To allow quadrature encoders & all the extra signals on each motor, the new nozzle has a dedicated control board for each motor, with a single wire UART stringing them together. 2 boards are dumb motor drivers which read H bridge bits & write hall effect sensor values. 1 board is the brain board. All 3 share a single UART wire.
A quick mockup showed a new board with the DRV8833 & the ATmega328 side by side would take more space than the DRV8833 breakout stacked under the Atmega328. Without stacking, they wouldn't even fit on the nozzle. The stack would fit neatly under the motor. The breakout board also does a better job connecting the ground pad of the DRV8833 than a home made board can do.
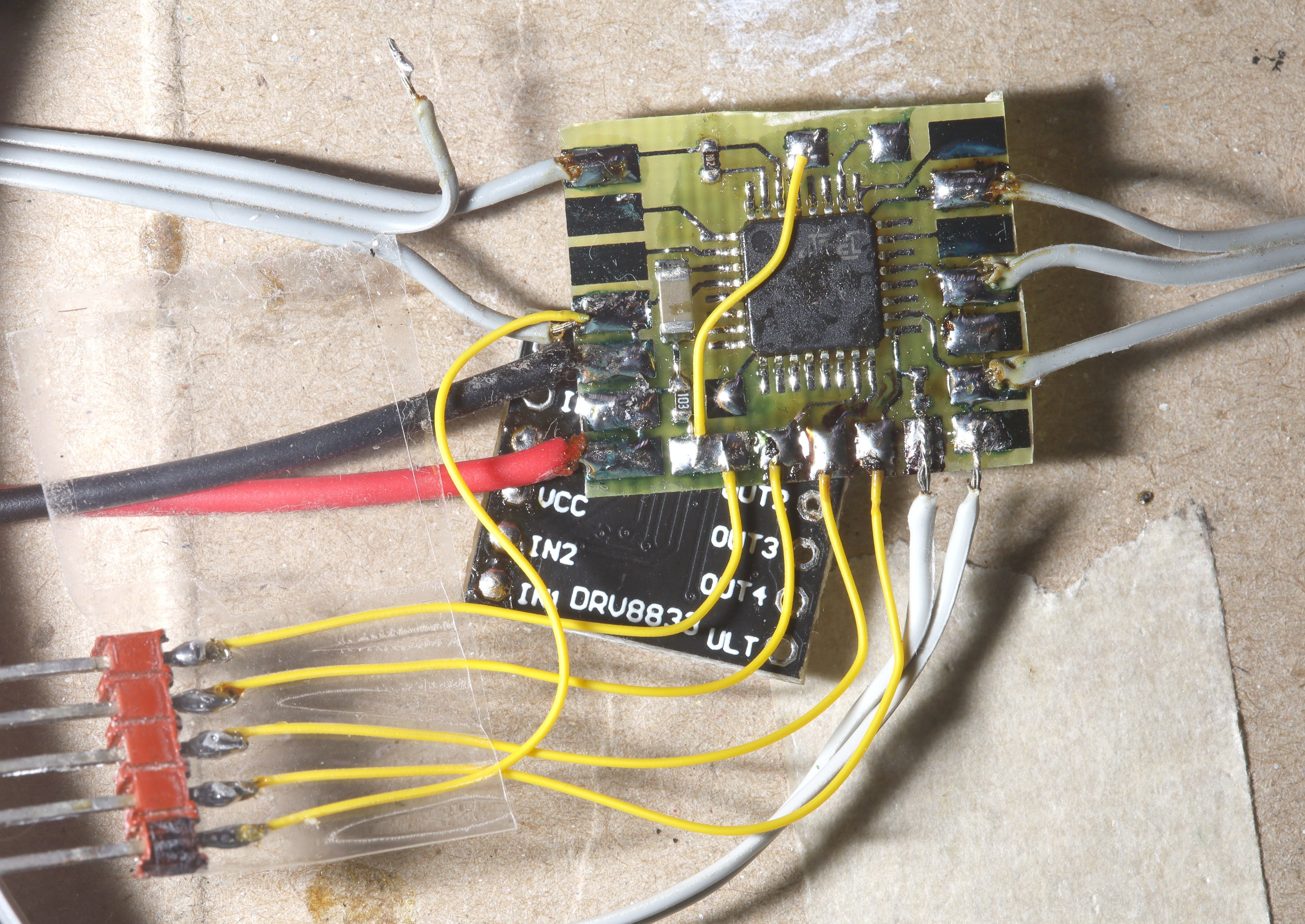
Testing showed the IR parsing could work in its internal 8Mhz oscillator by assuming all the IR codes are the same length. Who knew 5 years after the lion kingdom's 1st IR parser, there were still optimizations to be had.
There is a definite lean towards a bootloader to reduce the wiring. It would entail custom hardware to drive the single wire UART & indirecting the interrupt handlers does not appeal.
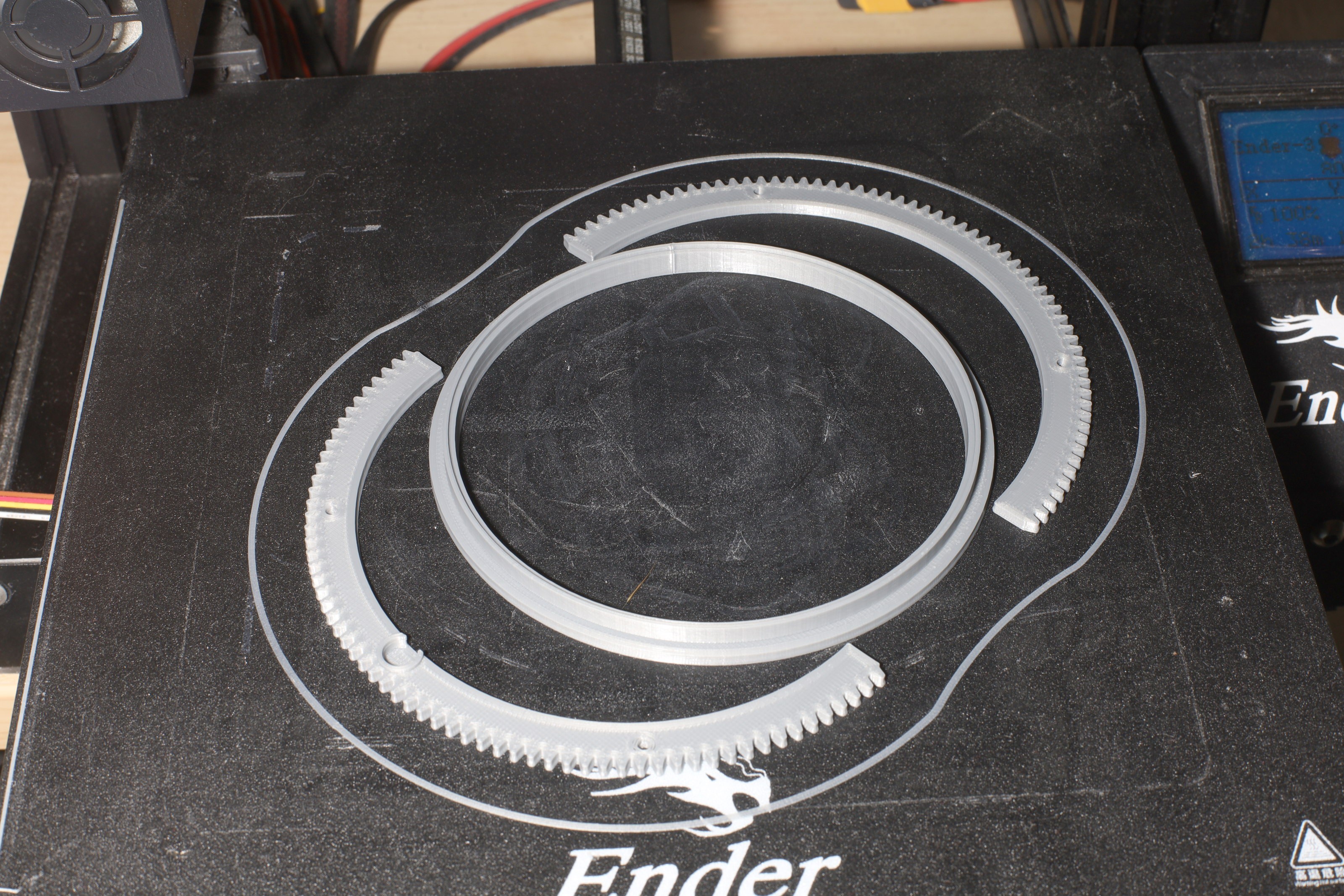
2 years later, an old friend returned. The mane bearing was the 1st 3D printed part a lion ever modeled. It received several upgrades. It kept the 2-56 farsteners since self tappers didn't seem strong enough.
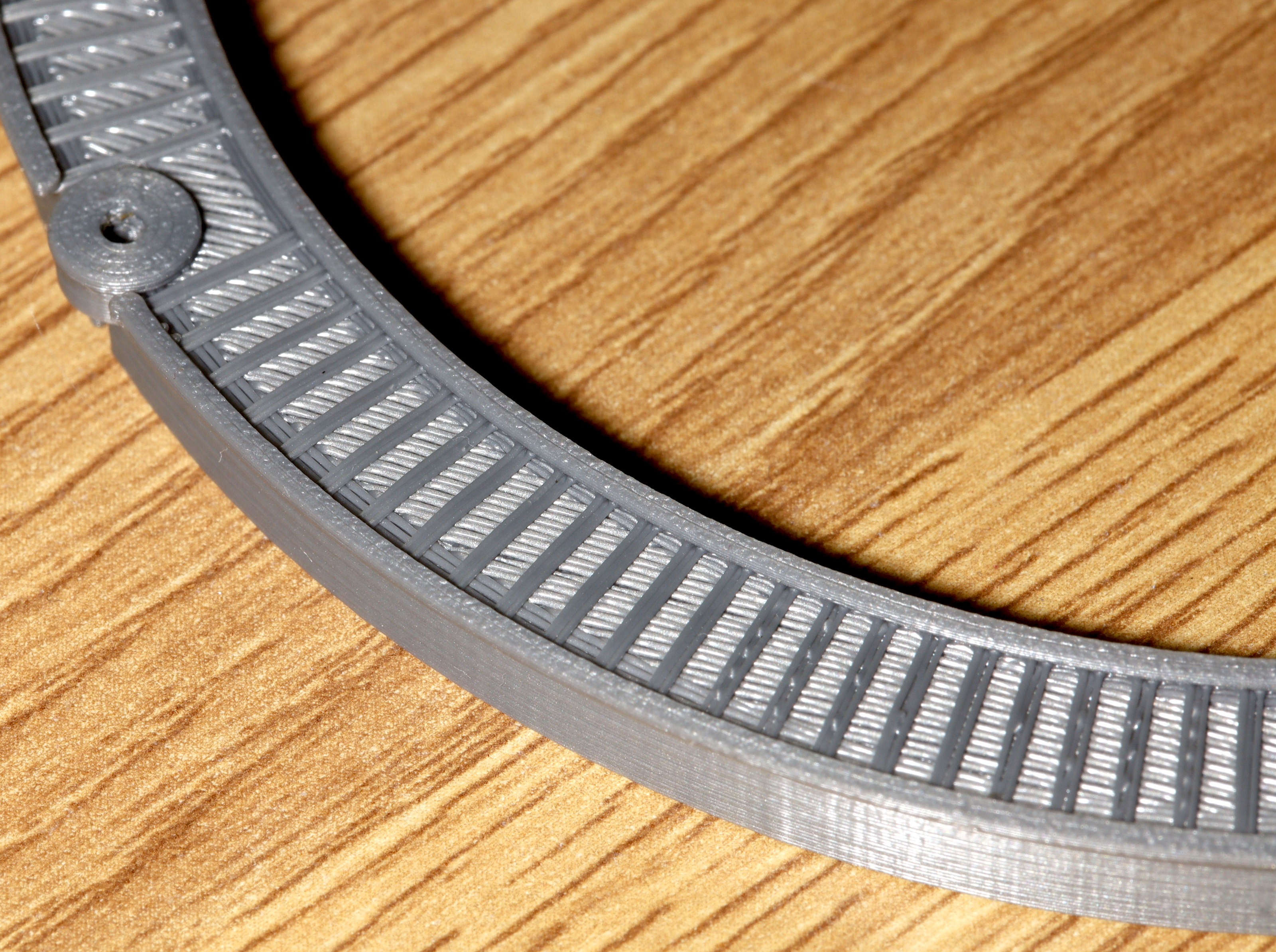
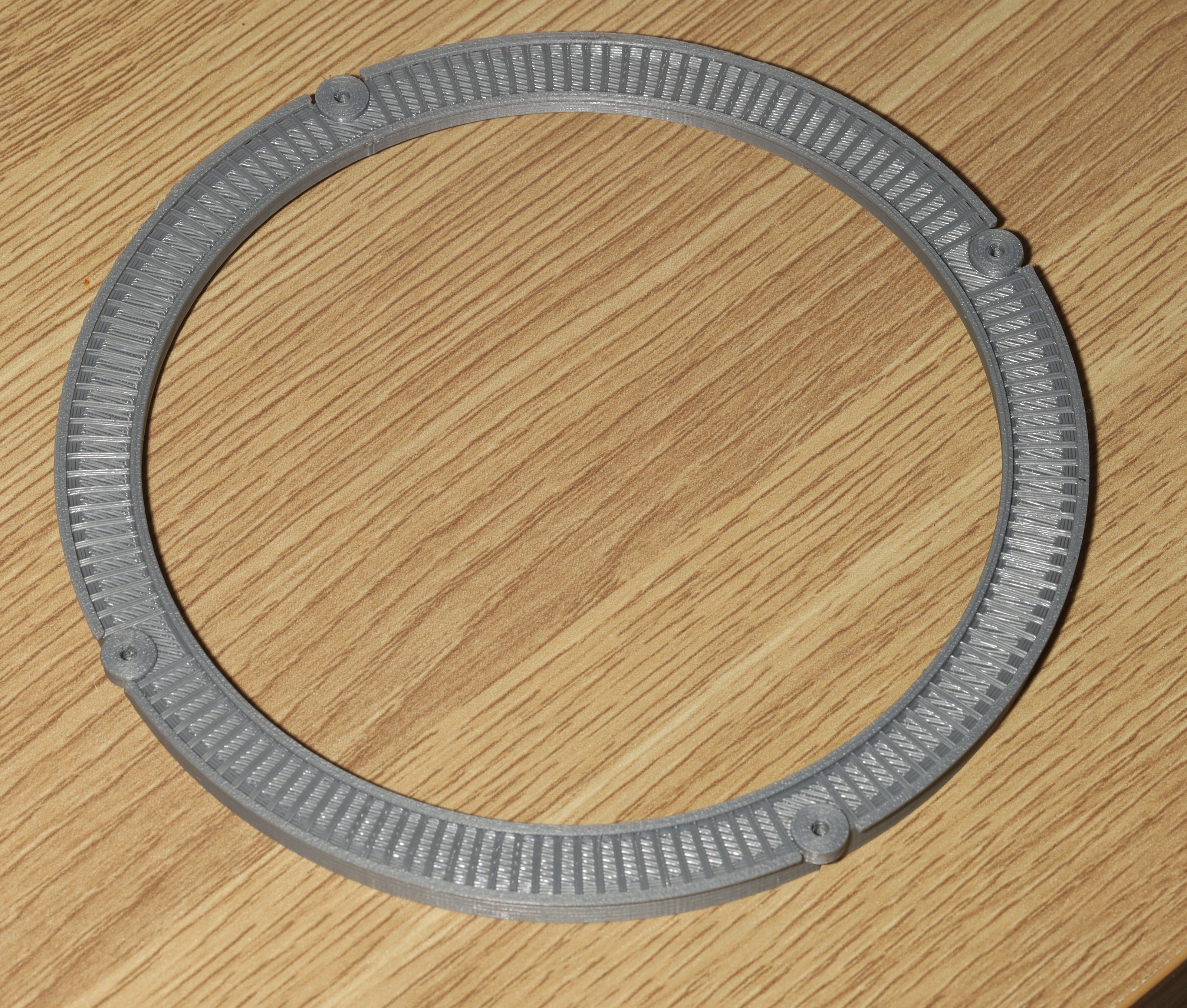
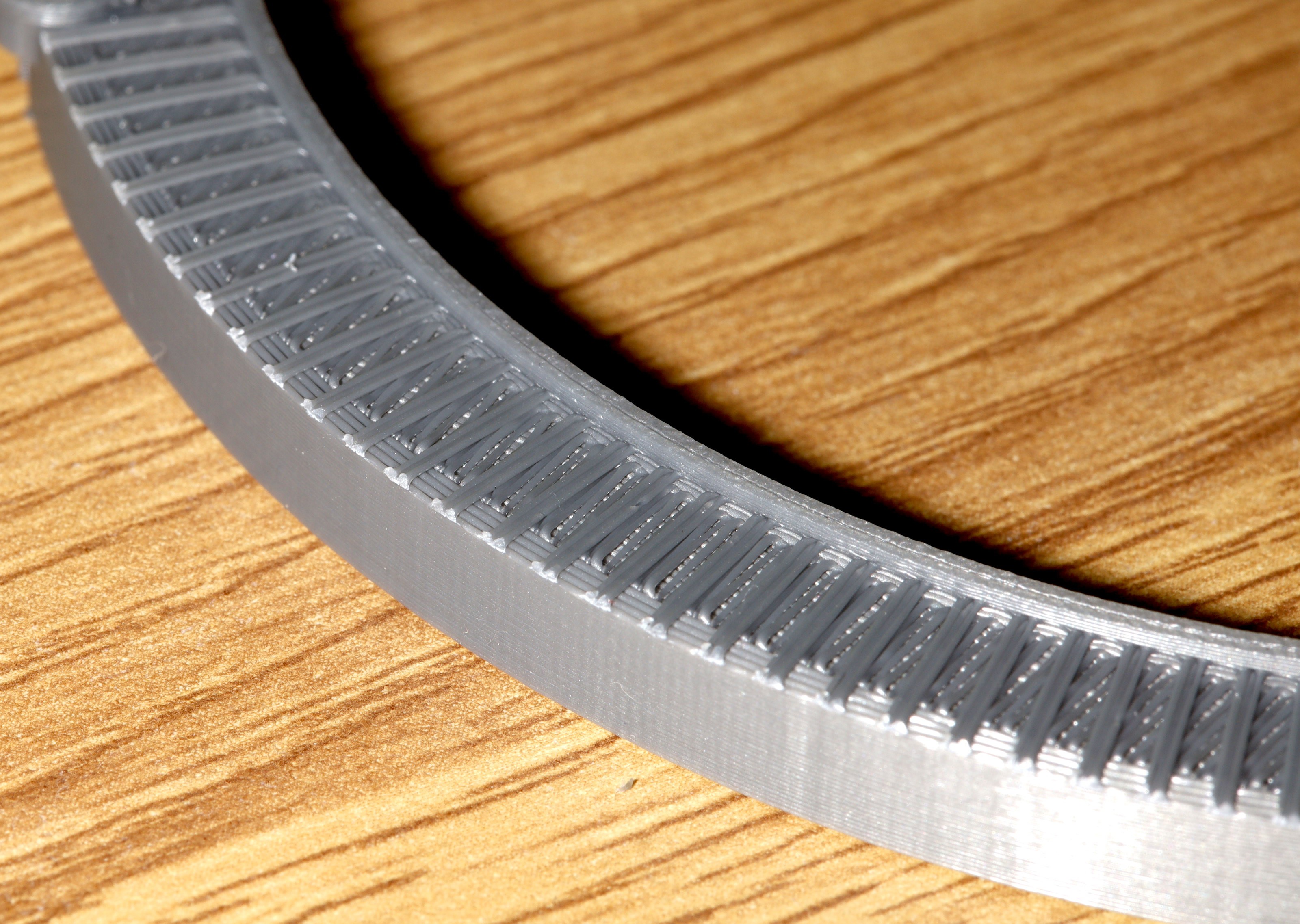
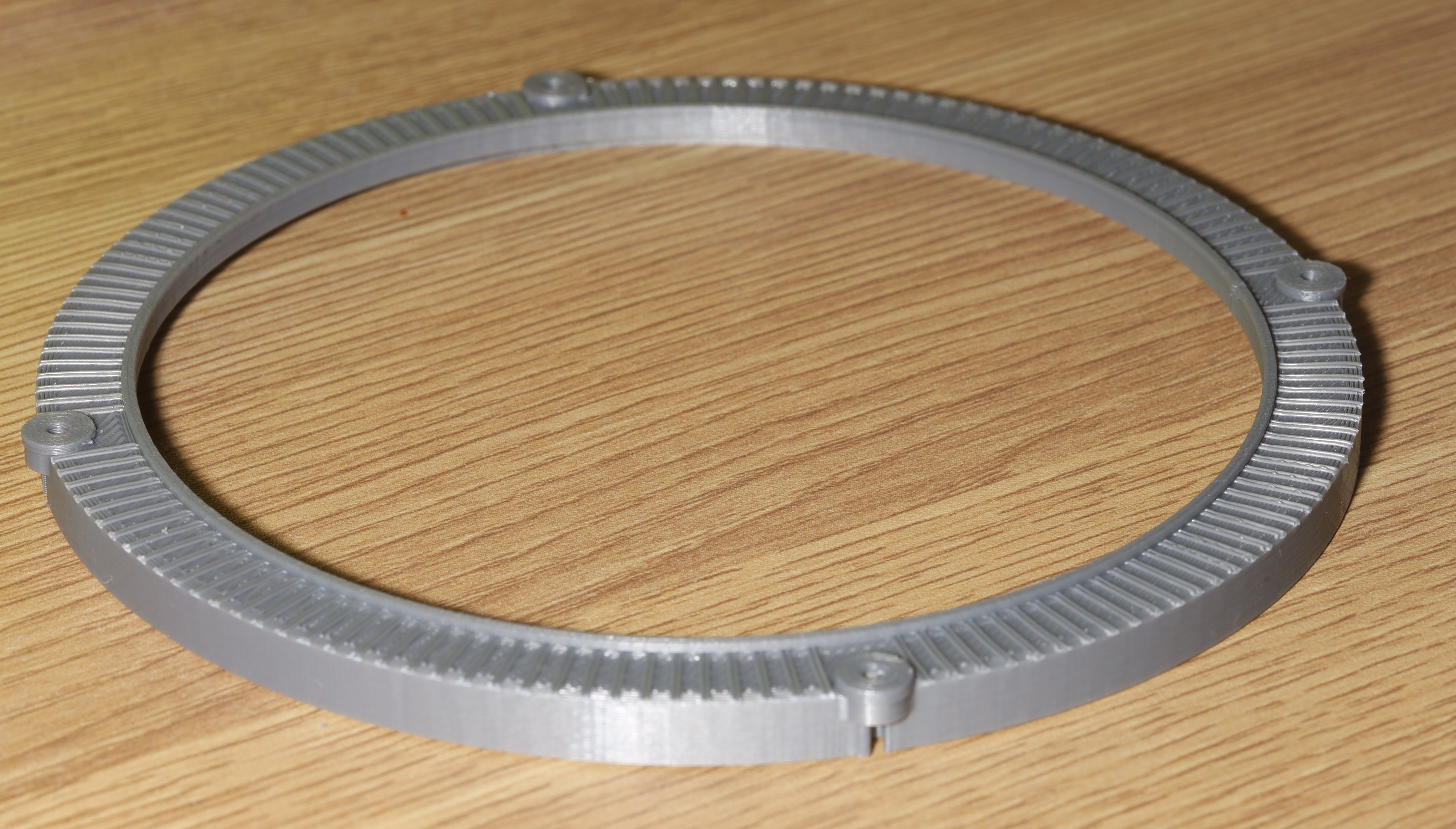
The difficult overhang got a modern modeled support.
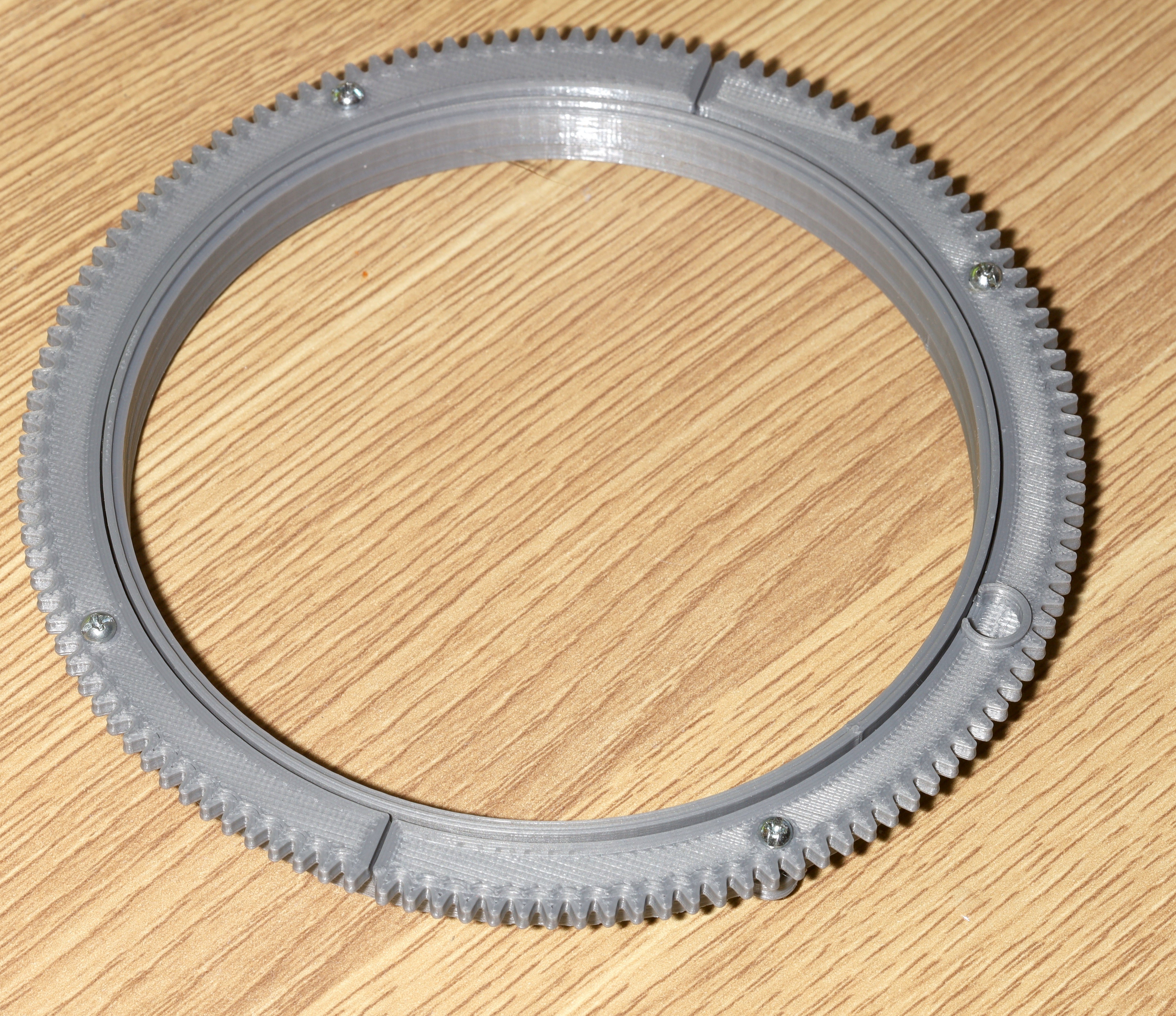
This one rotated a lot more freely than 2 years ago.
Discussions
Become a Hackaday.io Member
Create an account to leave a comment. Already have an account? Log In.