We made multiple changes which aimed to improve the assembly experience when building Stanley. The most substantial one was the decision to flip (mirror) the Cable mechanism of the hip.
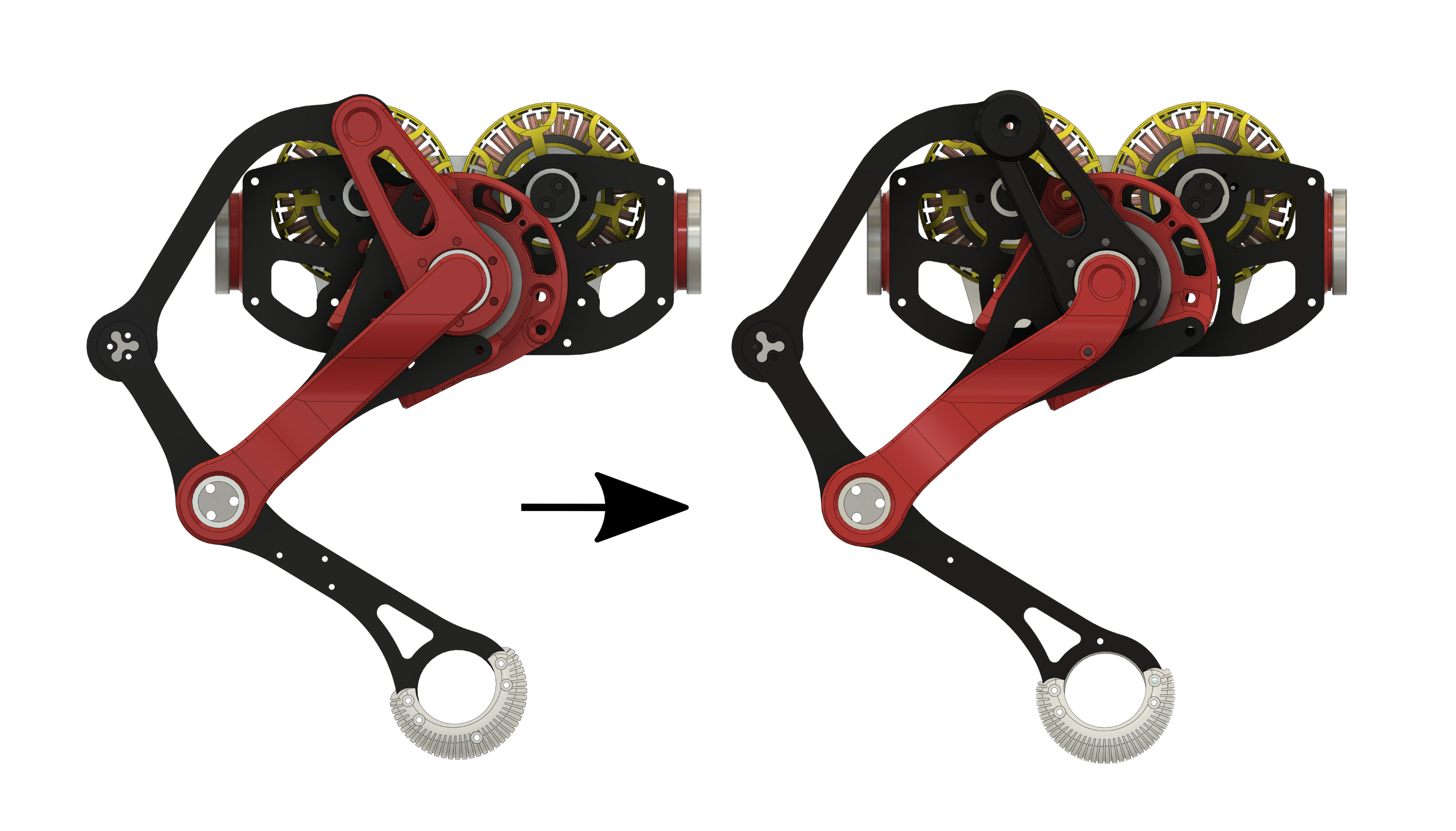
This change brought a few key benefits:
- The Femur Scaffolding (grey part along the femur) was straight on the old design and has a bend in the new design. It is now mounted with fewer, but better-placed screws, which means it provides better support and a small mass saving.
- There is significantly better access to hip mechanism cable tensioning.
- The assembly process of the hip cable mechanism is less fiddly.
Other changes include:
- Reducing the number of screws per leg: 12 fewer screws per leg needed!
- Rotating the floor a bit more downwards so it is facing the ground at a more universal angle
- Improving access to cable tensioning nuts
- Making the entire leg assembly 6 mm shorter (eliminating some dead space in the ABAD mechanism)
Discussions
Become a Hackaday.io Member
Create an account to leave a comment. Already have an account? Log In.
I love this project and while I'm not an expert in any of this stuff, you may want to take a cue from nature and design some components to be able to deform (flex) without being damaged. However, you could take more engineered approach would be to have a stress relief mechanism that would trigger if "too much" force is applied.
It is important to keep in mind that evolution has made leaping quadrupeds utilizing far weaker materials.
Are you sure? yes | no
The problem with flexible parts in robots is all about control. Yes, it could be beneficial to have flexibles in limbs and joints. But non-rigid mechanical systems (where you can't assume perfect rigidity as a good enough approximation) are much harder to control - these are "higher-order systems" - flexibles add unactuated degrees of freedom to robots. Rigid body control theory is much better understood, more established and much less compute-intensive.
Are you sure? yes | no
They don't have to be highly flexible, I'm just suggesting it as an alternative to being rigid until it snaps but I understand your point that it increases the system complexity and should be accounted for in the software. Running a small neural network on bare metal should be able to keep the computing to a minimum while enabling sophisticated control and feedback, more like a biological system. However, the design doesn't strike me as trying to minimize the computing requirements considering a full-blown SBC running Linux is being utilized. Not sure about your plans, so perhaps that will change in the future.
No matter your approach, I hope you find a way to remedy Stanley's tendency to break into pieces because I really like this project.
Are you sure? yes | no