In the last few days, I did some cutting tests using a 1.6mm electrode from a TIG welder.
Here is the design that I used so far:
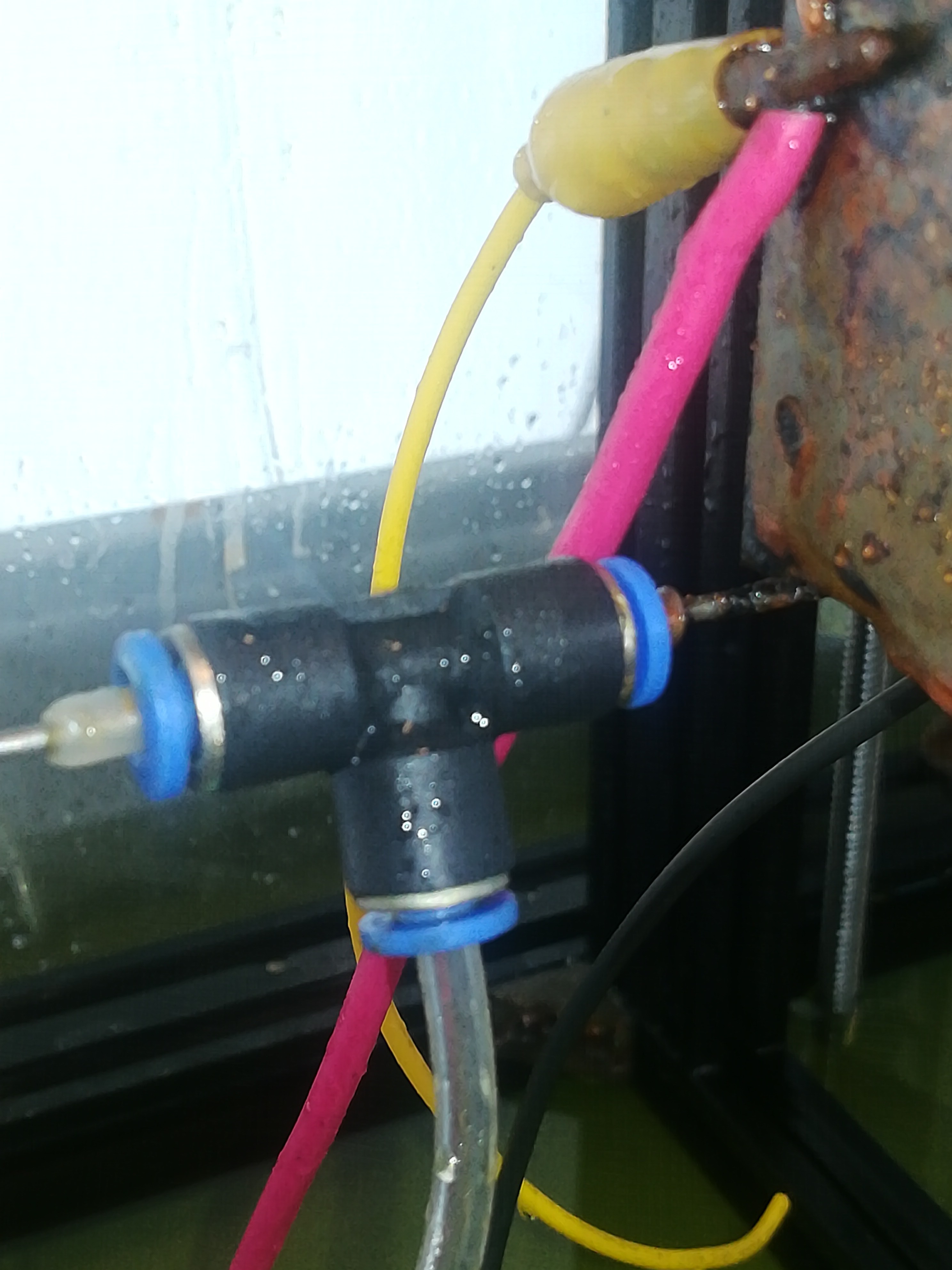
1.6mm tungsten electrode with 4mm T fitting, a piece 4mm tube at the back, and a 4mm brass tube at the front.
On the Wikipedia Page about ECM, they write that the removal rate in mm/minute is proportional to the amps per square mm - So for fast machining I would need a high amps per square mm value.
I tried out different things and noticed that there are some challenges to overcome:
First, it seems like machining takes place wherever the stream of water hits the workpiece (around the electrode). The closer to the electrode, the more material is removed.
I also noticed that if the stream diameter gets larger, the conducting surface gets also larger and with it, the cutting path diameter increases and the resistance decreases - like if you use a cable with a larger diameter.
If everything would stay the same during cutting this would not be a problem like you set your stream diameter and it always stays the same so that you always get the same cutting path size.
The problem with that is that after some time, dirt from cutting builds up on the electrode, which alters the steam and while doing so leads to a changing cutting path size and also slower machining because with a larger water stream the machine is removing more material. It also messes with the distance keeping because if the distance threshold was set to eg. 3.15A in the beginning, with a larger stream diameter and reduced resistance, the machine reaches a reading of 3.15A at a position further away from the workpiece than intended.
So this is a problem that needs to be solved.
Here you can see a picture of the stream before and after cleaning off the cutting dirt from the electrode. You can also see the cutting path that increased its diameter over time because of the dirt.
I think I will first try to find a way to prevent dirt from building up on the electrode to get a consistent cutting path quality and after that, I will focus my work on getting higher amps per square mm / cutting speed.
Discussions
Become a Hackaday.io Member
Create an account to leave a comment. Already have an account? Log In.