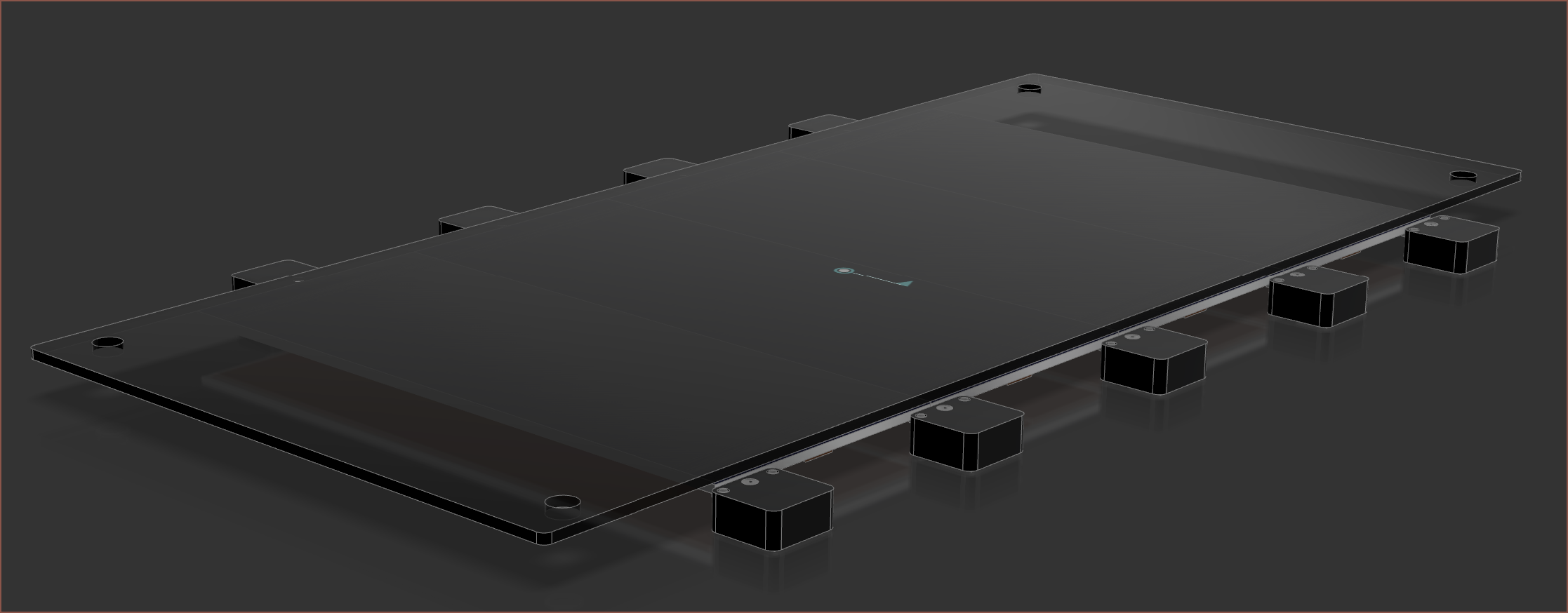
The past two days, I've been thinking about possible ways to automate the bed levelling process. This was because different features require different beds, meaning that they will be swaped out more than usual, as well as the W axis (rotary bed) would likely need a good amount of precision to reduce failed prints. I also wanted to see if I could further open up my bed size options to 3x2.
Thus, I started researching motorized 3D printer bed solutions. After remembering that I have a limited amount of wires on the slip ring used for the rotary bed, and noting that I have no inherent need for the ability to have something like a 3x2 segment bed layout, I rejected the idea and the specification change.
However, I still believe that automatic calibration is an important feature to strive towards. It looks like 5 axis CNCs take a non-negligible amount of time to calibrate:
Add this to the multiple bed segments that need to be adjusted, and tool offset calibrations, and there would be quite a bit of overhead time just to get a print started.
Computer vision can be used to calibrate the tool offset for X+Y, as well as Z. I was also thinking of using computer vision to see the top of the bed leveller and use an "allen key and dial indicator" tool head to mechanically adjust the level.
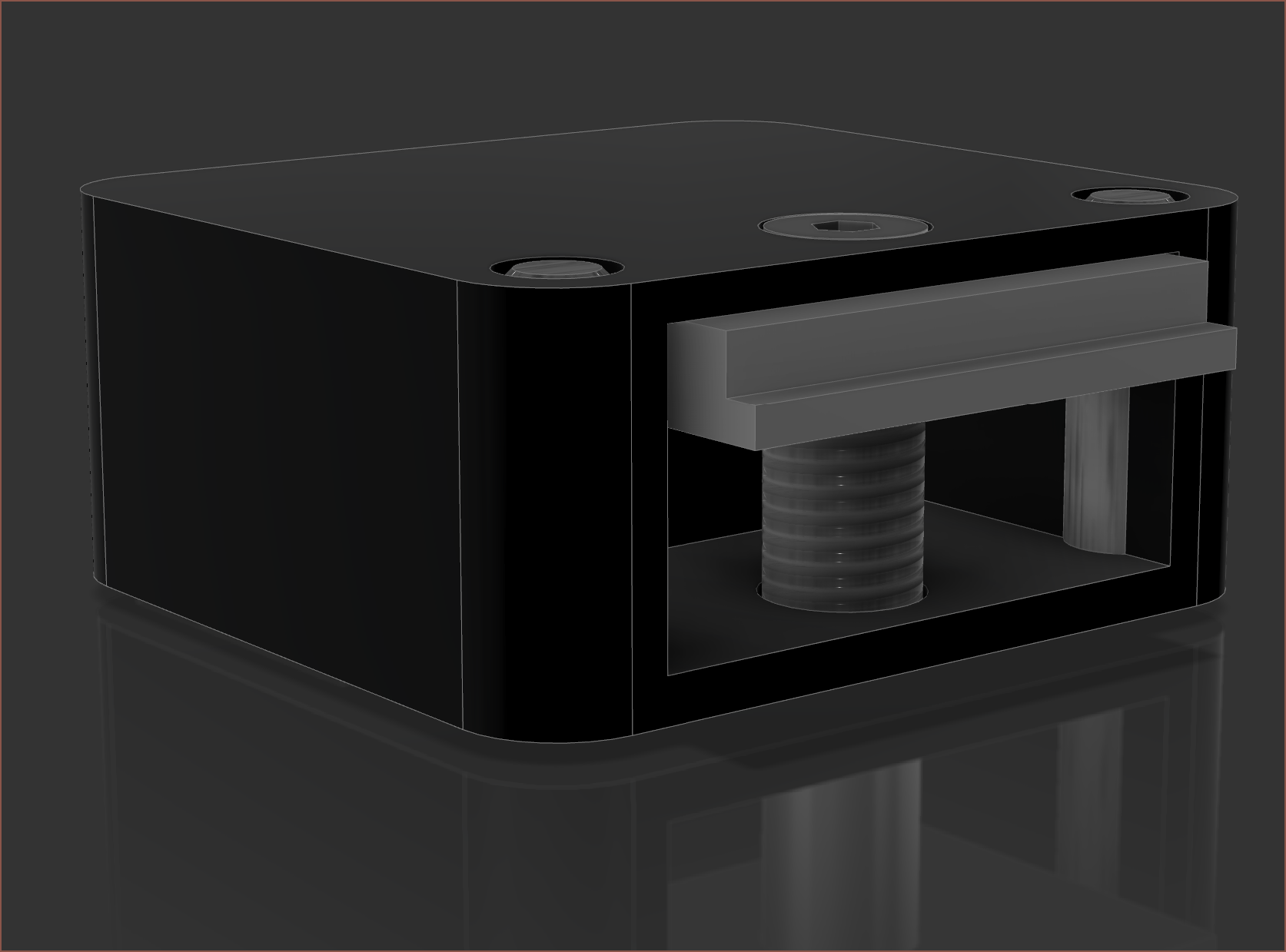
Discussions
Become a Hackaday.io Member
Create an account to leave a comment. Already have an account? Log In.