Vishnu, Trevor and I are working to reduce refrigeration energy use in breweries and cideries. Trevor owns Goat Rock Cider, our test location.
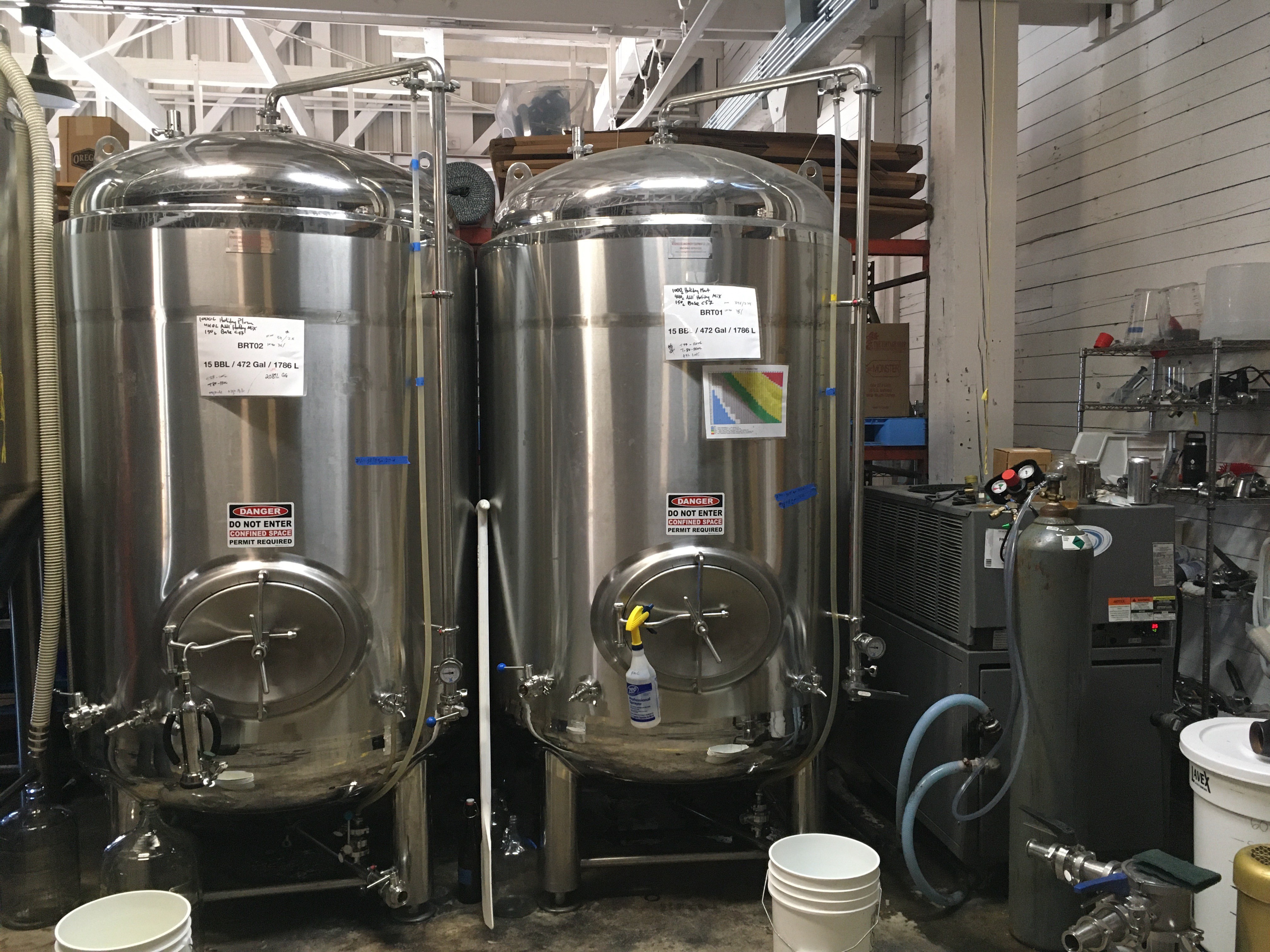
Above, two out of five fermentation tanks and a glycol chiller on the right, behind the gas cylinder.
Many breweries/cideries have a system design where an air-water chiller cools a propylene glycol and water mixture and continuously circulates it in a loop. Each tank has a temperature controller that opens a valve to allow that cold glycol to flow through a metal jacket on the tank, as needed, to lower that tank’s temperature for fermentation (~60sF/15-20C) or storage (~35-45F/2-7C). The cold glycol has a 28F/-2C setpoint.
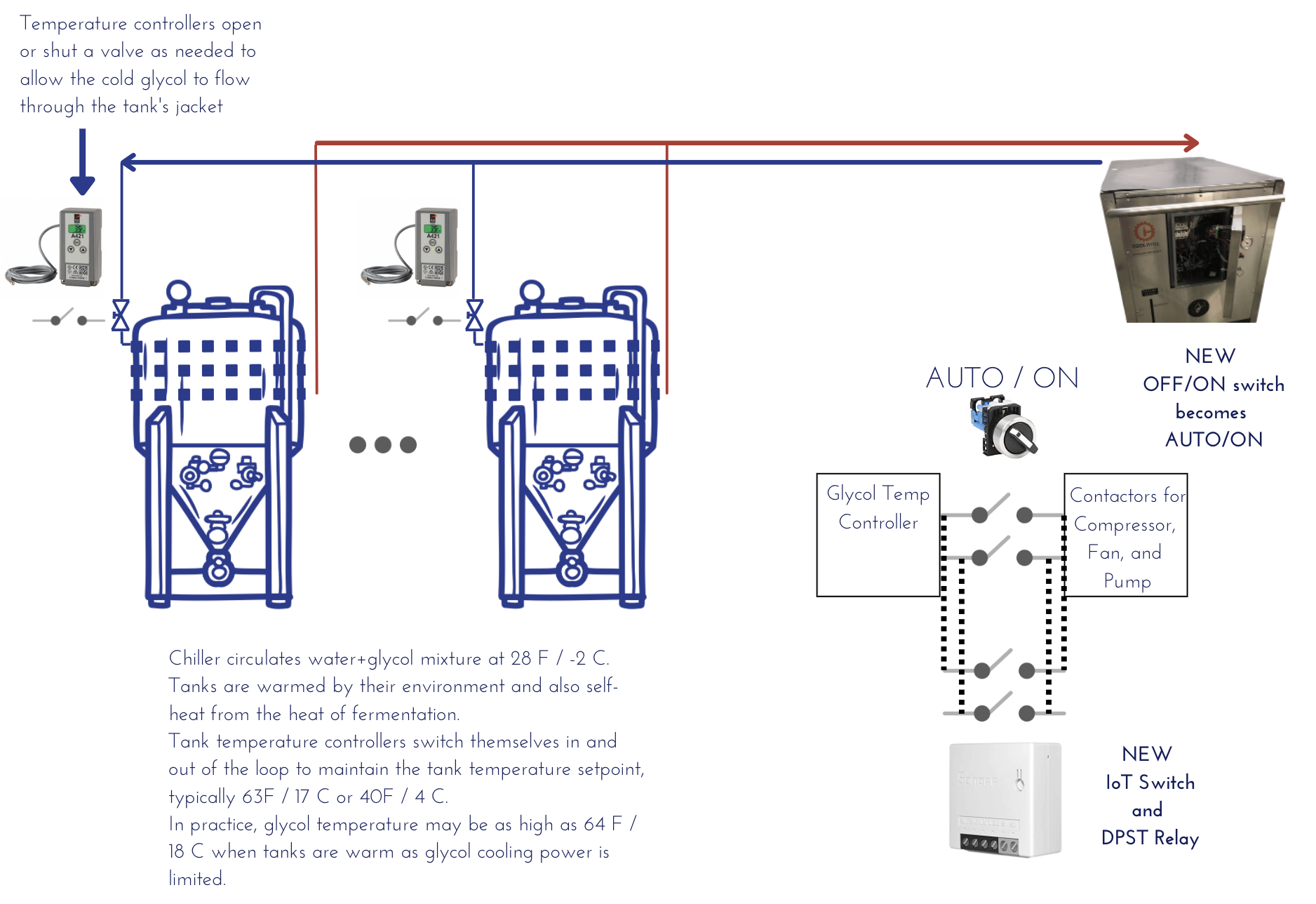
Above, we have added a simple IoT switch and DPST relay to control the chiller in parallel with its existing DPST on/off switch. They allow the chiller to be scheduled to turn off during times of peak electricity demand. This also means that the chiller wastes less pumping energy.
We can shut the chiller off for a period of time each day because the thermal mass of these tanks of cider (5-45 barrels, 155-1500 gallons, 600-5000L) is such that it takes several hours for the tank to change temperature within the typical hysteresis or deadband of the temperature controller. For example, the valve allowing cold glycol to a tank will open when the tank has warmed to 64F/18C, and will close several hours later once the tank has been cooled by the circulating glycol to 61F/16C. Then the tank of beer will spend several hours warming again to 64F/18C, because of the heat generated by the fermentation itself.
We can shut the chiller of for several hours each day and the tanks will not see a temperature change any larger than they already experience due to the hysteresis in their temperature controllers.
Other than simply using scheduling, we plan to experiment with other chiller control strategies to see what will lead to the most energy savings. We hope to use tank temperature, valve position, chiller electrical demand, tank cooling power, solar energy availability, and chiller inlet and return temperatures as data sources for control.
Our goal for this project is to enable further energy savings at other craft cideries and breweries, where refrigeration on average is 35% of electricity use. At our test cidery we have modified a 3 ton / 10kW chiller. Other craft breweries have chillers up to 20 ton / 70 kW.
We can also see this control strategy applied to any space or object that contains thermal mass, such as HVAC systems in buildings. Internet of things (IoT) technology allows for these control strategies to be implemented at low cost.
Pros
- IoT control allows for easy scheduling of the chiller
- Local IoT device remembers the schedule, so no dependence on the internet/cloud for scheduling operations
- IoT App (eWeLink) has LAN mode for local / non-cloud control of devices
Cons
- Off-site operation of the chiller depends on the cloud / internet for operation
- You have to make sure it is safe that the chiller can be turned on at any time by someone with remote access.
Licenses
This is an open source software and hardware project. The software and hardware design files and documentation are available under GPLv3 license.
The third-party IotaWatt based energy monitoring hardware "extraAC" is open source, and GPLv3 licensed.
The third-party IoT wifi switch and temperature controller hardware components of this project (Sonoff) are used with their stock closed-source firmware and third party cloud software. Open source firmware is available for the Sonoff hardware (Tasmota).
Github
Documentation on adding IoT control to the chiller: https://github.com/Hudson-Sonoma/glycol-chiller-control-docs
extraAC Temperature and Electrical Power Monitor: https://github.com/Hudson-Sonoma/extraAC
extraAC is a fork of the excellent IotaWatt open source electrical energy monitoring system: https://github.com/boblemaire/IoTaWatt
References
Energy Usage, GHG Reduction, Efficiency and Load Management Manual, Brewers Association
Energy Efficiency Improvement and Cost Saving Opportunities for Breweries, Lawrence Berkeley National Lab LBNL-50934