(copypasted from mainline project: #Minamil: a minimal CNC mill. And friends. )
Responding to a comment on an earlier log, I wrote:
I haven't written much yet about the blue Wen dremeloid used for most of this project so far to keep it cheap. The main trick [...blah blah...] acceptable runout. I don't think it was ever going to cut the SSOP footprint tho.
Since then, I got some renewed motivation to try again...
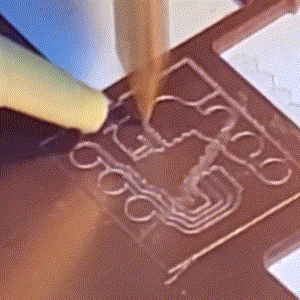
...and made it happen. A perfect spindle would be nice, but in the spirit of pushing down the hardware requirement and frustration with the "better" tool, I went back for another round of tweaking away runout. I'm finding more tricks but don't really have that down to a method for a good how-to yet.
The overall process for milling this example went something like:
- use stable magnification
- I've used a phone (camera) held in a phone claw on a tripod...
- ...until gaining unfair advantage coincident with this iteration
- tweak the v-bit to small runout (...see? just type the words and its done...)
- adjust spindle speed to minimize resonant vibration at v-bit tip
- I've read of doing this by sound and/or feel, but I had to actually watch the tip of the bit under magnification while adjusting speed
- assuming speed control either onboard or external to the rotary tool
- peck a hole just through the copperplate
- 1 oz. copper is nominally 0.035 mm or 1.4 mil thick
- measure the breadth of the hole - I did it like this:
- using magnification...
- turn the v-bit sideways to view the tip edgewise as a fine point
- set jog step to 0.025 mm = one whole step (20 steps/rev, 2 revs/mm)
- position the bit over the hole just a step above the surface
- jog a few steps to one side
- step the bit point back toward the hole and stop at the first edge
- continuing in the same direction, count steps across to the other edge
- hole diameter = steps * 0.025 mm
- ideally 4 steps for a narrow-angle 0.1 mm v-vbit
- more likely 5 for a "perfect" setup, and 6 or 7 will be pretty good
- use measured peck diameter as tool diameter for generating gcode
Tool changes for drilling and milling won't be so carefully precise. Notice in the video below:
- pilot drilled the through-holes with the v-bit in an attempt to help the center the less carefully chucked drill bit
- maybe might have helped with precision of through-hole locations maybe
- didn't prevent the swinging drill from carving an oversize hole in the top surface
- drill did self-center and exit holes are not oversize
- narrowing of through-holes with depth somewhat visible in vid thumbnail below
Sub-2-minute video for eye-candy:
Discussions
Become a Hackaday.io Member
Create an account to leave a comment. Already have an account? Log In.