Tuesday, 18/06/2024, 19:06
Well, I’m writing this in a google docs first and then later posting on hackaday.io because it is having a lot of trouble staying up.
Power Source:
So I will write what is in my mind right now:
So, I’m kinda pissed off because it seems like the molten carbonate fuel cells and molten hydroxide fuel cells kinda fricking suck and are equally dangerous. Plus, I don’t really need lithium carbonate in a lot of quantities because it is more of a catalyser for the carbonate solution. Most of the articles that I could find on the subject said that they used a nickel anode and a cathode with a layer of lithium while only using potassium carbonate and sodium carbonate.
On top of that, one of the recurring problems is that the molten carbonate fuel cell also needs the CO2 from the exhaust of its own reaction to be mixed back for whatever reason. And it also can suffer from layer separation, since the carbonates have different densities (akin to what happens to water and oil).
And well, I also revisited the idea of using magnetohydrodynamic generators, but I’m really not confident on its resulting performance and on its viability while building it homemade.
The idea is simple:
- First, using the plasma jet engine to power a tip-jet rotor.
- The tip-jet rotor will rotate an axial compressor.
- The air from the air compressor will go to a plasma jet rocket engine.
- On top of the plasma, a fuel (gaseous, liquid or powder) will be introduced, increasing the performance of the plasma jet rocket engine.
- On the combustion chamber and nozzle there will be a Magnetohydrodynamic generator coil that will turn the flow of air and combustion into electricity.
- The electricity will be used to maintain the reaction going just like in a conventional jet engine and the excess used to power the other systems.
- This will be an Air-Breathing Plasma Jet Magnetohydrodynamic Rocket Engine Generator (ABPJMREG).
- The plasmatron turns hydrocarbons into hydrogen and CO/CO2, so MAYBE the plasma can end up doing something similar on either making more complex reactions and/or more toxic byproducts.
- Another problem is the amount of noise, heat, vibration, fumes etc.
Obviously there will be a LOT of variables and a LOT of thought on the type of material required to make this beast to work continuously, and on top of that, dealing with this kind of machine can easily cause my own death.

And although ChatGPT (that f*cking stupid chat bot) keeps saying the efficiency of the MHD systems is “90%” the own sources it shows to me prove otherwise, this article (which gpt itself sent to me as the said source) said the magnetohydrodynamic generator on the rocket engine achieved a maximum of:
“There are energy losses in the MHD channel. These include friction with the wall, heat transfer, electrical resistance of the gas, and electrical losses at the ends of the channel and the conductor walls (17:331). These losses give linear MHD channels using gases at 2000-3000K only a 15% efficiency (35:31).“
The pancake type is more efficient, but it is said to be 30% efficient. I don’t see the appeal of working my butt off on a glorified plasma furnace that will blow up in my face, melting years of work and thousands of moneys into a giant pile of molten slag.

Source: https://en.wikipedia.org/wiki/Magnetohydrodynamic_generator
This image is from a supposedly “optimized Stellarator fusion reactor”, only god can tell me if any fusion reactor structure would be practical/useful for MHD generators…
This article is about a nuclear enchanced MHD generator which uses molten metal, and it still only achieves maximum 30% alone. The metal it uses is Rubidium, but I could use Tin, Indium, Bismuth and Lead. And through that, I would increase the surface area in which the liquid moves, probably increasing the efficiency.
Actually, this gave me the idea of using a molten metal magnetohydrodynamic heat engine. The liquid metal would be heated by a furnace and move through some piping, turning the motion into electricity. I found this article about an open cycle coal powered MHD generator that is said to achieve 60% of efficiency, however, the thing was designed for 1.5 Megawatts (1,500,000 watts). Five times more power than the peak power designed for the mech. The magnet used in this was 5000 tons alone (dunno if it is a typo mistake or it is actually 5 million kilograms), so you can imagine how heavy this thing would’ve been.
It would be really fucking nice (and cool) if I could fit a MHD generator in my backpack and produce enough energy to power up a city, but unfortunately, reality isn’t that convenient.
The Molten Fuel Cells aren’t any better and the safer solution would be to use a conventional combustion engine generator.
And a conventional hydrogen fuel cell would be my first choice in ages, but there is absolutely no practical way of storing hydrogen gas in any shape or form. Even the best metal hydrides can only store 10% of its own weight in hydrogen, and assuming an efficiency of 50% in conversion to electricity, I would need 4,2kg of hydrogen per hour at 100hp. This would require 400kg of metal hydrides for 10 hours of activity.
What made me think of using molten fuel cells and magnetohydrodynamic generators in the first place is fuel cost and accessibility.
100 liters of fuel (whatever type) to make this mech going would be the cost of a minimum salary (or more), and the only fuels that are somewhat possible to make at home are Wood-Methane, Methanol and Ethanol. Unless I suddenly find a charcoal powered piston engine or a way of making “liquid charcoal”, I don’t think that the combustion engine will be a good option.
And yes, there are “charcoal” engines that were popular during the war, but in reality, those engines had a SynGas generator using wood or charcoal, which has half of the energy density of butane.
There is liquid coal or “coal to liquid” process in which coal is converted into diesel or gasoline using a huge fricking plant.
Lastly, the only combustion engine that I could find that uses charcoal without a chemical process or extra steps are turbine engines. And those aren’t as simple and cheap as making a piston engine.
I like all the ideas I presented, but when it comes to power-to-weight ratio, practicality, efficiency, cost, complexity and safety, all of them fall short.
Well, personal note: if it was this simple to make a portable power source, there wouldn’t be a concept such as “world energy crisis”.
And all of this fucking sucks.
However, before we delve into the next and last option, let me try to check the possibility of making the thermoelectric generators one last time.
The only reason that I got the will to try to design a TEG with around 30% to 40% is because I didn’t care enough to understand how it works at the first time because it used gold.
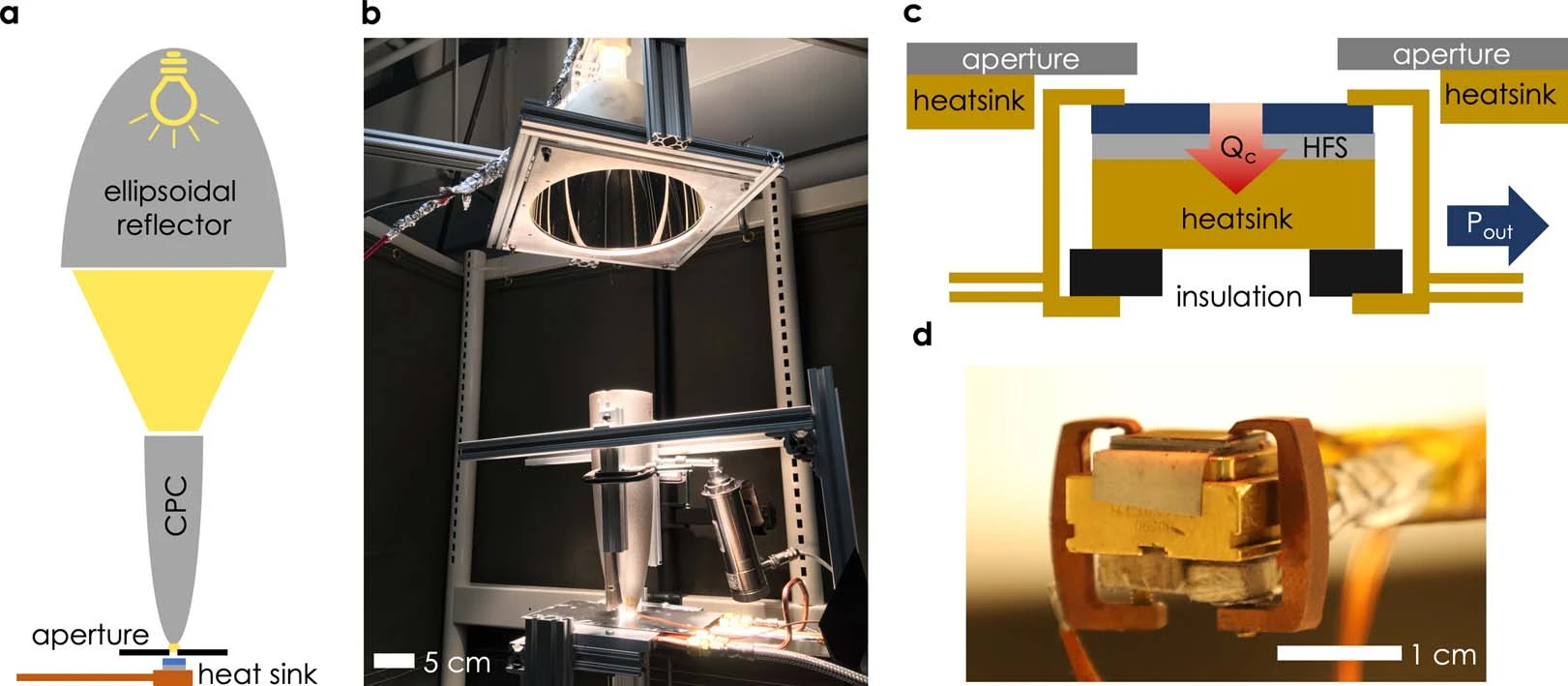
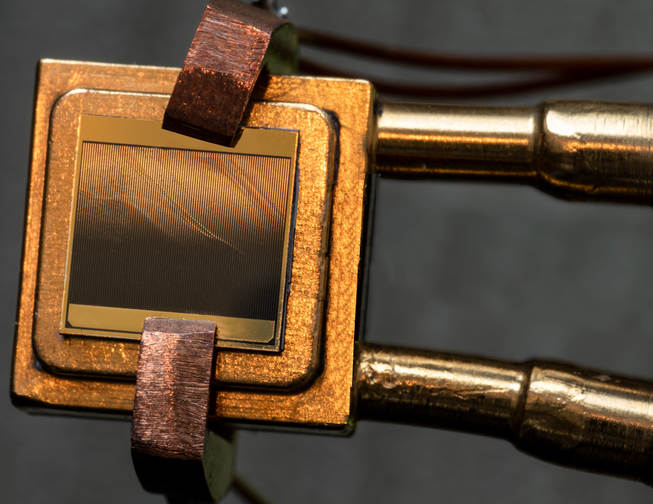
Source: https://www.nature.com/articles/s41586-022-04473-y
The gold is used because it is a great reflector of infrared light, that is why the hobbes telescope uses it. And the materials were tuned to both work as a thermoelectric device and as a photovoltaic device, a literal solar cell-TEG hybrid. That is why it uses germanium and GaAs (gallium arsenide) and other types of materials, they are meant to filter all other frequencies and only let infrared radiation pass through.
The article says that it achieved higher efficiency because of this filtering, but I want to understand why only allowing infrared to pass and not other bandwidths, I mean, the more sources the better, no?
Well, the idea for now is to do the following:
- Make a thermoelectric and thermophotovoltaic using cheaper materials.
- Make reflectors with cheaper materials
- Structure the TEG/TPV materials in a way that maximizes absorption of heat and radiation (there are a lot of papers on that).
- Add a magnetohydrodynamic generator and a plasma source to make it as hot as possible (3000 to 5000ºC). The MHD will stop the flames/plasma from destroying the materials.
- Use a blanket of air between the heat source and the actual contact with the TEG/TPV.
- Make a really long path for both MHD, TEG and TPV to absorb as much as possible.
- Add tin as a liquid metal coolant in the primary radiators.
- Connect the primary radiator to TEG/TPV and then connect to the secondary oil radiators (the oil/liquid could be conductive to allow MHD generation).
- Connect the secondary oil radiators with TEG/TPV to the tertiary air radiators.
- Vent the heat from the tertiary radiators into the air input, recycling heat into the system.
- Pass the already heated air through the exhaust heat exchanger to recycle even more heat.
- Introduce the heated air into the turbocharger into the combustion chamber and add a plasma source for the MHD generator.
- And maybe making everything in a circle, just like the stellarator.
I also need to find what would be the best size for the plasma flame, too big and it may not allow the TEG/TPV/MHD to fully absorb the energy, too little and numerous and the heat source may not be hot enough to make the system work.
And then make it 3D printable…
All of this is starting to sound more complicated than the charcoal engine, to be honest…
Well… I was expecting to find cheaper materials that have similar properties to the ones that the article has, like using aluminium and/or tin as the heat/infrared reflector (because mirrors can reflect infrared too), but… Well, the problem is that there really isn’t any other material that can reach the heights of the ones used in the TPV (thermophotvoltaic) with 40% of efficiency.
MAYBE by using a little more expensive materials like silicon carbide, boron based compounds, nitride related materials and sulfide materials (like Lead Sulfide), I could increase the efficiency from less than 5% to around 15% that is the normal efficiency of non-precious materials TEG/TPV cells using optimized surface area for better absorption (which I was able to find articles saying they reached even 23% efficiency only doing that).
Then, MAYBE by using the MHD would add another 15% of efficiency, with pseudo-photovoltaic cells (like DIY solar panels) and any other type of thermoelectric generation device, just MAYBE I could increase the efficiency to a maximum 30% or even 40%.
And I did find out that plasma is a type of “blackbody” that can absorb any kind of wavelength/frequency and emit it as thermal radiation, but it needs to be really opaque in order to work, unlike in a Tokamak which works in near vacuum. So, maybe an additional 2% of efficiency? lol
Taking into consideration all the nuisances that would come with a charcoal engine electric generator and the compound thermoelectric generator (this aberration I’m suggesting), I don’t really know which to choose.
- An experimental never tested thermal to electrical energy conversion/generation
- A well understood diesel converted to charcoal engine with a conventional electric generator.
Just now I discovered that there are other thermoelectric effects that can be used to generate power:
- Thermionic Converter:
A thermionic converter consists of a hot electrode which thermionically emits electrons over a potential energy barrier to a cooler electrode, producing a useful electric power output. Caesium vapor is used to optimize the electrode work functions and provide an ion supply (by surface ionization or electron impact ionization in a plasma) to neutralize the electron space charge.
Maybe this is a simpler example to understand, you don't necessarily need to make the gaseous media to be some weird exotic chemical or vacuum, just working on air/plasma can work.
It is said that Thermionic Converters have higher effiicencies (around 20%) than TEGs, but need higher temperatures and a medium of vacuum, rarefied conductive gases (like mercury) or plasma to work properly. - Pyroelectric generator:
Pyroelectricity is a property of certain crystals which are naturally electrically polarized and as a result contain large electric fields. Pyroelectricity can be described as the ability of certain materials to generate a temporary voltage when they are heated or cooled. The change in temperature modifies the positions of the atoms slightly within the crystal structure, so that the polarization of the material changes. This polarization change gives rise to a voltage across the crystal. If the temperature stays constant at its new value, the pyroelectric voltage gradually disappears due to leakage current. The leakage can be due to electrons moving through the crystal, ions moving through the air, or current leaking through a voltmeter attached across the crystal.
There was actually more designs and machines designed to convert heat to electricity, but the google results lead me to weird websites and videos. That is how I found out about the "blackbody" property of plasma, because it lead me to a scam/conspiracionist website of a guy that claimed making a 100% efficient way of converting infrared radiation into electricity by using plasma.
... Which would break the laws of thermodynamics... And the author/weird fans were convinced that the "scientist groups" were "persecuting" him because they did not accept his "free energy generator". :|
Anyway, the idea would be to add mutiple types of thermal to electric generators/converters in order to squeeze as much electricity as possible from the heat source.
... But I feel like this is just an stupid idea for some reason... My guts tell me that I can't simply add up the efficiency of different types of generators in order to absorb more power... Well... MAYBE stacking the copper/copper oxide photovoltaic cells with the thermoelectric generators would work, since you don't necessarily need the TEGs to be in direct contact with the heat source. So stacking them would actually work.
But I don't know about the pyroelectric and thermionic generators, not to mention that I don't know crap about a cheaper way of making thermophotovoltaic cells.
Also, I forgot to say, but I saw a few articles that had some charts about thermoelectric, magnetohydrodynamic and stirling engines that had really high efficiencies based on the temperature.
So all of these generators actually had effiicencies increasing from a single number to even 40% with higher temperatures.
Diesel Engine to Charcoal Engine:
Well, well, well, look at that, after 2 days looking at random crap spilled by google, it finally shows what I wanted.
There is research on the performance of diesel engines using charcoal/coal slurry, now I “just” need to read all the 29032993232 pages.
“Charcoal emulsification
In order to be pumped, the charcoal powder had to be mixed into an emulsion of diesel and fatty acids to produce a slurry. The target of these studies was to obtain a charcoal slurry with viscosity less than 100 cP at 25 C and high calorific value.
Charcoal Charcoal type: cedar.
The particle’s median diameter 10.33 microm, Fig. 5
Water Distilled water
Diesel Summer type, 6.5 cSt at 25 C
Weight ratio: Charcoal:diesel:water 25:72.2:2.8 (with surfactant)
Mix speed Mixed by homogenizer at average speed: 6000 rpm, Fig. 5
Viscosity For measurements, a rotor type viscometer was used.
Viscosity was measured at spindle’s speeds: 60 rpm, 6 rpm, 0.3 rpm. Temp.
Both production and measurements took place at room temperature.”
In the end the project said that it would be more efficient to use indirect injection of charcoal powder instead of slurry.
Well, since we are already here, then why not use compression ignition anyway?
It still needs a spark plug for controlled ignition.
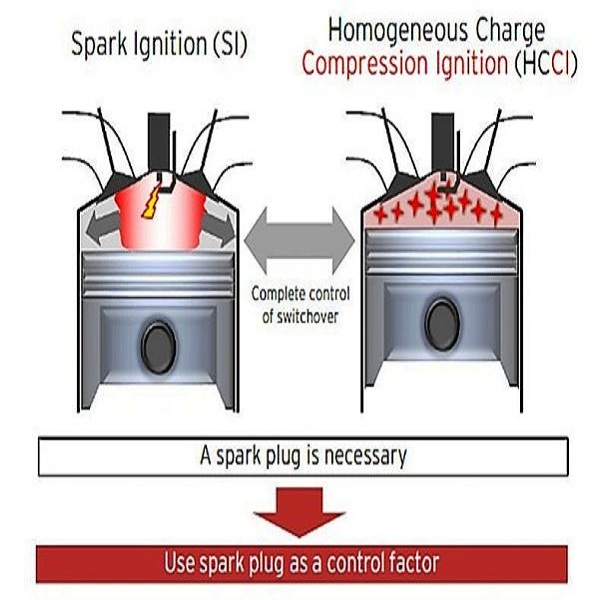
Now, I need to learn it and find a 4 stroke diesel engine that is best for this job, especially if it is a single cylinder. Just like one of those super high compression ratio engines for ships. On top of all that, building it to be an adiabatic engine.
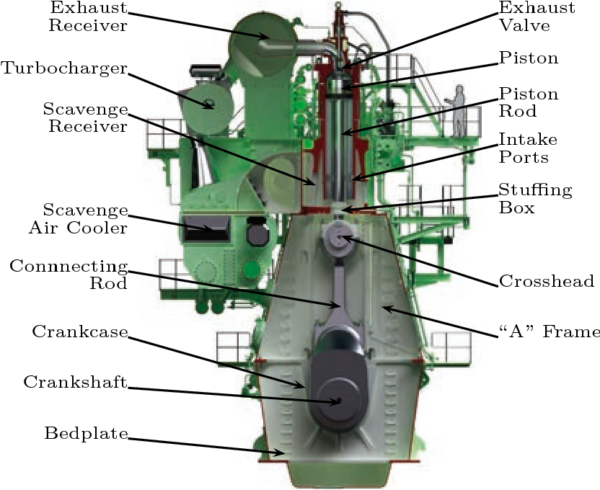
Well, it seems like compression ratio isn’t everything when it comes to engine horsepower… It is possible to double the output of a combustion engine by simply increasing the air input pressure with a few PSI.
I was intending on making the engine with the fastest rpm possible, so the piston would need to be as small as possible, but… It is said that the maximum speed diesel engines can is 5500 rpm because diesel doesn’t burn fast enough, although I would like to doubt that if the engine in question is adiabatic (and using charcoal), which could lead to fast combustion… Maybe?

Obviously, I’m not going to simply coat a polymer engine with ceramic, but make an insulated composite base material for the engine and then add the polymer on the outside.
The electric generator will be just like I was planning before:
A brushless stator and an electromagnetic rotor, the brushless stator will increase its amperage, thus, its resistance to torque gradually until the speed of the motor is slightly reduced, then, through that you can tune it whenever you like. For example, you could lower the amperage when the motor is rising and increase it when it is descending, allowing the motor to only experience resistance on its power stroke.
Well, f*ck.
As always, it took me a while to figure out the obvious: It is really fricking hard to design an engine and generator from scratch, so now I need to find a diesel engine that can output 100 to 300 horsepower with as few cylinders as possible. I was thinking of a single cylinder because (supposedly) it would be easier to make, but I doubt I will find a single cylinder engine (and a generator at that) with 300hp that isn’t as big as a building…
Well, I kinda found it, but it is not that simple (as always).
The thing is: I’m going after the biggest engines out there and divide the number of cylinders by the output power, and even if a single cylinder produces too much power, then I will “just” reduce its size. Or take an already existing engine and increasing its size x amount of times
I'm still procrastinating, but for some reason I went to check on batteries and the like.
Not because I found a crazy battery that has thousands of watt-hours, but because I went calculating its weight based on the amount of joules it would provide.
Wattage is like kilometers per hour and Joules are the exact distance you travelled, so even though you went to 100 km/h, you only went that fast for around 100 meters. If you were to keep going for 100 km/h for an entire hour, then yes, you would have travelled 100 kilometers.
The same apply to wattage and amount of joules.
So, an Iron Air battery that could supply around 1,000 watt-hour per kilogram, would store around 1000 x 3600 joules per hour in each kilogram.
So, 3,600,000 or 3 MJ per kilogram (gasoline can provide 46 MJ/kg).
- 100 horsepower hour = 268,451,953 joules, or 268 MJ
- 268,451,953 joules / 3,600,000 joules = 74.5699869444
- I would need an iron air battery with at least 74 kilograms for every hour consuming 100 horsepower.
However, my interest peaked because I was wondering if I could throw away the oxided iron in order to be lighter and consume less energy for every moment.
Then, I also thought about supercapacitors and my little research that I've made with dielectric elastomers, which are the same thing.
For some reason unknown to me, supercapacitors use an electrolyte to store the charge as both ions and electrons, unlike dielectric elastomers.
And it got me wondering:
How much energy I could store with those dielectric materials?
I was talking about materials with dielectric strength/voltage breakdowns around 50 KV or even more, with dielectric constants around 80 to 300 using titanium dioxide and lead zirconate titanate (which have 500 to 6000).
So I got to a capacitance calculator and I inserted these values, however, I don't know how correct these values are.
So, I found this:
"And so, the dielectric constant for teflon is 2.1, and we multiply that by permittivity of free space 8.85 times ten to the minus 12 farads per meter. And then, multiply by the area of five square meters and divided by 0.01 millimeters, which is 0.01 times ten to the minus three meters. And, this gives 0.93 microfarads as the capacitance."
So, doing the same thing with the supposedly material with 300 as dielectric constant:
- 300 x 8.85x10^-12 = 2.655e-9 farads per meter
- Capacitance calculator: 0.00000331875 farads
The area was around 1.25 m² because I took a cylinder volume calculator and made a cable with 10cm of length and 4cm of thickness, which would be a cable for 1000 amps. Then I've input the values of a rectangle volume caculator and matched the volume from teh cylinder with the rectangle with 1mm of length, 10cm of height and around 125cm ofwidth.
Which when I've inputed on the rectangle area calculator, gave me around 1.25 m² of surface area.
(this thing would weight around 10kg btw)
I inserted then the separation distance of 1mm and the calculator gave me a capacitance of 0.00000331875 Farads.
When I inserted the capacitance and the voltage (50,000 volts) on the capacitor energy calculator, it gave me the value of: 4,148.4 joules for every 10 kilograms of capacitor.
Even if I changed it from copper to conductive polymer, it would still be 4 kilojoules per kilogram (10 times lighter). :|
By the way, 8.85x10^-12 = 0.00000000000885.
So I would need to increase the capacitance by 112,994,350,282 times in order to increase its capacitance to 1 farad per meter. :|
Well, now I know why the electrolyte is required alright...
A conventional supercapacitor stores around 20,000 Joules of energy per kilogram, and it normally uses aluminium oxide as the dielectric material, which in turn, has a dielectric constant of around 10.
Assuming that I use the diamond powder to increase the dielectric constant to 1000, then I would store 100 times more energy, which would be around 2 MJ (2 million joules) per kilogram.
The dielectric consant is related to the temperature of the material, some increase with heat, some decrease with heat.
Maybe using these changes could increase the energy density of supercapacitors, although, the electrolyte would need to be comfortable in these conditions in order to work.
Well, I don't know if I can even approximate how much energy it would be stored, since the thickness of the aluminium oxide layer in aluminium supercapacitors is around 4 nanometers (or 0.00004 millimeters). And on top of that, it is highly porous to increase its surface area without increasing its size.
It is really a complex science and at the moment google doesn't show me a single article about the effect of temperature and dielectric material on the energy density of supercapacitors. :/
... And I doubt this would change too much, a graphene supercapacitor (the most energy dense supercapacitor) was able to achieve 88,1 wh/l, or 317,160 joules per liter (which is probably per kilogram too).
... So, another useless detour. lol
Well, I was mentioned in a Mech video (not as this account's name) and I saw a bunch of comments talking about a variety of different manners of storing energy.
For example, there are molten batteries and molten-air batteries. Which I never heard about.
Molten-air battery's storage capacity among the highest of any battery type (phys.org)
Accordingly to this news article, a carbon molten air battery would have around 28 MJ (megajoules = 1 million joules) per kilogram of mass.
I would need around 10 kilograms of this stuff for every 100 horsepower-hour that I would consume.
The page links to an article on the subject, I gotta study about it to check if is going to work in a practical manner.
I do hope they don't need some acidic/toxic electrolyte to work tho...
Well, too bad, in this specific article they use lithium carbonate and barium carbonate for both the iron and carbon battery (I didn't care about the vanadium battery because it is expensive).
So, if I'm going to use molten lithium carbonate at 800ºC at the risk of losing charge to the formation of CO2, then why not just use the Molten Carbonate Carbon Fuel Cell?
(I just checked, most articles still use molten carbonates based on lithium, sodium and potassium, just like molten carbonate fuel cells)
... For some reason I feel less pro-active these days, I don't have energy for anything at the moment. Maybe I should stick with Molten Carbonate or Molten Hydroxide fuel cells instead of making the adiabatic carbon-diesel engine with the brushless generator.
Before writing about the new coil actuator down below the off-topic section, I do think this project log in specific is pretty useless, I just complain that other methods aren't that viable and jump straight to a combustion engine. Which is the one of the most complex systems I suggested.
Besides, I could also use the TEG generators to recycle some of the wasted heat of the Molten carbonate fuel cells.

I just found this concept for a molten carbonate fuel cell, it looks just like a conventional fuel cell and I do think this way it could allow for a system to properly control the electricity output.

While looking for other molten carbonate fuel cell structures I found out you can literally use anything that is carbon based, even wood and hydrocarbons, but I'm not really going to test inserting gasoline in a 700-800 ºC furnace, lol
Actually, if I'm not mistaken, they process the fossil fuels in order to take out elements like sulfur and then insert into the fuel cell just like that. :|
Now I'm doubt which one I should choose: molten air carbon battery or molten carbonate fuel cell.
- Both need to be at 650-800ºC to work
- Both need carbon.
- Both need energy heat itself up and mantain functionality
- Only Molten carbonate needs air intake and co2 recycling
- I would need to find an energy source to charge the batteries
- I would need need to find fuel for the carbonate
- The molten battery could have multiple cells around the body, both risky and redundant
- The molten carbonate would only need a single cell
- The battery needs to carry all the 200kg of carbon while the fuel cell consumes it
Oh well, I guess this is settled
Just found this video, common table salt can become a ionic liquid until its molten (around 800ºC). So maybe this could be an useful material for the carbonate fuel cell, of course, assuming that the carbonates aren't working as an ionic fluid already, since these are considered "salts".

Source: https://www.sciencedirect.com/science/article/abs/pii/S0378775301009429
This is a 250 KW Molten Carbonate Fuel Cell that uses hydrocarbon gas fuel by the way...
Is the idea of maintaining the electrolyte solution in a ceramic bucket even remotely viable?
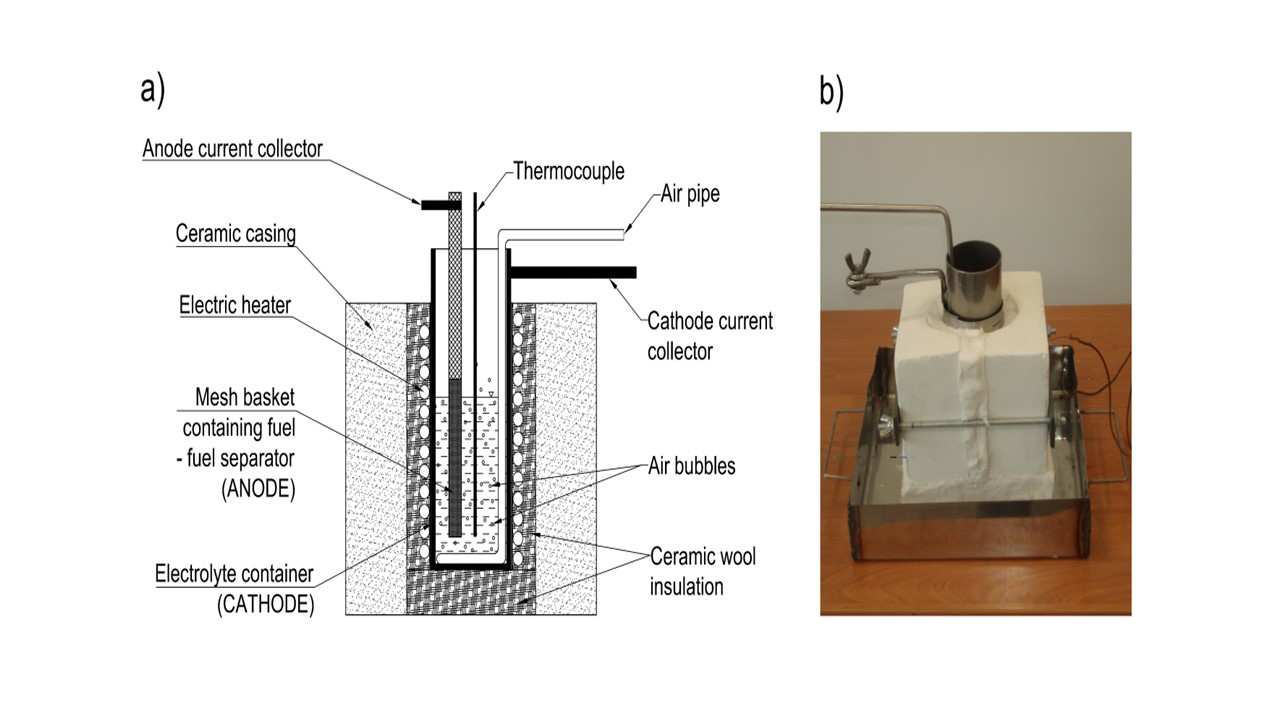
I was even thinking on mixing the carbonates with their equivalent carbonates: sodium silicate, potassium silicate and lithium silicate and using a sacrificial fiber material, so it becomes some kind of huge sponge-like cell.
Why do they need such immense sizes for a 250 KW fuel cell?
Hydrogen fuel cells can be this smaller too:
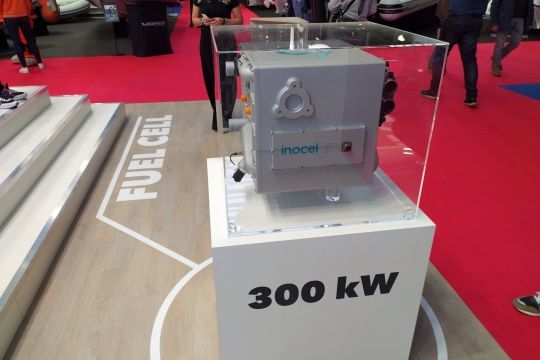
I also just found out about molten chloride fuel cells, which use things like table salt (sodium chloride). Dunno what is the difference between these two in the matter of performance and efficiency, but I suppose there are many, many types of molten fuel cells.
Off-topic:
So, I just scrolling on youtube shorts (definitely not procrastinating) and I saw this little video here:
The spheres are magnetic (can lift 9 kilograms), which is interesting, but anyway.
I was thinking: could you make a "disactivation" coilgun with this?
I've made a rough estimative with that by inputing the weight of a possible projectile and the thrust required to accelerate it towards mach 4 in 0.001 seconds (the length of a 60cm barrel), and basically, it would need a thrust of 6000kg.
Well, I don't necessarily need to start with 6 tons of electromagnetic force, but you you get what I mean.
Basically, I thought on lining up those holding electromagnets (since they are just like permanent magnets) launch the electromagnetic projectile in its direction and once it gets more or less in the middle of each section, the electromagnet is disactivated and its remaining electricity is pumped into the next electromagnet until the thing is launched.
A 100kg holding electromagnet only uses 14 watts, but I do know that I would probably need to increase its output power severely, since the "trick" to these electromagnets is that they complete the magnetic field using the ferromagnetic target (the object it attaches itself to).

However, the idea would be to put the nort and south poles of electromagnets in a "C" along the tube of the gun.
Kinda like this:
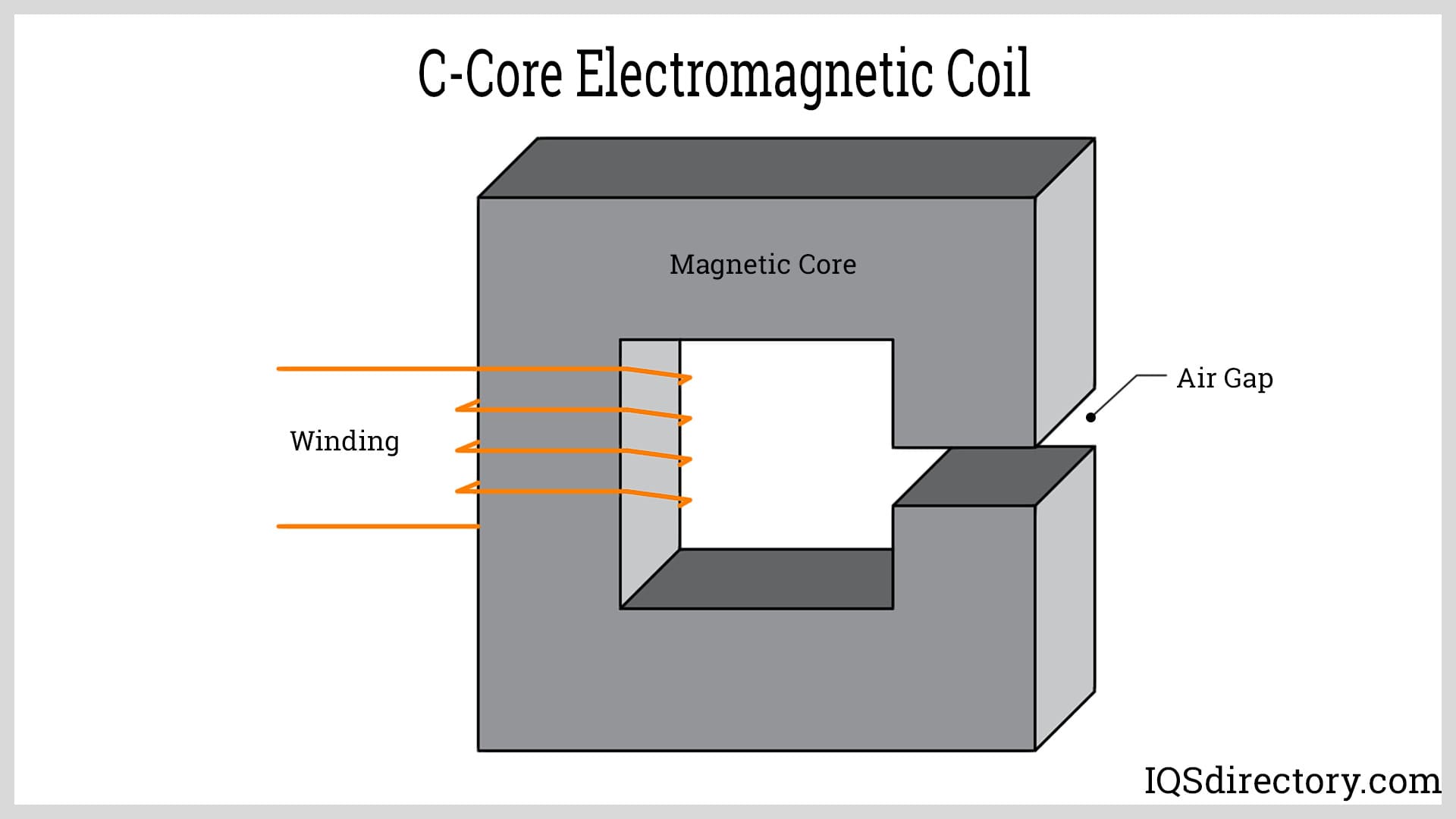
Insert a tube in the air gap and it is pretty much what I thought.
I just couldn't find any kind of coilgun like that, the closest I found was a "quench coilgun" that instead of disactivating the coils, it quenches/heats up superconductors in a sequence.
I just said that, and it seems this is a "reluctance coilgun", which would be better with aircore solenoids instead of iron core electromagnets because the core has a limit on the amount of magnetic flux it can allow to pass through itself.
Source: https://4hv.org/e107_plugins/forum/forum_viewtopic.php?id=83108
There is a lot of interesting concepts would there, for example:
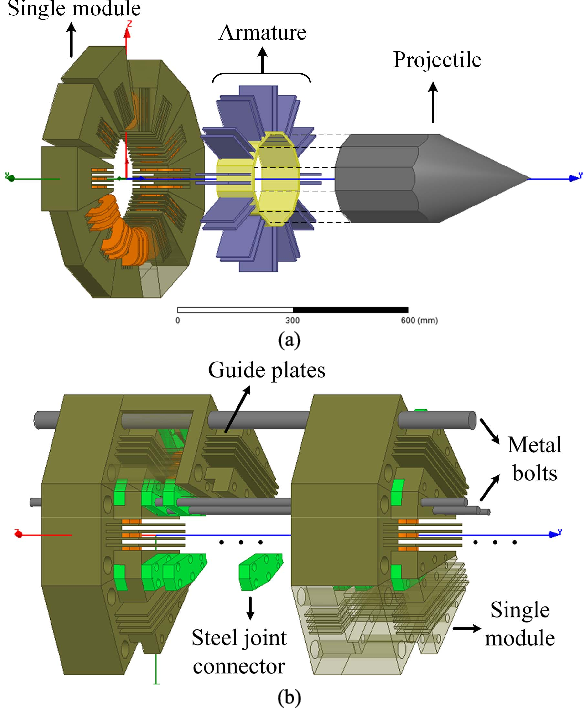
Wait a minute, wouldn't this be actually great for pilebunkers?
The magnetic rod wouldn't scape the solenoid's insane electromagnetic field and would go back and forth just like the first video of the magnetic sphere.
Pilepunkers are always depicted as a combustion/detonation machine, but I don't think anything would be able to survive the detonation and be cheap enough for its use.

... But if that is the case, then why not just use it to push a projectile really fricking fast instead of launch it with a coil gun?
There was actually a silenced projectile/gun like that, but with combustion instead.

It is called a "captive piston cartridge".
Not Off-topic - Revisiting Actuators:
Now that I ended up procrastinating and researching about railguns, I found out that the lower the speed of the railgun, the higher its efficiency.
So, a 1000 m/s (Mach 2.9) railgun has efficiencies around 40% while a 3500 m/s (Mach 10) to 5000 m/s (Mach 14) has efficiencies around 30% to 20%.
So, this made me think: what if the speeds were actually 1.33 meters per second just like the mech needs?
If the efficiency raises up to 80% to 90% at these speeds, then I could make an actuator that is super light, effiicent, strong, cheap, simple and fast.
Even better than artificial muscles and electric motors.
Just now I found out that the maximum efficiency would be 50%, but I asked chatGPT to make the calculation on how efficient it would be for a railgun to push a 3000kg projectile at 2 m/s and it said it would be around 1% to 0.2%...
I went asking around to see if there is something like this, but people normally just scoffs at the question, just says it is idiot or plainly ignores it.
... Which is kinda frustrating... I just want to understand if it works or not... And I don't think I have the resources to test this out...
I just found a few articles about it, and they don't even mention the efficiency of the system...


Do I really need a railgun actuator tho?
The coilgun actuator could do the same work, an 1 ton solenoid holding magnet uses around 1 to 3 kilowatts of power and weighting 3kg to 5kg.
Of course, the holding solenoid isn't that powerful because it needs a ferromagnetic material to close its magnetic loop, but would a solenoid be able to pull up this much power by also using an electromagnetic inner rod/plunger?
... But the solenoid rod has less moving force the further it is from the center, so you would need it to be stronger X amount of times.
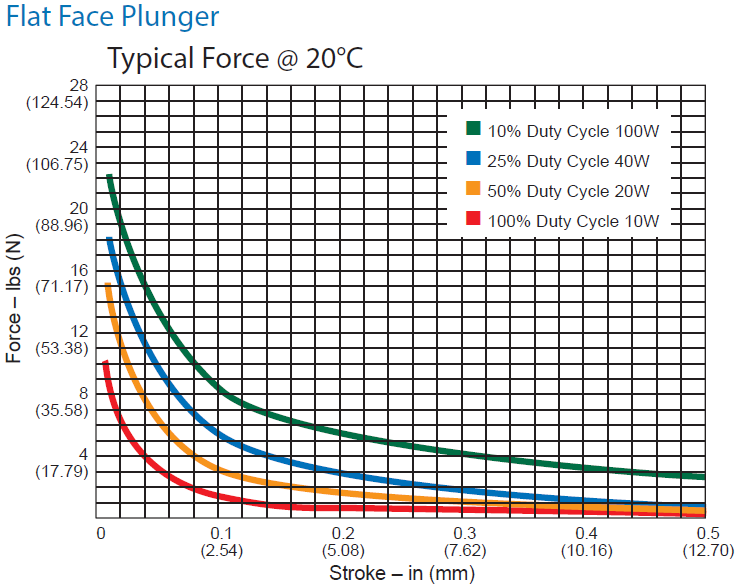
... No matter how much I feel I learned with this project, I always learn that I know nothing.
I'm in the right path? I'm making real progress? I actually checked every option properly?
I should've been in an engineering college or something like that... Or else I can't see this project being completed... 🤔
I just now found something similar to the railgun-coilgun hybrid, but for actuation porpuses.
And stopping to think about it, I don't think this is an "hybrid" like the templin institute said, but just a coilgun with a commutator...

Source: https://lifeboat.com/em/chapter.4.pdf
As you can imagine, the idea is pretty simple: make the sliding contact coilgun, but use it as an actuator instead.
Could this finally mean that I could have an efficient, simple, cheap, practical that outputs force proportional to the energy input?
You could also built it with flexible tubes/fibers in order to work just like a muscle, which would be a pain in the butt to maintain and verify for defects and wear. But at least you would have the first and only electric artificial muscle with efficiencies above 80%.
Well, the only problem would be the wear and friction of the commutator/sliding contact, which is also a source of inefficiencies and cost of maintenance on normal brushed motors.
MAYBE this time it will be easier to find the energy input and efficiency because both are coils/solenoids.
... But I think I'm looking at it in the incorrect manner... Should I make it brushless instead?
You see, the first idea I had for this was the linear brushless motor... And I discarded it because it would be too heavy and expensive.
Maybe it didn't work at first because I've made a brushless motor with a rotor (the moving part) with too many slots? Just like in the image above?
... And also because I couldn't possibly make an ESC controller with hundreds of amps and hundreds of volts.
... Which I wouldn't worry about while building the brushed linear motor.
Sorry for not calculating this thing right now.
For some reason I'm feeling indisposed...
But goddang it, it kinda a pain in the butt to convert joules to watts.
Supposedly, accordingly to kinect energy calculators, I woud need around 2,665 joules to move the 3000kg load at 1.33 m/s target. But the problem is that joules can't be directly converted to watts because watts is a matter of work over time.
So I can't just convert joules to watts and watts to volts and amps. It would be so much easier this way tho...
So, basically, I need to make coils on Blender and measuring their height, diameter, number of turns and thickness of wires in order to use a solenoid force calculator.
And even then it is not that easy, because the calculator probably only shows the force at the center of the solenoid, not on its outside.
... But I could just use a back iron plate to redirect the electromagnetic field...
I guess one way of looking at it would be thrust to move an object to certain speed.
If we use a speed calculator to move something at 1.33 m/s with a 30 cm distance, it would take 0.22556 seconds.
If we take an acceleration calculator, to move from 0 to 1.33 m/s would need an acceleration of 5.896 m/s².
If we take a thrust to acceleration calculator, to move a 3000kg mass to 1.33 m/s with an acceleration of 5.896 m/s², it would need a thrust of 17,688 newtons or 1,803.8 kg-force.
If we want to quadruple the speed (let's say, when jumping), you would need 7,215.2 kg-force.
Obviously, the transmission of power isn't perfect and it would require more energy, but at least I think it will be easier to find a result for said brushed coil actuator.
Also, let's remember that the reduction in the transfer of the lever limbs (aka, where the actuator is attached to the limbs in the body will work like a lever) will be 3:1, an increment of 3 times the speed and decrease of 3 times in its strength, reaching the speeds the human body reaches.
From stationary to even 12 meters per second or 43 km/h while carrying 1 ton of weight.
A kind soul told me that I should start calculating the inductance first and then calculate how the solenoid should be.
Well, I roughly calculated the inductance, magnetic field strength etc. And I still can't tell how strong the electromagnet would be, neither if this electromagnet would be strong enough to lift 3 to 10 tons.
I'm mcfuckin losing it my guy, I can't find a way of predicting the force output of the coils no matter how much I look into it.
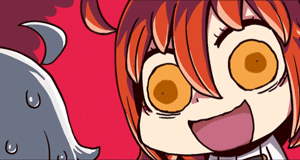
Also, I think the previous estimative that the actuators would need to accelerate masses to 1,33 m/s is incorrect because I didn't take into consideration the gravity of earth, which is 9,8 m/s².
So, essentially I need to counter that acceleration of gravity and then add the 1,33 m/s to the mix.
No matter what, the results are never consistent.
I ask to chatgpt and it says it will have less than a single newton of force, I go to solenoid force calculators and they say my coil would have 10 million newtons of force.
Here is the question that I copy paste for every ChatGPT:
I need an electromagnet solenoid coil to pull up an outer electromagnetic with an X amount of force.
How I can calculate its force?
The outer diameter of the inner coil is 190mm, the inner diameter is 110mm, the space between the turns is 1mm, the height is 82mm, number of turns is 2, the length of the wire itself is 1193.8mm, the ampearge is 1000 amps, the voltage 200 volts, it has a distance of 1mm between this coil and the outer coil and is at 10mm above the inner electromagnet.
The outer coil has a wire thickness of 40mm, a spacing of 1mm between the turns, 2 turns and an inner diameter of 194mm, so an outer diameter of 274mm, the amperage is 1000 amps, the voltage is 200 volts, the length of the wire itself is 1721.6mm
Mistra-medium from PoeGPT said the following:
Sure, here are the calculations for the force exerted by each solenoid coil with 400 V and 500 A:
For the inner solenoid coil:
The cross-sectional area of the inner solenoid is:
A = π * (190/2)^2 - π * (110/2)^2 = 14,094 square millimeters
The force exerted by the inner solenoid can be calculated using the formula:
F = (μ₀ * N * I^2 * A) / (2 * g^2)
F = (4π × 10^-7 * 2 * 500^2 * 14,094) / (2 * 1^2)
F = 88,220 Newtons
For the outer solenoid coil:
The cross-sectional area of the outer solenoid is:
A = π * (274/2)^2 - π * (194/2)^2 = 39,377 square millimeters
The force exerted by the outer solenoid can be calculated using the same formula as above:
F = (μ₀ * N * I^2 * A) / (2 * g^2)
F = (4π × 10^-7 * 2 * 500^2 * 39,377) / (2 * 11^2)
F = 37,364 Newtons
Now, let's try the same thing again:
If you increase the voltage to 500 volts and the amperage to 400 amps in both coils with the 40mm wire thickness, the force exerted by the solenoids will increase significantly due to the increased current flowing through the coils.
The force exerted by an electromagnetic solenoid is proportional to the square of the current, so doubling the current will result in a four-fold increase in the force. Using the same calculation as before, the force exerted by the inner solenoid coil at 500 volts and 400 amps would be:
F = (μ₀ * N * I^2 * A) / (2 * g^2)
F = (4π × 10^-7 * 2 * 400^2 * 14,094) / (2 * 1^2)
F = 352,880 Newtons
Similarly, the force exerted by the outer solenoid coil at 500 volts and 400 amps would be: F = (μ₀ * N * I^2 * A) / (2 * g^2)
F = (4π × 10^-7 * 2 * 400^2 * 39,377) / (2 * 11^2)
F = 149,456 Newtons
Well, this value is unnusually high, so I asked it to recalculate with an wire with the proper diameter for 400 amps, but it got way less force, so I asked why that was the case.
And the answer from the Mistra-medium was:
I apologize for the confusion in my previous responses. You are correct that the forces I calculated earlier for the 40mm thick coils were much higher than the forces I calculated in my latest response for the 14mm thick coils.
The force exerted by an electromagnetic solenoid coil is proportional to the current flowing through the coil, the number of turns in the coil, and the cross-sectional area of the coil. Since the current and number of turns are the same in both cases, the difference in force can be attributed to the difference in cross-sectional area.
For the 40mm thick coils, the cross-sectional area of the inner coil was approximately 14,094 square millimeters, while the cross-sectional area of the outer coil was approximately 39,377 square millimeters. In contrast, for the 14mm thick coils, the cross-sectional area of the inner coil is approximately 1,848 square millimeters, while the cross-sectional area of the outer coil is also approximately 1,848 square millimeters.
Therefore, it is not surprising that the forces exerted by the 14mm thick coils are much lower than the forces exerted by the 40mm thick coils. In general, larger coils with more turns and a larger cross-sectional area will be able to produce a stronger magnetic field and exert a greater force.
I hope this clarifies any confusion. Please let me know if you have any further questions or concerns.
No, seriously, this doesn't make any sense. I asked around and people told me I'm stupid.
I mean, they aren't wrong, but I guess it is useful tho...
Dunno if this is useful at all, but I was only expecting an approximation, not an absolute answer. But I guess it is better than start with absolutely nothing.
Just now I decided to calculate the weight.
The weight of a single aluminium coil actuator in the molds I just talked about would weight around 28kg.
840kg in total for all 30 actuators.
The 14mm thick wire would weight around 5kg per actuator, 150kg in total.
Maybe sticking with the HASEL artificial muscles is a better idea?
Of course, that is the weight of all actuators that can output 10 tons to 50 tons (accordingly to the chatbots), I could make the upper limbs lighter (and weaker).
It took me almost an entire month just to figure this idea wouldn't work...🥲
(assuming ChatGPT is correct)
I think that the slip contact coilgun turned actuator could be used in a round planar format for certain axis.

The image is from a coreless axial flux motor, but you could turn it in a single coil/solenoid and maike a rotary brushed coilgun turned actuator.
Now what?
What I do now?
Also, like I said before: I can't buy anything for the next 7 months because that is how much I divided the cintiq style table.
So I don't know if I will be able to continue this project until next year. In fact, I don't even know how to start.
I guess a good start could be making the 3D model of the linear actuators and parts that I would need to make/print.
Another thing is that now that I look at it, I don't feel confident with the Stewart Platform's range of motion. But I will only know for sure when I at least make a non-colision simulation.
(I think I need to figure out a way of turning this linear motor into a telescopic one)
Actually I figured out how to make telescopic, but it hard to explain without a proper picture, and I couldn't find a proper picture.
Just imagine a linear motor's stator and its moving rod, if you "simply" puts the hollow stator in the middle, a moving rod in the center and hollow rod outside of the stator, you can move both rods at the switching of the electromagnets of the hollow stator in opposite directions if both have opposite poles.
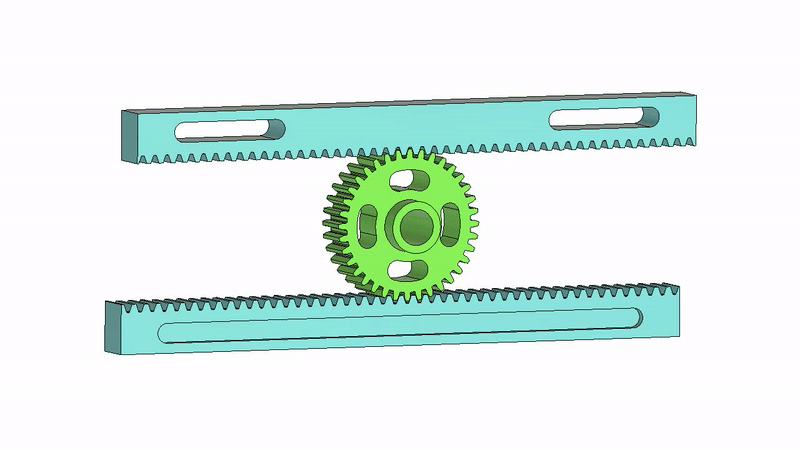
Just replace the gears and teeth with electromagnetic coils.
Also, I was wondering if a dual solenoid coil would work for an electric artificial muscle.
Basically, a center solenoid has a fixed length and the outer solenoid is all stretched out, both have opposite polarities, forcing the outer stretched solenoid to "contract" in the direction of the fixed length solenoid.
Dunno if it would work tho...
I was just going to test it on my adjustable power source that I bought a time ago and the plug literally broke its teeth.

Well, I made a quick fix and tested it anyway.
It didn't work, probably because I'm stupid.
Behold, the utimate mech:
Source: https://www.p
Discussions
Become a Hackaday.io Member
Create an account to leave a comment. Already have an account? Log In.
i'm working on the actuator tech! (electrostatic). will def let you know when it gets good enough https://www.youtube.com/shorts/KBmnelunbLc
also, for power supply, lightcell might work? https://lightcellenergy.com/ they seem to be rather early, but seems promising as a lightweight electricity supply.
Are you sure? yes | no
actually there is another idea, nucleation of plastics to gasoline. There are a few videos on youtube that might be worth looking into. The machines are not too complex either, some designs use magnetrons though so you'll need some microwave ovens
Are you sure? yes | no
This process of converting plastic to fuel not exactly makes gasoline, and it results on the plastics turning in a really toxic by-product.
https://youtu.be/Dkl5TyGP5eo
Are you sure? yes | no
If the problem is availability of liquid fuels then maybe liquefying your own methane from syngas is a better idea? if you can get wood/coal for very cheap then it might make sense to convert hundreds of kilos of wood into some liters of liquid methane.
Of course you can also attempt a bioreactor to obtain mostly pure methane from organic garbage, but it might take a while.
Are you sure? yes | no
But methane only gets liquified at -82ºC and at high pressures, no?
Are you sure? yes | no
yep..... with a double loop cooler you can reach -82 C, maybe by recycling the loops from old refrigerators. Pressure wise you might get away with 30 Atm if you reach -82, it falls quickly the colder you get.
sounds crazy but it miiiiiight be easier than making your own diesel engine to run on coal dust.
Are you sure? yes | no