How not to make a spot welder pen
My first attempt at making a spot welder pen has failed.
I bent the electrode ends of my existing spot welder pen inwards, then smashed them flat with a hammer and flat-end punch until they were about the thickness of the connector leads (about 0.02") as shown:
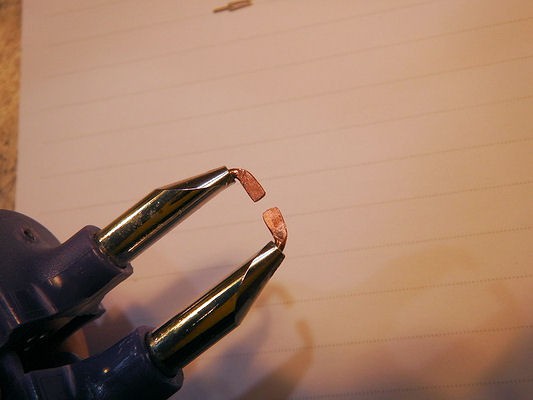
For side shields, I cut 2 nibbles from 0.03" PCB material and removed the copper plating, to make the shields even thinner.
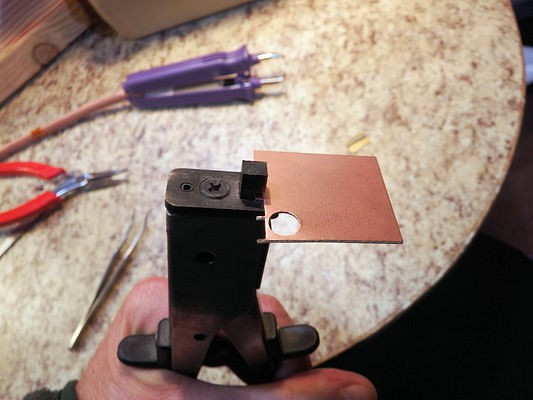
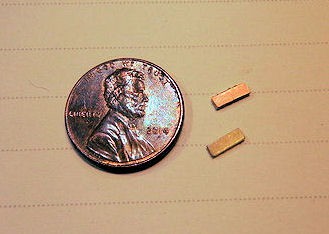
Next, I glued the shields to one of the flattened electrodes using some JB weld:
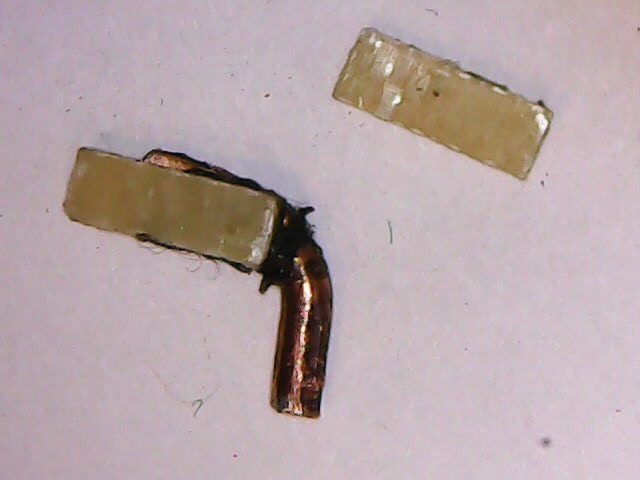
The intent was to form a channel surrounding one of the electrodes that would corral the wire and connector lead and keep them from sliding off of the electrode, then the other electrode would slide into the top of the channel, pinning the wire and connector lead between the two electrodes.
This doesn't work.
Smashing the ends of the electrodes was the wrong process. The flattened ends are not accurately the right thickness, and the sides are not parallel so that the side shields angle in towards each other.
It seems like the corral idea should work if the electrode surfaces are the right thickness and parallel.
The bigger issue was in the pen itself. The cheap Chinese spot welder pen was not made for pinching things together, the end hinge failed (for that purpose), and holding the sides of the pen together is too clumsy.
The solution might be to build a bespoke pen with a captured hinge.
Discussions
Become a Hackaday.io Member
Create an account to leave a comment. Already have an account? Log In.