The idea is conceptually simple. A runout sensor is just a lever switch pressed on filament in a constrained path. When the filament runs out, it makes noise or turns off the printer. The problem is mounting the runout sensor where it doesn't interfere with the filament.
They're usually mounted on a bowden extruder because the bowden doesn't move. The problem is mounting them on a direct extruder. If it's mounted on the extruder, it's heavy & reduces the vertical clearance. The 1st attempt around this was an arm which moved in 2 dimensions but not up & down. It could follow the extruder horizontally but not vertically.

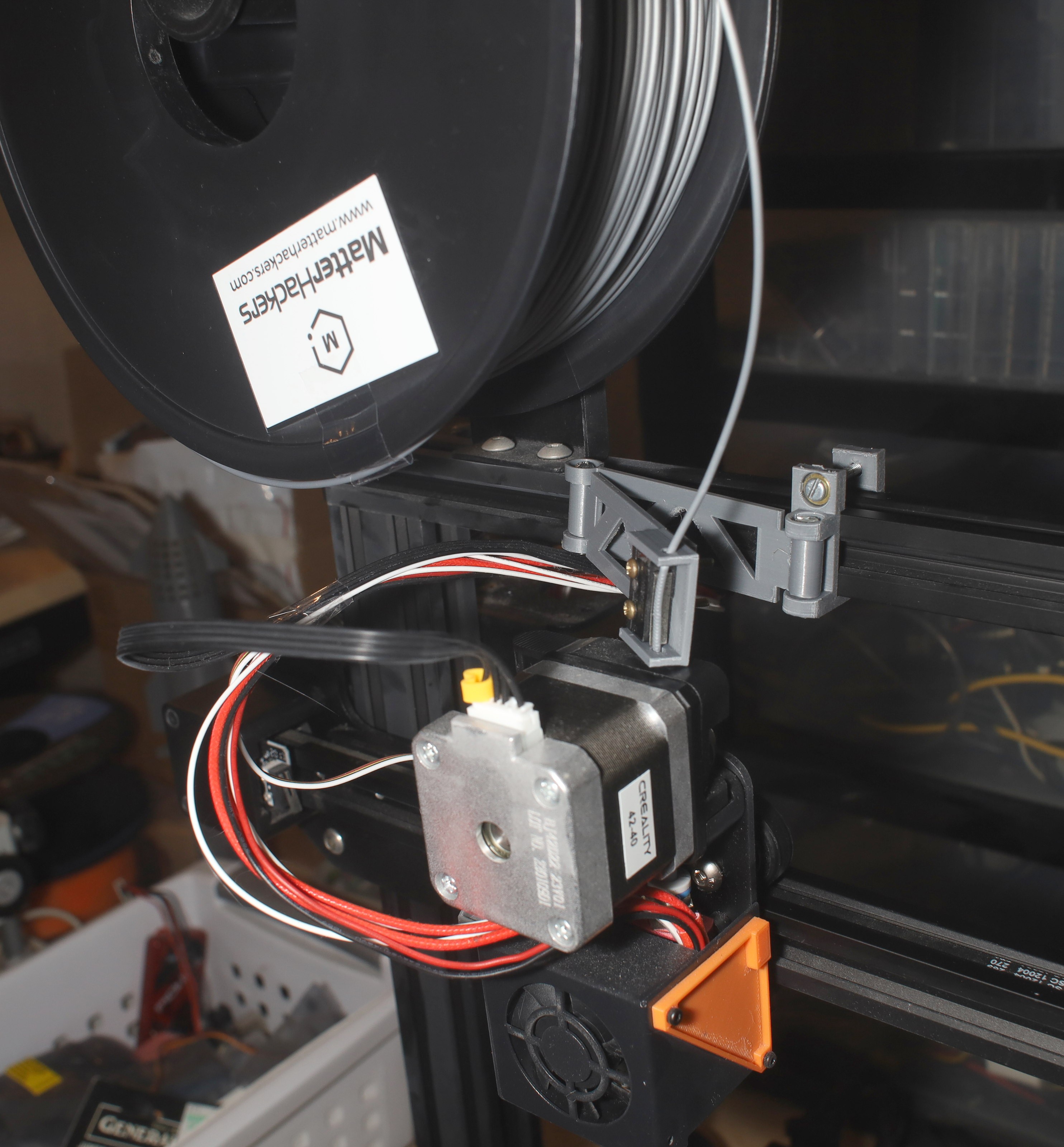
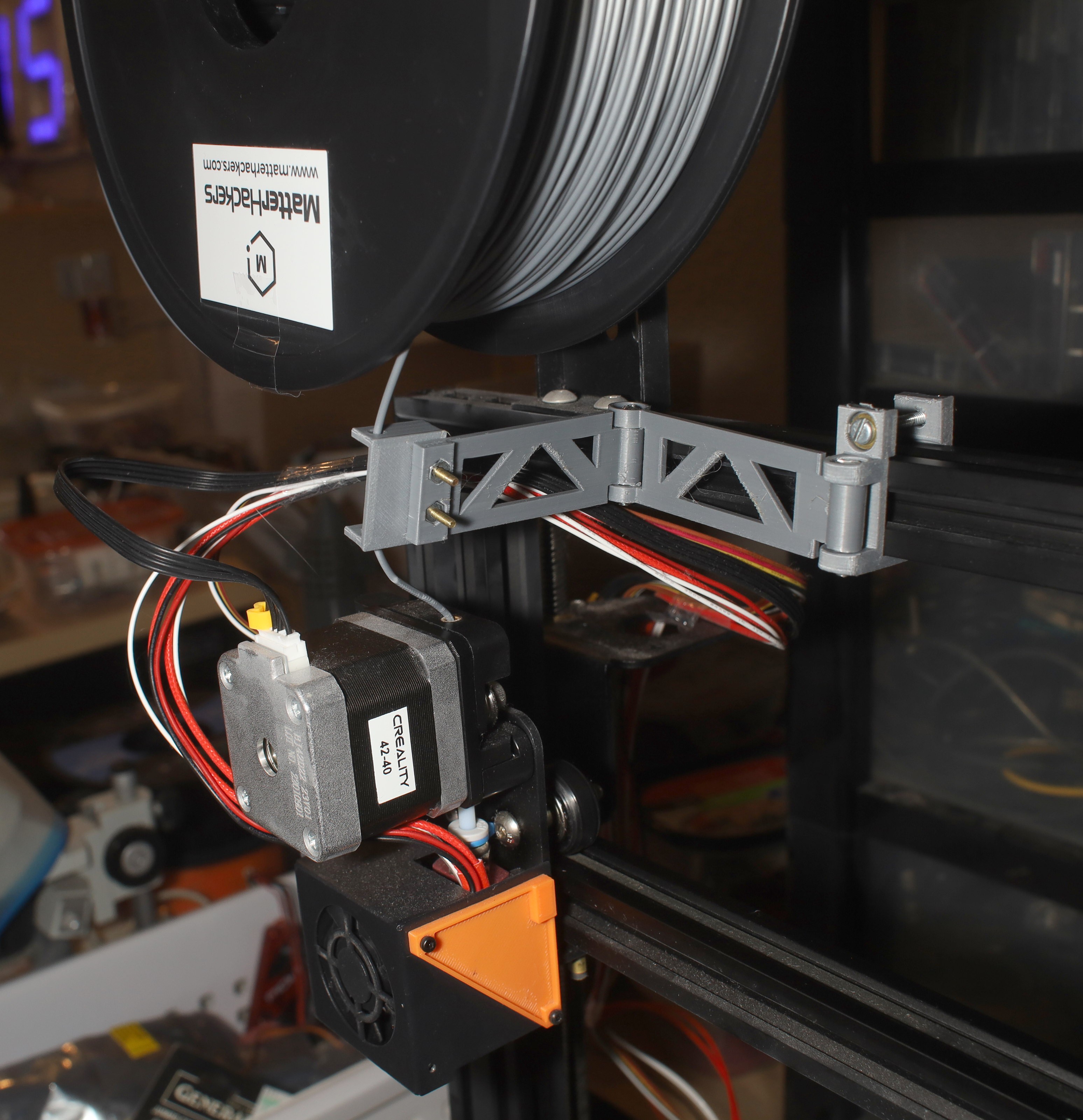
When the nozzle got high enough, there were gimbal locks & bending filament. Some requirements are for the filament to not bend & the print area to be at least 220mm high.
Because of the variety of nozzle positions, the sensor would have to not only move horizontally but rotate. It almost requires a robot. It became clear that the conventional lever switch wouldn't do for a direct extruder.
Discussions
Become a Hackaday.io Member
Create an account to leave a comment. Already have an account? Log In.