Saturday, 24/06/2023, 20:06.
Edit⁴:
Although I always forgot to say this, ChatGPT is not a trained and well informed professional on anything, and all the affirmations that it makes and that I take as somewhat truth are not, in fact, true.
I could say or take something incredibly wrong and incomplete as truth, when in fact, I don't dominate the subject in any capacity to simply say "I know what I'm doing".
It is not like I can pay some professional to actually make this project, so I will be forced to work with what I got.
And what I got is gut feeling and a stupid AI that doesn't know how to do math. :|
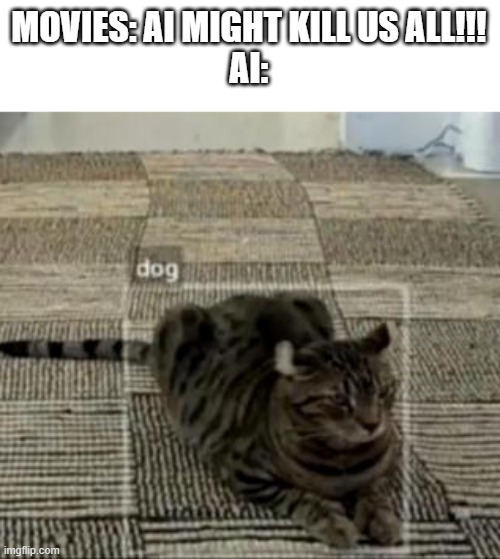
Also, relevant:
Summary:
Each DIY alkaline eletrolyte membrane will be made using 10g of PVA (polyvinyl alcohol) 5g of PVP (polyvinyl pyrrolidone) mixed with water, molded into shape until dry with no bubbles, prensed between two glass plates for 24h for optimal surface.
Then 20ml of glutaraldeyde (2%), 10 drops of HCL (Chloridric Acid) and 40ml of pure acetone will be mixed in a crosslink solution in which the membrane will be submerged for 40 minutes for the reaction to occur and transform the membrane in some hydrogel looking material.
Lastly, a solution made with 50 ml of water, 8.6g of KOH where the membrane will bath is then heated up to 60ºC for 3 hours until the membrane gets a brownish colour. Meaning it is ready to be used.
_____________________________________________________________________
Right now I feel stupid and dumb.
You know the Alkaline Hydrogen Fuel Cell that I talked about? That it needed pure oxygen and all that stuff?
Well, guess what, I can just use a Carbon Dioxide Scrubber System at the air entrance of such hydrogen fuel cell.
The CDS system, although it sounds fancy, it is just Sodium hydroxide (caustic soda/lye) beads/granules in a filter before the system, so the KOH (potassium hidroxide) electrolyte/proton exchange membrane and the iron/nickel based catalysts don't get poisoned with carbon.
Once these are saturated with the product of the reaction (Sodium Carbonate or soda as), you can just heat up the material so it releases the carbon dioxide (CO2) and then it is ready to be used again.
There are even tutorials on youtube.
There are some tutorials teaching how to use it to "purify your air".
Welp, I don't know about you, but I ain't putting caustic soda in my homemade filter.
PS: I read somewhere that you could also use activated carbon in order to capture the CO2 from the air, but these are not as efficient.
I showed this project log to a friend of mine and he didn't quite get what was so simple about this conundrum. So, in summary:
Basically, I thought so fricking hard to make an hydrogen fuel cell that doesn't break down in contact with regular air that I completly missed the point on asking *why* it breaks down in contact with the air.
And the reason is because of the CO2 in the air that slowly destroys it, and I can simply put a filter in front of a fuel cell in order to make it work properly.
That's why it was so simple to solve.
And that's why I felt so dumb: I could've just have asked the right question and I would've found the right solution.
____________________________________________________________________
In fact, you could literally use sacrificial KOH before the Alkaline Hydrogen Fuel Cell and then reverse it.
How do you reverse it?
You dissolve in water.
:|
You could literally dissolve KOH on a water tank, then pass gas bubbles through the tank, cause the cristalization until it is satured and fully crystalized, then open it to ambient air so the CO2 can escape the solution.
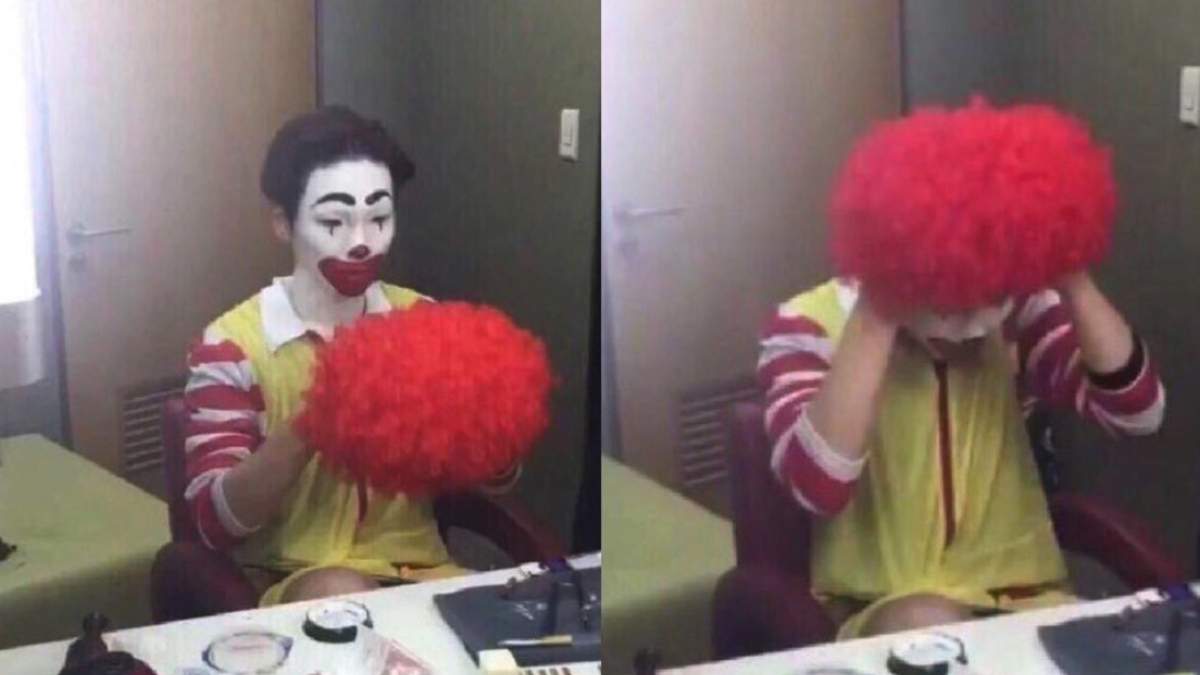
Edit¹:
As it is the nature of ChatGPT, it kinda oversimplified some steps, for example, the reversibility of the sacrificial KOH from Potassium Carbonate back to Potassium Hidroxide.
It involves mixing it with other acids in order to get back at KOH, and at first, it suggested some really dangerous and nasty acids such as Nitric Acid.
However, it gave the following solution using acetic acid, which in its own impure state is also known as vinegar:
Acetic acid (CH3COOH), commonly known as vinegar, can also be used to convert potassium carbonate (K2CO3) back to potassium hydroxide (KOH). The reaction with acetic acid proceeds as follows:
K2CO3 + 2CH3COOH → 2CH3COOK + CO2 + H2O
In this reaction, potassium carbonate reacts with acetic acid to produce potassium acetate (CH3COOK), carbon dioxide (CO2), and water (H2O). The carbon dioxide is released as a gas, and the resulting product is potassium acetate.
To obtain potassium hydroxide from potassium acetate, you can perform another step. You would need to react potassium acetate with a strong base such as sodium hydroxide (caustic soda/lye) or calcium hydroxide (slaked lime/hydrated lime):
CH3COOK + NaOH → CH3COONa + KOH
In this reaction, potassium acetate reacts with sodium hydroxide to produce sodium acetate (CH3COONa) and potassium hydroxide (KOH). The sodium acetate is a byproduct and can be separated from the potassium hydroxide solution.
Alternatively, you can also convert potassium acetate to potassium hydroxide by electrolysis. By passing an electric current through a potassium acetate solution, you can split the acetate ions and generate hydroxide ions, leading to the formation of potassium hydroxide.
So, while acetic acid can be used to convert potassium carbonate to potassium acetate, an additional step with a strong base or electrolysis is required to obtain potassium hydroxide from potassium acetate.
And once both Caustic soda and/or Slaked lime are saturated with CO2, you would need to heat up both to around 800 ºC.
Well, it would be easier to simly stay at Caustic Soda to begin with instead of all this convoluted plot.
I say this, because I was thinking on actually pumping the KOH solution inside and outside of the fuel cell system in order to continiously purify its air and its electrolyte at same time, after all, soon or later the electrolyte would also become poisoned with CO2 content since no method is 100% efficient at keeping these things alway.
However, I don't know if it would be wise to literally heat caustic alkaline water to 800 ºC constantly in a system in order to keep it from getting CO2 poisoned.
I know that it would be possible to heat small spoon quantities of Caustic Alkaline Water to 800ºC in continuous steps, but it would be safer/practical/efficient to do that?
_____________________________________________________________________
Also, I'm asking a lot of stuff to Chat GPT, and it seems like the membranes used on Alkaline Hydrogen Fuel Cells are "Polymer Electrolyte Membranes" PEM, but it also says that I should use KOH impregnated Nafion, which is a proton exchange membrane PEM.
... Which is leaving me confused, but ok.
Also, I was asking what would happen with other components if I were to mix KOH with it. You know, it would be relevant since I was thinking on using cement or plaster.
"When potassium hydroxide (KOH) is mixed with sodium silicate (also known as water glass), several reactions and effects can occur:
- Formation of Silica Gel: The combination of KOH and sodium silicate can result in the formation of a silica gel. The alkaline nature of KOH reacts with the silicate ions in sodium silicate, causing the gelation of silica. This gel formation can lead to increased viscosity and thickening of the mixture.
- Alkalinity: Both KOH and sodium silicate are highly alkaline compounds. Mixing them together will result in an even higher alkalinity in the solution. This increased alkalinity can have various effects, such as enhanced reactivity, increased dissolution of certain materials, and potential damage to organic substances.
- Binding Properties: Sodium silicate is known for its binding properties, and when combined with KOH, it can act as a binder or adhesive. The resulting mixture can form a solid mass or bond surfaces together, depending on the application and concentration.
- Increased pH: The pH of the mixture will be significantly high due to the presence of KOH and sodium silicate. This high pH environment can impact the stability and reactivity of surrounding materials, including cement, plaster, or other substrates.
It's important to note that the specific effects and outcomes of mixing KOH with sodium silicate will depend on the concentrations, ratios, and specific conditions of the mixture. These factors can influence the viscosity, binding properties, and chemical reactions that take place. It is recommended to conduct small-scale tests or consult experts in the field to assess the compatibility and desired outcomes for your specific application."
Well, you now know that if you simply mix KOH with Sodium Silicate (liquid glass) you will make a really good electrolyte membrane for the Alkaline Hydrogen Fuel Cell. :|
Edit³:
Actually, mixing Sodium Silicate with Potassium hydroxide (KOH) won't work, it will result in Potassium Silicate and Sodium Hydroxide (Caustic soda).
(potassium silicate can be either found as liquid glass, such as sodium silicate, or fertilizer, but I don't know which type is the better for this application, I would bet on potassium silicate liquid glass, since it would probably be purer than fertilizer)
You would need to mix Potassium silicate and Potassium Hydroxide together in order to make the somewhat solid electrolyte compound of "Potassium Silicate Hydroxide", it isn't super soluable in water, but it could affect it after some time.
I was kinda wondering it wouldn't be better to simply make a reversible hydrogen fuel cell, where after the pure hydrogen and pure oxygen are converted into water, you could separate both again and store both in a container.
It would work just like a battery, but not with 90% of efficiency... Althogh I would just mix tanks and explode everything, lol.
Also, I asked the same thing in other chats with chatGPT and basically, if mixed with water, it can transform the things into hydrates, which doesn't seem to be that useful for the reaction.
But in any case, an alkaline hydrogen fuel cell can either be KOH (potassium hydroxide) based or Sodium Hydroxide based, in either case you would need to mix potassium silicate with potassium hydroxide and sodium silicate with sodium hydroxide.
You could also use both at the same time.
____________________________________________________________________
Mixing transparent PVA glue with polyvinyl alcohol (PVA) and/or chitosan bioplastic with KOH (potassium hydroxide) can have various effects depending on the specific concentrations and conditions. Here are a few possibilities:
- Enhanced adhesive properties: Both PVA glue and polyvinyl alcohol are water-soluble polymers with adhesive properties. Mixing them together may result in an adhesive with improved bonding characteristics, such as increased strength or tackiness.
- Changes in transparency and flexibility: PVA glue is known for its transparency and flexibility when dry. Adding polyvinyl alcohol or chitosan bioplastic may alter these properties. The resulting mixture could become less transparent or less flexible, depending on the concentrations and interactions between the components.
- Gel formation: When PVA or polyvinyl alcohol comes into contact with potassium hydroxide, it can undergo a gelation process. The KOH acts as a cross-linking agent, causing the polymer chains to link together and form a gel-like substance. This reaction could lead to the formation of a gel when PVA glue is mixed with KOH.
- Structural changes and material properties: Chitosan bioplastic is derived from chitin, a natural polymer found in the exoskeletons of crustaceans. When chitosan bioplastic interacts with KOH, it can undergo structural changes and potentially dissolve or break down. Mixing chitosan bioplastic with KOH could result in a change in material properties, such as reduced strength or altered biodegradability.
It's important to note that the specific outcomes of mixing these materials depend on the concentrations, ratios, and other factors involved. The effects can vary significantly based on the specific formulations and intended applications. It is always advisable to conduct small-scale tests or consult relevant scientific literature before proceeding with large-scale applications or experiments.
Well, since I will be mixing everything with sodium silicate, I think it would be a good idea to not mix chitosan with it since it can literally decompose in the presence of such alkaline solutions.
But PVA with Polyvinyl Alcohol could stay, I guess.
Also, there are other Alkaline Polymers that could be used, such as Polysulfone or "Poly(ether sulfone) (PES)".
I don't know if "Polysulfone" and "poly(ether sulfone)" are the same thing, but I found on aliexpress some ads selling 100 units for less than 100 reais (20 dollars) as disposable syringe filters.
It would be a hell of a work to do, but it would be orders of magnitude cheaper than actual fricking nafion and platinum.
... It was this f3cking easy...
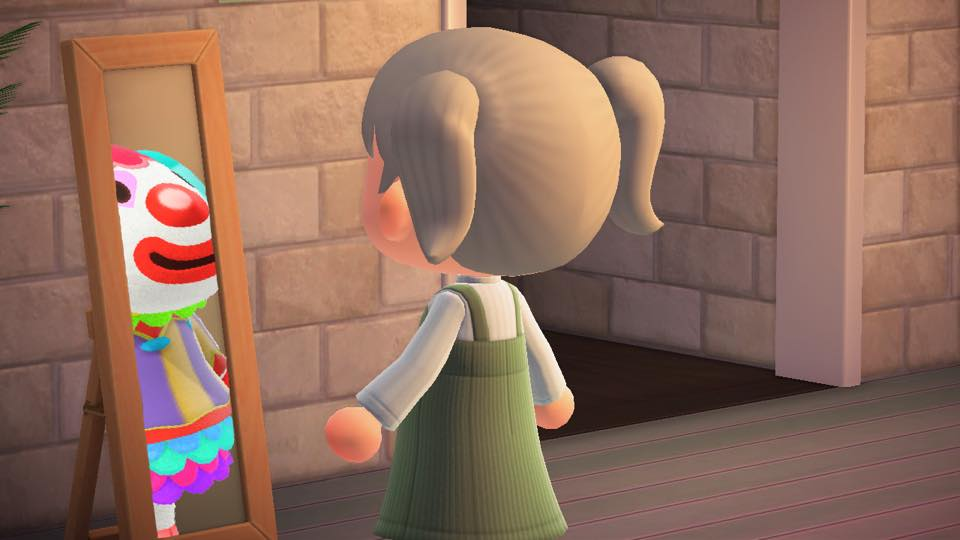
Edit²:
Dunno if I should have created a new project log or just make an edit to this one.
So, I asked a crapton of questions to ChatGPT and it gave me interesting suggestions.
Materials to enhance the Electrolyte:
(graphene and carbon nanotubes also work very well)
Determining the "better" or most efficient additives among the listed options depends on various factors such as the specific application, desired properties, and compatibility with the PES-KOH membrane. It is important to note that the effectiveness of additives can vary depending on the specific system and performance requirements. That said, here are some additives that are generally recognized for their potential to enhance PEM efficiency:
Ionic Liquid Additives:
- 1-Ethyl-3-methylimidazolium bis(trifluoromethylsulfonyl)imide (EMIM TFSI) is a commonly used ionic liquid additive known for its high ionic conductivity and stability.
Conductive Polymers:
- Polyaniline (PANI) and polypyrrole (PPy) are widely studied conductive polymers known for their high electrical conductivity and compatibility with PEM systems.
Plasticizers:
- Glycerol is a commonly used plasticizer that can improve the flexibility, processability, and ionic conductivity of PEMs.
- Propylene carbonate is another effective plasticizer known for its ability to enhance the mechanical properties and ionic conductivity of PEMs.
Fillers:
- Carbon nanotubes (CNTs) have shown promise as fillers due to their excellent electrical conductivity and reinforcement properties. They can enhance the mechanical strength and electrical conductivity of PEMs.
- Silica nanoparticles are commonly used as fillers to improve the mechanical properties and thermal stability of PEMs.
It's important to note that the efficiency and performance of the additives can vary depending on their concentration, dispersion, and interaction with the PES-KOH membrane. Conducting thorough experimentation and testing is crucial to evaluate the specific performance enhancements provided by each additive in the intended application.
Ceramic cloth, also known as ceramic fiber cloth, is a high-temperature-resistant material typically made from ceramic fibers. It is commonly used for insulation, sealing, and protection in various industries, including aerospace, automotive, and high-temperature applications.
While ceramic cloth may possess advantageous properties such as thermal stability and mechanical strength, its direct application as an additive or filler in polymer electrolyte membranes (PEMs) for fuel cells is less common.
In PEMs, the addition of ceramic cloth may introduce challenges and considerations such as:
- Porosity and Ionic Conductivity: Ceramic cloth is typically porous, which can hinder the ion transport and ionic conductivity within the PEM. Efficient ionic conductivity is essential for the performance of PEMs in fuel cells.
- Compatibility and Integration: Ensuring proper integration and compatibility between the ceramic cloth and the polymer matrix can be challenging. The difference in thermal expansion coefficients and mechanical properties between the ceramic cloth and the polymer matrix may lead to delamination or reduced mechanical integrity of the PEM.
- Manufacturing and Processing: Incorporating ceramic cloth into the PEM matrix may require specific processing techniques and optimization to achieve uniform dispersion and proper adhesion. This can add complexity to the fabrication process.
It is worth noting that the specific application and design of the fuel cell system can influence the feasibility and effectiveness of using ceramic cloth as an additive in the PEM. Research and development efforts are ongoing to explore novel approaches for incorporating ceramic materials into fuel cell systems, but currently, other fillers and additives may be more commonly used to enhance PEM properties in fuel cell applications.
If you are considering the use of ceramic cloth in a PEM for a fuel cell, it is advisable to consult experts in the field and conduct thorough testing to evaluate the compatibility, performance, and long-term stability of the ceramic cloth within the PEM system.
Me:
So, what it is the porosity Required for every part of an Alkaline Hydrogen Fuel cell?
Does the electrodes need to be microporous? How to achieve the required porosity?
Does the KOH electrolyte membrane needs to be porous? Microporous? Solid?
ChatGPT:
In an alkaline hydrogen fuel cell, different components have specific requirements for porosity. Let's discuss the porosity requirements for each part:
- Electrodes: The electrodes in an alkaline hydrogen fuel cell typically consist of a porous material, such as nickel or nickel-based alloys. These electrodes need to be porous, specifically microporous, to facilitate efficient gas diffusion and allow for the electrochemical reactions to occur. The porosity in the electrodes provides a large surface area for the reactant gases (hydrogen and oxygen) to come into contact with the catalyst and participate in the electrode reactions.
To achieve the required porosity in the electrodes, various methods can be employed, such as:
- Sintering: This involves compacting the metal particles into a desired shape and then subjecting them to high temperatures to bond the particles together while retaining porosity.
- Coating: A porous layer can be applied to a solid substrate through techniques like electrodeposition or plasma spraying.
- Electrochemical deposition: This method allows for the controlled growth of porous structures by applying a current to a conductive substrate in a suitable electrolyte.
- KOH Electrolyte Membrane: In alkaline fuel cells, the electrolyte is typically a potassium hydroxide (KOH) solution. The electrolyte membrane in these fuel cells does not need to be porous. Instead, it is typically a solid, non-porous material that separates the anode and cathode compartments, allowing the transport of ions (OH-) while preventing the mixing of hydrogen and oxygen gases.
The KOH electrolyte membrane is commonly made of materials like polybenzimidazole (PBI) or polymeric blends, which provide good ionic conductivity without the need for porosity.
To summarize:
- Electrodes need to be microporous to facilitate gas diffusion and electrode reactions.
- KOH electrolyte membranes are typically solid, non-porous materials.
It's important to note that specific design considerations and variations may exist depending on the type and configuration of the alkaline hydrogen fuel cell being used.
Me:
Is there any kind of solution that I can mix with the carbon substrate to increase its strength? This carbon sponge sounds quite fragile.
Mixing resin won't make the electrode less microporous?
ChatGPT:
You are correct that adding a resin to a carbon substrate can potentially decrease its microporosity. Resins tend to fill the pores and reduce the overall porosity of the material. This can hinder gas diffusion and affect the performance of the electrode in a fuel cell.
If you want to maintain the microporosity of the carbon substrate while still improving its mechanical strength, an alternative approach is to reinforce the carbon structure with fibers or additives that do not significantly block the micropores. Here are a couple of options to consider:
- Carbon nanotubes (CNTs): Incorporating carbon nanotubes into the carbon substrate can enhance its mechanical properties while maintaining microporosity. CNTs are known for their high strength and conductivity. They can be dispersed within the carbon matrix to provide reinforcement without significantly affecting porosity.
- Carbon fiber reinforcement: Adding carbon fibers to the carbon substrate can improve its mechanical strength. Carbon fibers are lightweight and have high tensile strength. By combining them with the carbon substrate, you can create a composite structure that maintains microporosity while gaining enhanced mechanical properties.
In both cases, the carbon fibers or CNTs can be mixed with the carbon substrate during the fabrication process. For example, in the case of a carbon sponge, you can incorporate these reinforcing elements into the sponge structure before carbonization.
By using these reinforcement methods, you can potentially strengthen the carbon substrate while preserving its microporosity, allowing for efficient gas diffusion in a fuel cell application.
It's important to note that the specific process and parameters for incorporating these reinforcements may require further research and optimization. The proportion and distribution of the reinforcing elements should be carefully considered to achieve the desired balance between strength and porosity.
Mixing sodium silicate with a carbon substrate, such as cotton, and subsequently subjecting them to high temperatures in a low-oxygen environment is a process known as carbonization or charring. This method can potentially result in the formation of a carbon-based material.
When sodium silicate is heated, it undergoes decomposition and loses its water content, leaving behind solid silica (SiO2) particles dispersed within the carbon structure. The carbonization process involves the conversion of the organic material (cotton) into carbon, while the silica particles become embedded in the resulting carbon matrix.
The addition of silica particles from the sodium silicate may offer certain benefits:
- Reinforcement: The presence of silica particles can potentially enhance the mechanical strength of the carbon material, providing additional structural integrity.
- Templating effect: The dispersed silica particles can act as templates during carbonization, helping to maintain the porosity of the carbon material.
- Thermal stability: Silica particles can contribute to the overall thermal stability of the carbon material, improving its resistance to high temperatures.
However, it's important to consider potential challenges and limitations:
- Uniform dispersion: Achieving a uniform dispersion of silica particles within the carbon matrix can be challenging. Uneven distribution can lead to areas of higher or lower mechanical strength or porosity.
- Porosity control: While the addition of silica particles may help maintain porosity during carbonization, the overall porosity and pore size distribution will still depend on the initial structure of the carbon substrate and the carbonization process parameters.
- Compatibility with KOH electrolyte: The presence of silica particles in the carbon material may affect its interaction with the KOH electrolyte. It is important to consider potential changes in electrochemical performance and stability when evaluating the material for use in an alkaline fuel cell.
In summary, the addition of sodium silicate and subsequent carbonization can potentially modify the properties of the carbon substrate. However, achieving the desired balance between mechanical strength, porosity, and compatibility with the fuel cell system would require careful experimentation and optimization. It is advisable to thoroughly test the resulting material and evaluate its performance in an alkaline hydrogen fuel cell setup to ensure its suitability and long-term stability.
So yeah, although pure silica nanoparticles are as expensive as gold on the internet, you can literally just heat it up in order to make it useful for the entire Alkaline Hydrogen Fuel Cell.
And yes, you would want to do it in order to make it useful, since pure sodium silicate is soluable on water, and since the result of hydrogen and air reaction is the generation of water...
Anyway, I don't remember if I already posted this here, but I saw a guy making a carbon sponge out of bread exactly the same way ChatGPT suggested.
So I was thinking on literally mixing all the ingredients for the Alkaline Hydrogen fuel cell with bread dough, put it on the oven until it actually becomes actual bread (with carbon fiber, sodium silicate and all that stuff that you don't wanna eat), cut it into slices of your choosing and then use the process shown above to convert to electrodes.
So yeah, let's just take a moment and appreciate how I literally came up with an Hydrogen Fuel Cell that you actually bake in the oven with bread.
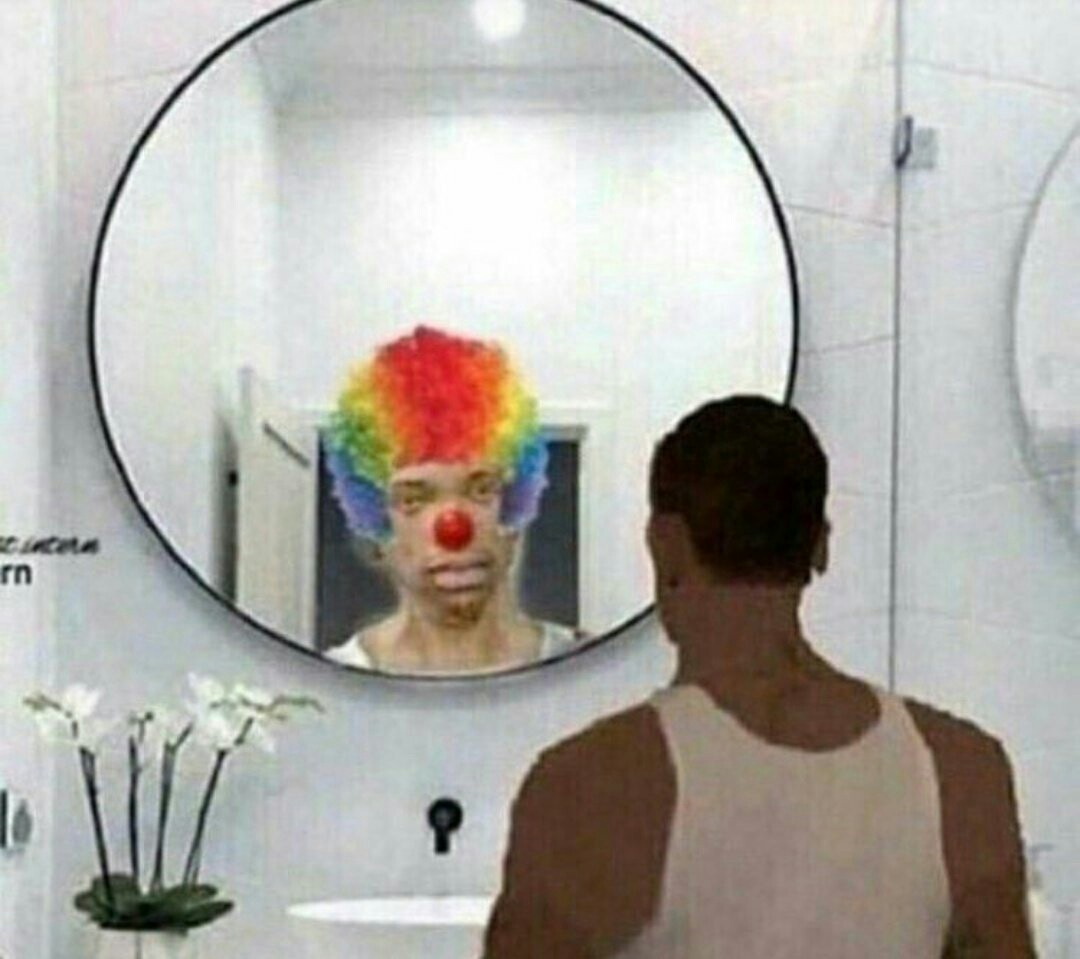
Another method that I found is a little more dangerous and I still didn't check if it would alter every ingredient or anything like that, but if you mix sugar with sulfuric acid, you get carbon sponge.
Mixing house sugar (sucrose) with sulfuric acid does indeed result in a carbonized material, commonly referred to as "black snake" or "carbon snake." This reaction is often demonstrated in chemistry shows due to its visually interesting and dramatic nature. However, it's important to note that the resulting carbonized material may not be suitable or optimal for use as a microporous layer in an alkaline hydrogen fuel cell for several reasons:
- Purity and impurities: The carbonized material obtained from the sugar-sulfuric acid reaction may contain impurities from both the sugar itself and the reaction process. These impurities can affect the material's performance and stability in a fuel cell.
- Porosity control: While the carbonized material may have some inherent porosity, the control over the porosity and pore size distribution may be limited compared to specialized materials designed for fuel cell applications. The porosity of the carbon sponge may not be optimized for efficient gas diffusion in a fuel cell electrode.
- Chemical compatibility: The carbon sponge obtained from sugar and sulfuric acid may not be chemically compatible with the alkaline electrolyte, such as KOH. The presence of impurities or residual sulfuric acid remnants can lead to chemical interactions and potential degradation of the material in the fuel cell environment.
- Mechanical properties: The mechanical strength and durability of the carbon sponge produced from sugar and sulfuric acid may not be sufficient for long-term operation in a fuel cell. Specialized carbon substrates and reinforcement techniques, such as carbon fibers or nanotubes, are typically used to enhance the mechanical properties of fuel cell electrodes.
While the sugar-sulfuric acid reaction produces an intriguing carbonized material, it is generally more suitable for educational purposes or as a novelty demonstration rather than as a functional component in a fuel cell.
For optimal performance and stability in a fuel cell, it is recommended to use commercially available materials specifically designed for fuel cell applications or to explore other established DIY methods that offer better control over the desired properties, such as those mentioned earlier (e.g., carbon nanotubes, carbon fibers).
Discussions
Become a Hackaday.io Member
Create an account to leave a comment. Already have an account? Log In.