It has been a handy machine, and I've made a few upgrades over the past years and forgot to update here.
The single most useful change has been adding X + dual Y mechanical limit switches and a hall effect sensor z-limit switch. They aren't perfect and sometimes re-homing is off by almost 1mm (usually less), but it works well enough most of the time and is especially helpful recovering when I need to e-stop.
I also added a z-axis connectivity test to zero the z-axis with a touch-off (or x/y if cutting metal) - this has been super helpful, and I'm surprised to have seen some people say they are not useful.
Next, the rotary tool needed to go... I use the tool too much for it to live in the machine. Also the runout is pretty bad (forgot to measure), and limiting myself to 1/8" bits/mills was a pain. So, the last job of the rotary tool was to mill holes for the new spindle to mount:
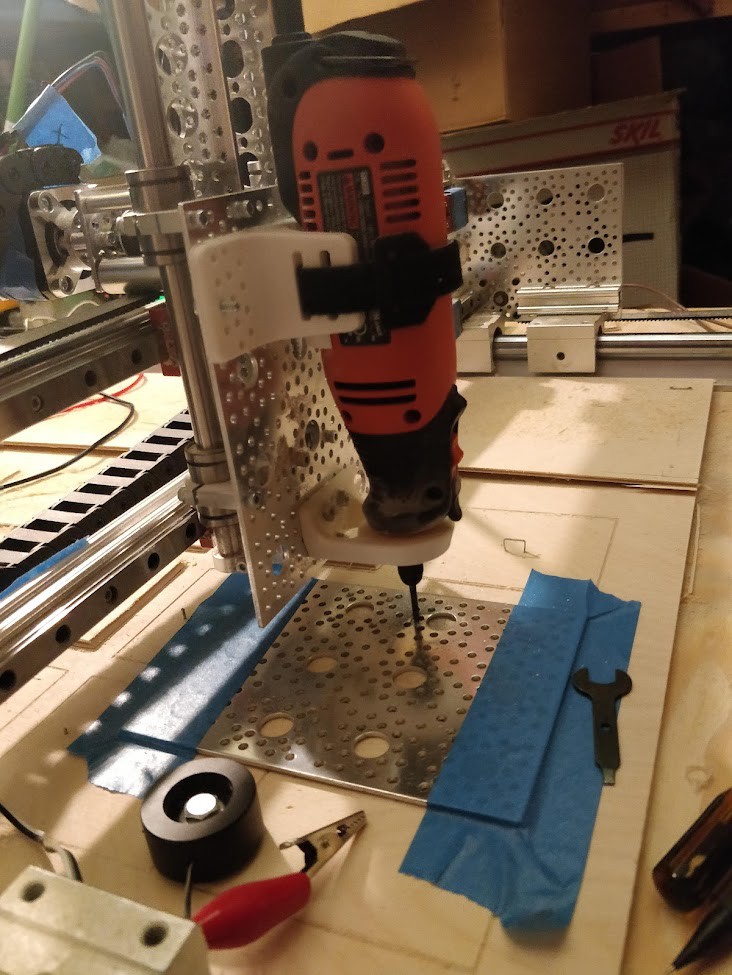
Now it can make faster and cleaner cuts in wood. (working on a doll "sets" - a window in this case)
It is a big improvement in noise over the rotary tool as well. Especially at lower RPMs (5k-8k)
I opted for slightly more expensive brushless ER11 spindle to theoretically get better torque at lower speeds than a brushed motor. I do wonder if I should have gone with ER16 instead of ER11 though.
And with ever growing wires with limit switches and brushless motor, it's time to add cable guides and some wiring terminals...
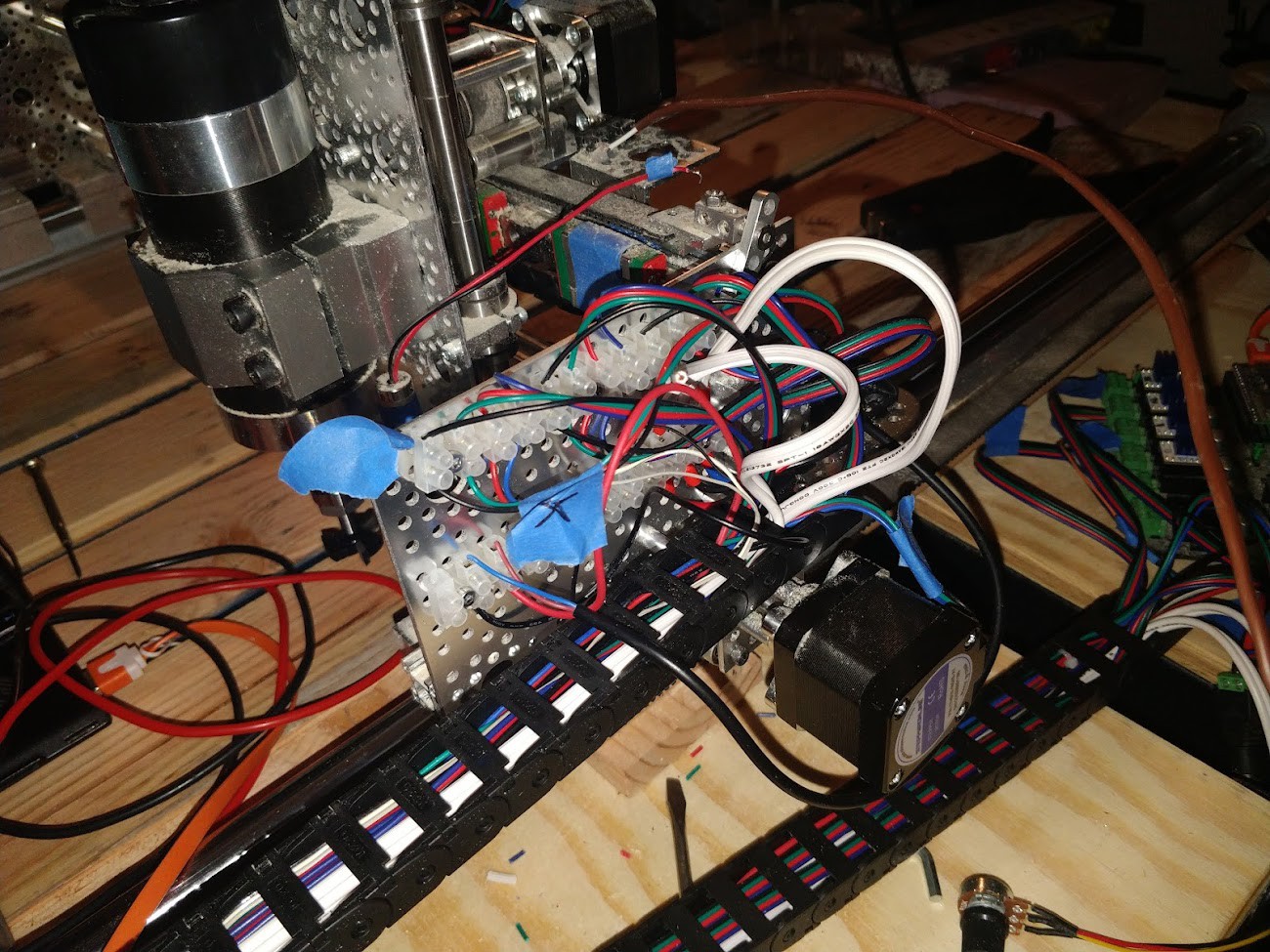
Really it was a mistake to not to cable guides and the wiring terminals from the beginning - it's a very worthwhile quality of life improvement.
It then became clear I need a better way of mounting things than tape or staple gun, so I build a spoil board from scrap lumber with tracks for clamps.
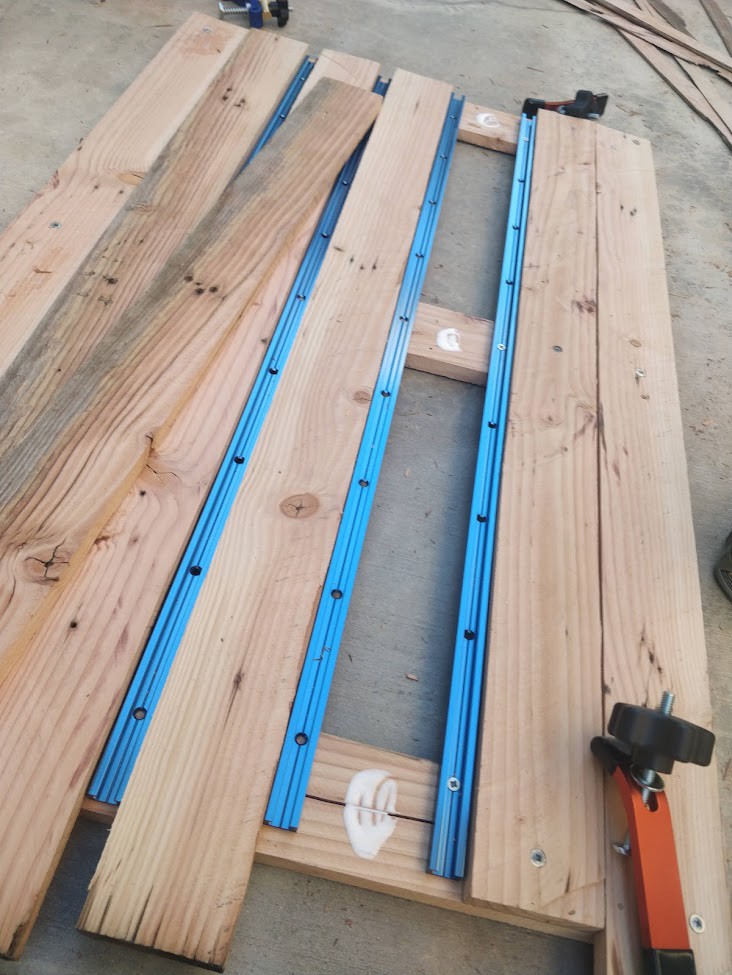
The clamps are too thick for the gantry to clear, ooops. Maybe a future iteration will raise the gantry height (but that would also require making the z-axis more rigid, and the Z+Y axiis are very good with the current configuration.)
Still to come? I bought a light for the spindle, but it causes the controller to brown-out. So power supply needs an upgrade before that. That will be a near-term upgrade.
The there is still pitch wiggle problems, so the new spindle works great even on aluminum moving along X, but has terrible chatter along Y on tougher materials. Which it was never intended for, but I find myself wanting to cut more often. (I also wonder if I should just get a Carvera for that.)
I also experimented with a laser pointer for alignment, but I think I need to experiment with that more.
Ironically, the costume props I built this for I never made and only did one foam project. It mostly gets used for wood and some plastic.
Discussions
Become a Hackaday.io Member
Create an account to leave a comment. Already have an account? Log In.