The control unit is the brain of the OpenCTD. It's also the most vulnerable part. For the last two years, we've had volunteer naturalists deploy prototype OpenCTD during whale watching expeditions in order to help us streamline the end-user experience, provide feedback on the design, and find increasingly more creative ways to break the CTD.
From that, we've evolved from a DIY control unit built into a small protoboard to a custom PCB, protected in a 3D printed shell that isolates the battery, keeps small leaks away from the precious electronics, and makes the entire system a little bit easier access.

The DIY control board, on the right, compared to the custom PCB control board, left.
But this presents a new problem. One of our missions is to minimize the number of custom parts in order to make the build as accessible to as many people as possible. The end result is that we now maintain two build pathways, one using a custom board, which is cheaper, faster, easier, and more reliable, and one using the old protoboard, which is available if you can't get a custom PCB.
Although, to be fair, at this point if you want to build an OpenCTD and provide feedback, I'll just mail you a board.
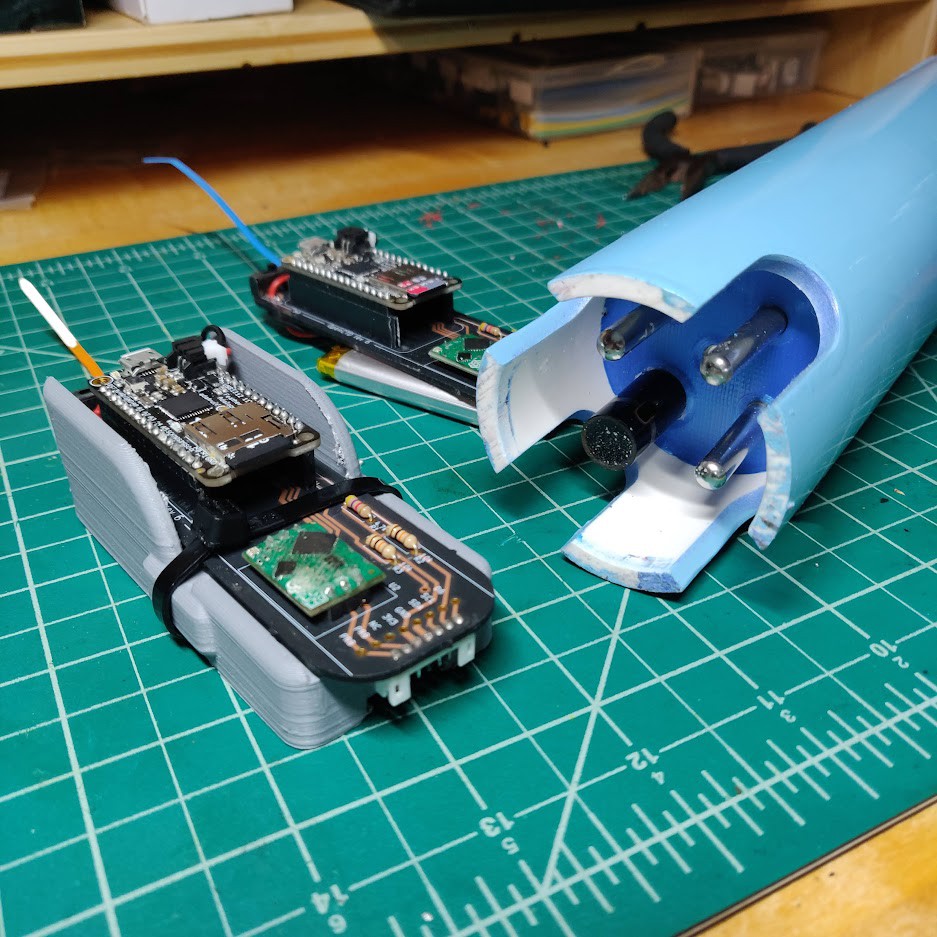
The control unit in a 3D printed enclosure.
Discussions
Become a Hackaday.io Member
Create an account to leave a comment. Already have an account? Log In.