Keeping the ink at the right viscosity is essential for getting a stable ink stream breakup and with that stable charging and deflection of the ink droplets.
In the initial design, I counted the time it takes until the ink level of the pressurized tank has dropped from full to empty.
After using just tap water for a while I tried using Vegetable Glycerin instead of water since it has a higher viscosity.
To measure its viscosity and compare it to the drain time counter I got a Zahn Cup 1 and a Stopwatch.
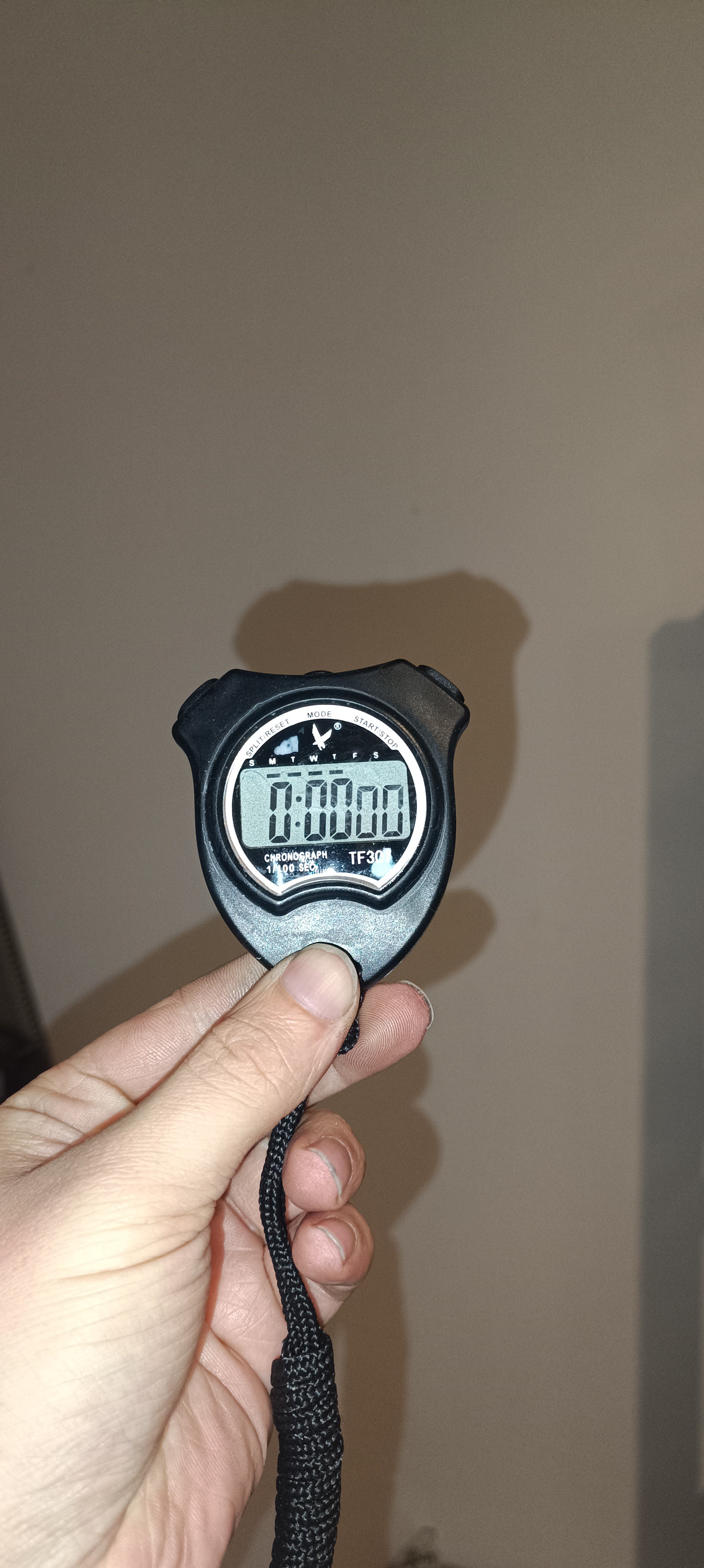
These cups have a hole on the bottom for fluid to leak out and are used by completely submerging them into a fluid, then lifting them and counting the time until the solid fluid stream from the bottom of the cup starts dripping.
By using the corresponding conversation formula, it's possible to calculate the kinematic viscosity of the measured fluid.
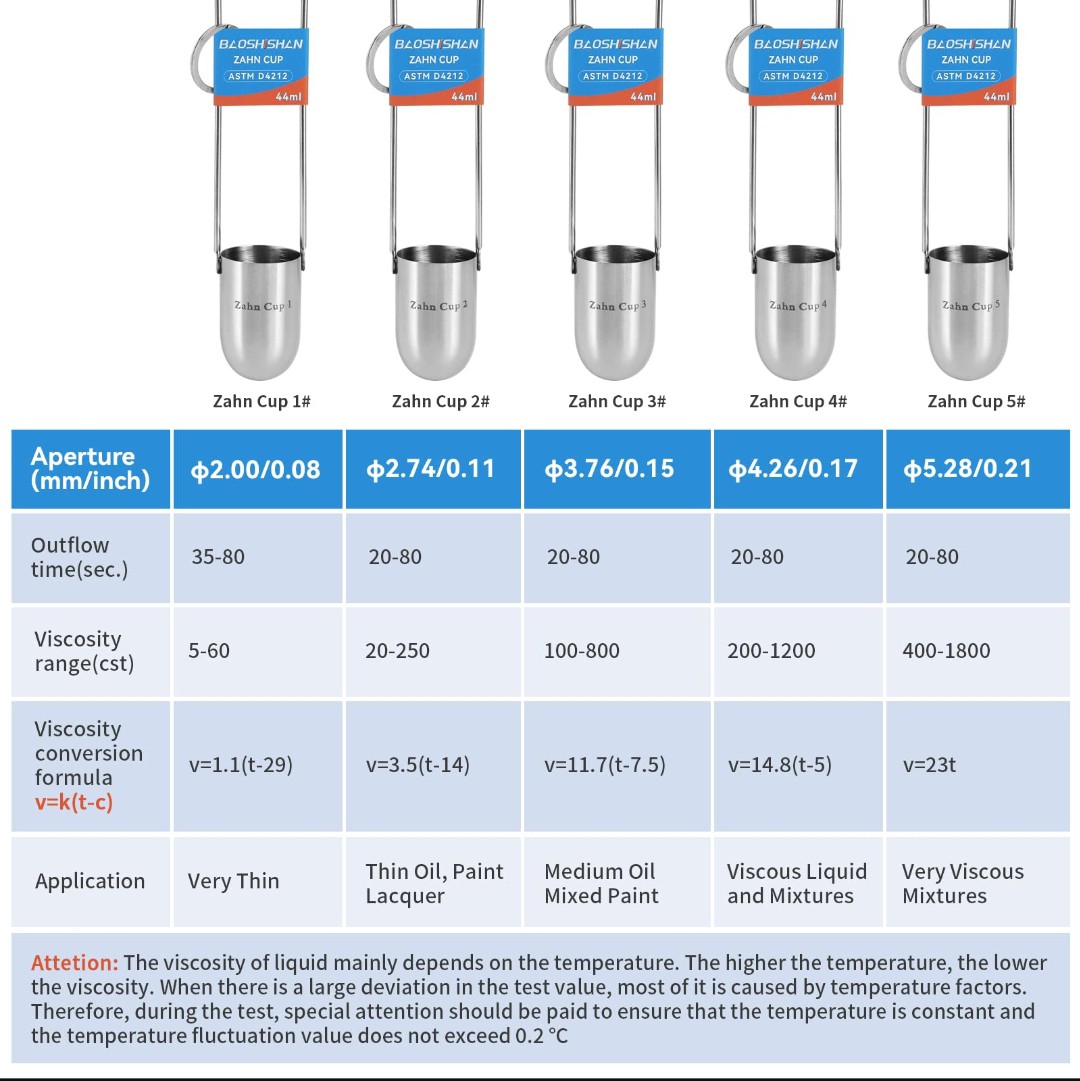
While testing I saw, that the values lined up to some point:
When I added VG to the water, the drain time got longer, when I added water the drain time got shorter.
It worked ok, but since I'm constantly changing parts of the fluid lines that are filled with ink it's hard to prevent that some of it hits the desk or floor, and because Vegetable Glycerin is an oily fluid that not evaporates (in contrast to water), it turned out to be pretty messy to work with and I switched back to water after this test.
The next update to the printer was adding a PPM meter and a temperature sensor for measuring conductivity and temperature.
Since viscosity changes with temperature, I thought it would be a good idea to not only keep track of the viscosity but also of the temperature.
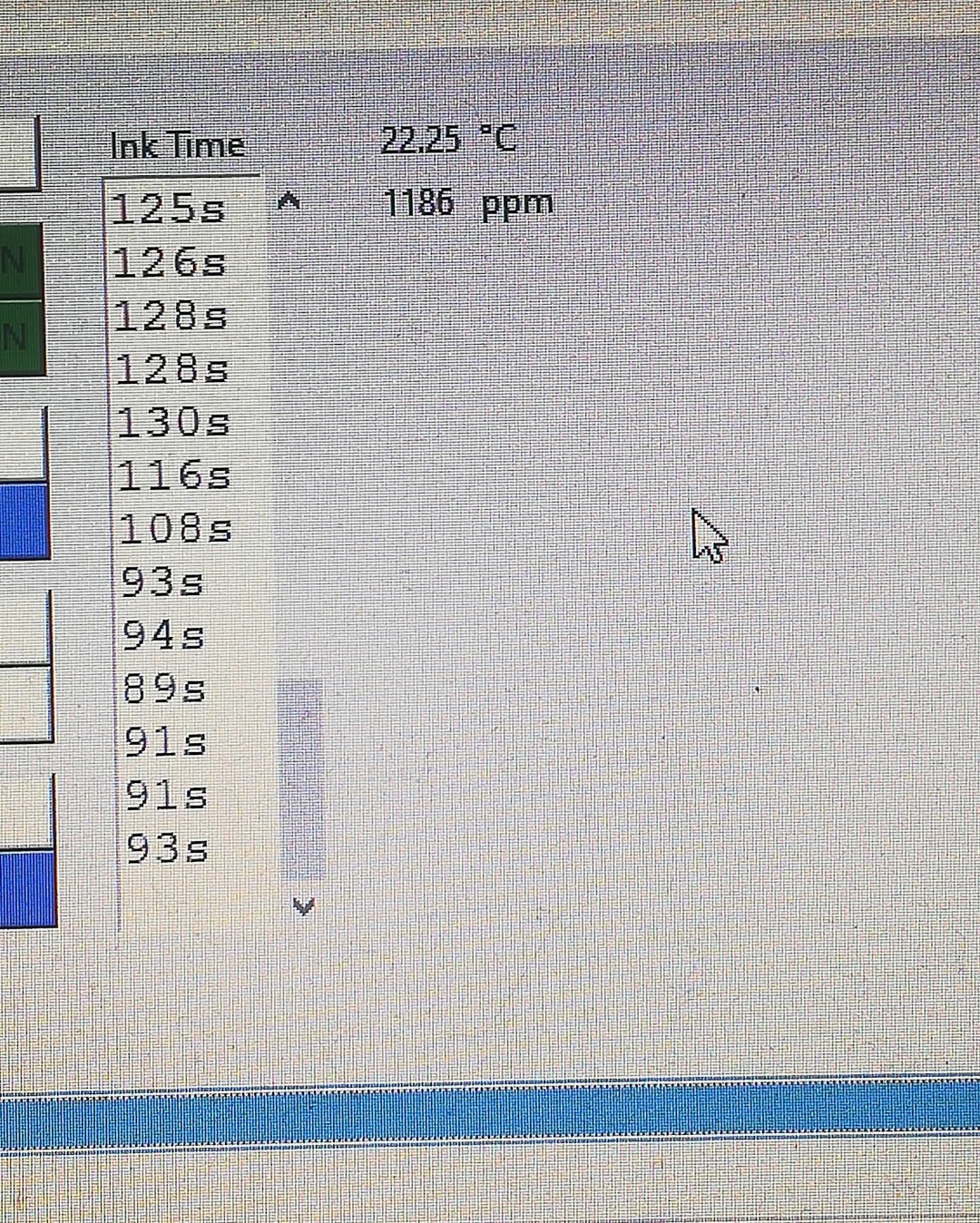
While the conductivity is not related to viscosity it's still important because the ink needs to be conductive for charging.
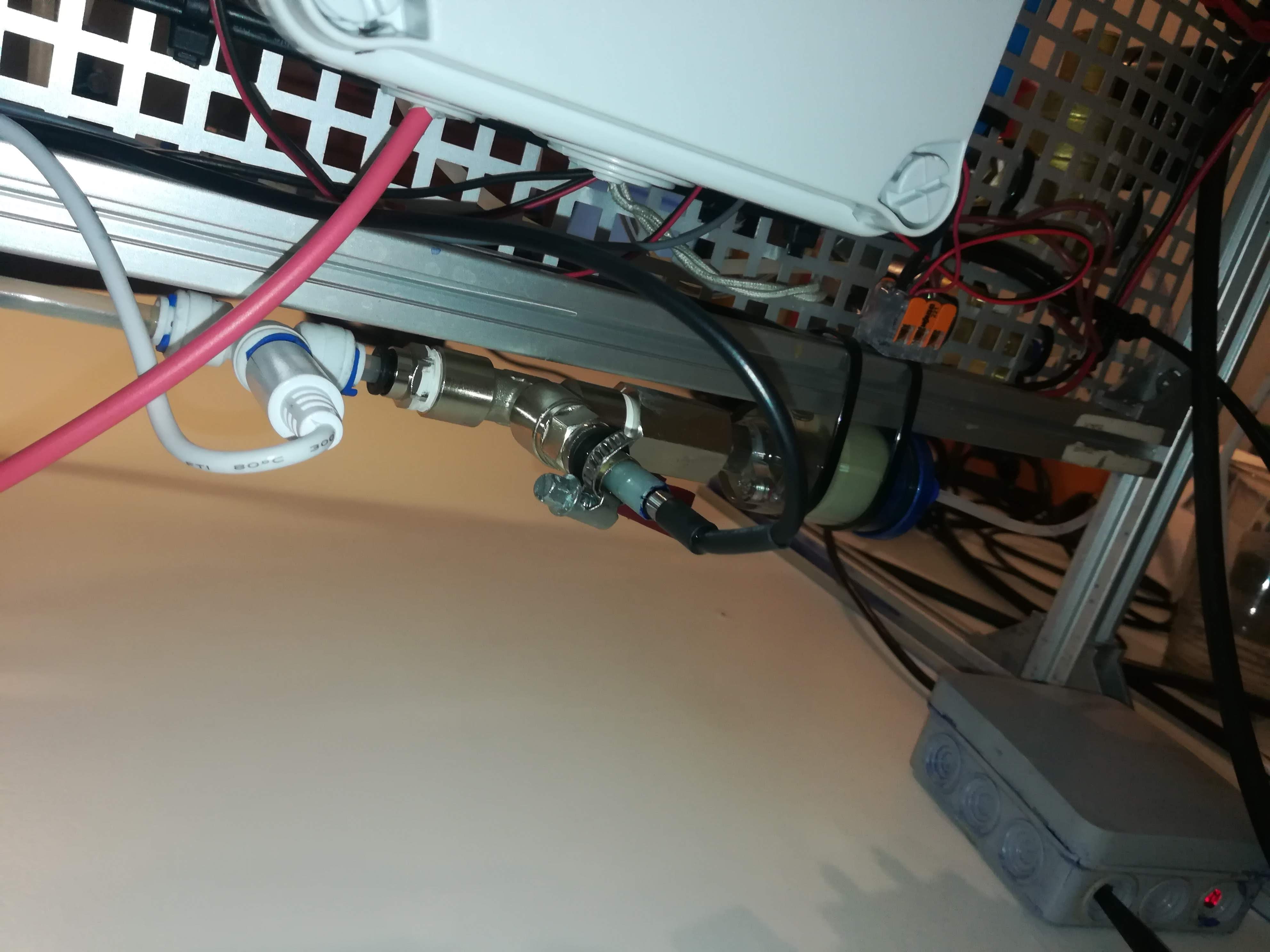
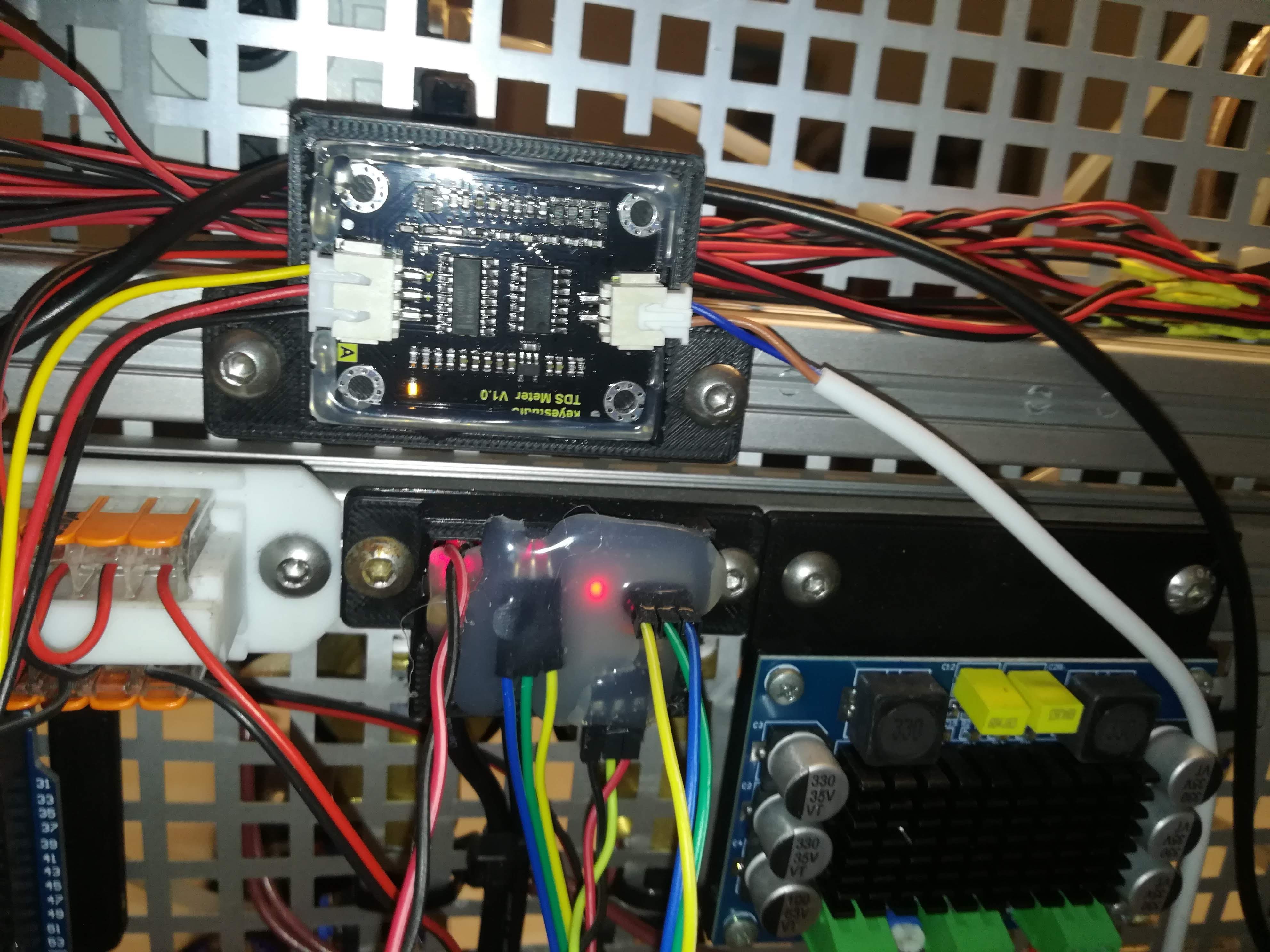
To increase conductivity I used different additives over time:
For water, I tried out:
- Table Salt
- Baking Soda
- Citric Acid
- Cleaning / Washing Soda
- Sodium Propionate
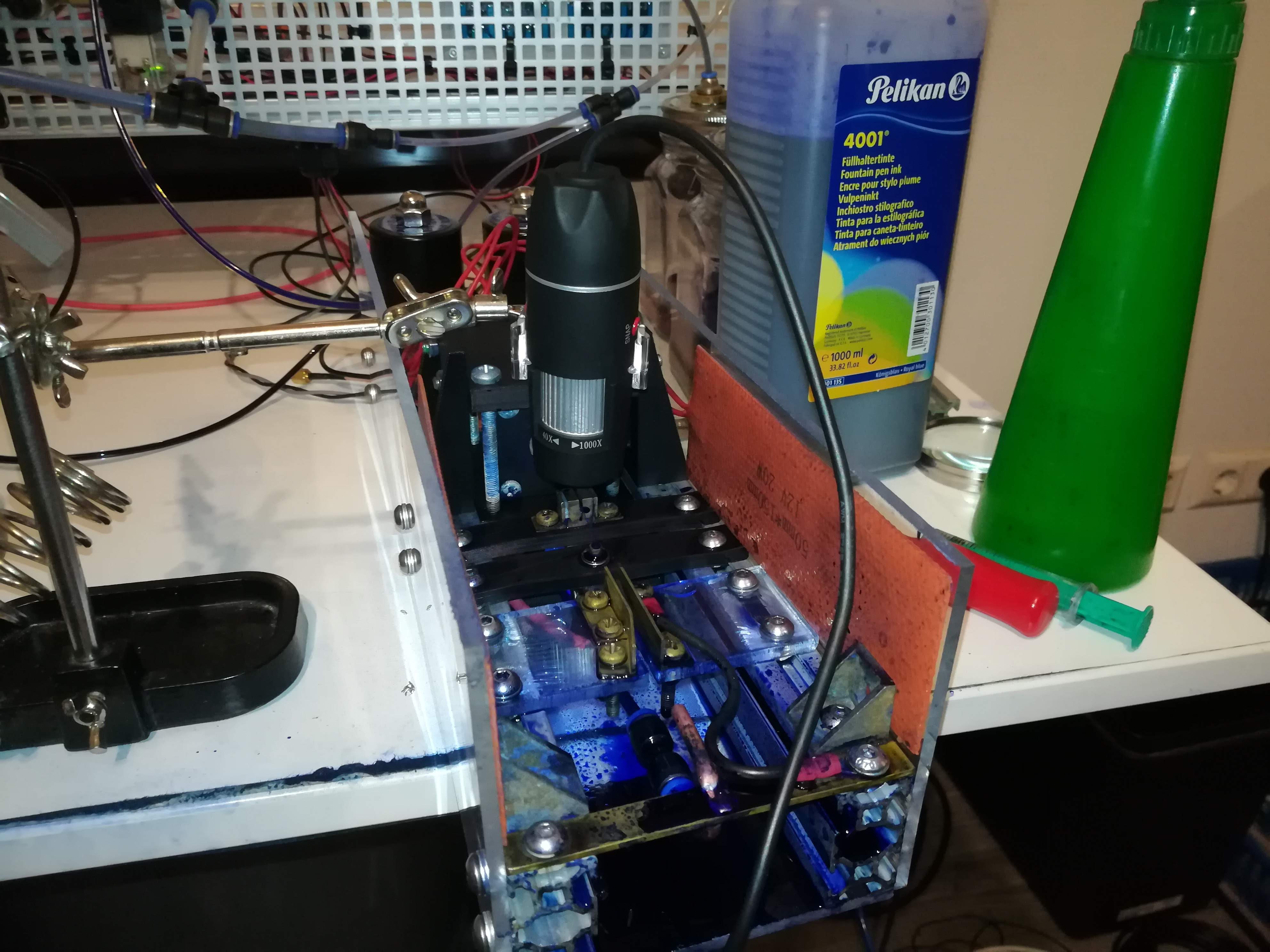
There are likely many more additives that are soluble in water, but since I switched from water to ethanol to get a fast drying and water resistant ink, I didn't test out more of them.
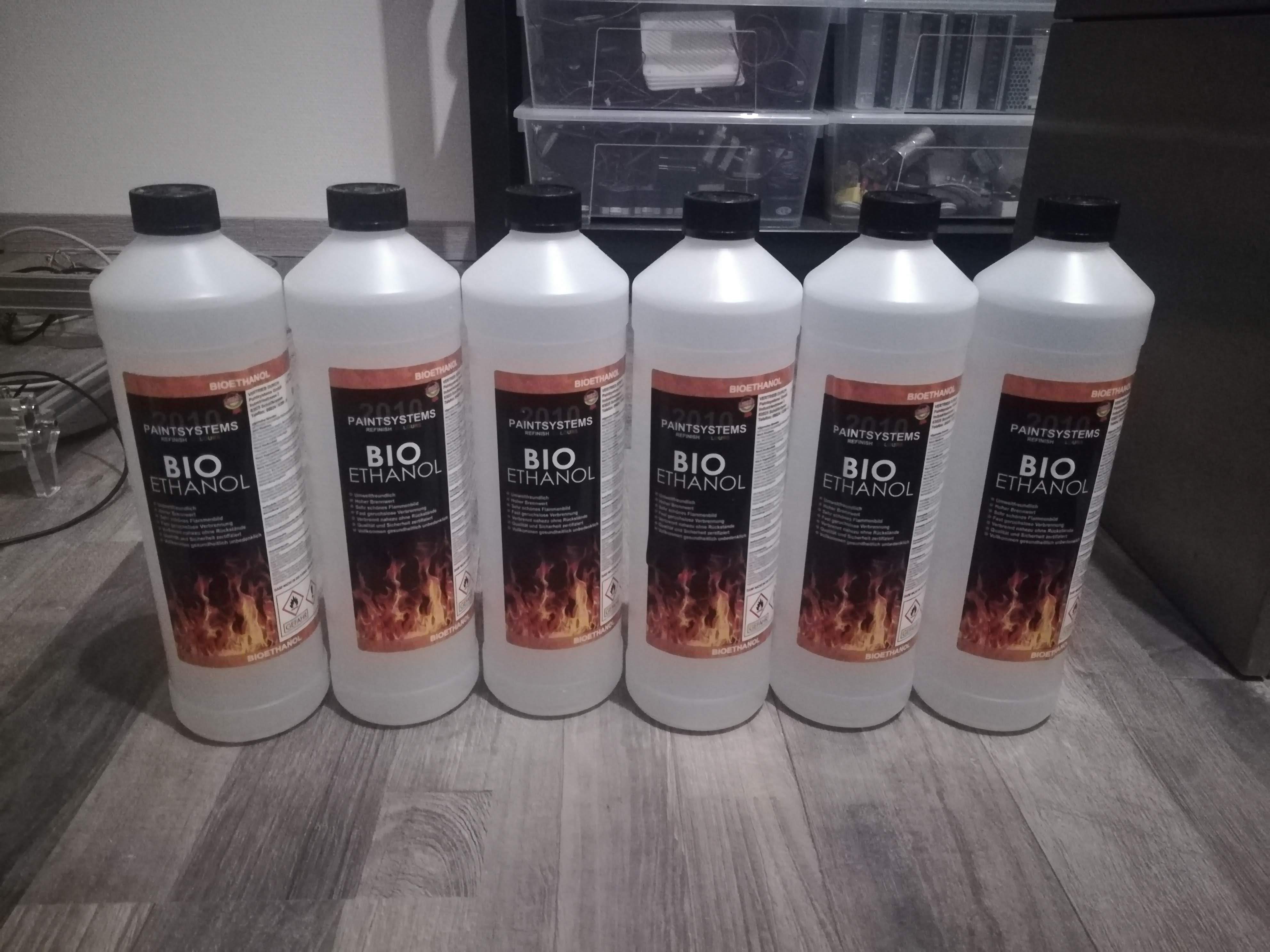
Since not every salt that is well soluble in water is also well soluble in ethanol, it was needed to start searching for ethanol soluble salts.
First I tried using Sodium Propionate, which was able to increase the conductivity but added an unpleasant smell to the ink and was quite corrosive on the metal parts.
I still used it for a decent amount of time.
Because of the corrosion on aluminum, copper, and brass parts that was caused by the sodium propionate and the former used additives, I replaced almost all feed lines and metal parts with either plastic or stainless steel at some point, to make the printer as corrosion resistant as possible.
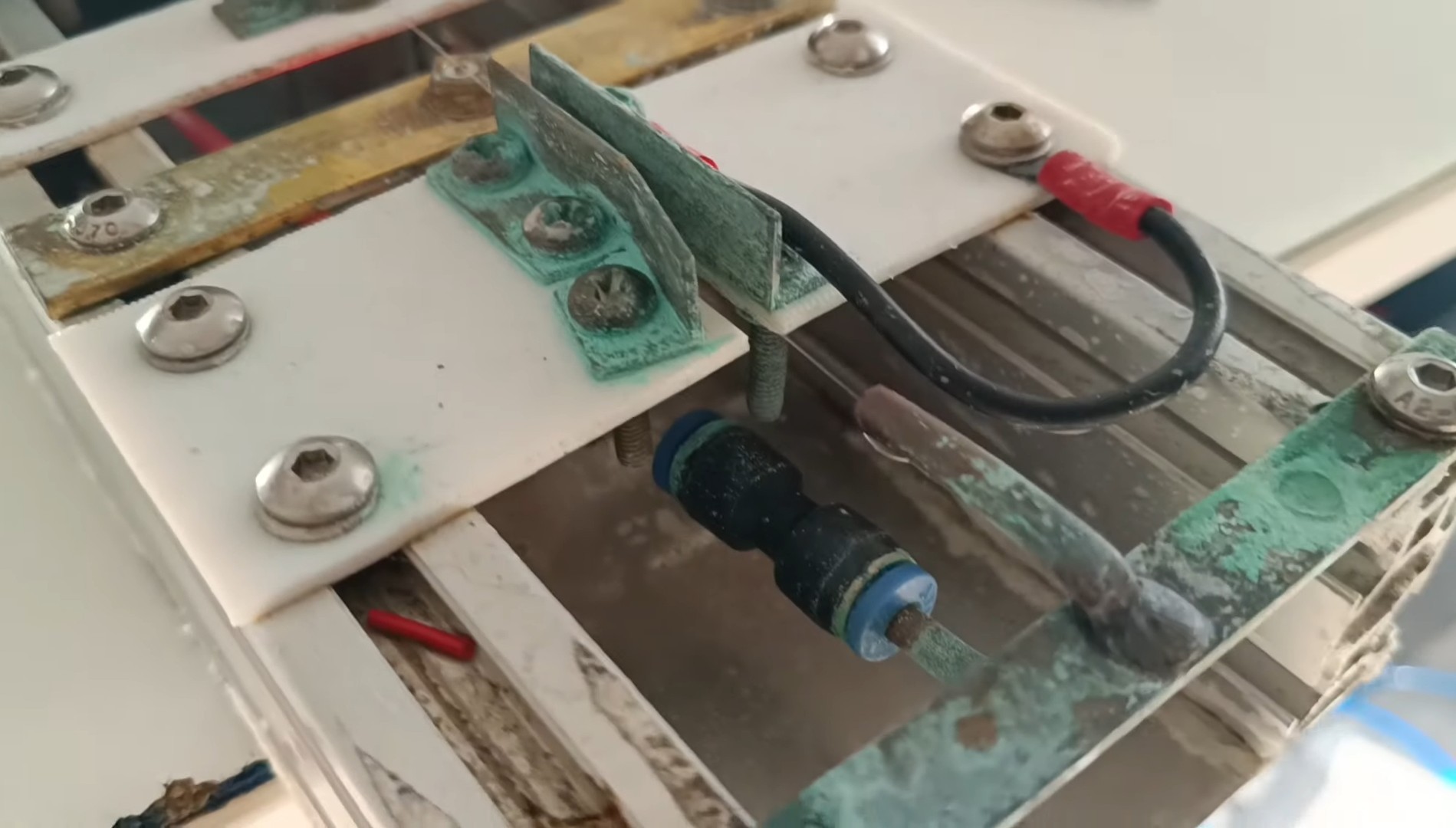
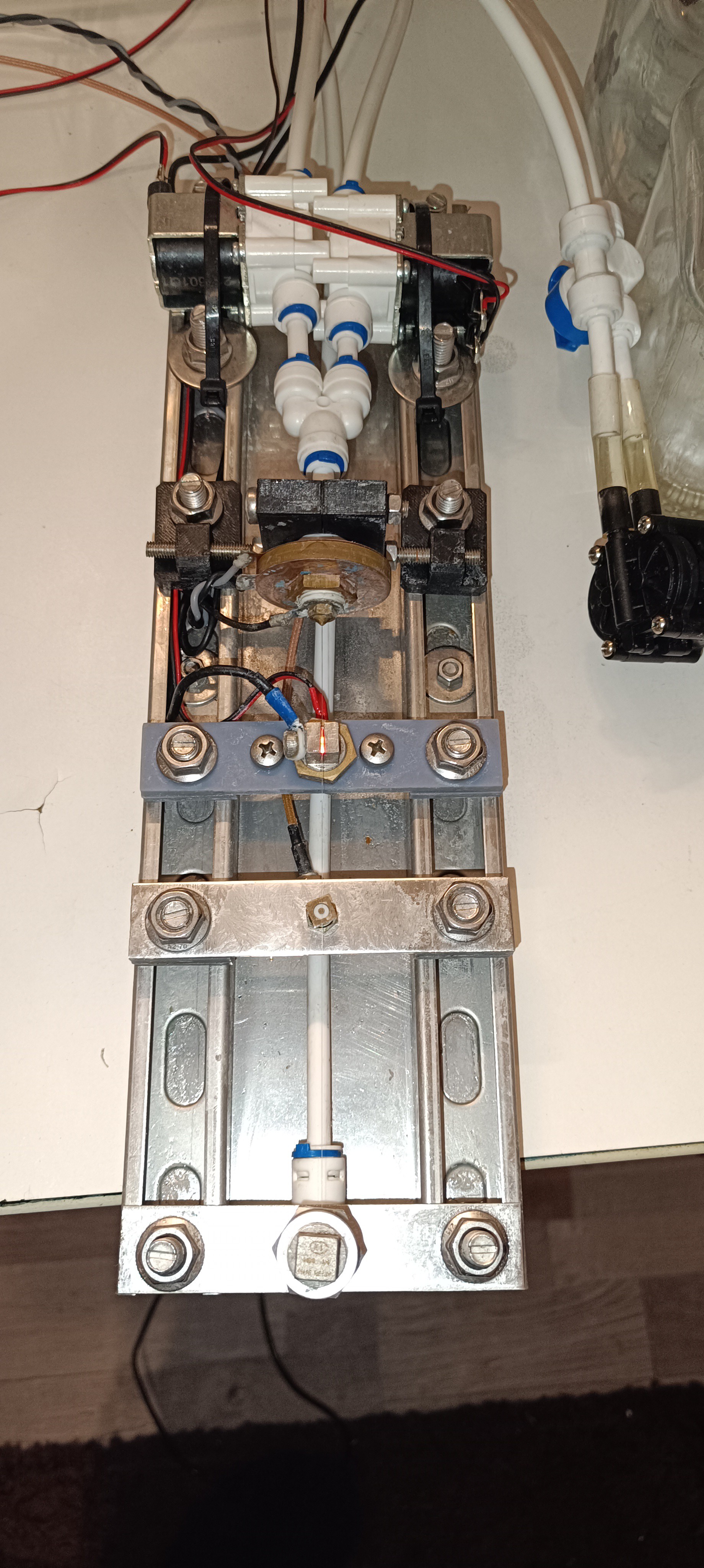
To get rid of the unpleasant smell and oily residue of the sodium propionate I searched for another ethanol dissolvable salt and found out that the Calcium Chloride from air dehumidifiers is also soluble in ethanol.
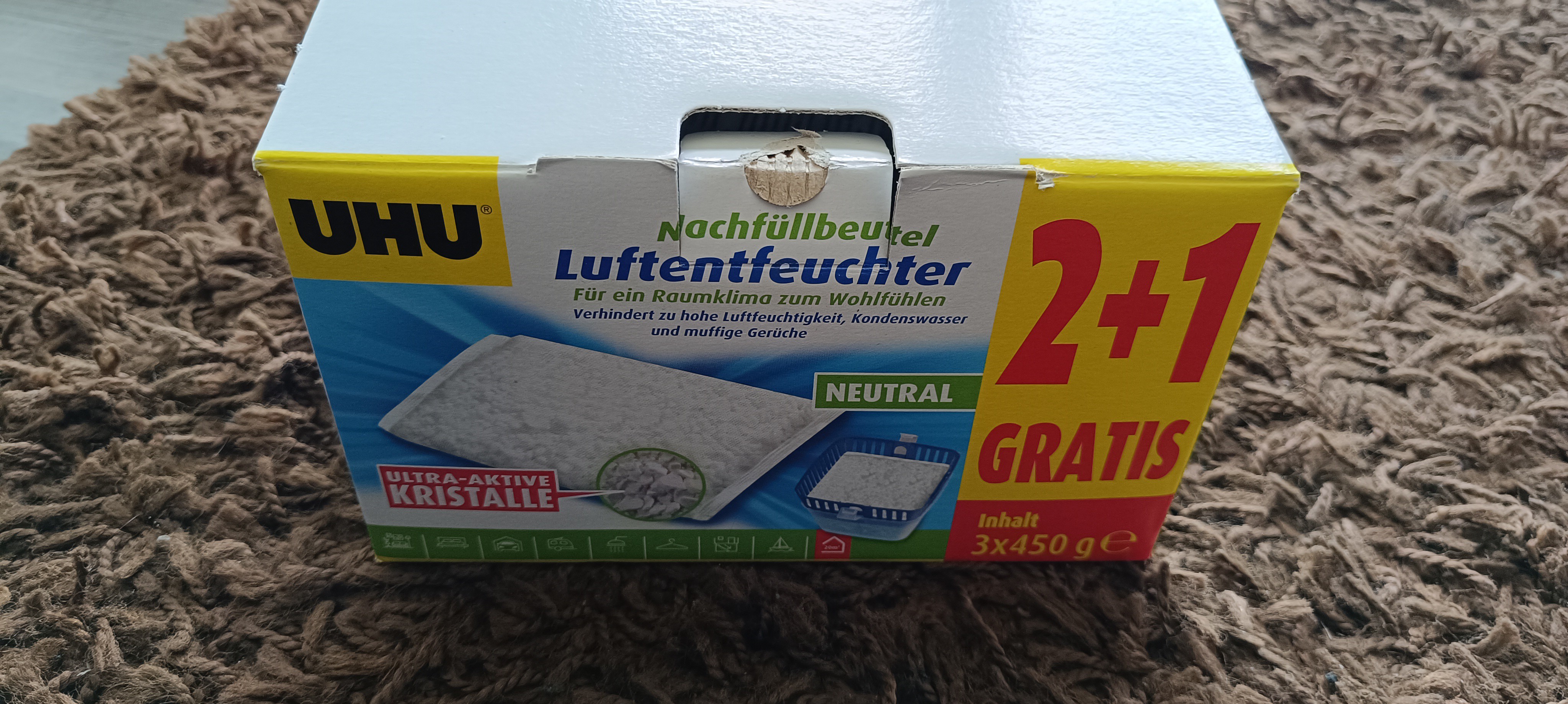
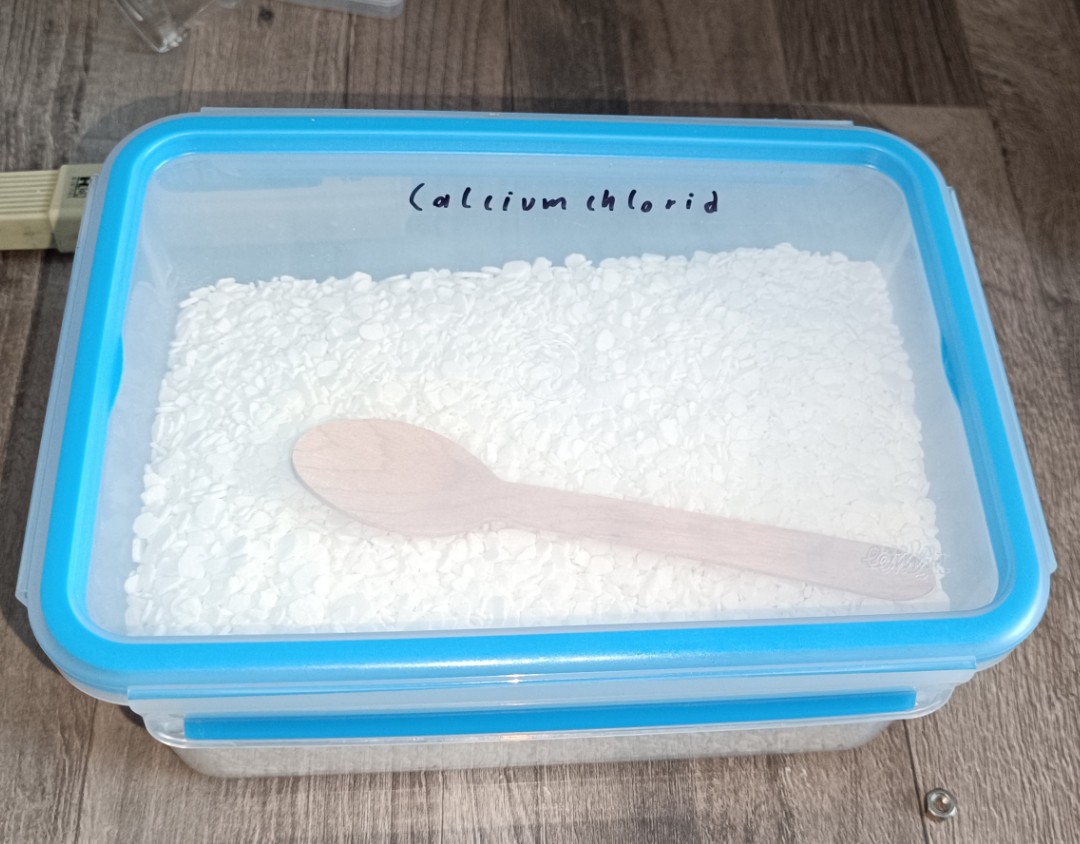
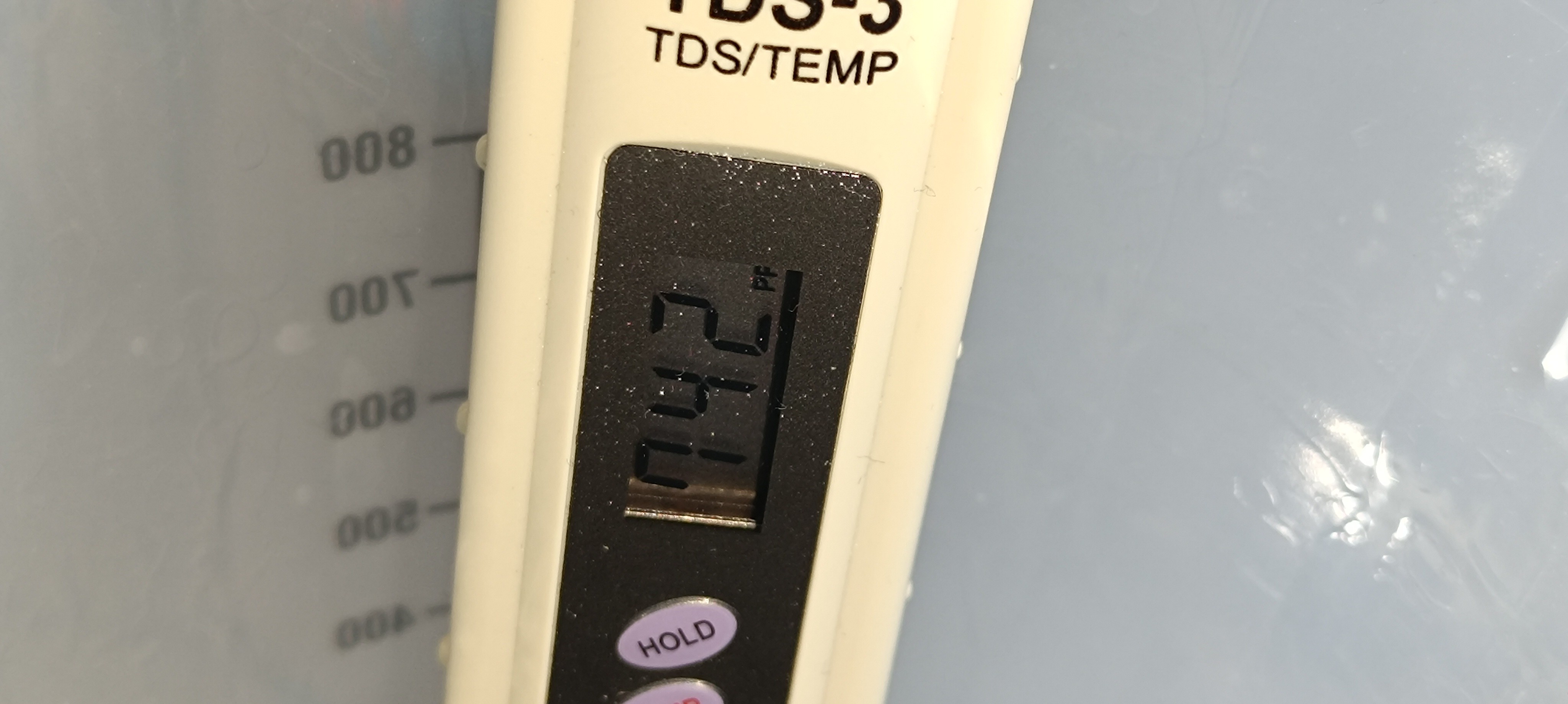
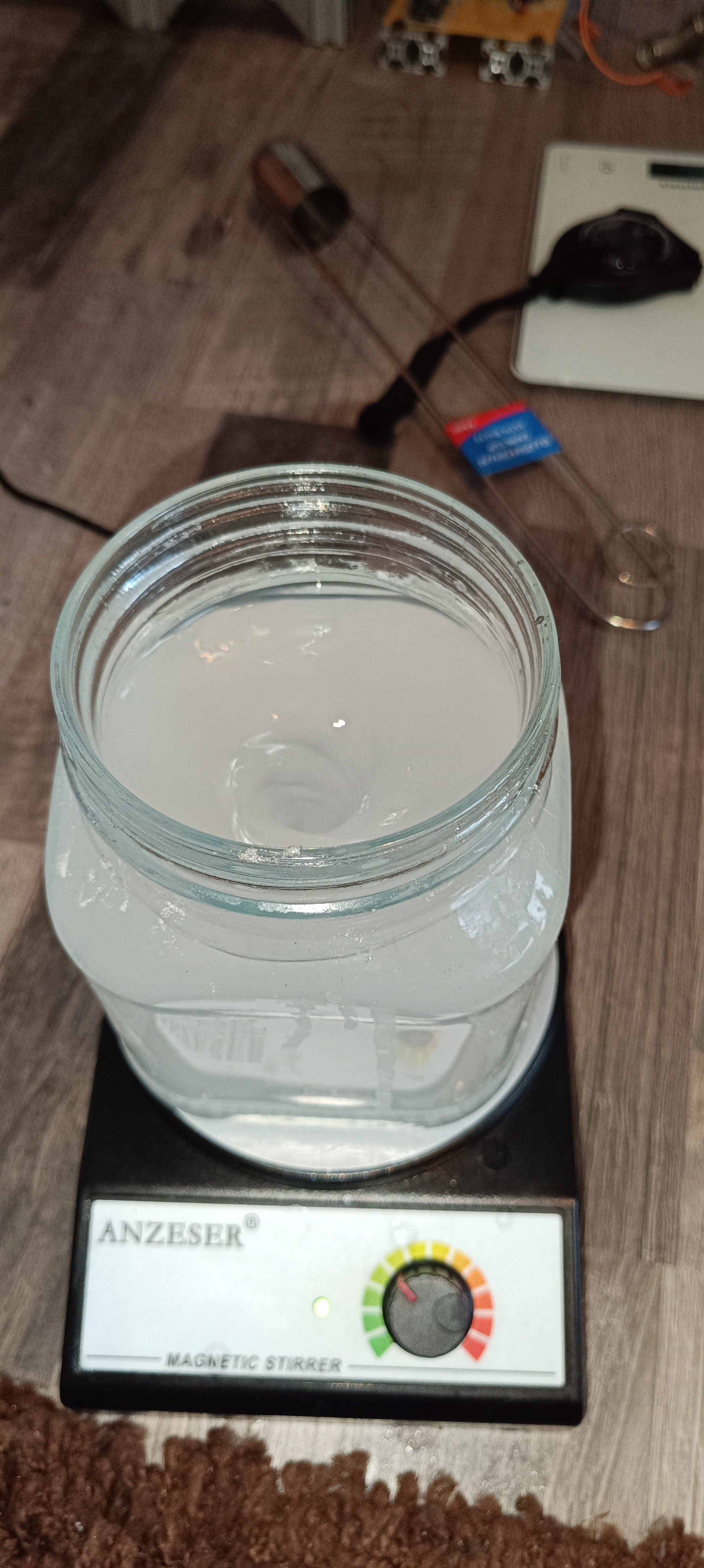
The Sodium Chloride was good for increasing conductivity, but after working with it for a while I saw that it was also very corrosive on the brass, copper, and aluminum parts of the printhead that I could not replace with the last update.
Since it is used for dehumidifying, it is very hygroscopic and forms a closed layer with water underneath it wherever it gets spilled while testing. So it was very corrosive and was somehow dirt attracting with its wet and flaky appearance.
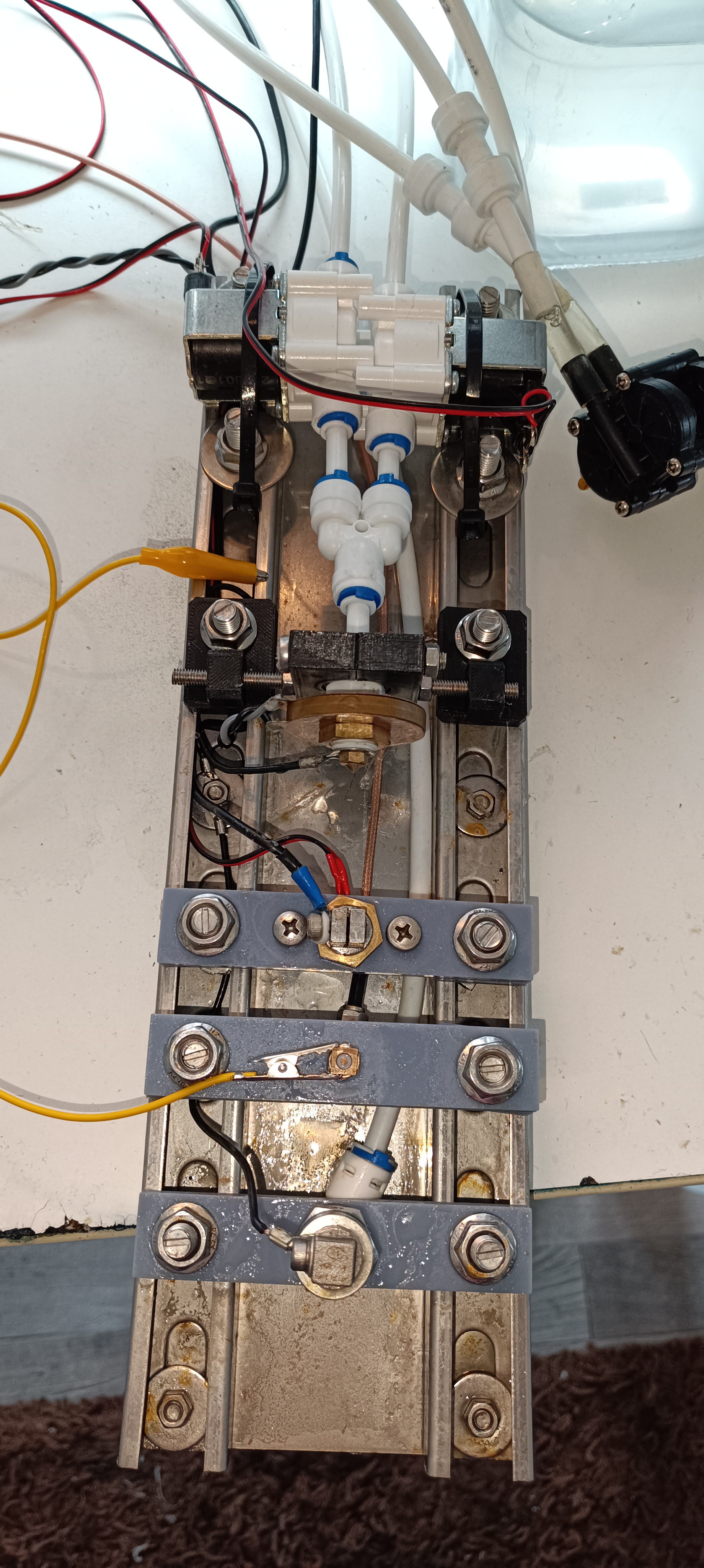
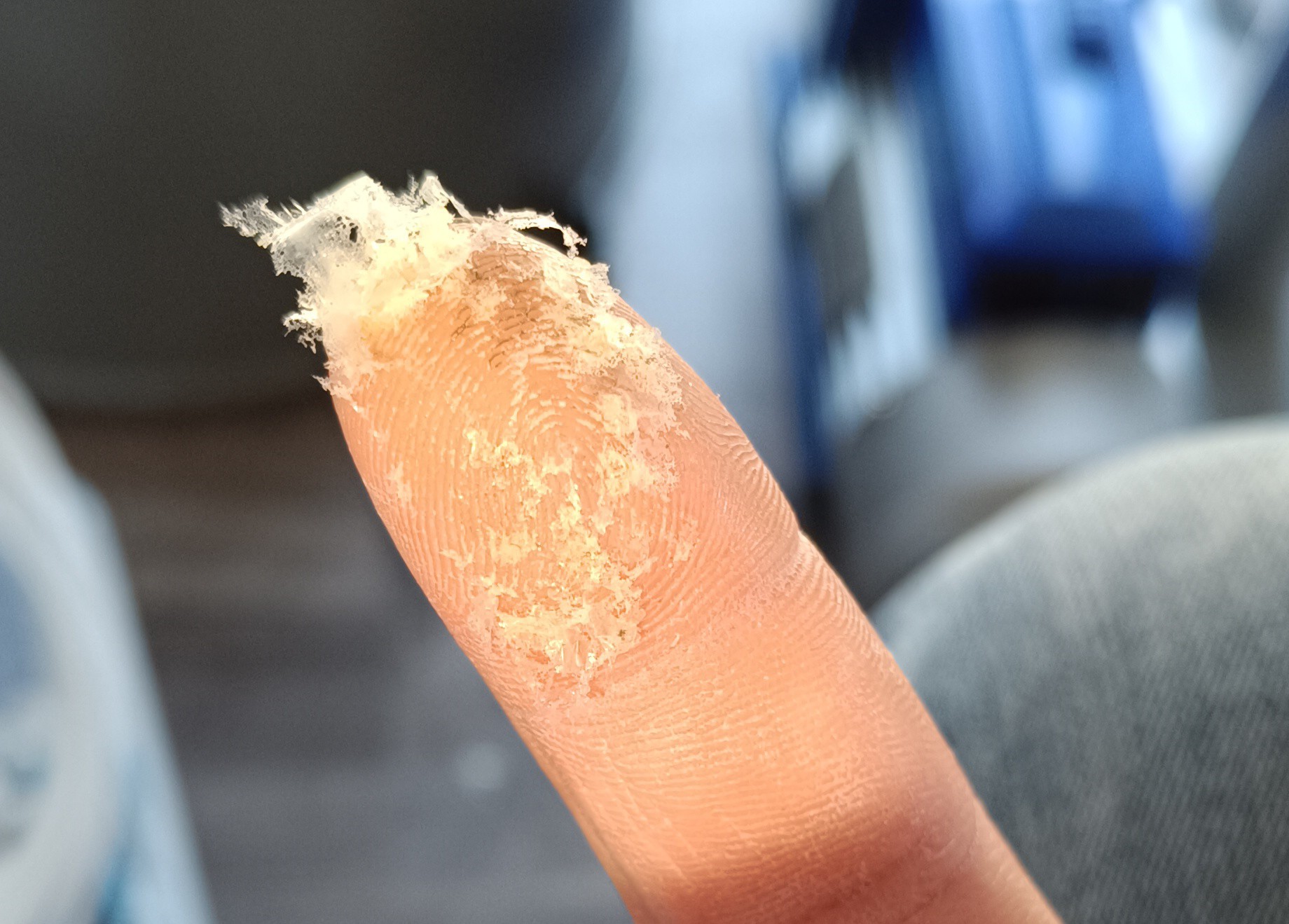
So another salt was needed.
After some searching, I found out that Sodium Acetate is also soluble in ethanol so I ordered 1kg of it.
It turned out to be a lot less corrosive than all salts I tried before and it was well soluble in ethanol. The vinegar like smell is also minimal when mixed with ethanol.
An important thing while working with it is that even though it dissolves very well, not that much of it dissolves in ethanol, and if the solution gets saturated, it tends to crystallize and settle on the bottom, which can cause problems at places that are not always filled with ink like vacuum lines and solenoid valves.
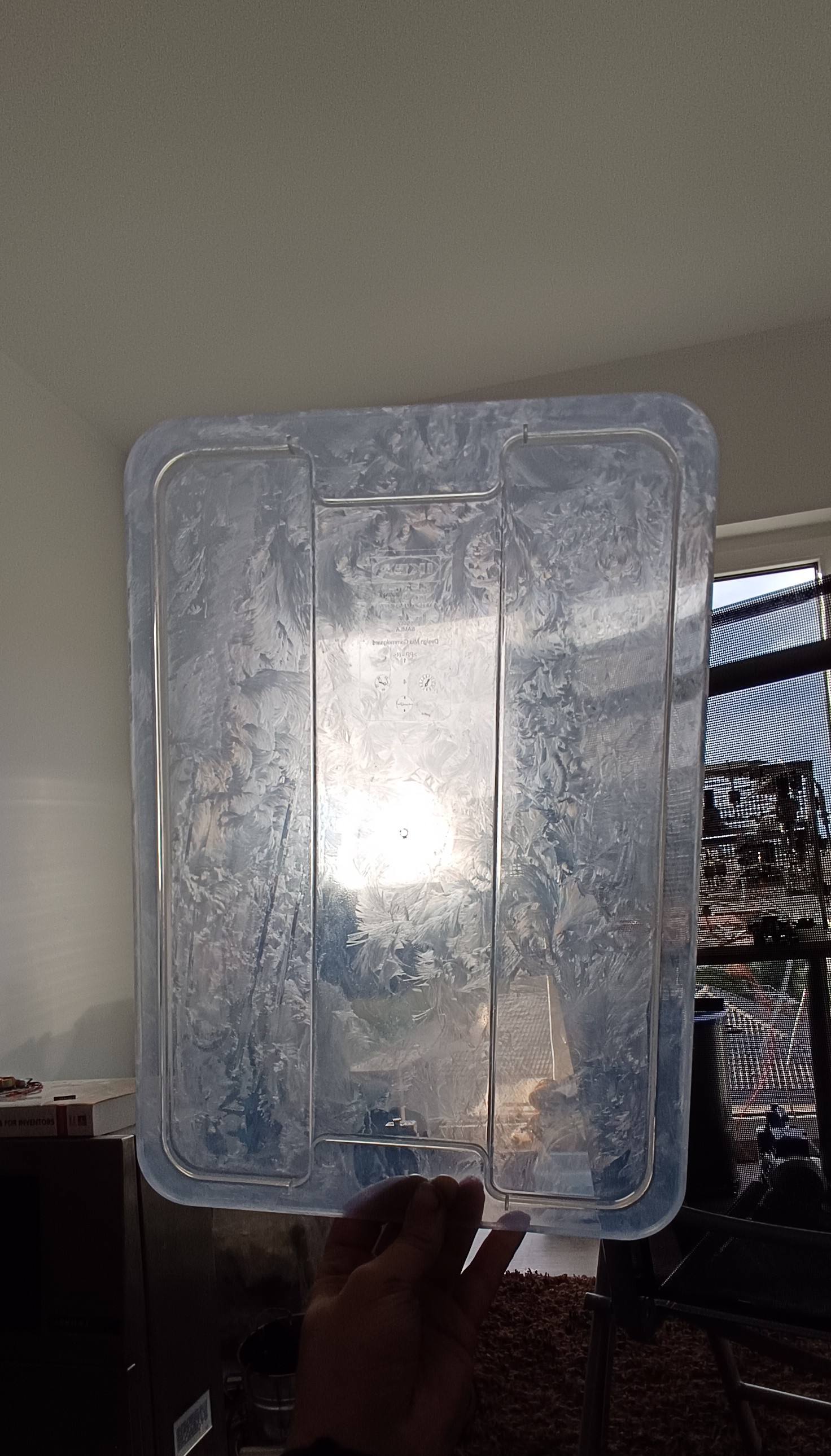
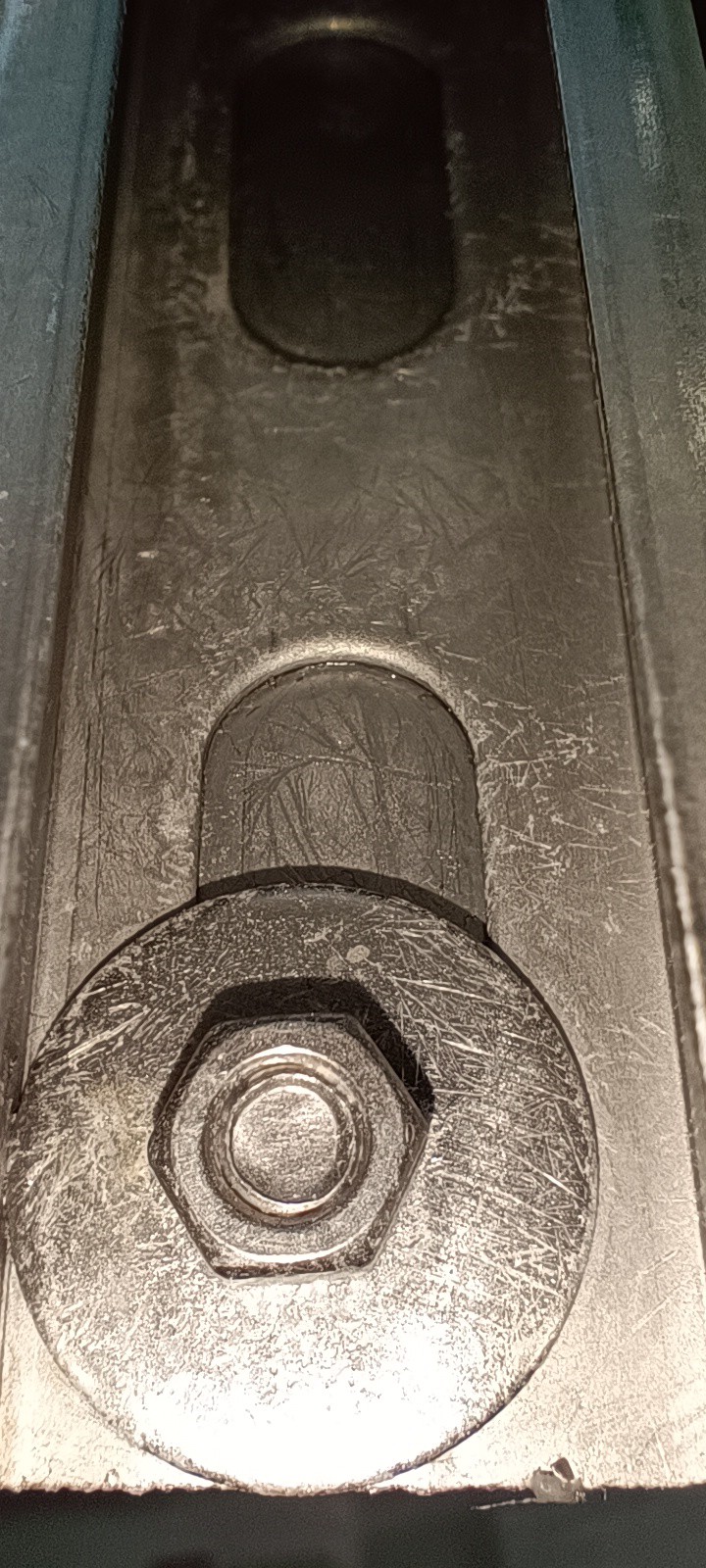
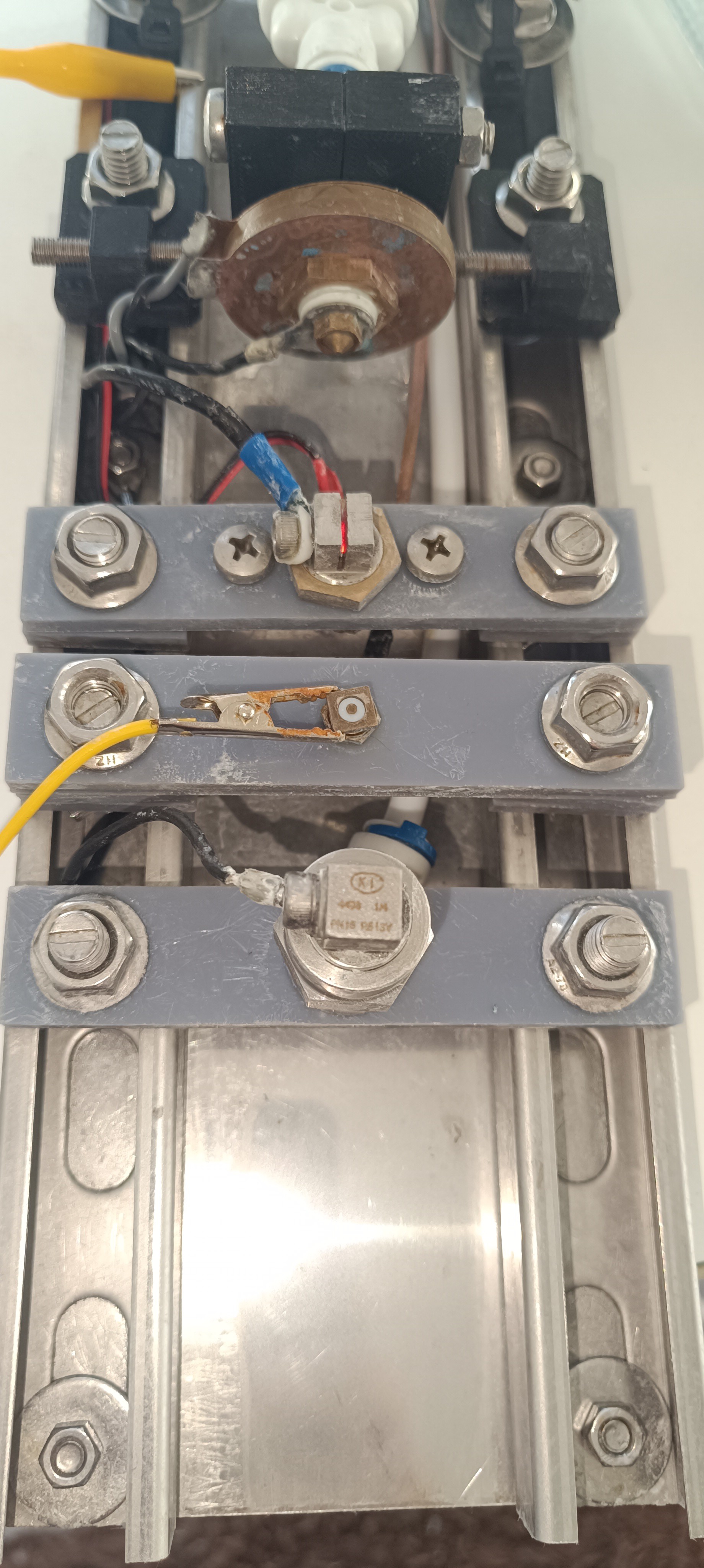
In contrast to Calcium Chloride, it's easy to wash it away with ethanol or water to clean the printhead.
At the time I'm writing this, I'm still using the Sodium Acetate without any major problems.
For now, there are:
- The Temperature in ⁰C
- The Conductivity in ppm
- The Viscosity in seconds for draining
While the conductivity and temperature readings give you the current temperature in ⁰C and conductivity in ppm, the viscosity reading is just a number that equals an unknown viscosity without a calibration factor. It still shows a rise or fall of the counted time if the viscosity rises or falls and can be used to keep the viscosity steady.
After working for some time with this viscosity measuring method, I noticed that the time count varies if some dirt particle enters the nozzle without blocking the stream. When this happens the stream is still present, but the orifice size gets slightly reduced which leads to a longer drain time without a change in viscosity.
This measuring method would also no longer be possible if I would switch to a pump feed system instead of a pressurized air feed system, in the future, since this would no longer have a pressurized tank.
Because of these drawbacks, I replaced it with a falling ball viscosimeter which they also use in some commercial CIJ Printers.
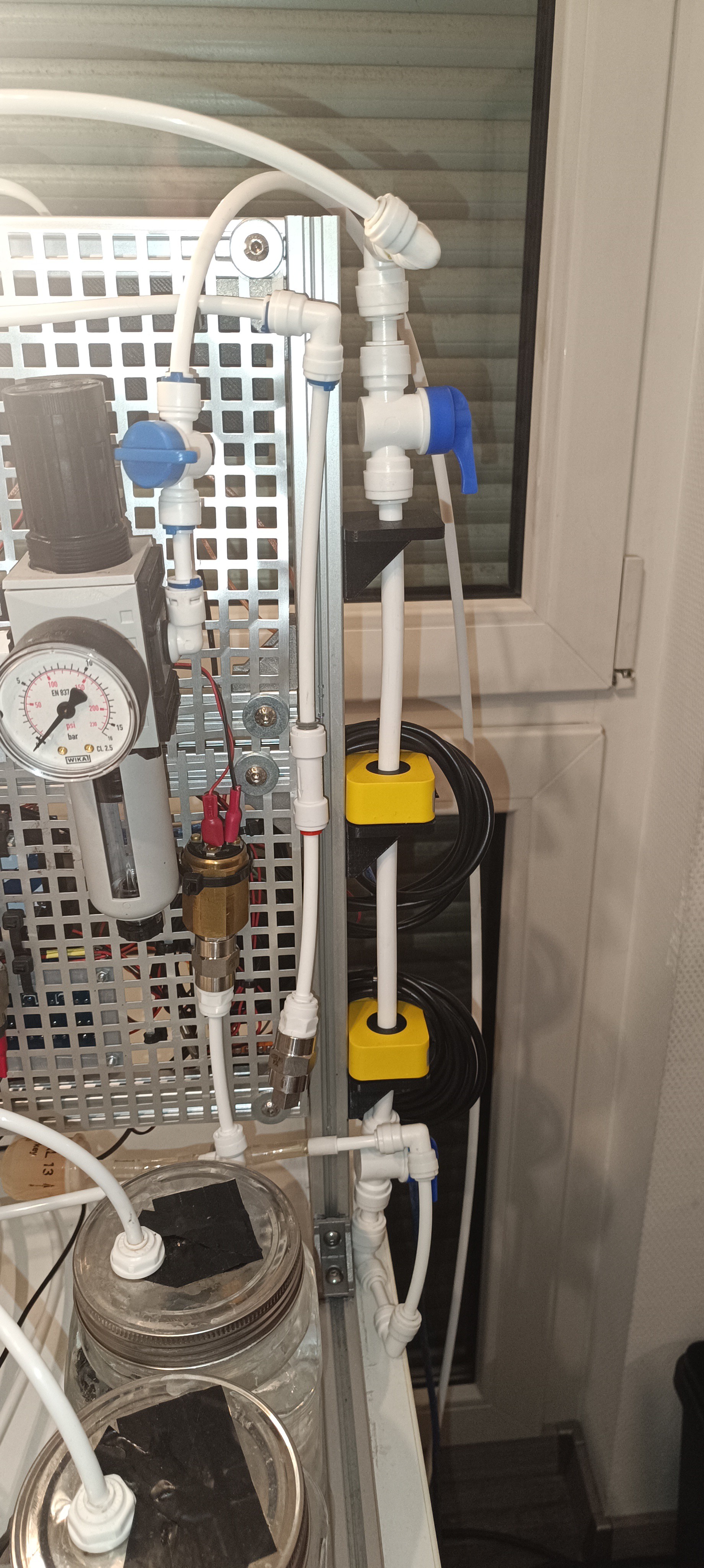
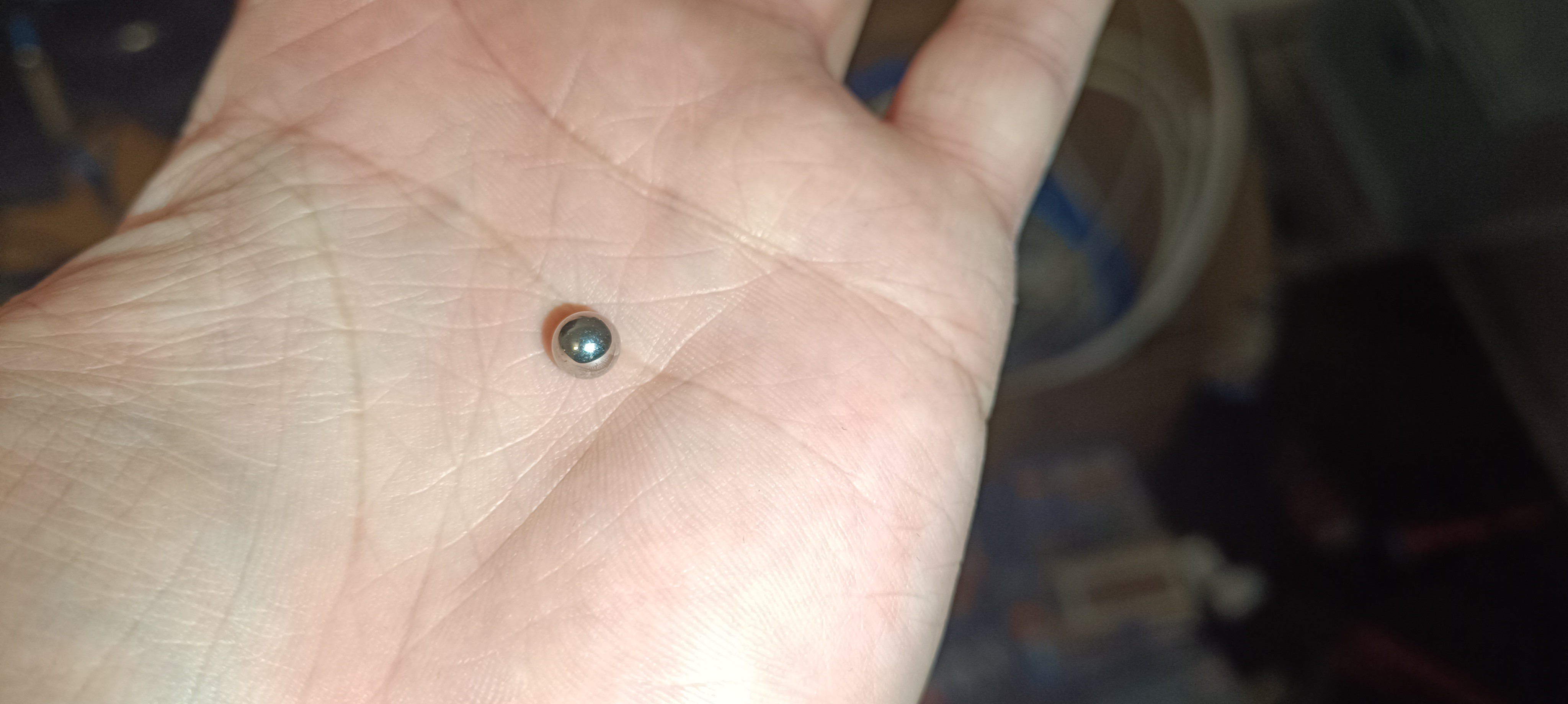
The falling ball viscosimeter works by lifting a steel ball in a fuild filled pipe and dropping it while counting the time it needs to fall.
I will write more about it in the next build log.
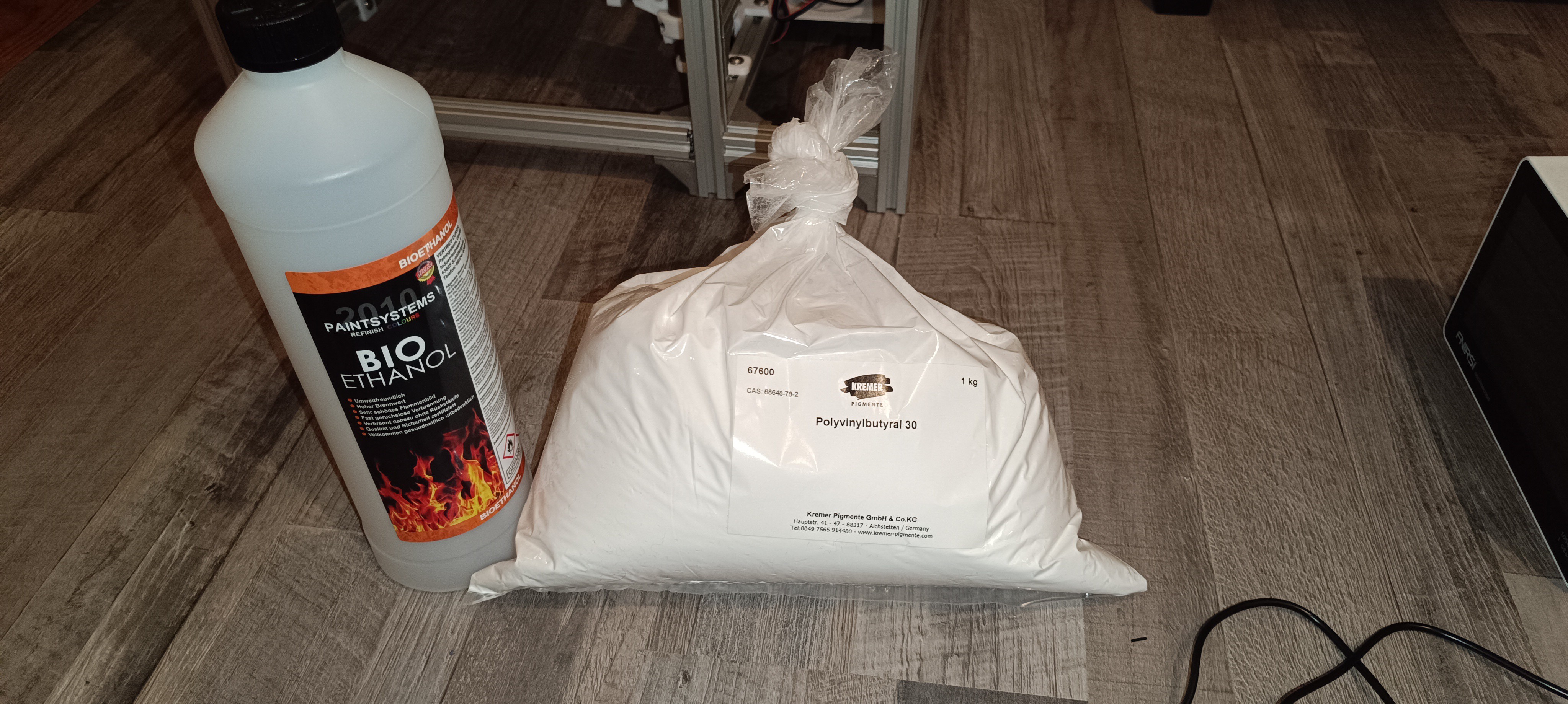
For mixing a real ink, that can be used for printing, there needs to be something in it that remains when the ethanol evaporates. While the sodium acetate crystals also remain when the ethanol drys up, they do not stick to the surface very well and they would dissolve again if the surface gets wiped with water.
By adding polyvinylbutyral to the ethanol + sodium acetate mix, not only the viscosity can be modified to fit your needs, but the PVB also sticks nice to the surface and forms a smooth and water resistant coating.
So, it's possible to mix a clear ink from only these 3 ingredients, and by adding some pigments it would also be possible to mix a colored ink.
I think, with that, the ink should be ready for printing without further modifications and as soon as the printing process is working it could actually be used.
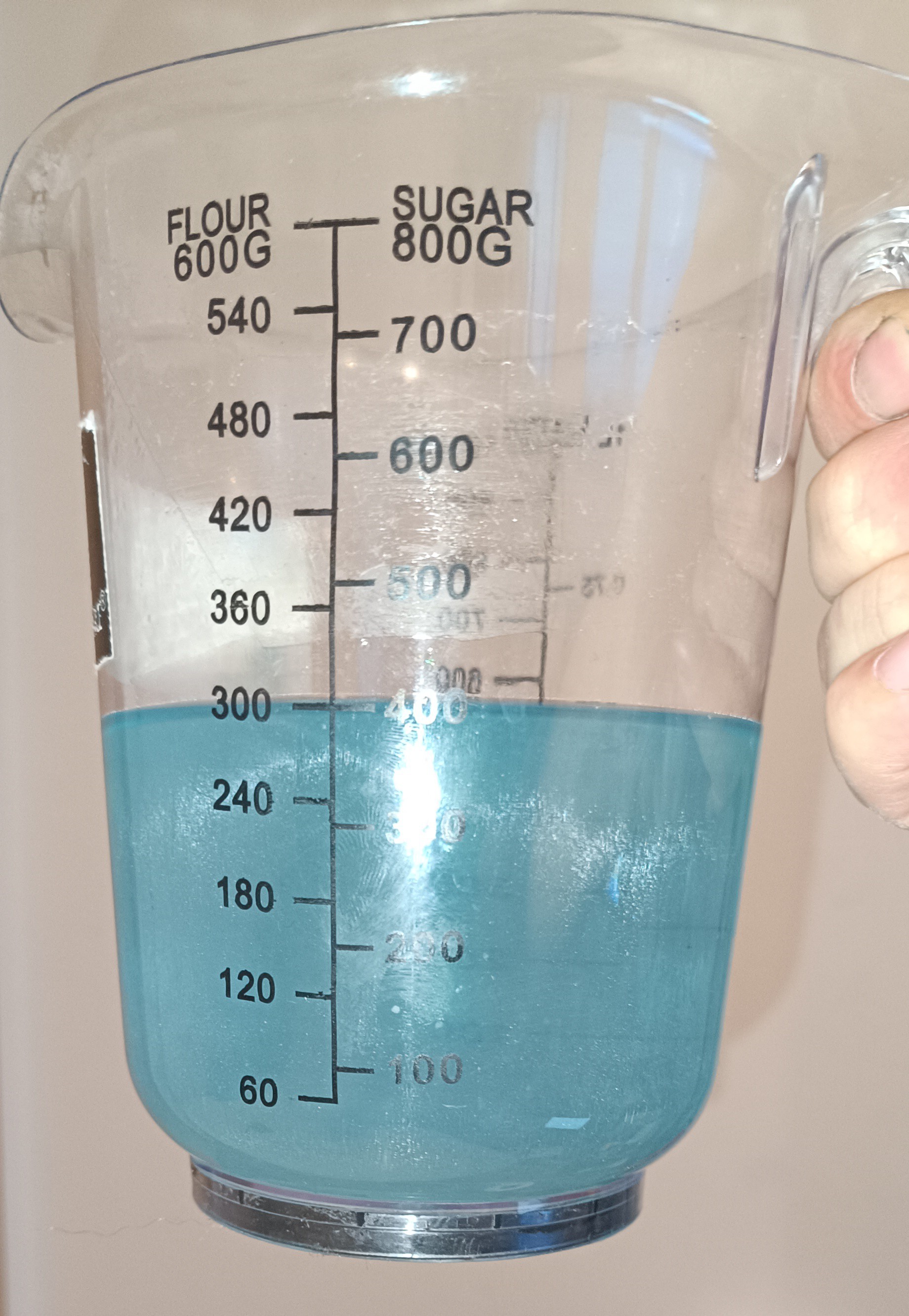
Discussions
Become a Hackaday.io Member
Create an account to leave a comment. Already have an account? Log In.