The servo started locking up again after only 700 miles, always in the same place. It was another case of static electricity. This time, nothing was rubbing in the wheel wells. It's believed to still be static electricity, but lacking a definitive source, the focus turned to where the potential difference could be occurring. There are the aluminum angle rods. It's believed a potential exists between the aluminum rods & the battery ground so some jumper cables were put in.
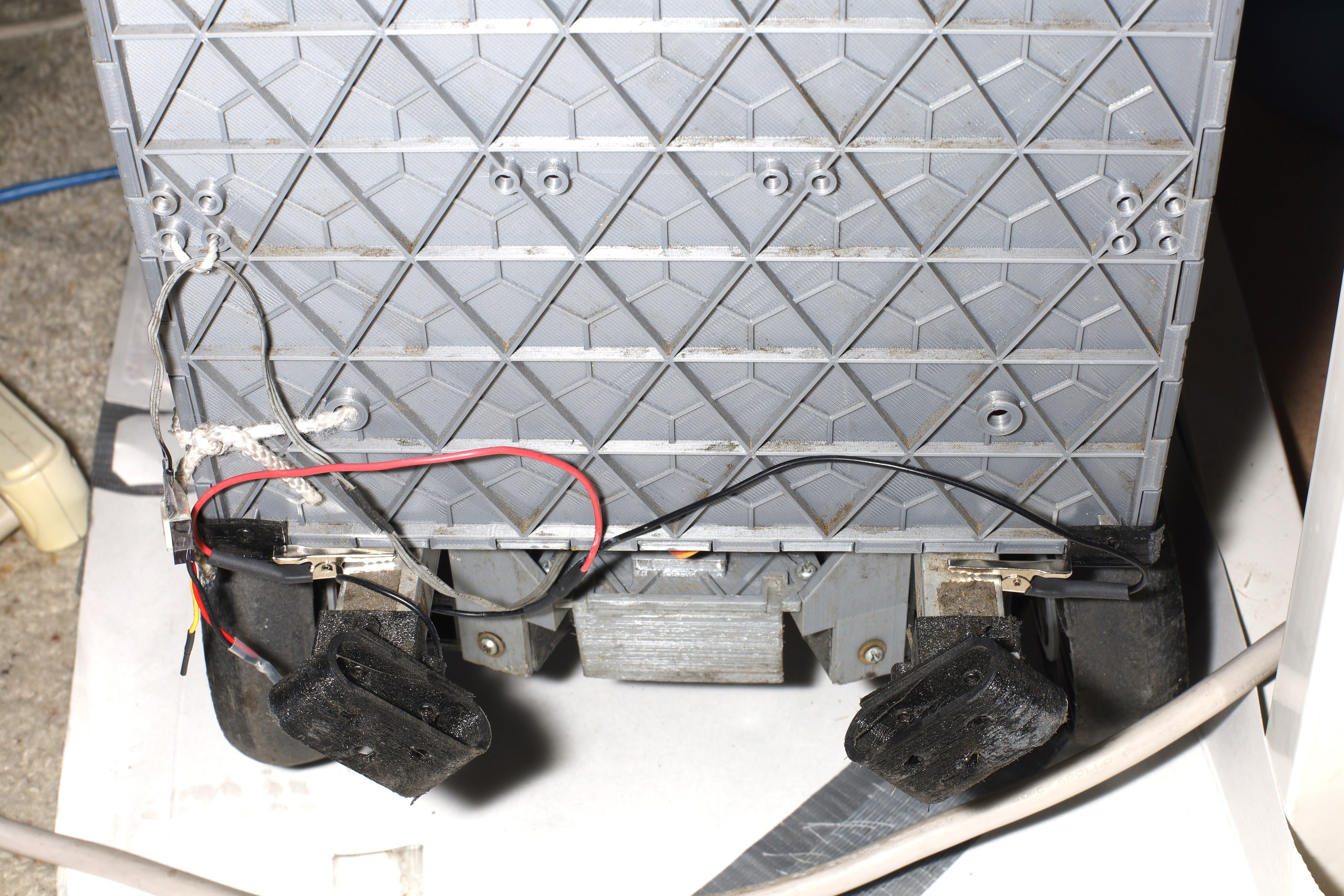
It immediately became obvious that getting good conduction with anodized aluminum was hard. The anodized layer is actually very resistive. It's not easily conducting with the motor driver ground. Only heavy scraping with the probe got a continuity beep. That resistance makes anodized aluminum prone to static discharge. It's believed to discharge into the motor driver ground, which causes the mane board to briefly have a large negative voltage.
The grounding straps did nothing & attention turned to the wheels. Maybe the TPU gaskets build up static electricity as they rub against PLA. A potential would develop between the stationary motor parts & the rotating motor parts.
Eventually, static discharges into the motor windings. Static discharge in motors is well known & manely happens in spaceships. It causes fluting of the bearings & failure of control moment gyros. They usually need a shaft grounding ring.
Creation of static electricity by rubbing materials is called the triboelectric effect.
https://en.wikipedia.org/wiki/Triboelectric_effect
No-one really knows why rubbing some materials creates static electricity while others don't. It's assumed 1 material has to be an insulator because 2 conductors would discharge when they touched. 1 material has to be an electron donor & 1 material has to be an electron receiver. A vandegraaf generator transfers electrons from an acrylic roller to a rubber belt. It doesn't rub anything. Electrons flow from the metal sphere to the brushes to the acrylic roller to the belt. The brushes transfer electrons through the air. The - charged belt deposits its extra electrons on a metal roller.
There's a table of electron donors & receivers. Polyurethane of TPU fame is shown as a good electron receiver. PLA would have to be a good electron donor based on observations. The outside of duct tape would have to be a good electron receiver based on observations & sure enough, duct tape is covered in polyethylene. Acrylic is a good electron donor. Some metals create charges. Paper & wood are bad generators of charge. Theoretically, rubbing 2 identical materials doesn't generate a charge.
A return path from the chassis to the wheels is needed, no matter what. Maybe using identical materials for the motor shroud & gasket would reduce charge.
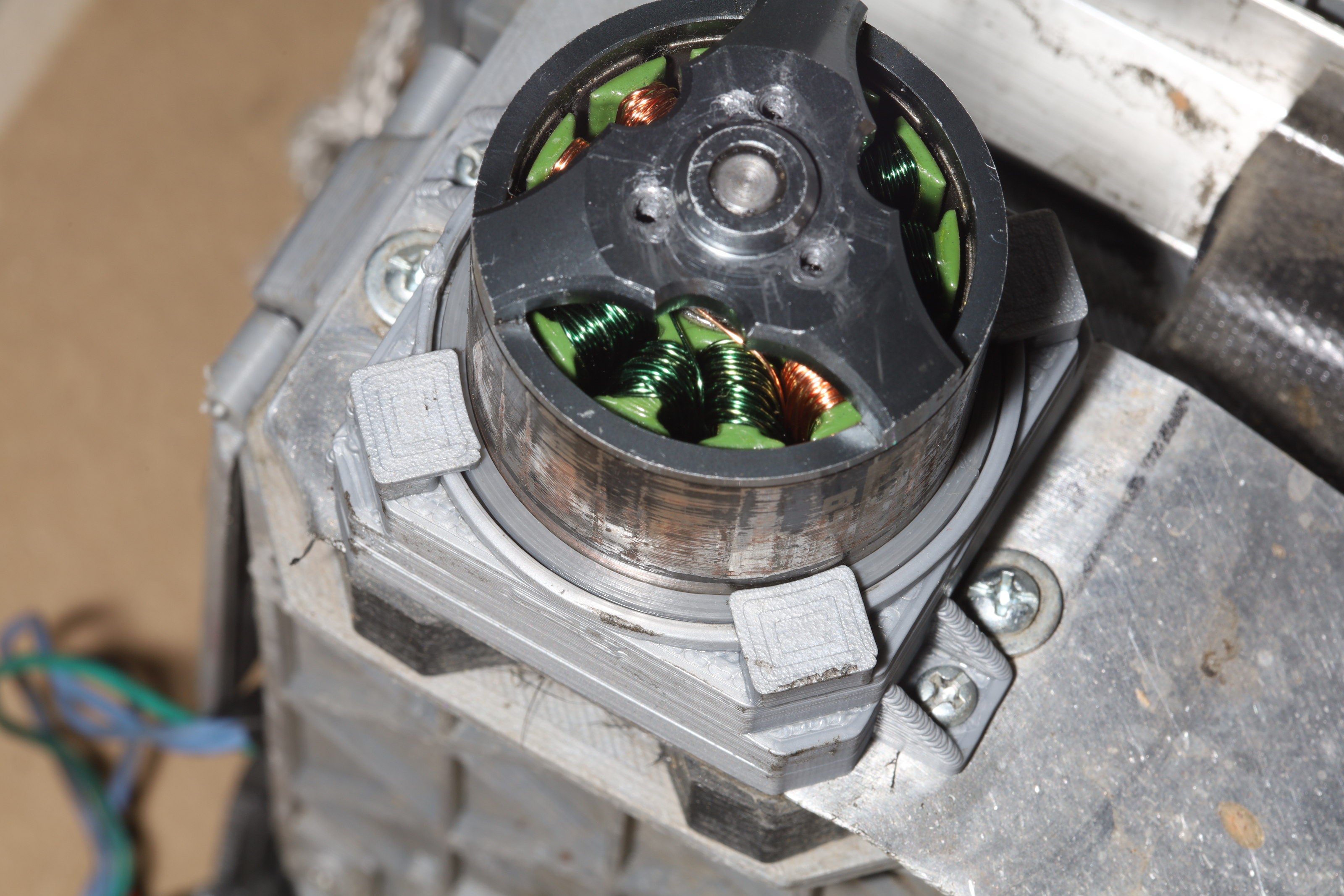
The decision was made to replace the TPU gaskets with PLA gaskets. They still managed to fit & rotate despite not being compliant. The theory is PLA will generate less static electricity than TPU. That didn't do anything. The servo still locked up in the same place.
The next plan is to print the gaskets & part of the shrouds out of conductive PLA. The lion kingdom ordered $20 of conductive PLA or 100 grams. 500 grams are now $50. The trick is printing the shrouds in 2 parts, gluing a conductive part where the shouds rub onto an insulating part. Then, the 2 rubbing parts would discharge into each other. Beyond the gaskets, the next source of static electricity could be debris inside the motor rubbing against the metal.
The trick with a 2 part shroud is it's very precisely aligned with the motor. It would need a filament change during a single print.
Discussions
Become a Hackaday.io Member
Create an account to leave a comment. Already have an account? Log In.