Tuesday, 14/03/2023, 19:09
So... Uuuh
I was searching a lot about the composite casting process and all of that, but eventually I had to face the problem with the progressive valves.
You see, the initial idea was to use a magnetic fluid that would solidify under an electromagnetic field.
So, this would (hyphotetically) allow me to achieve super high precision movements.
And the way I would do that would be using weight sensors (that are normally used on precision scales) to measure the force applied to them over time, and then translante that information into how much electricity would heat those electromagnets.
That would (hyphotetically) allow the "pilot" to achieve real time and precise movements (super hyphotetically).
However, since I'm changing the working fluid to plain water, and using centrifugal water pumps (that are normally used for pools or aquariums), this instantaneous progressive valve won't be possible anymore.
So, the obvious step to take was using servo valves, the 3D printed ones, the price commercial ones are obscene.
Some 3D printed servo valves simply strap a micro servo to a regulatory valve:

Link for this valve (there are tons of STL archives on servo valves).
Others use what is called a "pinch valve", simply put, it is a valve that squeezes the hoses, just like one would do when watering their garden.
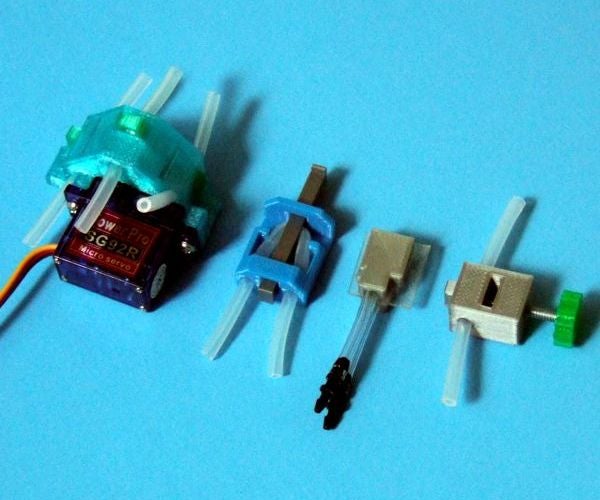
These are from this link.
There are a lot of ways of doing a pinch valve.
She posted the link to a github with the archives in her comment section.
However, those kinda present two problems: speed and torque.
Micro servos aren't known for being fast, neither strong, and I'm talking about really big hoses here.
... So... I was thinking on a possible pinch mechanism that could be operated manually...
And I think I came to the idea that maybe the best think for this matter is a bycicle brake:
It uses a scisor/pinch-like mechanism to squeeze the wheels of a bike, and can be used fully manually, with or without the servos.
You would only need to press the brakes with the movement of your body.
Of course, the placement of those things would be a little tricky... But doable.
Well, I don't know how much precise and effective these homemade pinch-valves will be, but...
If these actually work properly for the exosuit...
... This means that I would have an entire mechanical/analogical powered exosuit.

Dunno about you guys, but I always thought of exosuits as this super ultra technological stuff. But somehow I'm (hyphotetically) making one with random crap I found around my house :|
I don't know how to feel about this, lmao
And yes, I will take time to write more project logs, I'm still searching for stuff.
The only thing that is kinda making me angry is the fact that no one sells water pumps that can output 500 liters per minute without the electric motor.
So I literally have to pay 4 times more than a conventional hydraulic oil pump for... Reasons.
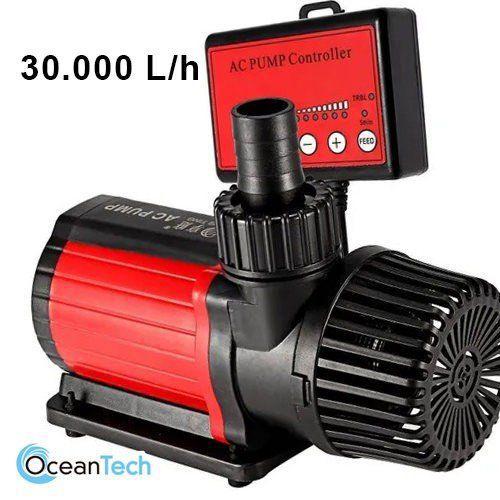
The entire pump is meant to be submerged, so the electric motor is (probably) extra sealed and extra protected.
THe thing is, I just need the plastic sh*t attached to it, and no online seller wants to sell me it separately. >:|
Edit¹:
I just said this and I immediatly found it:

Hard to believe this cheap piece of plastic costs 400 reais (76 dollars).
Edit²:
I found out in the same day I looked at the description, but basically, this thing is expensive because it is from a specific kind of underwater pump that puts the magnet core (the black stuff behind the pump) outside of the electric motor, so the water being pumped works as a coolant.
However, I couldn't find anywhere the rotor/impeller alone. :/
Discussions
Become a Hackaday.io Member
Create an account to leave a comment. Already have an account? Log In.