This is the pawn from the Fusion360 CAM samples, scaled 55% to fit in the 1" stock that I have. All cut with the 2mm cutoff tool.
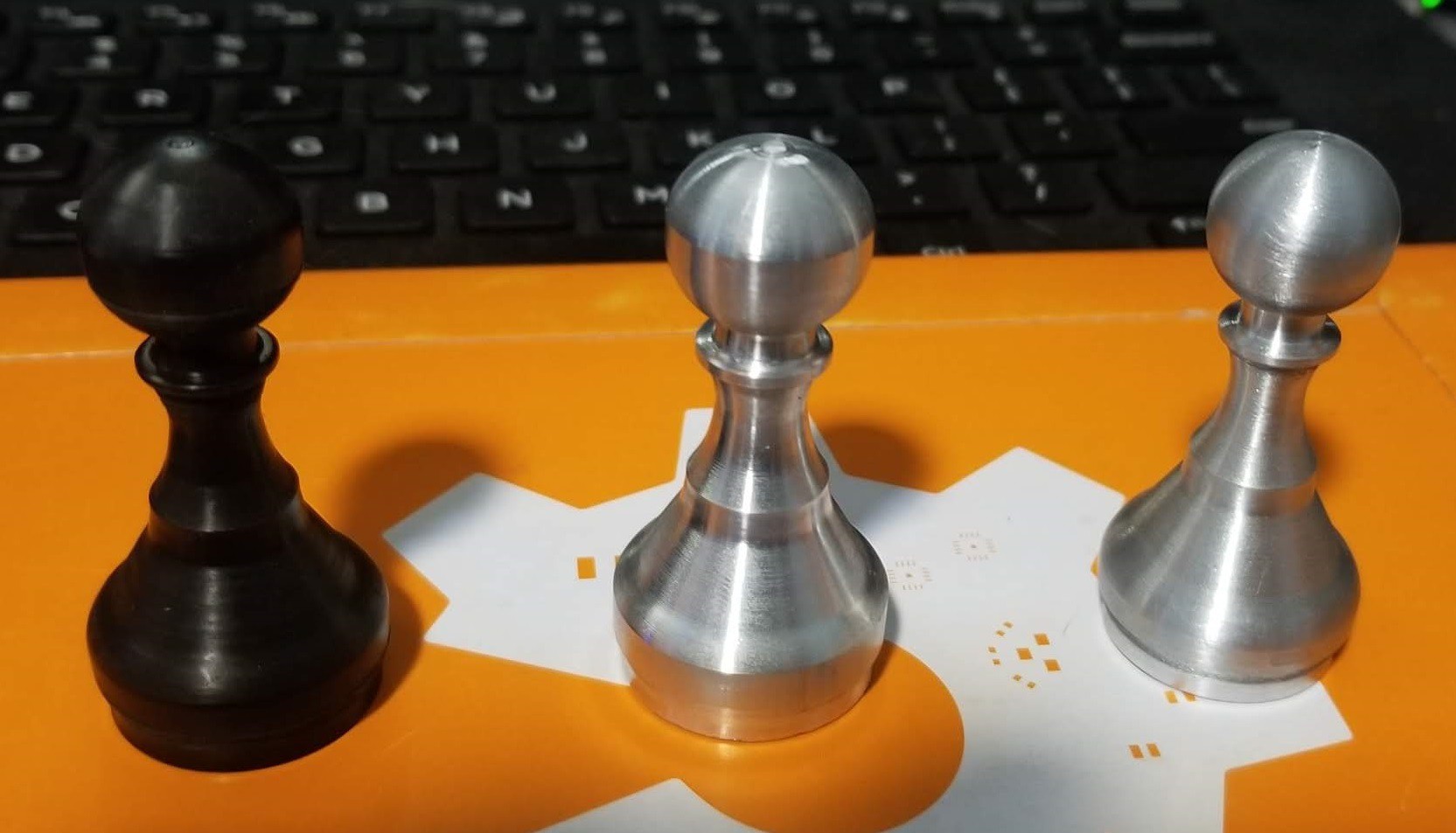
From left to right:
0: The first attempt I had the cutoff tool programmed as 4mm width. Start again.
1: Delrin. 2mm stepover and 1200RPM. Looks pretty good.
1.9: Not shown. Aluminum same settings. Horrible screaming chatter. Then I typed G0X0 instead of G53G0X and crashed the tool into the work....
2.0 Aluminum. 540RPM. 1mm stepover. Looks pretty good. But fat. Clearly the tool moved when I crashed it. Duh. Thers a clear step in the sphere - I think because the cutoff tool end was angled not square.
3 Aluminum. Reset the tool library. Also ground the end of the tool square - it previously had a slight angle on the end for clean manual cutoffs. The end ball actually looks spherical. Happy.
I also worked out my process for tool setting.
- Mount the Fowler electronic edge finder in the chuck - gently so as not to squish it.
- Offer up the tool to the edge finder radius and jog till the light it at on/off flicker threshold.
- Jog Z+ off the end
- Jog X-0.1
- Jog Z- till we find the flicker.
- Touch off 0:0
I should be able to use this whenever I switch from mill to lathe mode too after clamping down the toolpost. (except for the 4-jaw chuck)
Discussions
Become a Hackaday.io Member
Create an account to leave a comment. Already have an account? Log In.