...continuing, maybe even finishing, the log that's taking months to write...
Successful application of these slides requires loading them near the ends and avoiding any load in the middle of the flexibendy side plates.
Simply attaching a slide to something more rigid satisfies that constraint for free. Once the four corners of a side get screwed down it becomes as rigid as whatever it's attached to, without any further reliance on the flexible middle span of the side plate.
In that case, most of the side plate won't be missed:
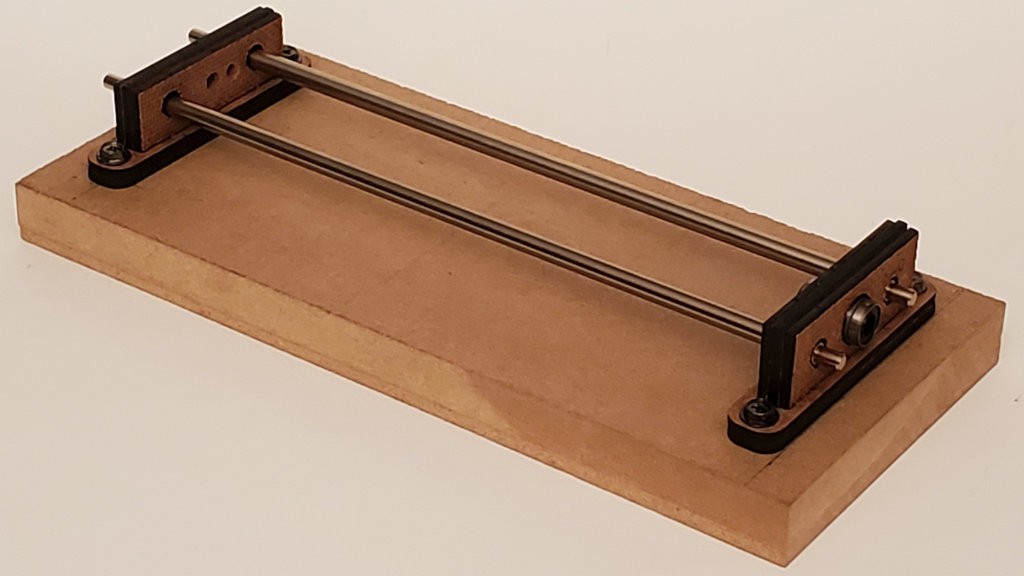
That uses less material, much less for a long slide, and yields end assemblies that fit any length of rod. One kind of assembly could be used at both ends when the material in the space opposite the bearing isn't used.
The shim plate keeps preparation of the mounting surface simple:
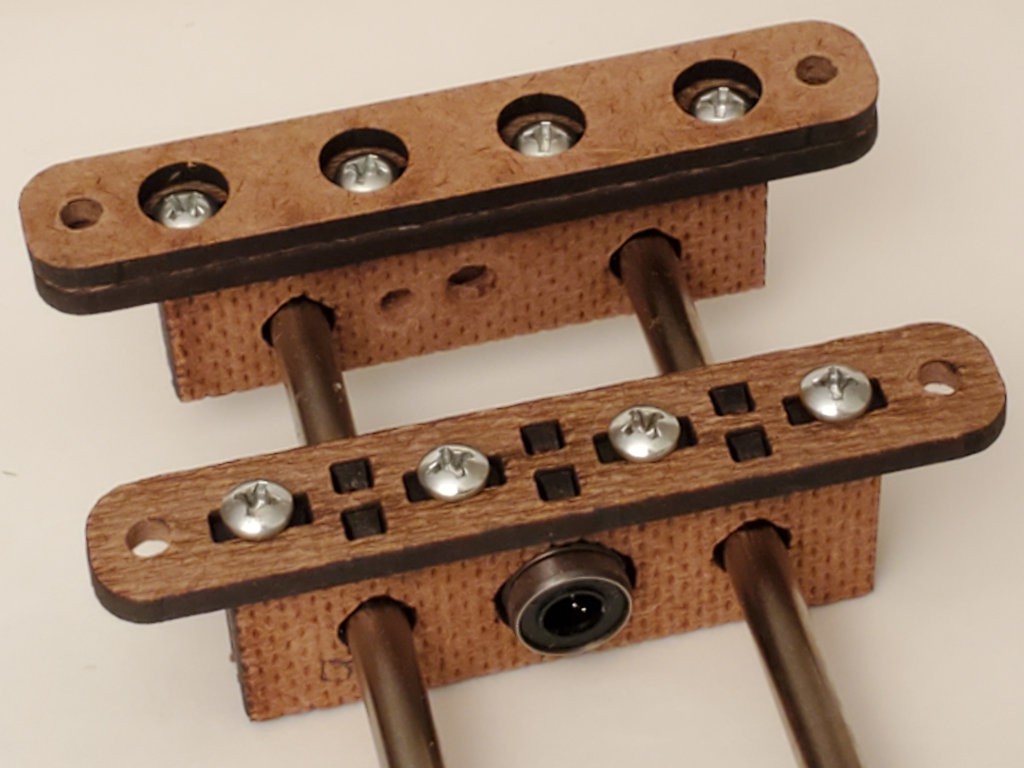
Drilling clearance pockets for the screw heads would work too. I've used the shim "feet" to concentrate complexity in the laser cut parts in order to keep other fabrication as simple as possible, and to chew up my base material less while iterating through several variations, but that's a choice for my motivating application. If used, clearance pockets should just clear individual screw heads and leave solid bearing surface under the V plates.
The end assemblies above may be assembled and incorporated into a complete, if fragile, slide, which can then be handled and mounted as a unit.
I also tried a variation of directly replacing the side plate with more robust material, without growing the end assembly to add mounting tabs or a shim plate. In this case by simply cropping the ends without alteration and adding the thickness of new material to the length of the screws. This version incorporates the heavier material directly in the slide construction and can't be assembled without it.
Here the cropped end of the side plate is kept for its laser-cut details. In principle, those details could be precisely cut into the heavier material, but availability of that capability might favor entirely different construction.
In line with keeping complexity in the laser-cut parts and out of other fabrication, the heavy material is simply cut to length and width. The laser-cut parts included a template of pilot holes (not shown) to guide sufficiently precise location of the drilled holes.
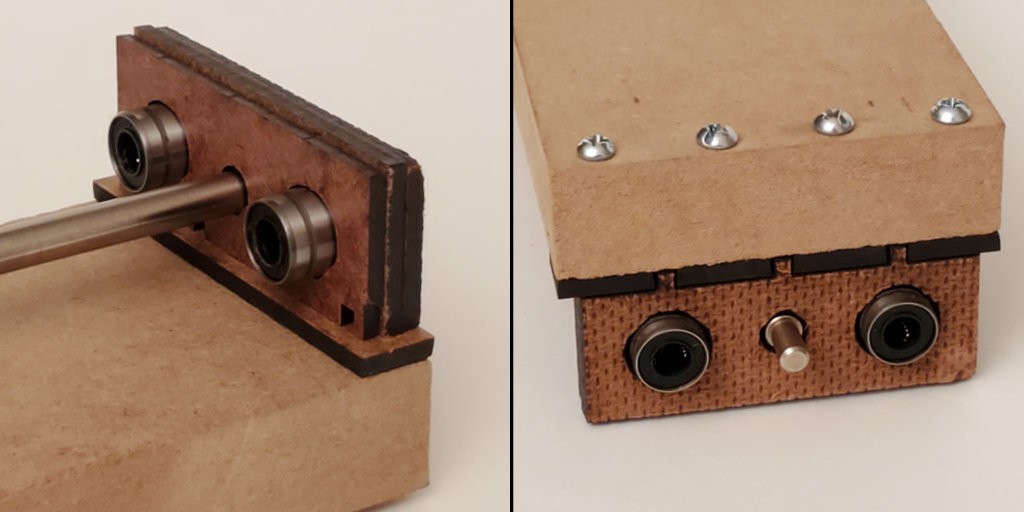
Aside: The two-view image above shows much more material in the clamping plate over the bearings than in any previous example. When fully extended these long slides have great leverage across the small remaining overlap in the center. Stressing the first example began to strain the thin bridge of material over the bearings. Because these separate end assemblies stand one or two material thicknesses higher above the side surface, they also gain that much additional clearance between the top of the clamp and the opposite side. In this example I used that additional clearance to add material to the clamp over the bearings.
A complete slide using the parts above:
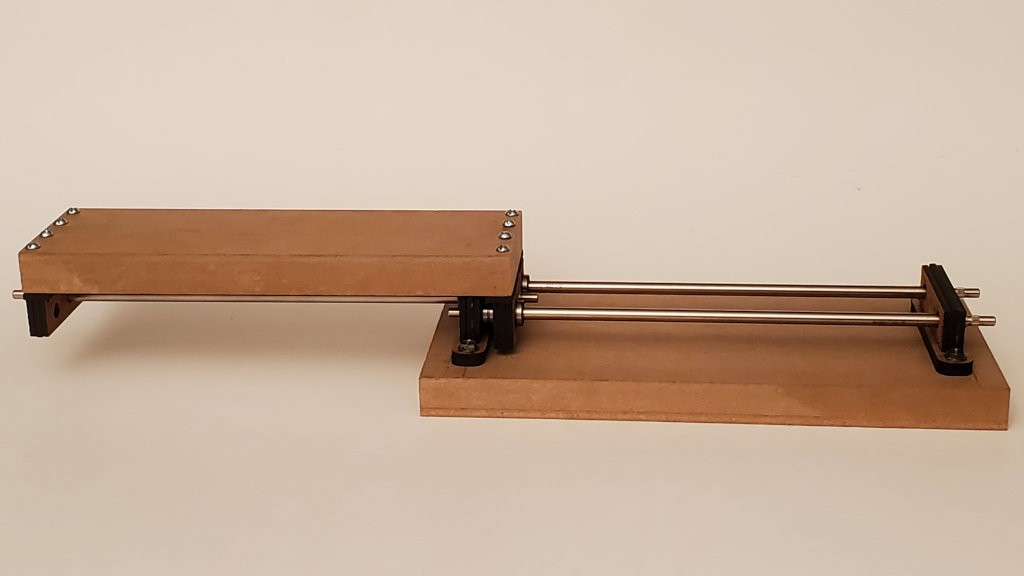
This long side of this slide easily bears load in the span between the ends. In this case the long side of the slide is far more rigid than the long rods.
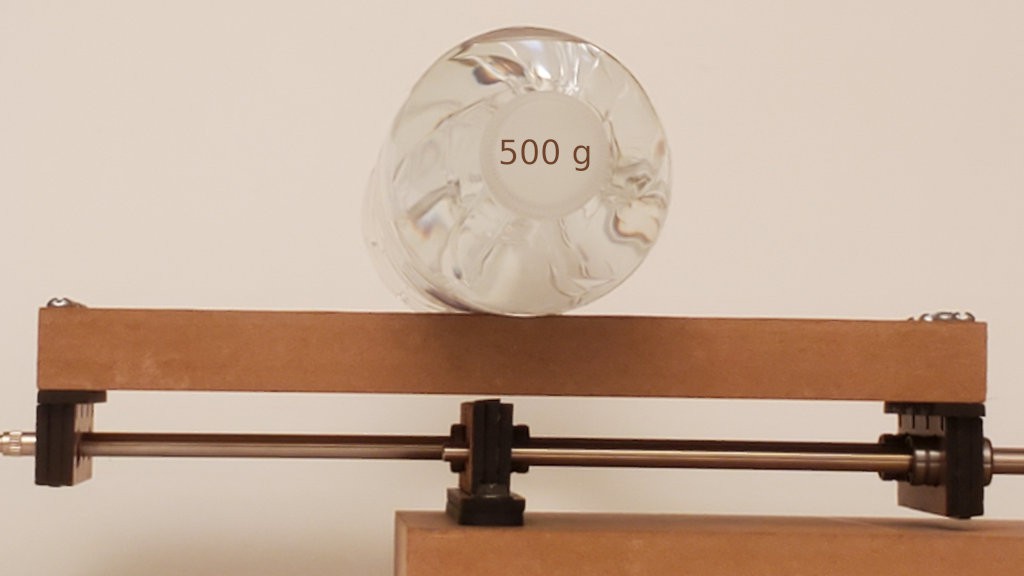
In this case the load carrying capacity is limited by the rods flexing when they are loaded in mid-span. As described above, I made the bearing clamps taller in this example. Using up less of the increased clearance for the clamps and leaving more room for the rods to flex would increase the load this slide could bear without scraping in the middle — when that much sag is acceptable.
The rods have turned/knurled ends because they came out of a printer.
From writing up my first try at a long slide:
It's really just the two ends in the middle constraining where the rods and bearings intersect the two nearly coincident planes that make the slide much more stiff than an equivalent span of hardboard.
These separate end assembles — and only the three ends that hold relationships between two or three things — clamped onto rods make a complete, if delicate, slide:
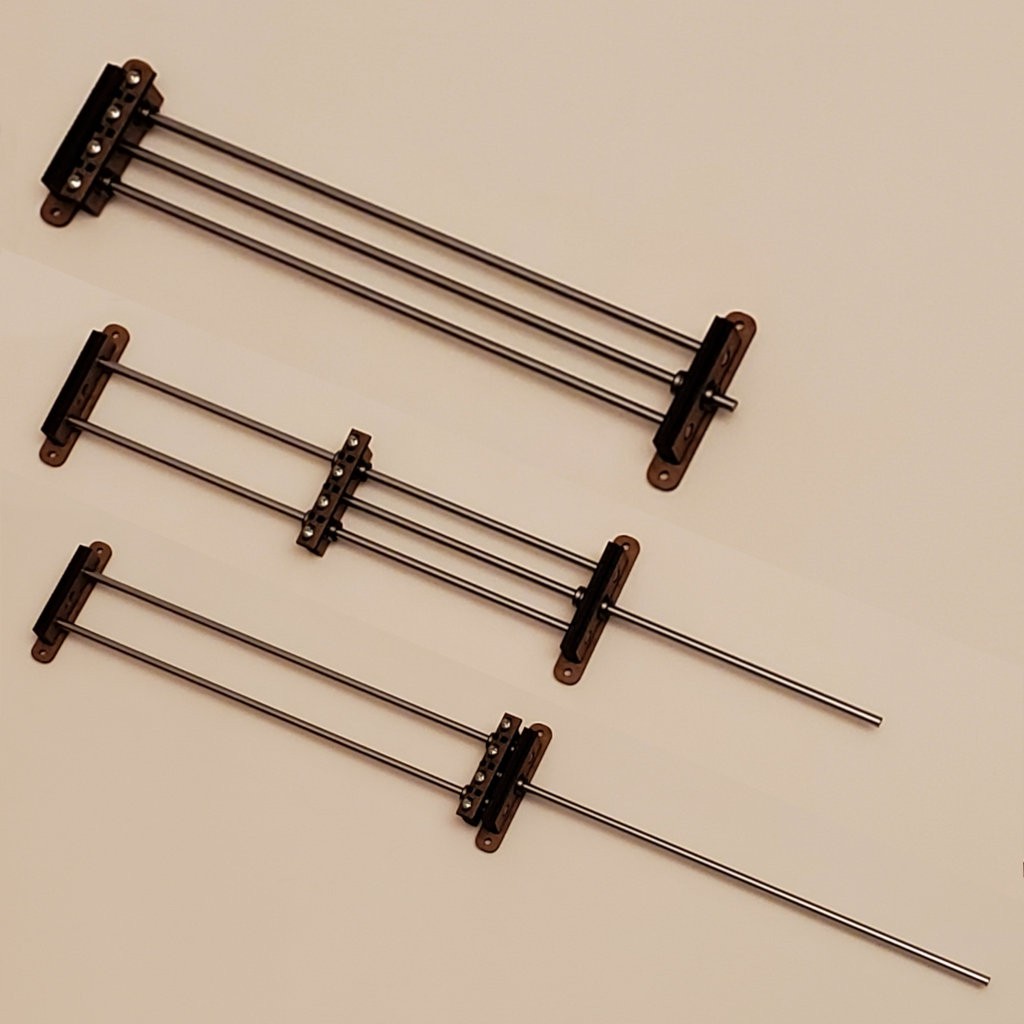
That skeletal arrangement has the stiffness of this earlier example:
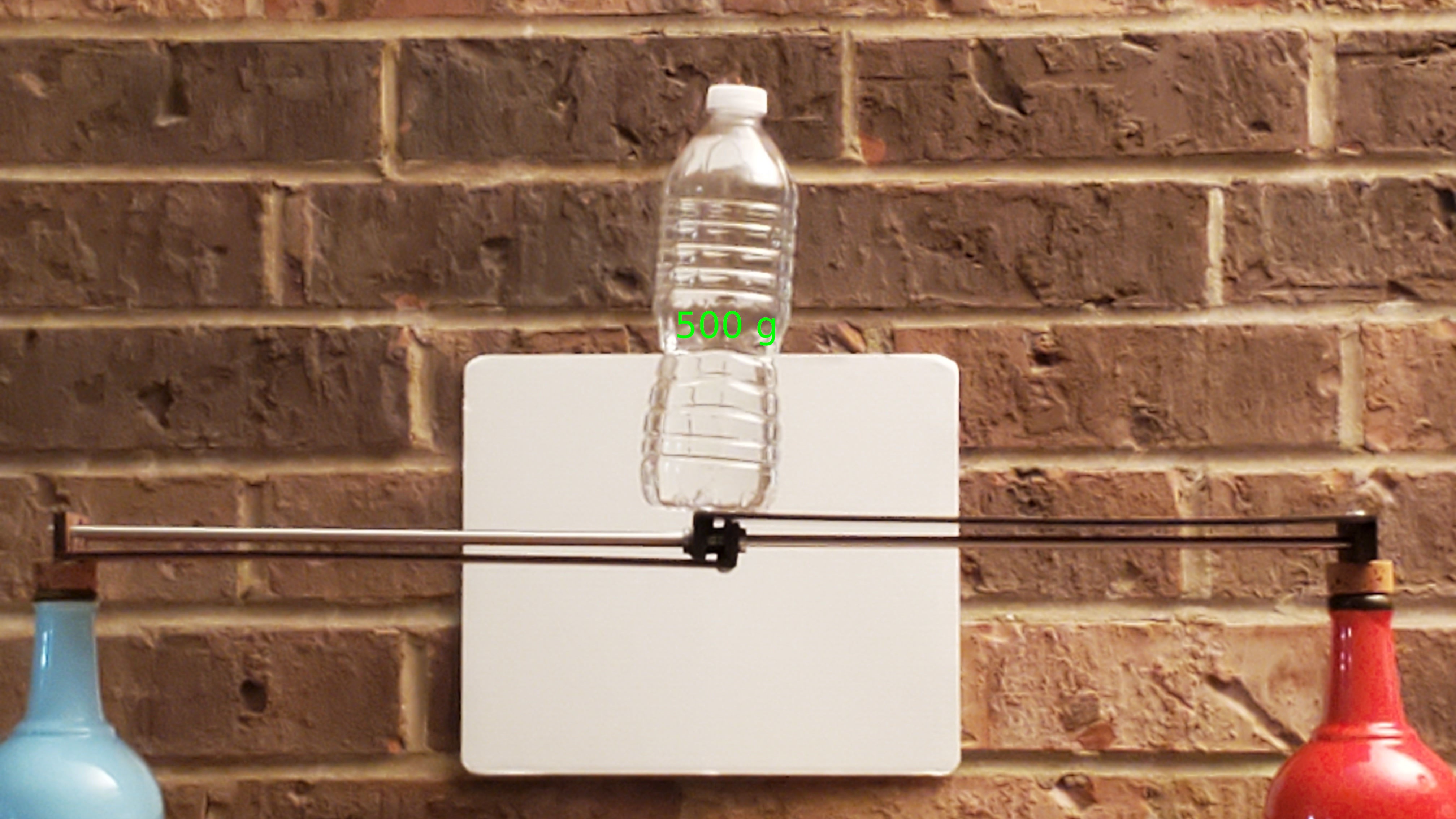
(apart from a flat place to park a load, and if not twisted)
... and smoothness of this example:
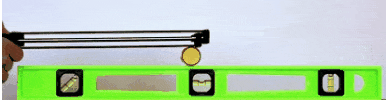
...which I've repeated here because I'd rather finish this log than stage new photo examples!
Discussions
Become a Hackaday.io Member
Create an account to leave a comment. Already have an account? Log In.