The decision was made to shrinkwrap a traditional printable grid pattern on a smooth speaker stand shell. The thinnest horizontal walls in PLA are .4mm. A .4mm vertical wall requires a .2mm nozzle & a lot of time, so it would be a .5mm thick shell.
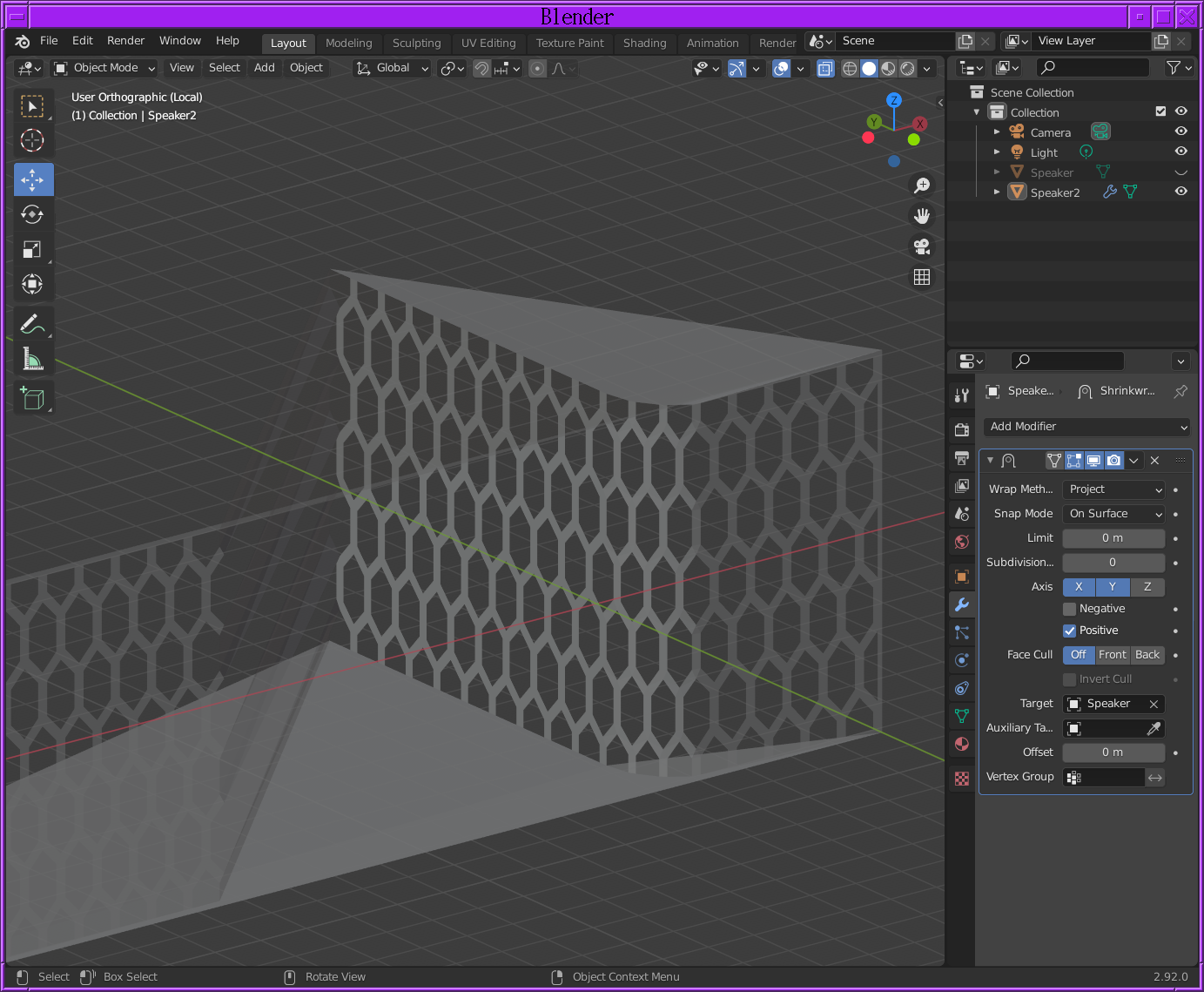
Blender happens to shrinkwrap surfaces on surfaces. The trick is selecting Project, X & Y axis. Then, it properly creates a solid with the solidify modifier.
The target needs to have parallel walls. The process leaves a lot of junk. It's not parametric. After creating a generic corner section, the corner sections would have to be fused & transformed in Blender to make the stand. There would be a solid column where the corners joined & the fusion would just use booleans.
There could be a simple python program which mapped a sketch on a hard coded corner section.
Discussions
Become a Hackaday.io Member
Create an account to leave a comment. Already have an account? Log In.