To rotate a bipolar stepper motor, pulses are applied in sequence to the windings, the sequence of these pulses, are applied externally with an electronic controller. Said controllers are designed in such a way that the motor can be kept in a fixed position and also so that it can be rotated in both directions.
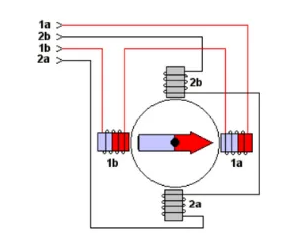
There are three characteristics that are common in stepper motors:
- Voltage: Stepper motors have a working electrical voltage. This value is printed on its case or is at least specified on its datasheet.
- Electric resistance: This resistance will determine the current that the motor will consume and its value affects the torque curve of the motor and its maximum operating speed.
- Degrees per step: This factor defines the number of degrees the axis will rotate for each full step.
Here is a quick guide for Stepper Motor Wire Color And Coil Pairs.
However, color codes are not always respected by manufacturers. So a test allowed me to find that my stepper motor works at 5 volts. I also found by means of an ohmmeter the two coils and the order of the pins as follows:
- pin 1 - gray
- pin 2 - yellow
- pin 3 - brown
- pin 4 - red
These motors have several windings that, to produce the advance of a step, must be fed in a suitable sequence. By reversing the order of this sequence, the motor turns in the opposite direction. The next table shows the sequence to generate the CW (Clockwise) and CCW (Counterclockwise) movements of a bipolar motor.
Discussions
Become a Hackaday.io Member
Create an account to leave a comment. Already have an account? Log In.