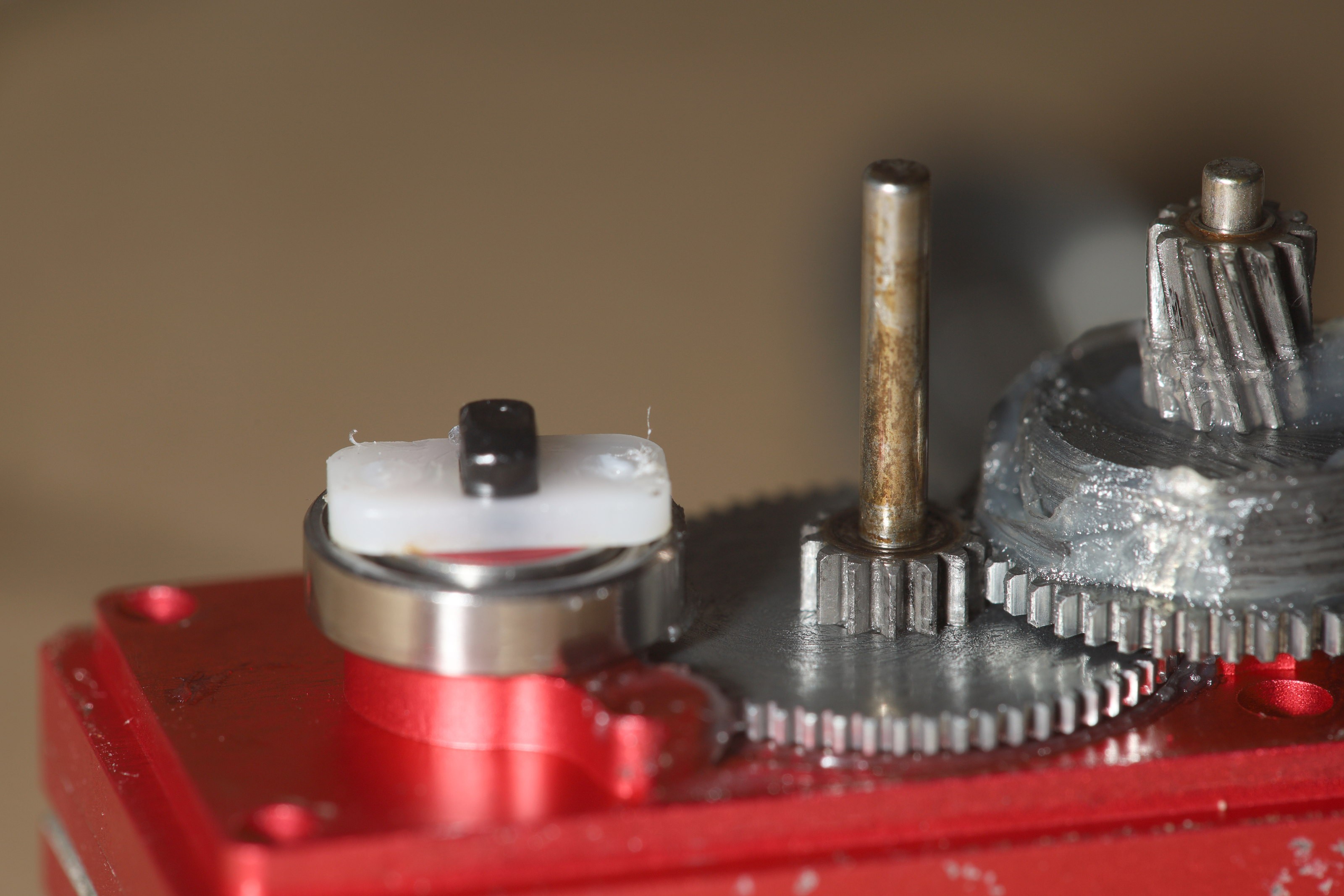
Then came chopping off the encoder lugs.
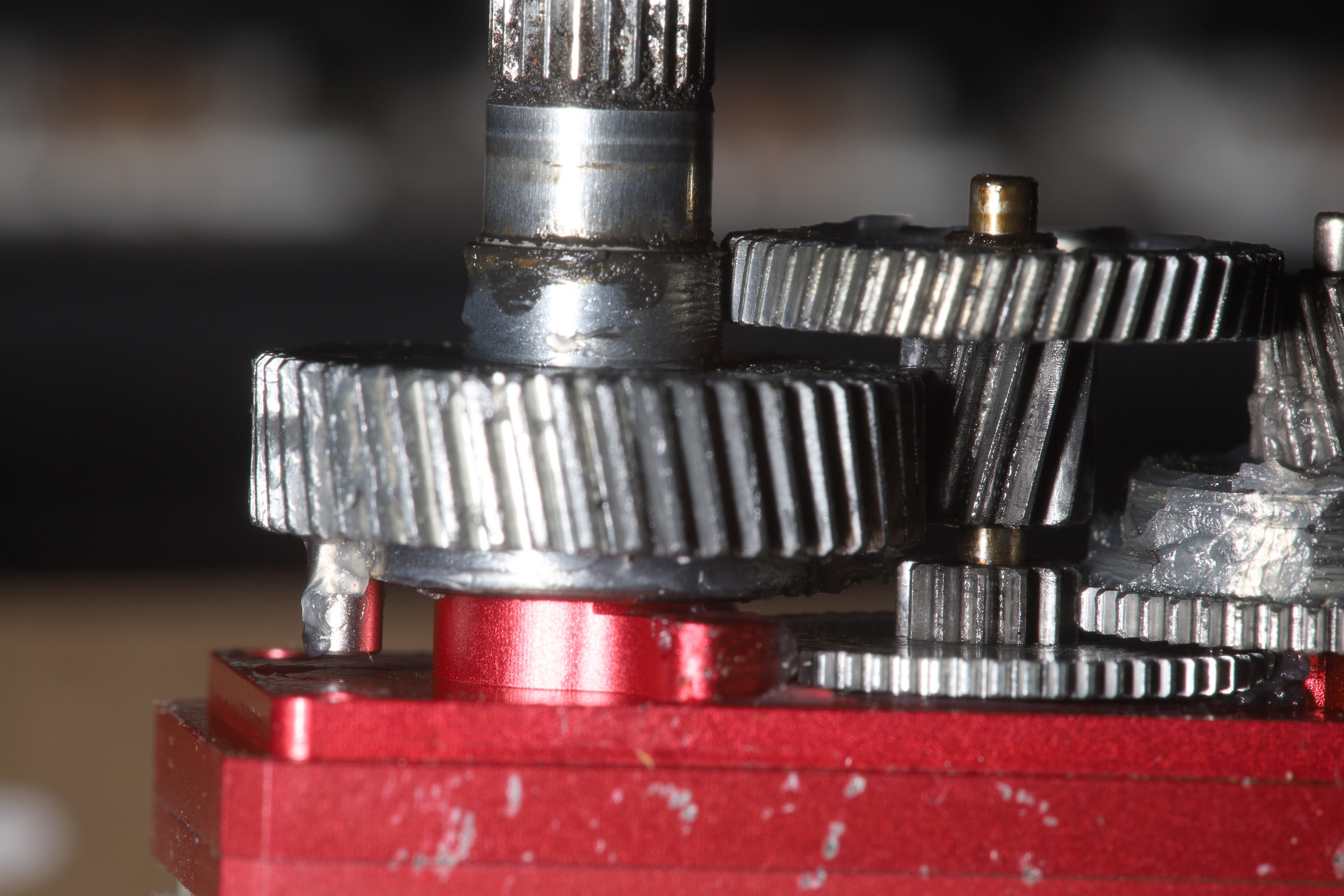
Then came grinding off the titanium stopper. The gears got cleaned & relubricated.
As a stepper motor, it needs to commutate really fast to get 1 revolution every 4 seconds.
At 5V, it burns 500mA. At 6V, it burns 1A & gets hot. Its key advantage is it doesn't need to be powered to stay in 1 place. Timelapse mode still requires the full current, so it can't be given the 1A. The standby current when it doesn't move is 50mA. It doesn't have as much torque as the stock servo.
A new servo mount was printed.
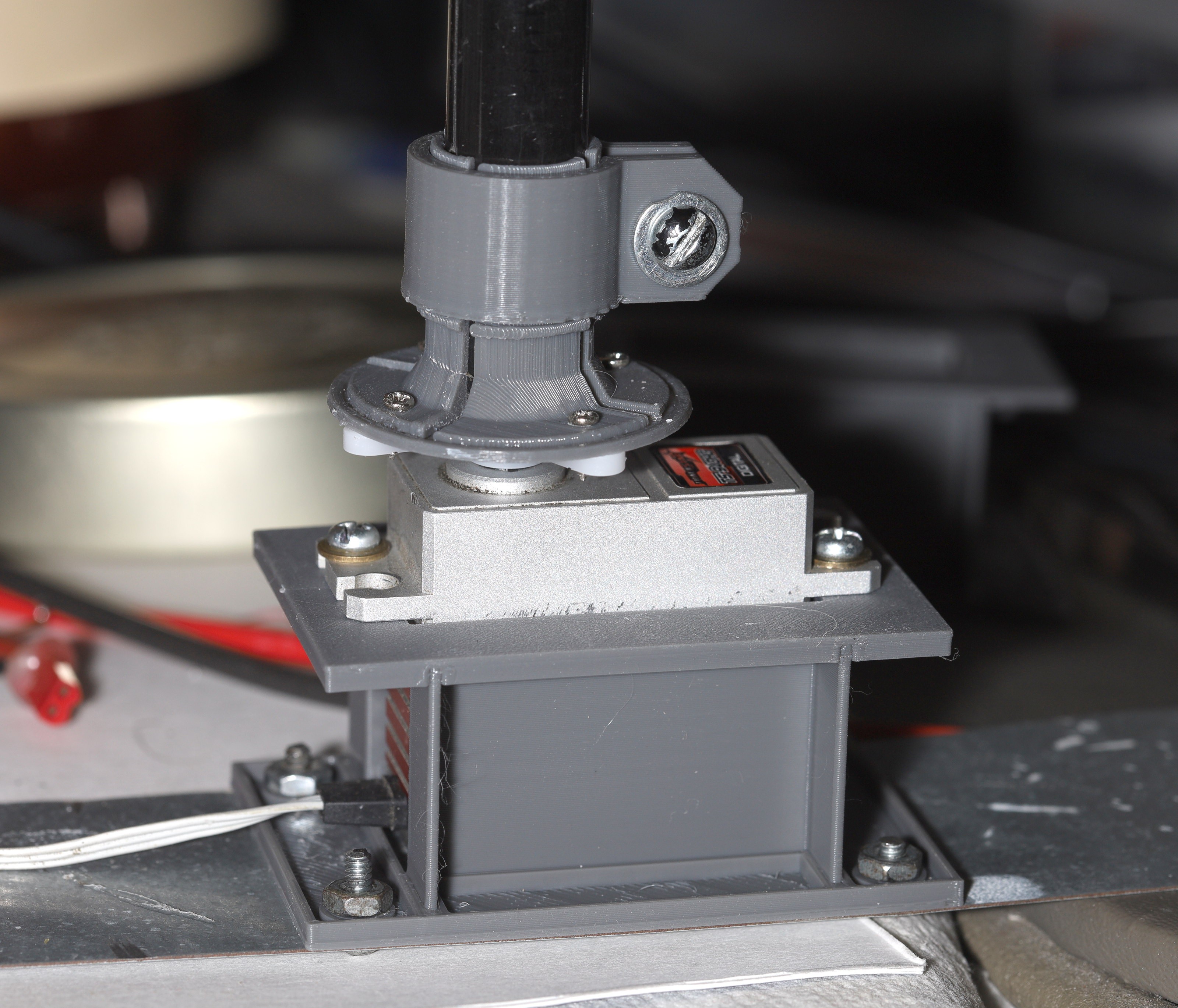
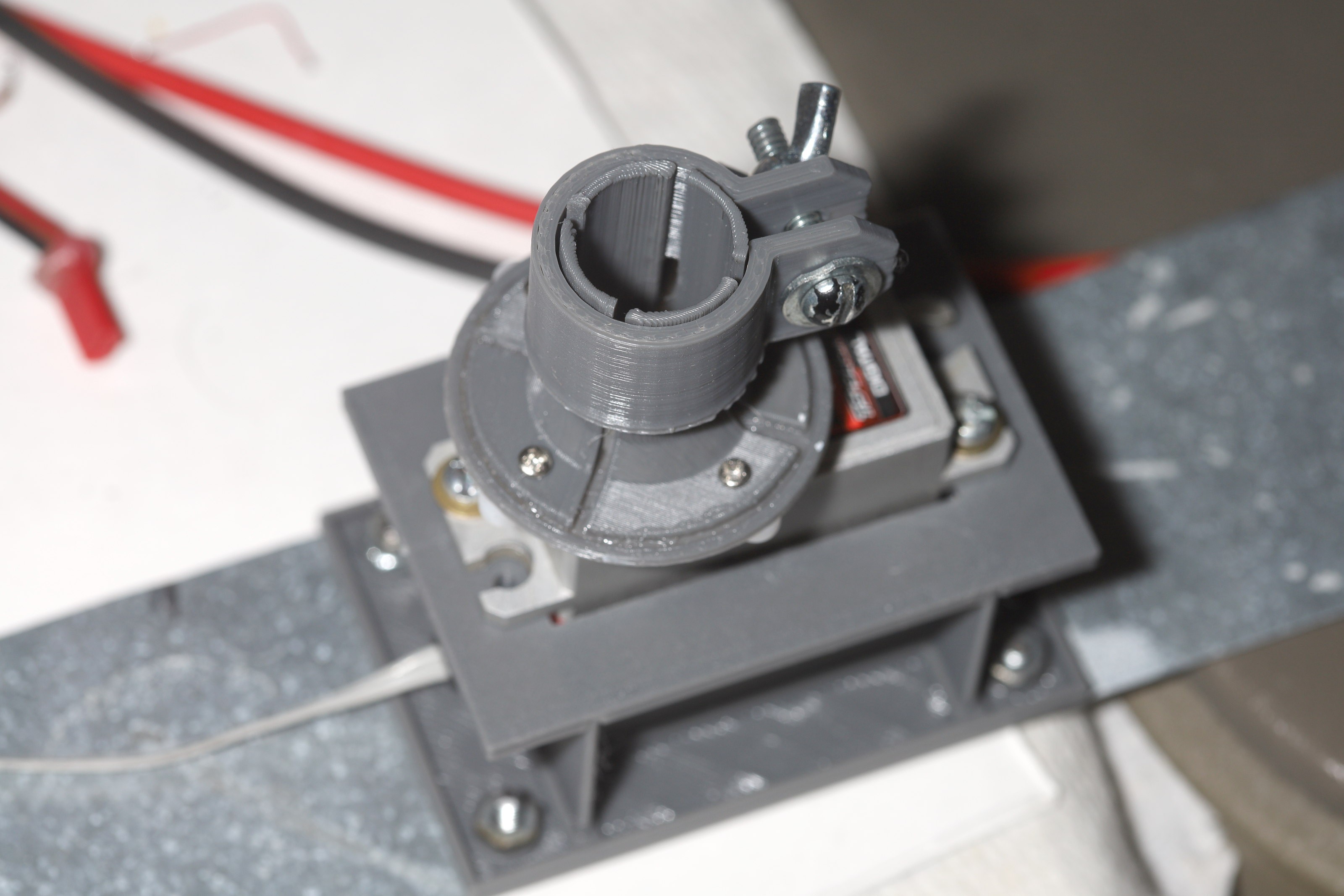
The carbon fiber adapter evolved to be more flexible & use less material.
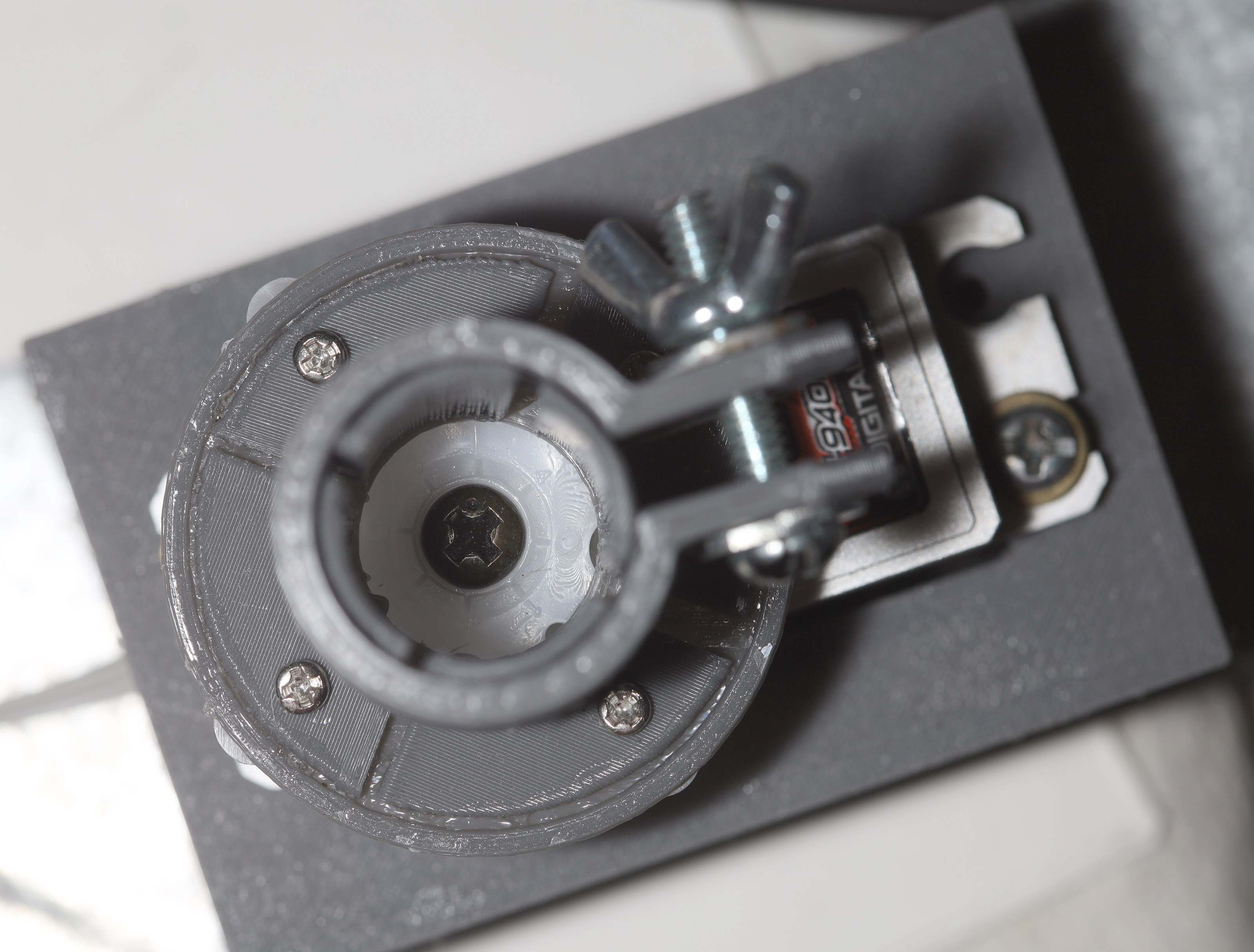
Servo must be screwed in before carbon fiber. There should be enough torque for clothing to not jam the rotation, but you never know.
While this turns very smoothy with very little power, it's still a horrible design. It uses an L6234 for the previous motor to directly drive the servo motor, even though the servo already had the electronicals for driving the motor. It would save a lot of space to reprogram the servo to do all the motor control & have a much smaller board outside just read the radio. The mane compromise was to give up empty space for less time programming.
The C8051F330 in the servo can be programmed with an arduino & the pads are pretty obvious.
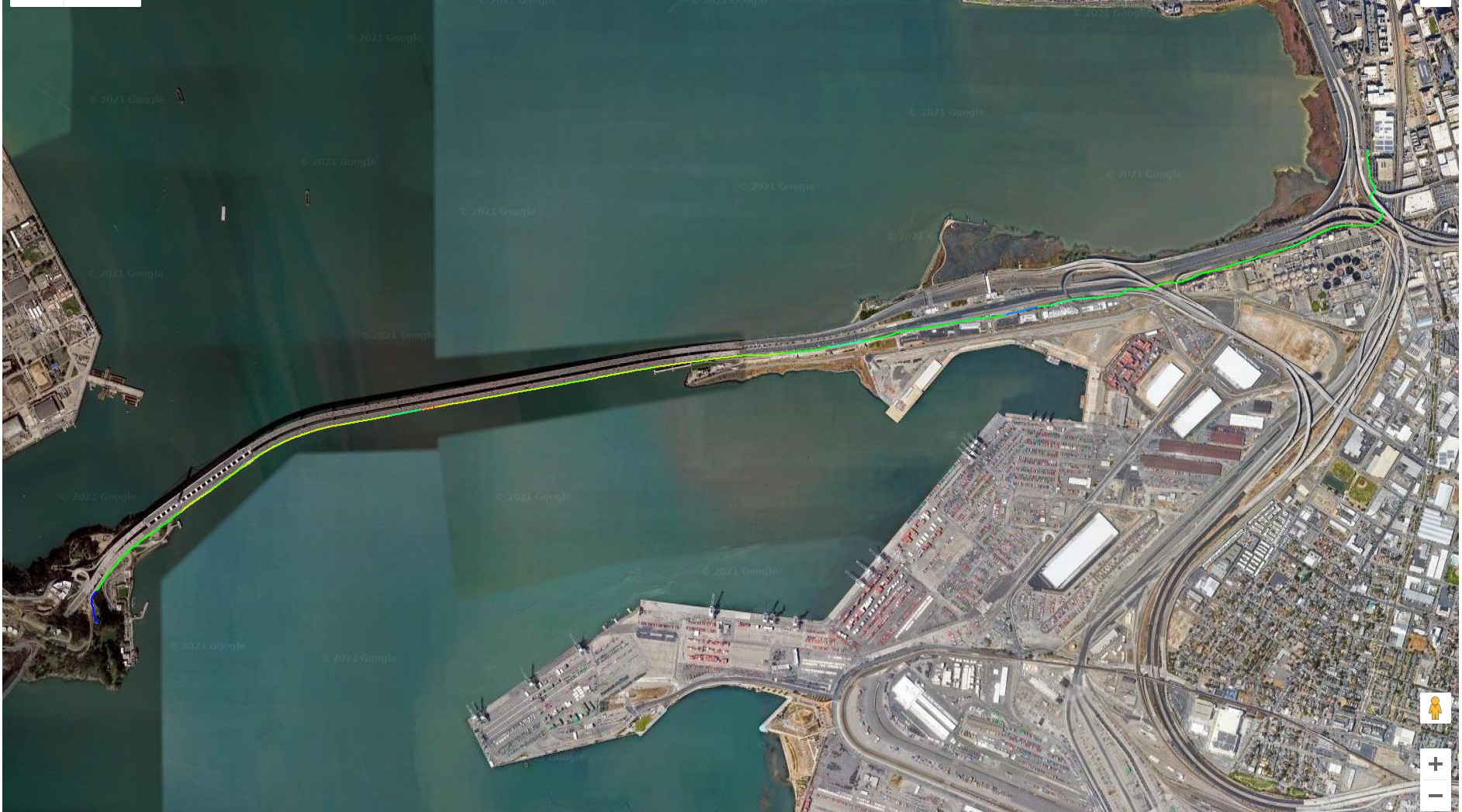
It easily did 7 minute miles going downhill, with the wind. The lion was wiped out after only 2 miles at this speed. The full 20 minutes considered a tempo run were at 7m34s/mile downhill, with the wind. It was disappointing.
There was renewed jamming of the radio by phone towers, despite all the amplification. These phone towers may have been closer. There's only so much amplification a lion can afford.
Then, the new panning servo raised the camera a hair, which caused new oscillations. It got underdamped surprisingly when driving over raised paint.
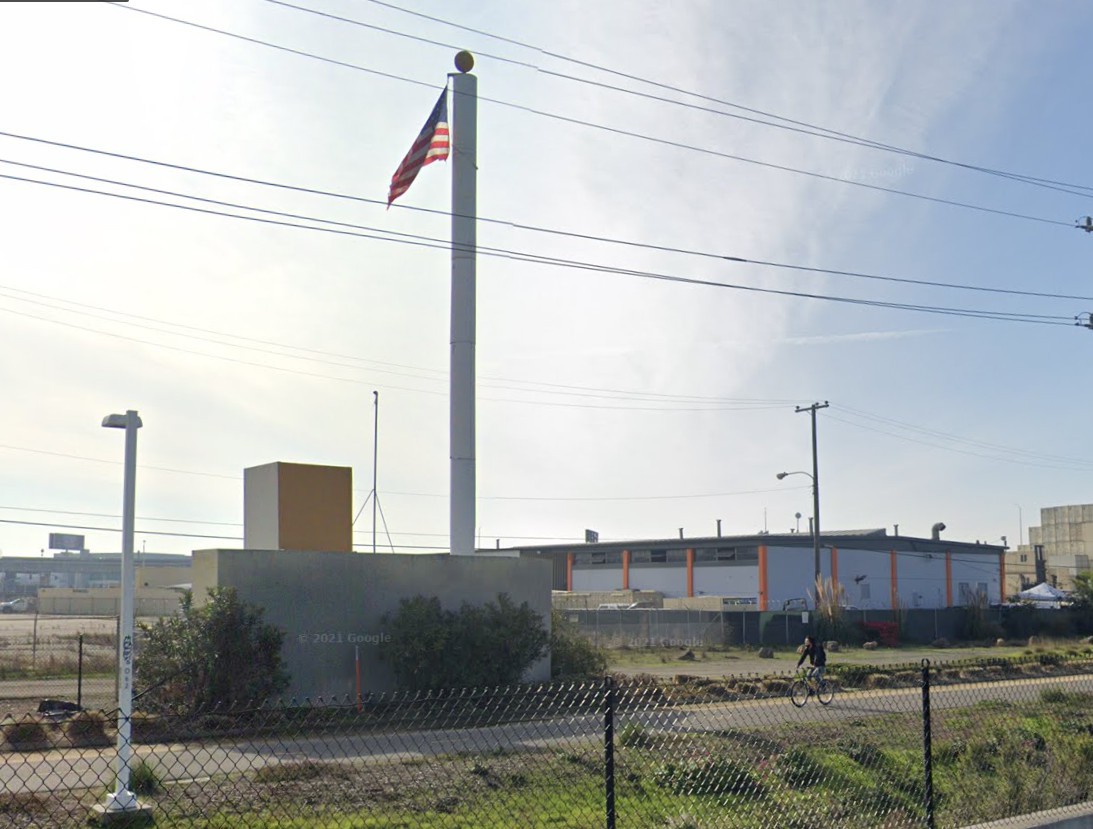
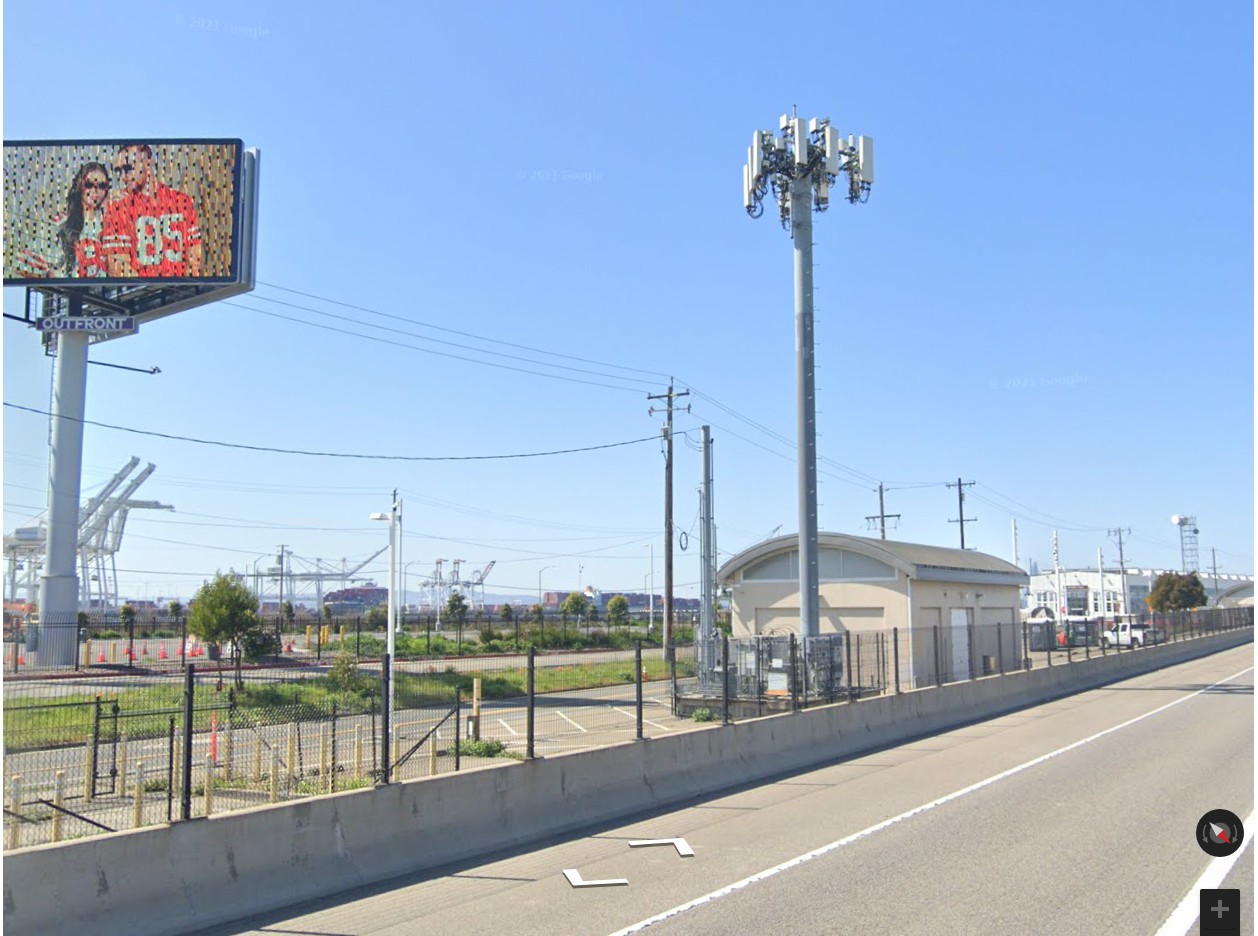
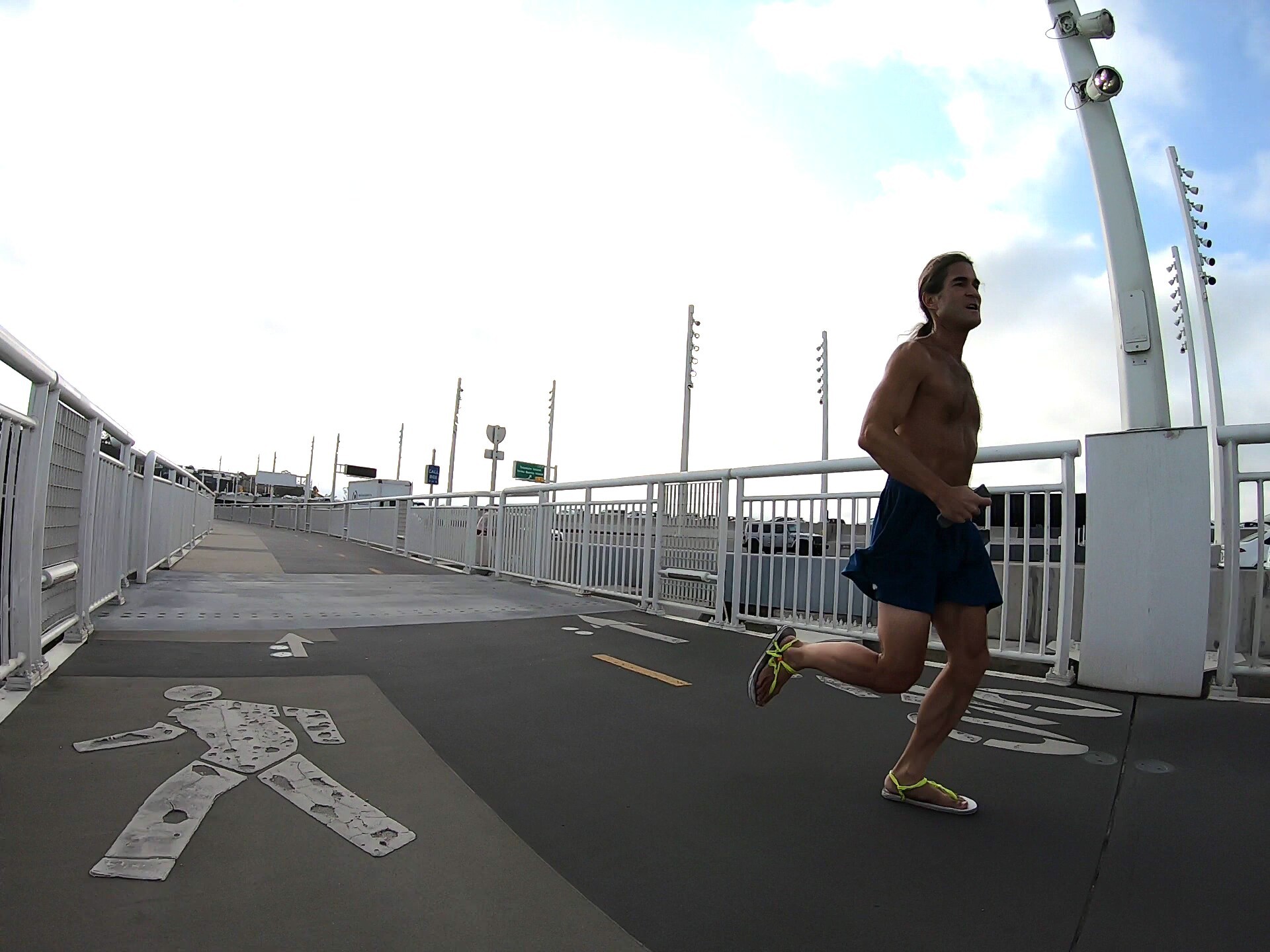
Discussions
Become a Hackaday.io Member
Create an account to leave a comment. Already have an account? Log In.