When considering the form of the hull there are two main criteria to consider; speed and stability. Two major components of efficiency of a boat hull are the wetted surface area and the wave making abilities of the hull. Minimising both of these resistance components allows for more efficient operation of the boat platform, including higher top speed and better acceleration. When considering displacement hulls (hulls that are displaced in the water when travelling at speed), the monohull typically has a higher wetted surface area than a catamaran.
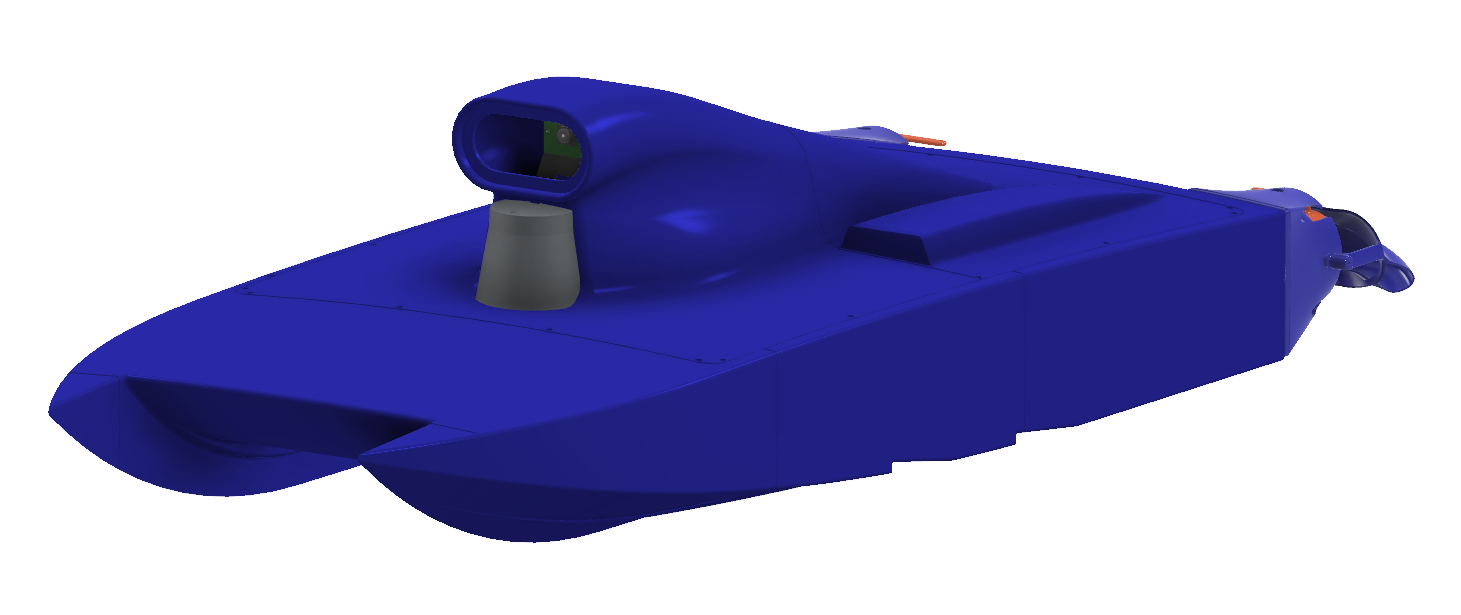
However, to reduce the wetted surface area of a hull dramatically, a planing or hydrofoiling hull can be used. These hulls allow the boat hull to rise above the water when traveling at speed. In this work, a planing hull was determined to offer superior performance to displacement hulls, and it was simpler to design than a hydrofoiling hull. The stability of a vessel is inherently determined by its size and weight distribution. As the weight and placement of components in the hull are usually already determined, the size and dimensions of the hull determine how stable the vessel is on the water. A longer boat will have greater stability in pitch and a wider boat will have greater stability in roll. The most unstable axis on the majority of boats is the roll angle. This is particularly prevalent when a boat is hit side-on by waves. Having a wider hull will again help with this issue. For this reason, a catamaran was chosen due to its superior roll stability characteristics. The hull beam of this platform is 250 mm wide, this is due to manufacturing restrictions due to the 3D printer bed size and was also deemed to be stable enough for a platform of this size. The mass of the vessel should be as close as possible to the water line and lower down than the centre of buoyancy to create a statically stable craft. The weight distribution of the catamaran needs to be even (avoiding majority of weight in one hull) so as to maximise stability, hence why the battery and all electronics are mounted centrally in the boat. One of the advantages of a planing catamaran is the reduction in the wetted surface area. As seen in the figure below}, the wetted surface area can be further reduced at speed by employing a stepped hull which further reduces contact with the water while planing. Also, it is evident that spray rails help lift the boat at speeds where the boat is unable to plane and narrow hull beams are utilised to reduce the wetted surface area. A reduced area tunnel is also used on the catamaran to increase the pressure gradient in that section, effectively creating a suspension of air in the tunnel of the catamaran so as to reduce damage and vibration when the hull slams against uneven water. The jet intakes were fitted with grates to reduce the chances of injuries that could be caused by the impeller blade.
This autonomous boat platform is intended to be easily reproducible by students with reasonable knowledge of mechanical assembly. For this reason, the boat was designed in a way that it wouldn't be too big or complex for anyone to manufacture. Both composite manufacturing and 3D printing are easily accessible and achievable by most students.
Composite manufacturing offers superior strength, rigidity, and waterproofing compared to 3D printing. This is due to composite materials often employing high tensile strength and light weight fibres combined with a resin matrix to produce a high strength, lightweight part. Boat hulls are often made from fibreglass as it offers enough strength for loading on water and is lightweight. Mechanically, composite boat hulls are superior to 3D printed ones but there are a few disadvantages of this manufacturing technique to consider. Composite manufacturing requires moulds to form the shape of the hull. The moulds can be quite expensive if they require the use of a CNC machine. 3D printed moulds could cause mechanical locking due to the surface finish of a 3D printed part but this issue could be negated with preparation of the surface before manufacturing. 3D printed moulds often fail under vacuum and high temperatures. Other costs of manufacturing for composites that need to be considered are the consumable components needed (vacuum bags, breather, release film, and mould release), the materials used, and a vacuum pump (if needed).
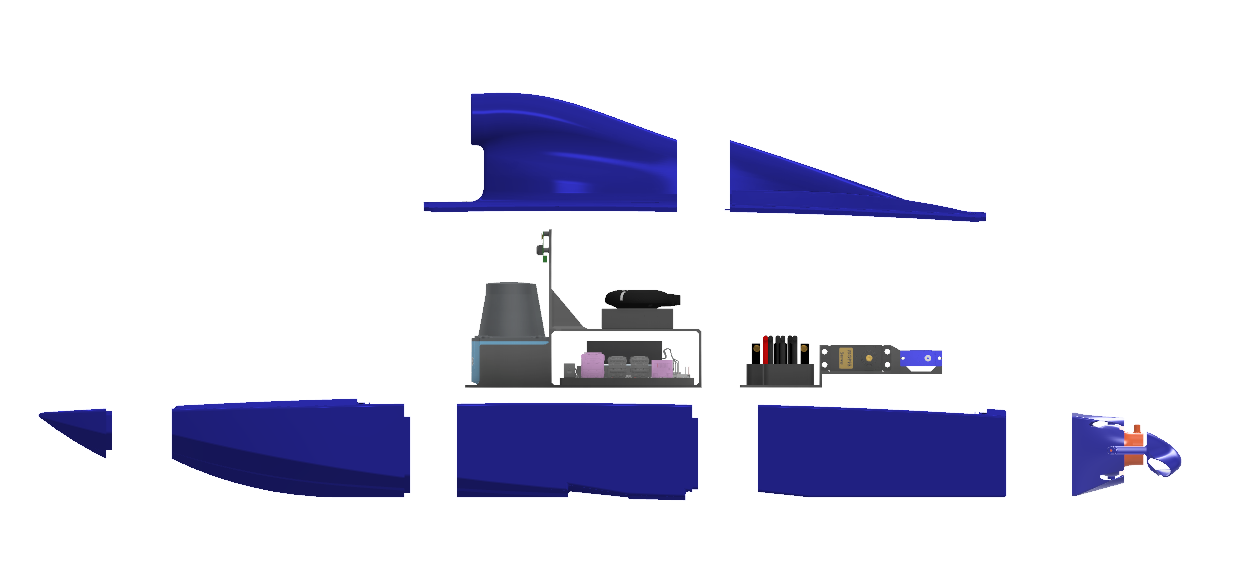
The autonomous boat platform designed for this competition was designed to fit onto a 250 mm x 210 mm x 210 mm 3D printer bed, a common size for FDM 3D printers. Four separate components have to be printed and later glued together with high performance resin (HPR). This process results in a faster and cheaper alternative to composite manufacturing as it does not require any moulds, consumables, or specialist tools. Due to PLA being able to absorb water and swell, a sealant of some kind is recommended for the 3D prints.
Discussions
Become a Hackaday.io Member
Create an account to leave a comment. Already have an account? Log In.