A friend gave me a nice coherent Gem-50L co2 laser and so I could build a laser cutter. It’s a pretty nice laser, rated 50W and doing 62. Datasheet here: http://www.istcgroup.com/pdf/GEM_50L.pdf
I have decided to make it as an attachment for the mill which will attach to the dovetail on the ram.
First thing I need to do is get the laser under control. I need to be able to run it at low power to check the orientation of the ATFR mirror that stops back reflections from the work. It needs to go in a certain position relative to the orientation of the polarization. Of the output beam. If it’s 90 degrees off it will absorb 97% of the beam instead of reflecting it.
To control the laser I am building a small box that handles the enable, mode, and PWM signals that the laser needs to work. For this I reused a little Teensy 3.1 board and pcb I made to attach to the back of a vacuum fluorescent display. I made another daughter board to attach to it that handle the IO. I really should have just designed a new board and send it out to JLCPCB with amount of time I reworked and debugged finding and fixing he mistakes I made when I laid out the Pcb years ago. I still might to clean it up. It’s a mess.
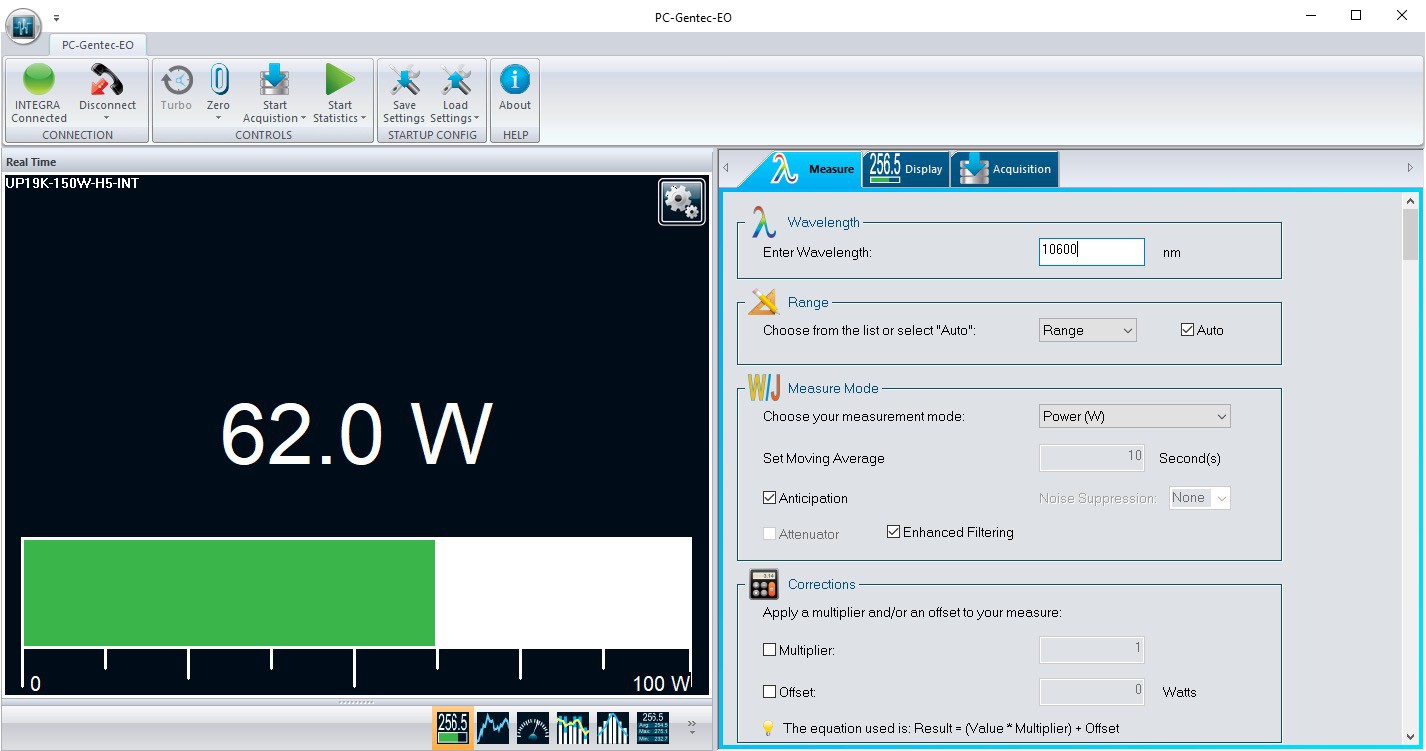
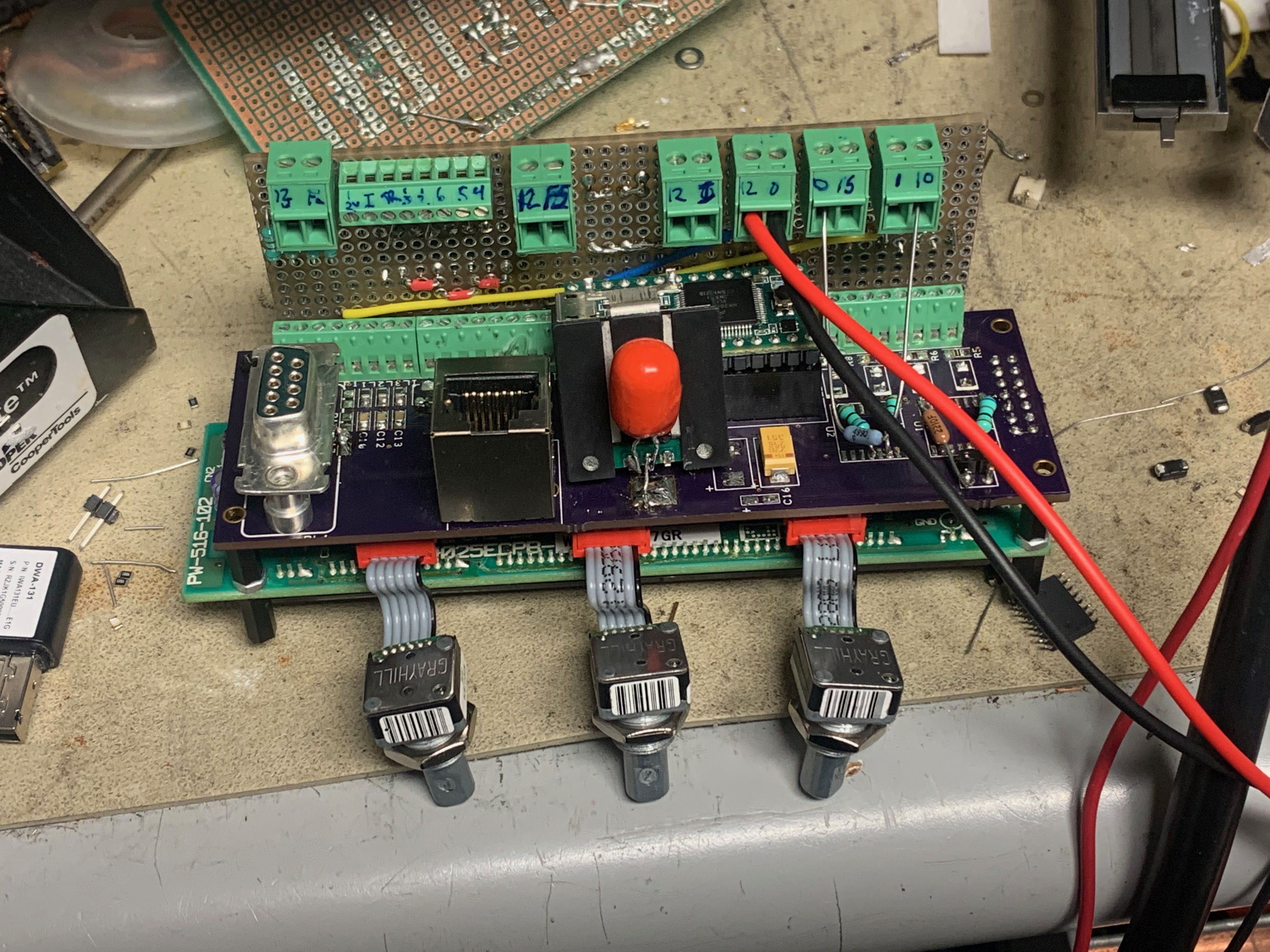
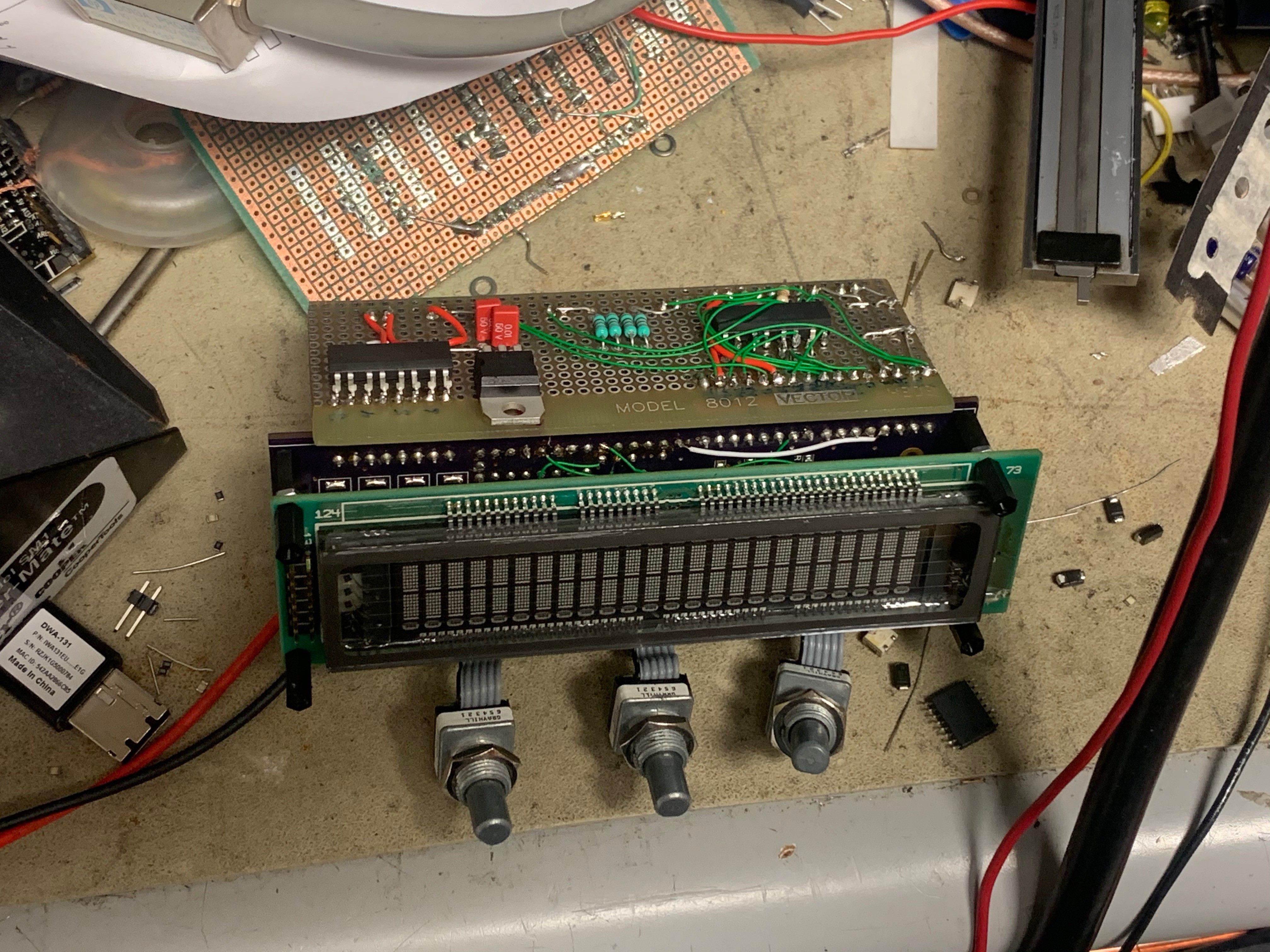
Discussions
Become a Hackaday.io Member
Create an account to leave a comment. Already have an account? Log In.