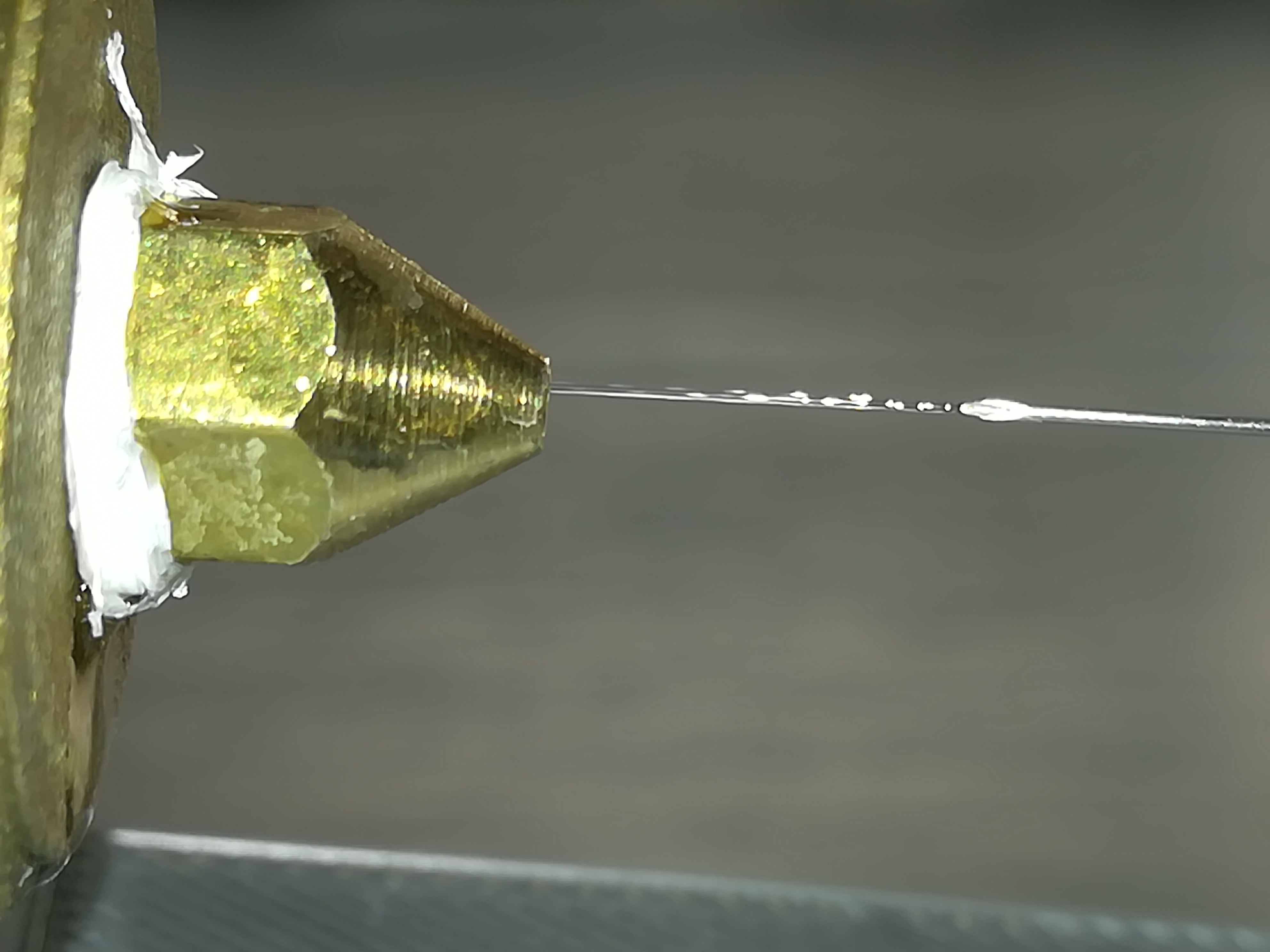
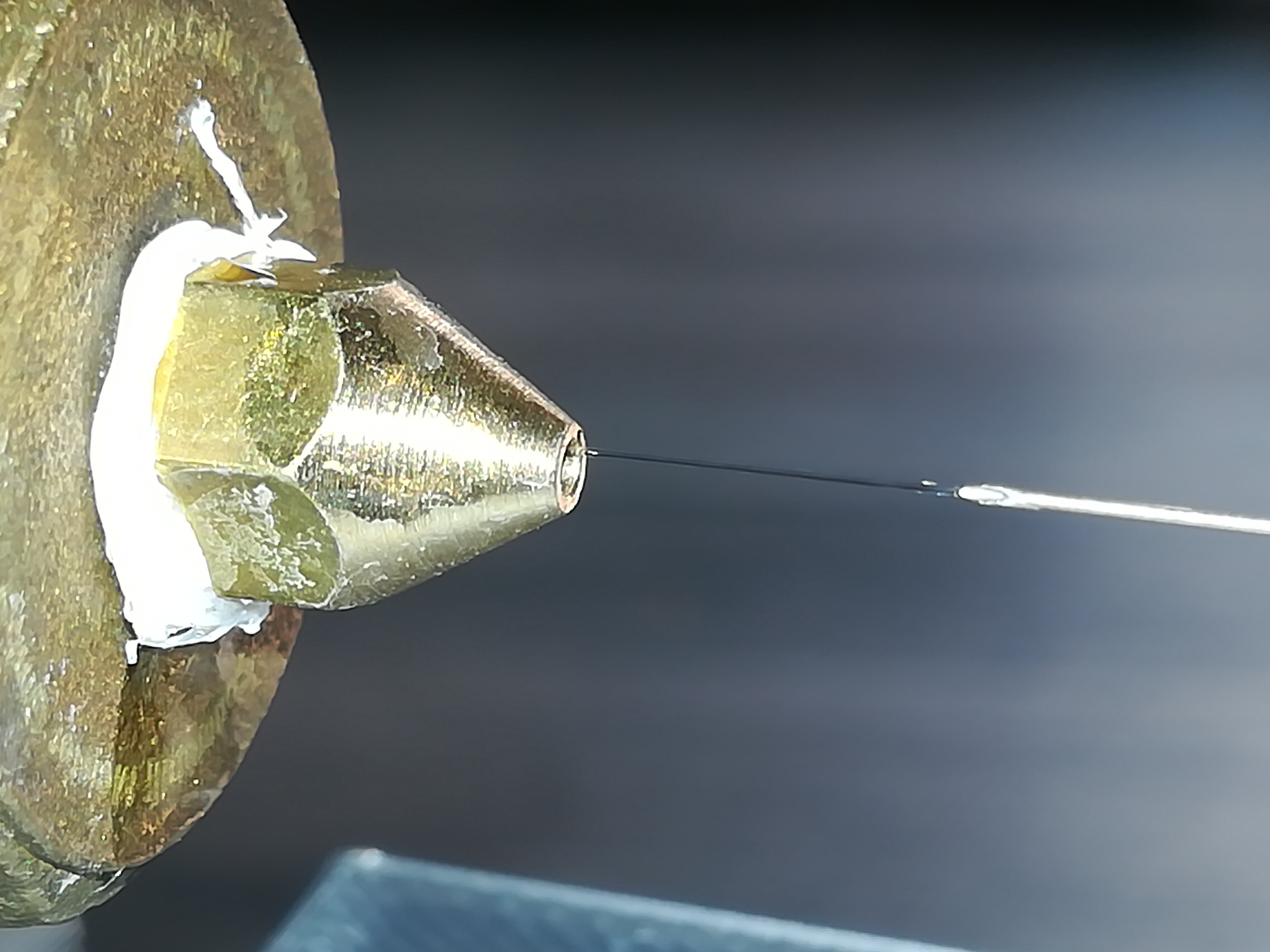
Over the last days I tested out the cycle to find out design flaws and improve everything to get it working reliably.
I also wired everything, so that I can now control everything from the Raspberry PI by setting the pin states and also read all the sensors.
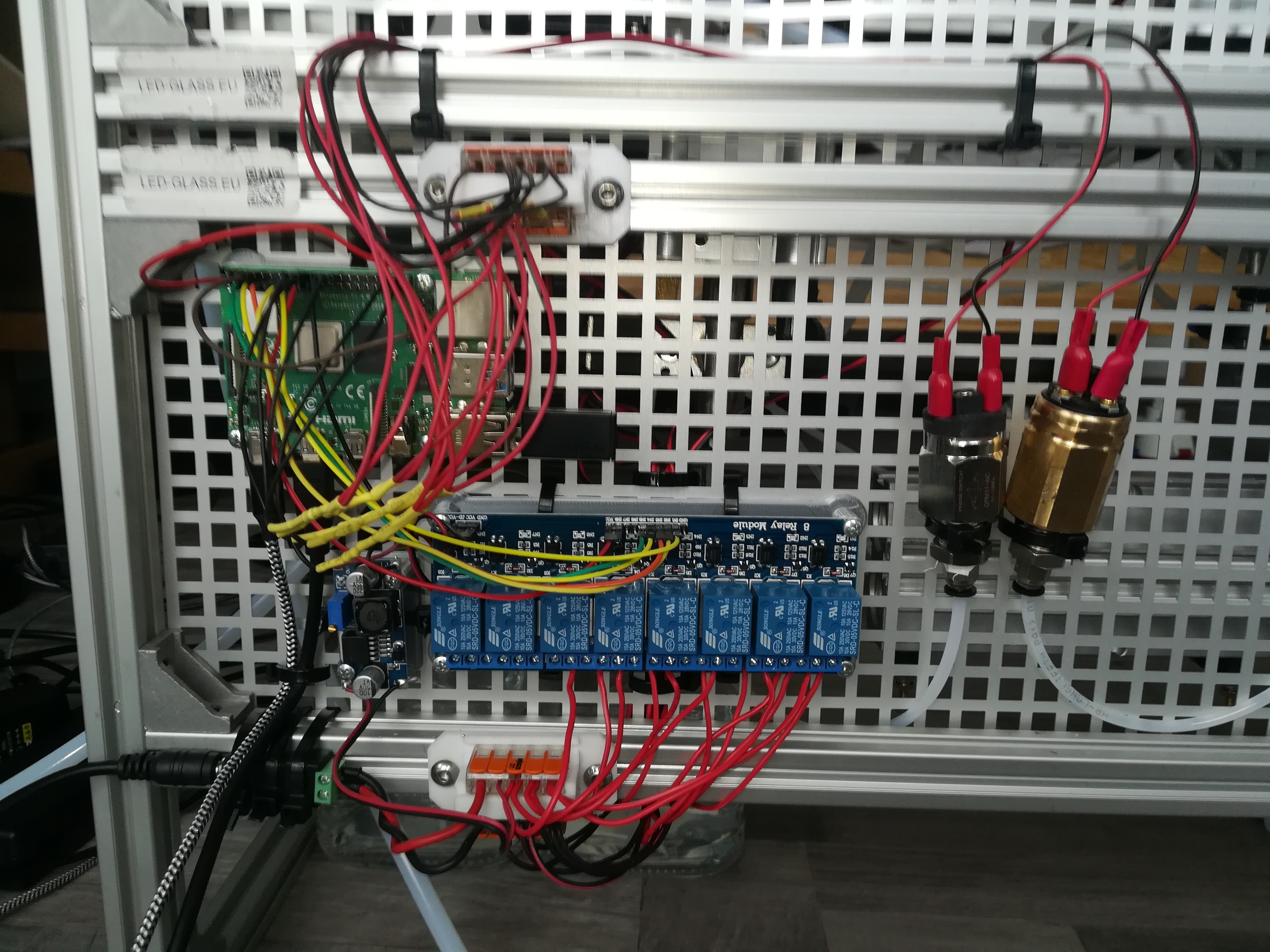
I wired 5 relays, a vacuum switch, a pressure switch, the upper and lower switch of the reservoir and the upper and lower switch of the viscosity counter to the Raspberry Pi.

Decided to remove the float switches from the ink and makeup bottle, because I think it will be more practical to check their level by just looking on them - Like you check your filament spool before starting a print.
It's also no problem to refill them while the cycle is running, because they are not pressurized and only used every few seconds if ink/makeup is needed.
The bottles could also be replaced by larger bottles or canisters if the printer's use case would need a lot of ink/makeup.
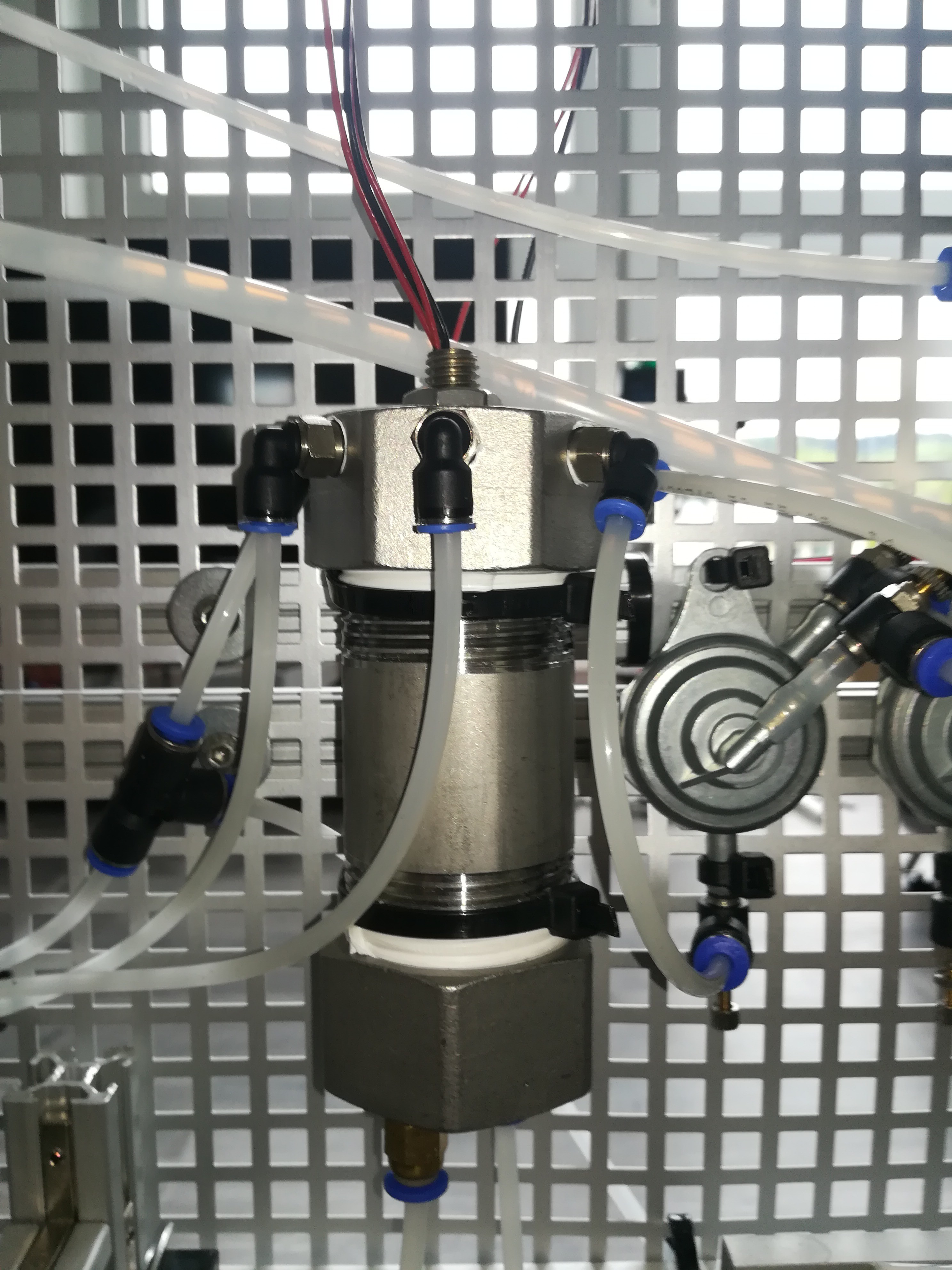
Added one more vacuum connection to the reservoir to have 2*2mm inner tube diameter for a higher vacuum throughput.
This was needed to be able to draw ink/makeup from the bottles while the return line is feeding the ink back to the reservoir.
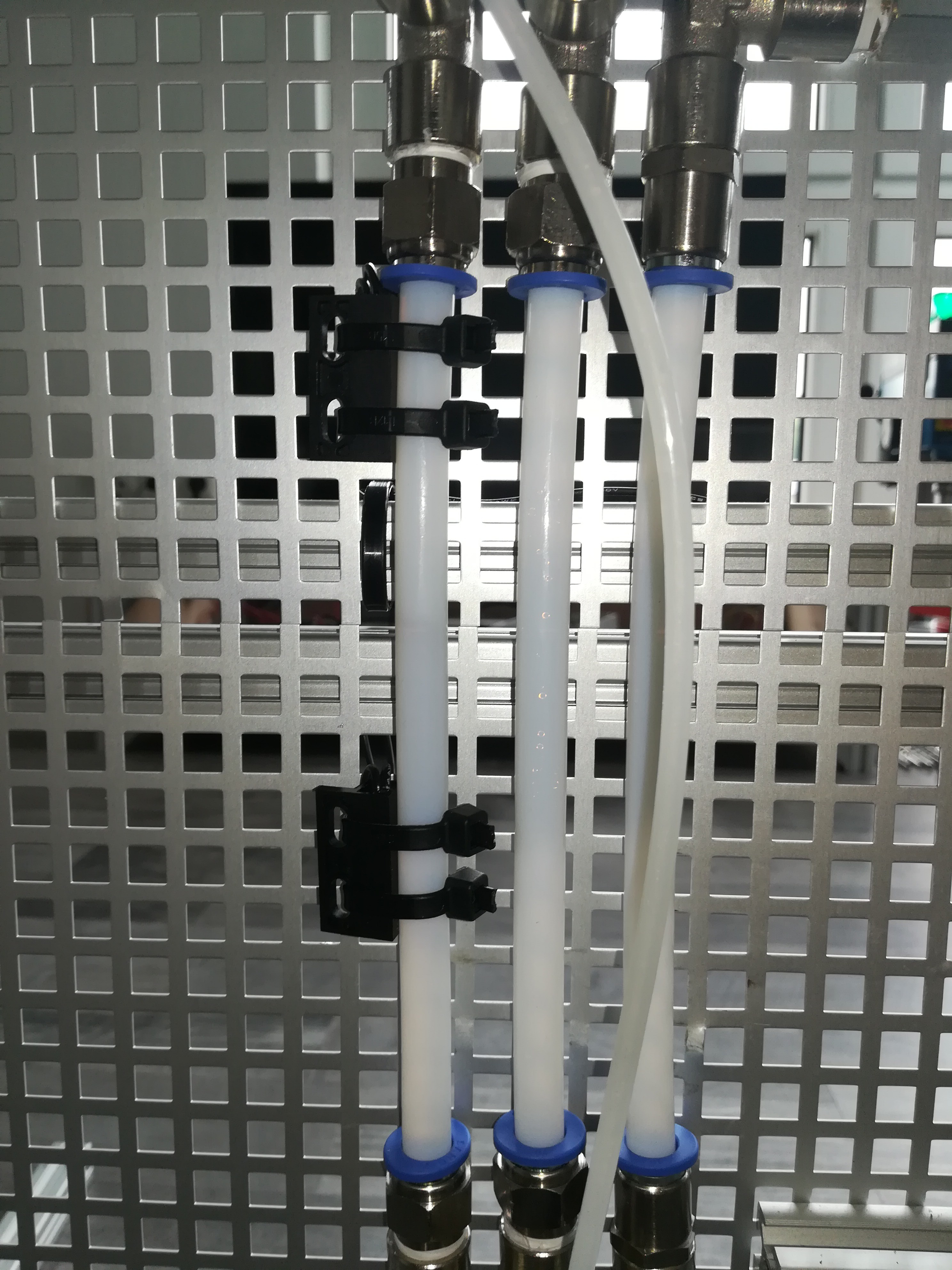
Changed the stainless steel tube and the two other tubes to PTFE tubes, because the stainless steel tubes inner surface was very rough, so that the magnetic float got stuck on it. It's also better because it is translucent, so you can see the float moving.
Also added a vacuum gauge to the vacuum overflow tube.
Changed some parts of the pneumatics assembly.
An important change was separating the pump solenoid from the ink/makeup solenoid block.
Before, the pump solenoid let the displaced air from the pump's piston flow into the vacuum lines, what caused serveral problems. By separating the solenoid that's no longer a problem.
An interim printhead to complete the cycle.
The ink (water) is streaming from the viscosity counter to a syringe needle into an 1mm 3d printer nozzle back to the reservoir.
The check valve before the syringe is to provide some resistance, so that the needle stops dripping if the pressure is turned off.
The check valve after the 1mm nozzle is also to provide some resistance, but this time to prevent the vacuum level from dropping too much through the return line.
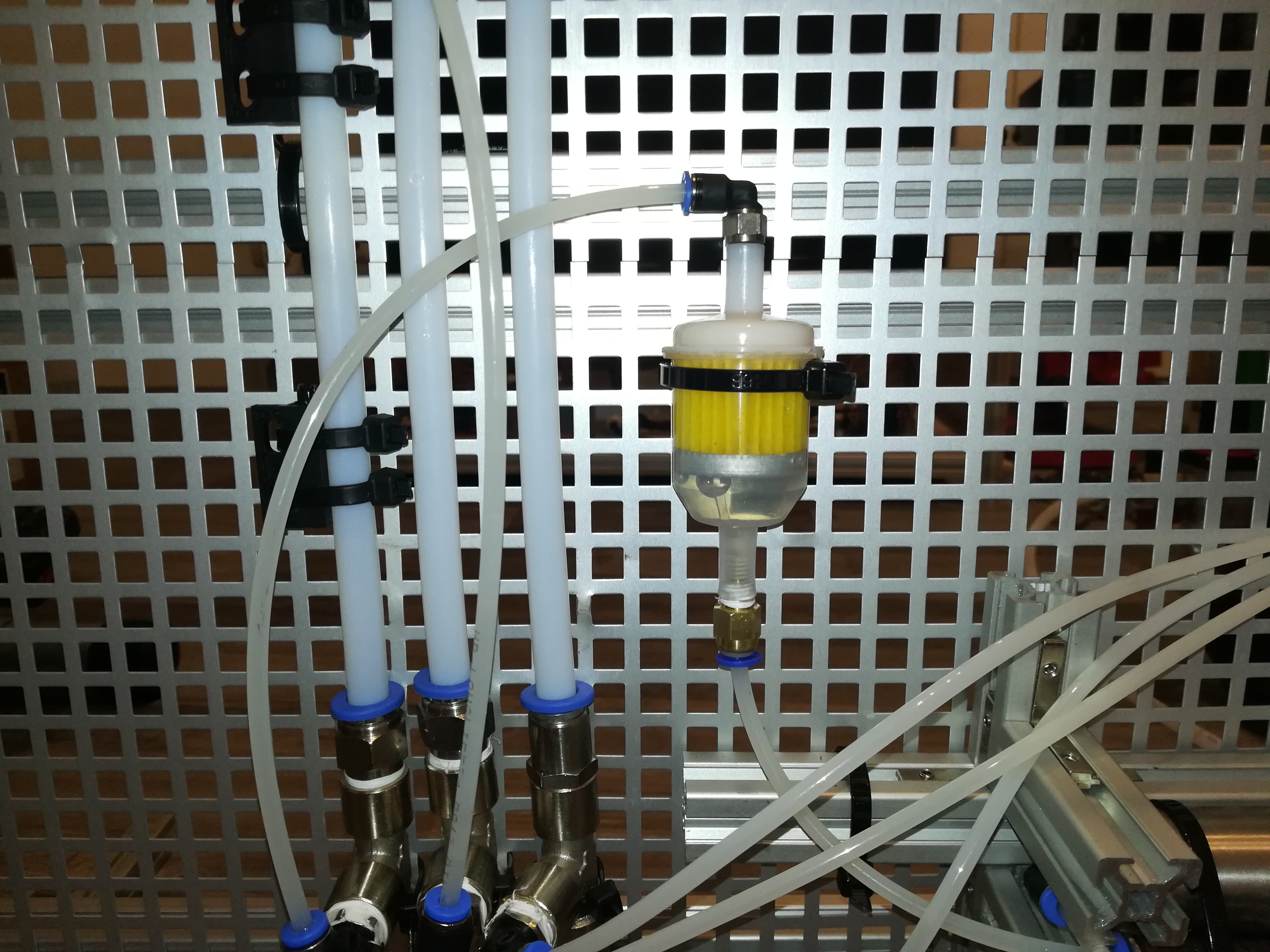
Added a filter to keep the ink clean.
Now I only have to write a CIJ Cycle Controller python script to get the cycle to work.
Doing this will just take some time, but I have no doubt that I will get it to work by using try and error and reading StackOverflow sites :)
The more critical part on which I want to work first will be building a nozzle that can split the ink stream into droplets.
To do this I will research ultrasonic vibration and pizo ceramics + their drivers.
I want to start by building some mist makers and their drivers.
Discussions
Become a Hackaday.io Member
Create an account to leave a comment. Already have an account? Log In.