Tuesday, 28/05/2024, 11:41
Well, well, well...
I didn't, in fact, "do it" and finally start building things.
And the previous project log was so long it started deleting new text, so I'm forced to make this one.
Uuuuuuugh, this is me from the future, and even though I call ChatGPT stupid for not making math correctly, guess what? Neither does I, I keep forgeting certain parts on the equations and I need to make everything again and again.
This is me from the further future, you know what? I'm gonna redo all the calculations!
(obviously, you won't notice after the log is edited)
Not related, but look, I just found this cool scene featuring a mech:
(and yes, I go around youtube watching all kinds of mechs in media, I just think the scenes are cool)
-
In any manner, I'm trying to figure out how to make the McKibben hydraulic artificial muscles. And before I actually build those, I need to figure out how much force the materials will need to withstand and how much force the actuator will be able to output.
As you may not remember, since it was many project logs ago, the best way of making the most efficient hydraulic McKibben muscles is to make a non-elastic (but flexible) bladder and make it more filament like.
Not to mention that the easiest way to mass-produce filament-like McKibben artificial muscles is by using a small sock knitting machine.
Sources:
- https://www.researchgate.net/publication/309272509_Modeling_and_testing_of_a_knitted-sleeve_fluidic_artificial_muscle
- https://www.researchgate.net/profile/Jordan-Chipka/publication/289579804_Variable_recruitment_inelastic_bladder_hydraulic_artificial_muscles_for_high_efficiency_robotics/links/6113ce070c2bfa282a391aec/Variable-recruitment-inelastic-bladder-hydraulic-artificial-muscles-for-high-efficiency-robotics.pdf
- https://www.researchgate.net/publication/308043606_Musculoskeletal_lower-limb_robot_driven_by_multifilament_muscles
- https://www.researchgate.net/publication/337094820_Recurrent_Braiding_of_Thin_McKibben_Muscles_to_Overcome_Their_Limitation_of_Contraction
- https://www.sciencedirect.com/science/article/abs/pii/S0924424723002303
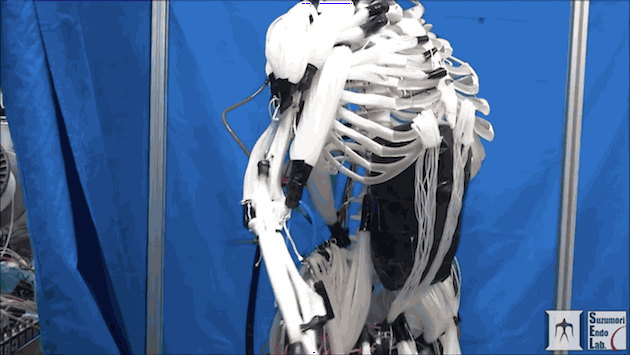
Anyway, I do need to figure out how to mass-produce the inner bladder, although I can buy kilograms of plastic tube, it would still be preferable to handmake those instead of buying, it will be expensive enough to buy the required equipment for the pump and electric motor.

This one costs 57 dollars or 250 reais (without the taxes).
Actually, I think I'm just overthinking the inner bladder thingie, I could "just" extrude it just like the filaments for the braided sleeve.
In any manner, it is only left for me to find out the optimal dimensions for the materials since I intend on applying 150 bars of pressure.
And after all of that, I need to figure out a way of making/testing/calculating the dielectric elastomer fibers, because I have a gut feeling that these braided sleeves won't be that great in the end.
Well, I think the first approach I will attempt on how to calculate the knitted braided sleeve is to assume each hole between the braided sleeve is a ring, just like in a chainmail.
This way I will probably find a rough estimation on how much force the fibers need to withstand in order to survive. Then I will add a safety factor of 7.
Funnily enough, the answers I got from ChatGPT are actually almost the same, but there is something I'm finding weird. Basically, they all agred that 900kg of force would be applied to the ring area and then divide the force bewteen the six links.
But since the tension on the links is being concentrated on 6 points, it doesn't make much sense that it would equally divide the force between linking points...
Maybe I should've asked it to pretend it is a chain link...
I got the answer and it keeps saying it is around 300kg or 2000kg, maybe the idea of a safety factor of 7 was asking for too much...
In either way, I will have to use those 2 ton sized HDPE ropes...
Well, I was looking at charts about Rope Strength based on material and thickness of the rope so I can figure out how thick should be the DIY HDPE rope for 2 tons in these artificial muscles, and lo and behold: any kind of polyethylene that doesn't use UHMWPE is not shown.
Source: https://denverrope.com/rope-strength-guide/
It seems like Nylon, Polyester and even Polypropylene have higher tensile strength than HDPE. :|
Well, Prolypropylene has an yield tensile strength (tensile strength before permanently deform) of 20 to 45 MPa, so this means that I still can use the composite of HDPE and graphene/silicon carbide to double the strength of the fibers of HDPE.
In any manner our rope of 40 MPa made out of HDPE+graphene+silicon carbide (I'm thinking on giving up on fiberglass it is kinda messy to work with) would need the following dimensions:
- 38mm of diameter and 3 twisted strands.
Well, I don't even know how I will fit this thing in a filament muscle with 28mm of diameter, lol.
Well, I asked chatGPT to use that old equation for McKibben muscles that I asked in this post
on worldbuilding stackexchange, but it gave me results around 900kg and 1600kg.
I tried to make the equation as follows:
- 15000*pi*28^2(3(cot(20)^2)(1-1.30*0.2)^2-csc(20)^2)
And it resulted in:
- 3142595105.5096786503920999.
(even if you take out the three zeros behind 15 KPa, it still gives around 300 tons of force, which is absolutely not possible)
I feel like I will never make this equation correctly...
Well, I found an article about a 21mm in diameter McKibben muscle that uses 7MPa of pressure and 8 kilonewtons (800 kg) of force.
I couldn't check it with sci-hub either, but at least this is a good indicator.
If we simply take the pressure and output and doubles, the result of 1600kg is also right.
kelvinA kindly shared the source for a free access article.
Source: https://www.fujipress.jp/ijat/au/ijate000600040482/
However, the article only uses 7 MPa as the maximum pressure input and 2 MPa as the nominal pressure input.
But in one of the graphs it is shown that in fact, it would output 800 kg of force with a diameter of 21mm.
At 2 MPa it outputs 300kg of force.
By the way, I was calculating the weight of the hydraulic fluid if I were to fill the hydraulic muscles.For example: let's assume that the muscles have 30cm (24cm when contracted) of length and a diameter of 28mm when fully actuated. So, this single muscle would weight 0.12kg.
- 0.12kg x 90 (9000kg of output) x 30 muscles in total = 324kg in total for the hydrauic liquid alone.
Just remember that in reality the artificial muscles would be way longer since I intend on braiding them to increase contraction ratios, so it would weight way more than that.
Sure, not all muscles would be contracted at all times, but letting things as simple as that wouldn't change much either.
Now I need to figure out where the hell I'm going to find 300+ kg of hydraulic oil (400 Liters). :|
If it was water, it would be easy to collect, now hydraulic oil...?
I think I could reduce the liquid volume required by using sponges or other materials, although the sponges aren't rigid, they still occupy space, but since they are solid and not compressible, they wouldn't allow for more fluid to get into the muscles.
Reducing the weight based on the amount of volume they are occupying.
I suggested sponges because it was the first thing in my mind, solid rods/chains of plastic/metal would still help to reduce the hydraulic oil required, but not saving in weight. HDPE has a density similar to hydraulic oil, it would still weight the same, but I wouldn't need to expend money on hydraulic oil.
Yes, I could "just" use water and a water pump.
But even then, I don't know anymore.
a 30kg brushless motor with a 80kw output converted to 300kw or even 400kw would weight around 120kg to 150kg.
How much would the pump weight?
So, 300kg to 400kg of working fluid + 120kg of motor + Xkg of pump + 200kg of fuel + 100kg of pilot + Ykg of skeleton (that would weight just as much as the rest of it) = 720kg + X + Y.
All of this crap just to lift 1 ton of weight...
I don't even know how to strike a balance of "weight required to be lifted" and "weight of the system".
Maybe someone smarter than me would've figured it out by now. Maybe a professional would.
... Or maybe a professional would rapidly understand that this whole endeavor is a waste of time.
Re-calculating:
I need to remember something:
- The artificial muscles that I'm calculating have a length, force and speed proportional to a human sized humanoid. I did it at the start for simplification's sake, like a template I can easily edit later. Depending on the final size of the mech skeleton or even an exoskeleton, the input wattage/horsepower would considerably change, maybe triple or even octuple (8x).
- On top of that, I do need a safety factor, which would increase the weight even more.
- Last, I need to add more muscles to compensate for the weight of the strucutre of the mech itself, like the weight of fuel, pilot, endoskeleton and equipment (containing the hydraulic fluid if it is to be used).
I don't know which value to use for the weight of the skeleton, and it will heavily change based on the size and shape, which will also require the increase in actuator's weight.
It may be a waste of time to calculate the weight of the muscles and horsepower output even before designing the rest of the structure, but I kinda prefer to just take this part out of my mind first.
When I finally start designing the skeleton, I will need to come back here and use the weights as reference.
But it got me wondering, is making the next limb x times stronger than the previous one even a good idea?
This is literally an exponential equation that would only get out of control
Multifilament Hydraulic McKibben Muscles:
So, 2 MPa is already good enough, me thinks. The paper does say it would output around 300kg of force, and I think this is already good enough. The author literally had to use PBO fibers (expensive) and a 3 layer inner bladder for this one.
3 times extra strength for every consecutive muscle 21mm:
- Biceps/Arm: 3 tons = 10x 2 MPa fiber muscles = 1.2kg x 2 sides = 2.4kg
- Shoulders: 3 ton x 3 Extra force = 9 tons = 30 muscles x 6 stewart platform actuators = 180 x 0.12kg = 21.6kg x 2 sides = 64.8kg
- Torso: 9 tons x 3 extra force = 27 tons = 90 muscles x 6 stewart platform actuators = 540 x 0.12kg = 64.8kg
- Legs: 27 tons x 3 extra force = 81 tons = 270 muscles x 6 stewart platforma actuators = 1620 x 0.12kg = 194.4kg x 2 sides = 388.8kg
- 2.4 + 64.8 + 64.8 + 388.8 = 518.64kg in total.
- Safety factor of 2: 1,037.28kg
- Safety factor of 4: 2,074.56kg
2 times extra strength for every consecutive muscle 21mm:
- Biceps/Arm: 3 tons = 10x 2 MPa fiber muscles = 1.2kg x 2 sides = 2.4kg
- Shoulders: 3 ton x 2 Extra force = 6 tons = 20 muscles x 6 stewart platform actuators = 120 x 0.12kg = 14.4kg x 2 sides = 28.8kg
- Torso: 6 tons x 2 extra force = 12 tons = 40 muscles x 6 stewart platform actuators = 240 x 0.12kg = 28.8kg
- Legs: 12 tons x 2 extra force = 24 tons = 80 muscles x 6 stewart platforma actuators = 480 x 0.12kg = 57.6kg x 2 sides = 115.2kg
- 2.4 + 28.8 + 28.8 + 115.2 = 173.04kg
- Safety factor of 2: 346.08kg
- Safety factor of 4: 692.16kg
- Safety factor of 7: 1,211.28kg
1.5 times extra strength for every consecutive muscle 21mm:
- Biceps/Arm: 3 tons = 10x 2 MPa fiber muscles = 1.2kg x 2 sides = 2.4kg
- Shoulders: 3 ton x 1.5 Extra force = 4.5 tons = 15 muscles x 6 stewart platform actuators = 90 x 0.12kg = 10.8kg x 2 sides = 21.6kg
- Torso: 4.5 tons x 1.5 extra force = 6.75 tons = 22.5 muscles x 6 stewart platform actuators = 135 x 012kg = 16.2kg
- Legs: 6.75 tons x 1.5 extra force = 10.125 tons = 33.75 muscles x 6 stewart platforma actuators = 202.5 x 0.12kg = 24.3kg x 2 sides = 48.6kg
- 2.4 + 21.6 + 16.2 + 48.6 = 86.64kg
- Safety factor of 2: 173.28kg
- Safety factor of 4: 346.56kg
- Safety factor of 7: 606.48kg
1.2 times extra strength for every consecutive muscle 21mm:
- Biceps/Arm: 3 tons = 10x 2 MPa fiber muscles = 1.2kg x 2 sides = 2.4kg
- Shoulders: 3 ton x 1.2 Extra force = 3.6 tons = 12 muscles x 6 stewart platform actuators = 72 x 0.12kg = 8.64kg x 2 sides = 17.28kg
- Torso: 3.6 tons x 1.2 extra force = 4.32 tons = 14.4 muscles x 6 stewart platform actuators = 86.4 x 0.12kg = 10.36kg
- Legs: 4.32 tons x 1.2 extra force = 5.18 tons = 17.28 muscles x 6 stewart platforma actuators = 103.68 x 0.12kg = 24.3kg x 2 sides = 12.44kg
- 2.4 + 172.8 + 103.68 + 124.4 = 403.28kg
- Safety factor of 2: 80.65kg
- Safety factor of 4: 161.31kg
Conventional Hydraulic McKibben Artificial Muscles:
Now I need to take that equation in the paper and see if I can actually find calculate something.
- F = (pi/4*(D0^2*P))*(1/sin(O0))^2*{3(1-e)^2*cos(O0)^2-1}
Well, I tried in MPa, in KPa and it still didn't give any result that made sense.
- (pi/4*(21^2*2000000))*(1/sin(20))^2*{3(1-0.20)^2*cos(20)^2-1}
- -565384994.5986882470453348857008804125900264872223170612834861024
But somehow ChatGPT was able to make the equation correctly for some reason. :|
The output force depending on the diameter at 2MPa would be:
Weight of one 50mm diameter muscle with 30cm length: 0.79kg
Weight of one 100mm diameter muscle with 30cm length: 4.77kg
3 times extra strength for every consecutive muscle 50mm:
- Biceps/Arm: 3 tons = 3x 2 MPa muscles = 0.79 x 2 sides = 1.58kg
- Shoulders: 3 ton x 3 Extra force = 9 tons = 7 muscles x 6 stewart platform actuators = 42 x 0.79kg = 35.55kg x 2 sides = 71.1kg
- Torso: 9 tons x 3 extra force = 27 tons = 20 muscles x 6 stewart platform actuators = 120 x 0.79kg = 94.8kg
- Legs: 27 tons x 3 extra force = 81 tons = 59 muscles x 6 stewart platforma actuators = 354 x 0.79kg = 279.66kg x 2 sides = 559.32kg
- 1.58 + 71.1 + 94.8 + 559.32 = 726.8kg.
2 times extra strength for every consecutive muscle 50mm:
- Biceps/Arm: 3 tons = 3x 2 MPa muscles = 0.79 x 2 sides = 1.58kg
- Shoulders: 3 ton x 2 Extra force = 6 tons = 5 muscles x 6 stewart platform actuators = 30 x 0.79kg = 23.7kg x 2 sides = 47.4kg
- Torso: 6 tons x 2 extra force = 18 tons = 13 muscles x 6 stewart platform actuators = 78 x 0.79kg = 61.62kg
- Legs: 18 tons x 2 extra force = 36 tons = 26 muscles x 6 stewart platforma actuators = 156 x 0.79kg = 123.24kg x 2 sides = 246.48kg
- 1.58 + 47.4 + 61.62 + 246.48 = 357.9kg
- Safety factor of 2: 715.8kg
1.5 times extra strength for every consecutive muscle 50mm:
- Biceps/Arm: 3 tons = 3x 2 MPa muscles = 0.79 x 2 sides = 1.58kg
- Shoulders: 3 ton x 1.5 Extra force = 4.5 tons = 4 muscles x 6 stewart platform actuators = 24 x 0.79kg = 18.96kg x 2 sides = 37.92kg
- Torso: 4.5 tons x 1.5 extra force = 6.75 tons = 5 muscles x 6 stewart platform actuators = 30 x 0.79kg = 23.7kg
- Legs: 6.75 tons x 1.5 extra force = 10.125 tons = 8 muscles x 6 stewart platforma actuators = 48 x 0.79kg = 37.92kg x 2 sides = 75.84kg
- 1.58 + 37.92 + 23.7 + 75.48 = 248.8kg
- Safety factor of 2: 497.6kg
- Safety factor of 4: 995.3kg
1.2 times extra strength for every consecutive muscle 50mm:
- Biceps/Arm: 3 tons = 3x 2 MPa muscles = 0.79 x 2 sides = 1.58kg
- Shoulders: 3 ton x 1.2 Extra force = 3.6 tons = 3 muscles x 6 stewart platform actuators = 18 x 0.79kg = 14.22kg x 2 sides = 28.44kg
- Torso: 3.6 tons x 1.2 extra force = 4.32 tons = 4 muscles x 6 stewart platform actuators = 24 x 0.79kg = 18.96kg
- Legs: 4.32 tons x 1.2 extra force = 5.18 tons = 4 muscles x 6 stewart platforma actuators = 24 x 0.79kg = 18.96 x 2 sides = 37.92kg
- 2.4 + 28.44 + 18.96 + 37.92= 87.72kg
- Safety factor of 2: 175.44
- Safety factor of 4: 350.88kg
- Safety factor of 7: 614.04kg
3 times extra strength for every consecutive muscle 100mm:
- Biceps/Arm: 3 tons = 1x 2 MPa muscle = 4.77kg x 2 sides = 9.54kg
- Shoulders: 3 ton x 3 Extra force = 9 tons = 2 muscles x 6 stewart platform actuators = 12 x 4.77kg = 57.24 x 2 sides = 114.48kg
- Torso: 9 tons x 3 extra force = 27 tons = 5 muscles x 6 stewart platform actuators = 30 x 4.77kg = 143.1kg
- Legs: 27 tons x 3 extra force = 81 tons = 15 muscles x 6 stewart platforma actuators = 90 x 4.77 = 429.3 x 2 sides = 858.6kg
- 9.54 + 114.48 + 143.1 + 858.6 = 1125.72kg
- Safety factor of 2: 2251.44kg
2 times extra strength for every consecutive muscle 100mm:
- Biceps/Arm: 3 tons = 1x 2 MPa muscle = 4.77kg x 2 sides = 9.54kg
- Shoulders: 3 ton x 2 Extra force = 6 tons = muscles x 6 stewart platform actuators = 12 x 4.77kg = 57.24 x 2 sides = 114.48kg
- Torso: 6 tons x 2 extra force = 18 tons = 4 muscles x 6 stewart platform actuators = 24 x 4.77kg = 114.48kg
- Legs: 18 tons x 2 extra force = 36 tons = 7 muscles x 6 stewart platforma actuators = 42 x 4.77kg = 200.34kg x 2 sides = 400.68kg
- 9.54 + 114.48 + 114.48 + 400.68 = 639.18kg
- Safety factor of 2: 1278.36kg
1.2 times extra strength for every consecutive muscle 100mm:
- Biceps/Arm: 3 tons = 1x 2 MPa muscle = 4.77kg x 2 sides = 9.54kg
- Shoulders: 3 ton x 1.2 Extra force = 3.6 tons = 1 muscles x 6 stewart platform actuators = 6 x 4.77kg = 28.62kg x 2 sides = 57.24kg
- Torso: 3.6 tons x 1.2 extra force = 4.32 tons = 1 muscles x 6 stewart platform actuators = 6 x 4.77kg = 28.62kg
- Legs: 4.32 tons x 1.2 extra force = 5.18 tons = 2 muscles x 6 stewart platforma actuators = 12 x 4.77kg = 57.24kg x 2 sides = 114.48kg
- 9.54 + 57.24 + 28.62 + 114.48 = 209.88kg
- Safety factor of 2: 419.76kg
- Safety factor of 4: 839.52kg
- Safety factor of 7: 1469.16kg
Fluid Flow:
Well, all options seem interesting...
However, all of these muscles still needs a fluid flow to supply them, and that needs to be taken into consideration for the hydraulic pump that is going to supply them.
Of course, let's take into consideration that:
- The muscles will already be partially full, meaning I will need half of the fluid flow.
- The plastic filler will also keep half of the muscle full.
- The lower density of the hydraulic fluid would make the total weight slightly lower, but the amount of liters would stay the same.
The 21mm muscle - 2 times stronger than the previous muscle - Safety Factor of 2: 346.08kg
- Actuated weight: 0.12kg if water, 0.1 kg if hydraulic oil
- Unactuated weight: 0.08
- 0.12-0.08 = 0.04 kg of liquid need to be pumped for every fiber.
- Amount of fibers: 346.08kg/0.12kg = 2884
- 2884 x 0.04 = 115.36 liters need to be pumped.
- Since it needs to be delivered in a speed to make the muscle contract with a speed of 1.33 meters per second: I will admit, I have no idea on how much fluid flow this would require, but I used the Hydraulic Cylinder calculator, added a bore of 20mm and a stroke of 130mm at 20 bar, and it said that the total volume would be 0.04 liters, and in order to achieve 1.33 m/s, it said it would need 25.0699 liters per minute.
- I also tried to take a Speed Calculator, inputing the speed and the distance, it gave me 0.015038 seconds, so I would need to supply 0.04 liters at 0.015038 seconds, which in one minute would be:
- 60 seconds / 0.015038 = 3989.89227291 x 0.04 = 159.595690916 liters per minute?
- 25.0699 LPM x 2884 fibers = 72,301.5916 LPM
- 36,150.7958 LPM if half of the muscles filled by the filler
- 18,075.3979 LPM if half of all muscles are actuated.
- If we assume that the 160 LPM is true, then it should be: 115,360 LPM (divided 2 times)
The 50mm muscle - 2 times stronger than the previous muscle - Safety factor of 2: 715.8kg
- Actuated weight: 0.79kg
- Unactuated weight: 0.53kg
- 0.79 - 0.53 = 0.26kg or liters if water
- Amount of fibers: 912 fibers
- 912 x 0.26 = 237.12kg or liters
- Hydraulic Cylinder calculator said it is: 156.6869 liters per minute for a volume of 26 liters.
- 60 seconds / 0.015038 = 3989.89227291 x 0.26 = 1037.37199096 LPM.
- 912 x 156.6869 = 142,898.4528 LPM
- 71,449.2264 LPM if half of the muscles are filled by the filler
- 35,724.6132 LPM if half of all muscles are actuated.
- If we assumed that the 1037 is true, then it should be 236,436 LPM (divided 2 times)
The 100mm muscle - 1.2 times stronger than the previous muscle - Safety factor of 2: 419.76kg
- Actuated weight: 4.77kg
- Unactuated weight:
- 4.77 - 2.35 = 2.42kg
- Amount of fibers: 44 fibers
- 44 x 2.42 = 106.48kg or liters
- Hydraulic Cylinder calculator said it is: 156.6869 LPM for a volume of 2.42 liters.
- 60 seconds / 0.015038 = 3989.89227291 x 2.42 = 9655 LPM
- 44 x 156.6869 = 6,894.2236 LPM
- 3,447.1118 LPM if half of the muscles are filled by the filler
- 1,723.5559 LPM if half of all muscles are actuated.
- If we assumed that the 96554 is true, then it should be 106,210 LPM (divided 2 times).
Well, well, well... Isn't physics a pain in the butt some times?
If I take a hydraulic pump that produces around 7 LPM with 1750 RPM and 5 Nm of torque at 1.25 horsepower, I would need:
- 115360 LPM / 7 LPM = 16480
- 1.25 x 16480 = 20,600 horsepower.
- 236436 LPM / 7 LPM = 33776.5714286
- 1.25 x 33776.5714286 = 42,221 horsepower.
- 106210 LPM / 7 LPM = 18966.0714286
- 1.25 x 18966.0714286 = 18,966 horsepower.
Of course, this is using the exponential growth and a random value that I took, but if you divide it by the number of safety factors, since it would mean the number of times the pressure inside the muscles are divided, it would get a little better, but not great...
I would really love to know how I could reduce the amount of horsepower... I mean, did I really do the calculations correctly?

Dielectric Elastomers:
Although I already calculated the hydraulic McKibben artificial muscles, screw actuators, hydraulic cylinders, linear motors and all of that stuff, I'm actually very interested on Dielectric Elastomer Actuators.
Not because they are "cool" or anything like that, but because they would eliminate the need for a Hydraulic Pump and an Electric Motor to drive the pump. Both have their own complications to deal with and I'm really concerned on how in the hell I would make a BLDC motor capable of outputing 300 kilowatts and the ESC required to move it.
Not to mention that in the case of dielectric elastomers, I wouldn't need to worry about the weight of the hydraulic fluid, neither about tubing, solenoid valves and all of that stuff.
Yes, I would still need to figure out some problems, like motion control, electrical insulation and converting the electrical output of the fuel cells to 5 kilovolts and the like.
With that in mind, the electrostatic actuators would clearly be better suited for that, but I do wonder if it is possible to simplify its construction...
I also doubt my idea of reppeling fibers would work, so I do think I should just compromise and use a dielectric elastomer like this:

As you can guess, this is a reversely actuated dielectric elastomer, sinze the inner electrode out get attracted to the outer electrode, increasing its length.
Although, I do wonder if it would be possible to mix this one with the below dielectric elastomer:
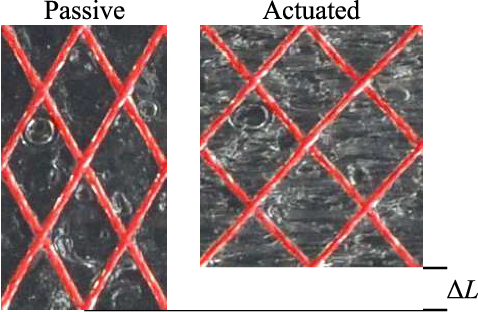
This one has a braided sleeve just like a McKibben muscle, and it contracts just like one, but I doubt I would be able to print a continuous fiber like the previous example.
In either way, I need to figure out how much force dielectric elastomer fibers would output, and then I would need to figure out how much force they would also be able to output if they were braided like a rope.
From the GPT chats capable of search the web for actual sources, it seems that braiding/twisting ropes can increase the strength of said rope from 3 to maximum 7 times.
Obviously I will take the conservative approach of 3 times. and add a safety factor.
Anyway, actually trying to figure out how much force they would output and how much they would weight.
Accordingly to the article of the braided dielectric elastomer above, it weights 0.219 grams and was able to lift 200 grams.
Unfortunately I'm kinda confused about the contraction ratio, it keeps changing the number on "tensile strain", one time it says it is 14.7%, other says it is 2% depending on the testing conditions. Unfortunately, it doesn't tell the exact dimensions of the samples.
So, taking into consideration the probable size of milimeters of the Dielectric Elastomer in the images, I would assuming it is a few millimeter squares.
By the way, the article says it uses VHB 4910 elastomer tape and 5 to 7 Kilovolts, such as in the image below:
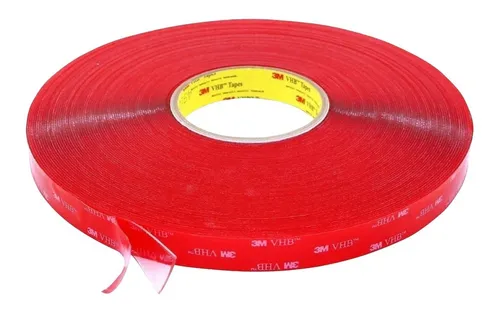
So, let's say it is 10 by 10mm and that its length is 300mm (30cm) or even larger since it will be braided/twisted, but let's take this length and then multiply a few times just to be sure.
- 0.200 grams x 30 = 6 grams = 200 grams of pulling force, I doubt it increases with length.
- 9000kg of pulling force / 1 fiber with 200 grams of pulling force = 45000 fibers x 6 grams = 270 kilograms.
- 270 x 30 actuators in total = 8100kg
- Even if you use only 3000kg/200 grams it gets 90kg per actuator.
My face thinking the dielectric elastomer would be lightest actuator of them all:

I did find this acrylate based dielectric elastomer that was capable of lifting 8kg while only weighting 0.15 grams, this would be more than 50,000 times its own weight.
Unfortunately, like all good things in life, I don't have access to it, not even through Sci-hub.
And I don't know if this performance is intrensically related to the Acrylic itself or the use of SWCNT (single walled carbon nanotubes) in the electrodes.
And yes, I keep asking ChatGPT and searching google scholar myself for high performance dieletric elastomers, but for some god-forsaken-reason they never show me what I'm looking for.
Well, I literally looked around all day and I doubt I would be able to replicate the materials, since these high performance dielectric elastomers are normally made of super mega specific chemicals that would probably summon a demon if you spoke their names out loud.
I really don't know how to proceed with this project.
Did I take the weight of the actuators incorrectly? I didn't research enough for alternatives? Maybe the strength I'm requiring for the actuators is just too much?
What should I do...?
-
Pneumatic McKibben
And yes, I'm still trying to find ways of increasing efficiency of pneumatic actuators.
One example is this one, it is said to be 31.2% stronger and 25.6% faster than conventional pneumatic muscles.
Accordingly to chat GPT, if we take the percentages, it would be something around:
- 30% = 0.30
- 22% = 0.22
- 31.2% increase = 1.312
- 25.6% increase = 1.256
- 0.30*1.312*1.256 = 0.4943616 = 49.4>#/li###
- 0.22*1.312*1.256 = 0.36253184 = 36.2>#/li###
Since the article doesn't talk about initial efficiency, we can only extrapolate like this.
This other article says it was capable of reducing the losses in 70%, but I'm unsure of what kind of losses...
By the way, one interesting thing I think about Pneumatic actuators is that it doesn't matter much the pressure you work with, it is still the same amount of liters, because gases are compressible.
So, it would be a waste of energy to attempt compressing the gases to 15 MPa, the lower the pressure, the more efficient the whole system would be.
Supposedly...
But this still makes me wonder: if the majority of the losses in pneumatic systems is due to the work being converted into heat, then why not just heat the gas?
Gases increase in pressure inside a chamber proportionally to its temperature after all...
Like adiabatic-pneumatics or isothermal-pneumatics, where heat is either not exchanged or at least constant.
I found this article that uses a reversible fuel cell membrane to convert water into hydrogen and oxygen, making a unthetered pneumatic muscle.
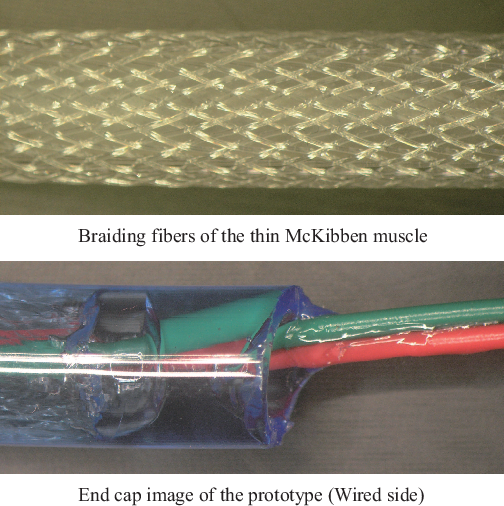
It is not hard to make a reversible proton exchange membrane, but it would be hard to make in this such high amounts...
... Or I could "just" use a central reversible fuel cell in one point like a pump and suplement the muscles in the mech...
One interesting thing is that I could re-use the oxygen and hydrogen in the fuel cell to recycle some of the wasted energy. Like a turbocompressor of some sorts.
Well, guess what? It would need a really small amount of water:
1 liter of water produces 1235 liters of hydrogen and 622 liters of oxygen.
Maybe in the end this is the solution for the mech?
Well, a reversible fuel cell/regenerative fuel cell is kinda hard to make, a simple hydrogen generator is easy, you can always just burn both for water again.
Although, I kinda wanted a regenerative fuel cell so I could react the hydrogen and oxygen after they're used so I could recycle some of the energy...
Wait, I could just build a hydrogen generator and a conventional fuel cell separately...
No, really, I'm serious, should I even attempt this one? This REALLY looks promising, simple, light and cheap to do.
My concerns are:
- Hydrogen is known to be so light it can actually pass through solid materials, although many carbon fiber tanks for hydrogen have a polyethylene layer separating the fibers from the hydrogen.
- If there is any leak at all (which will have, it is a pneumatic system), the lesser the gases to compress.
- Hydrogen is combustable, and even worse than that: it has an invisible flame to the human eye. Should I only work with the oxygen instead?
- There is also the issue of position control, pneumatics need precise control of antagonistic actautors, and on top of that, I don't know how much is difficult to make reliable progressive pneumatic valves.
- Would the low efficiency of pneumatic muscles still be a problem?
I normally use the festo air arm as a reference, but that is already 13 years old.

While nowadays, James Bruton's video showed that you can, in fact make simple precision control of pneumatic actuators using arduino.
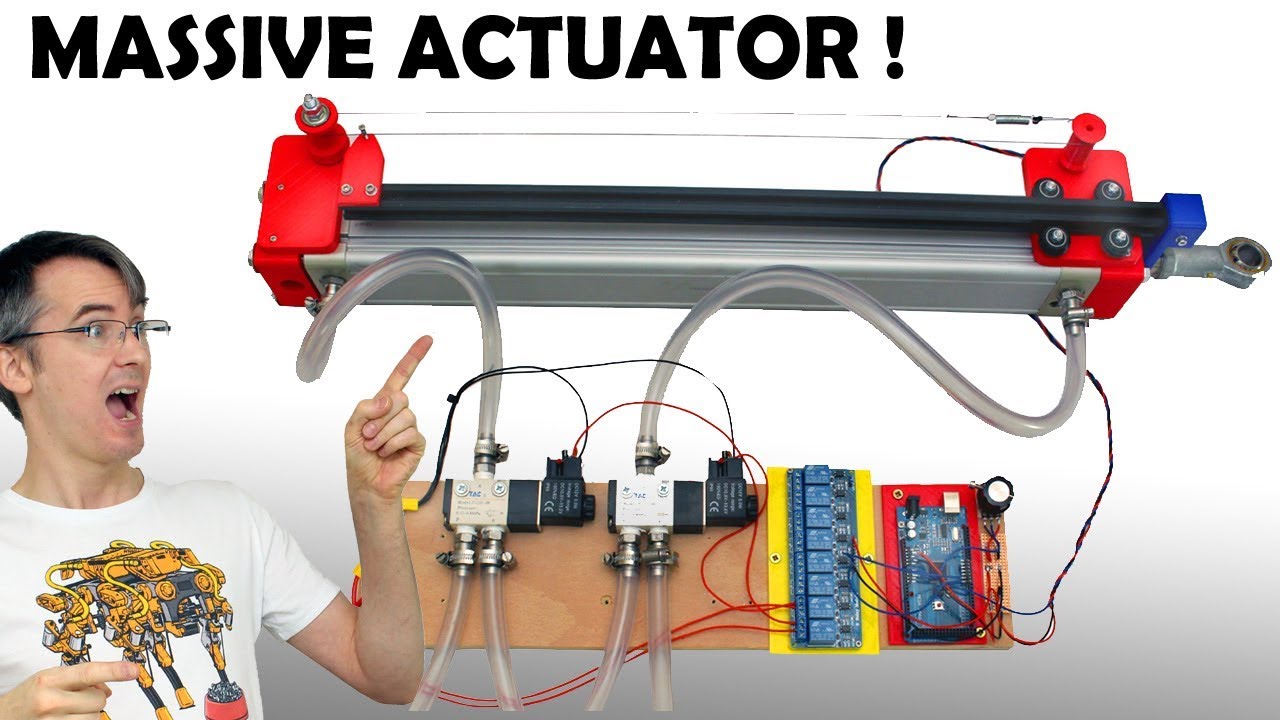
I also found this video, and its tittle made me know that there are in fact, mechanical breaks that could allow for reliable position control for pneumatics.
(unfortunately, for the life of me, I couldn't find a single image or video showing a pneumatic actuator with a mechanical brake)
There are also articles about position control using simple solenoid valves and mechanical brakes.
Screw actuator:
Before we start, I will need to calculate not only the size and weight of the thing (again), but also because I misunderstood something about volume and tensile strength.
You see, I saw once that Aluminium piston rods are 2 times bigger than steel ones, but they have the same tensilse strength, but 20% to 30% lighter.
So, my monkey brain went "this means that making it out of plastic would be even lighter!11!", which is absolutely stupid.
You just take the tensile strength of steel (200,000 PSI) and divide by the tensile strength of the material you want to use, then you multiply the result by the volume of said material and insert the density to find the weight.
For example:
- 1 m³ of steel = 7,850 kg
- Tensile strength of steel = 200,000 PSI or 1378 MPa
- Tensile strength of Aluminium = 95,000 PSI or 655 MPa
- 200,000/95,000 = 2.10526315789
- 1 m³ of aluminium x 2.10526315789
- 2.1052631578 m³ of aluminium = 5,705 kg
Now let's see HDPE graphene composite:
- Tensile strength of steel = 200,000 PSI
- Tensilte strength of Composite HDPE with graphene = 5801.51 PSI or 40 MPa
- 200,000/5801.51 = 34.4737835495
- 1 m³ of HDPE x 34.4737835495
- 34.4737835495 m³ of HDPE = 33,440 kg
As you can see, for every part made out of HDPE would literally weight 4.25 times more than any piece made out of steel (and yes, I know that a composite of HDPE graphene would have a different density, but that would probably make it maximum 20% to 10% lighter).
So I need to take a material that has a really good tensile/compressive strength, the first thing that comes to mind is carbon fiber, but that is just too expensive.
I also thought on aluminium matrix with iron or steel cables and silicon carbide for extra strength, or even using HDPE matrix in the place of aluminium.
Also, just now I remembered about an all PE based composite that could achieve around 1 GPa of strength. Maybe I could reach the same amount of strength by using HDPE.
Source: https://www.ncbi.nlm.nih.gov/pmc/articles/PMC7435843/
I found another which uses HDPE too:
Source: https://www.sciencedirect.com/science/article/abs/pii/S0032386118301514
The problem is that both UHMWPE and PE wax are expensive and harder to find.
(I said that and I immediately found a link for PE wax in my country costing 169 reais or 32 dollars the kilogram)
I also remembered about that DIY plastic that uses talc powder and PVA glue, I always assumed it to be weak or just acceptable, but I just saw some papers and they were capable of reaching tensile strengths close to 50 MPa of tensile strength.
Source: https://www.researchgate.net/publication/304572845_Structure_and_properties_of_highly_filled_poly_vinyl_alcoholtalc_composites_prepared_through_thermal_processing_effects_of_talc_size
(it is available on Sci-hub)
But this does makes me wonder:
PVA + Talc composite are obscenely cheap to buy and simple to make, but it is also has the problem of being soluable on water.
It would be like making a mech made out of paperboard, even if it was able to lift tons of weight, what is the point if it is going to melt in the rain?
This one uses polyvinyl alcohol with polyacrylic acid reached 50 MPa of tensile strength, maybe it would be less soluable in water.
This one is on PLA (also on Sci-hub), but they "only" got to around 50-60 MPa.
Well, first I will try to calculate the weight/volume of the all PE composites if they were to replace Steel:
- 1 m³ of steel = 7,850 kg
- Tensile strength of steel = 200,000 PSI or 1378 MPa
- Tensile sterngth of UHMWPE+PE wax composite = 1320 MPa or 191,449.8 PSI
- 200,000/191,449.8 = 1.04466027126
- 1 m³ of UHMWPE x 1.04466027126 = 1,013.3 kg
Almost 8 times less heavy than Steel while having the same volume, sweet.
However, there is always something, and this is that:
- The articles don't specify if it is yield or ultimate tensile strength.
- The articles also say it has increased elasticity/elongation of around 7.35%.
Both of these things may considerably change how much this thing would weight and how it should be shaped.
Accordingly to ChatGPT:
"However, for many engineering materials, the ultimate tensile strength is often found to be about 1.5 to 2.0 times higher than the yield strength12. This means that the yield strength is about 50% to 67% of the ultimate tensile strength."
Well, then it is actually 2,026.6 kg.
Although this is the equation that I was thinking of using, I'm kinda concerned when it comes to the screw actuator. The articial muscles would be "easier" to fix, because they are cylindrical pieces of cloth, not solid pieces of material.
It could mean that in the end I would need to make 6 different types of screw actuators with widly different sizes of motors.
I could simply use the final screw and just add it to everything, but... The motors would still be a problem.
Well, first, I need to find a 3 ton rated screw actuator/lifter and then take its dimensions.
(I'm having no success)
I also tried to ask ChatGPT and other gpts with access to internet to take the general value that screw actuators normally use for the dimensions and outputs in order to make a conservative approach based on the generalistic data.
Then they reach the conclusion of 2+2=22 around 40 times.
Me: "I need you to figure out the pitch of the screw based on the torque, which is 45 Nm"
GPT: "Why, yes, thank you, the diameter is 12mm and the torque is 2389 kilonewtons per meter"
Me: "That wasn't what I asked, please, redo the calculation."
GPT: "Why, yes, thank you, the diameter is 12mm and the torque is 2389 kilonewtons per meter"
Me: "That wasn't what I asked, please, redo the calculation."
GPT: "you reached your limit of allowable questions for the day, pay for the premium for more."
It is kinda pathetic how people wasted billions of dollars just to make an AI that can't even make f*cking math, how is that even possible since the AI are literally made out of MATH!?
Well, at least let me check about the hydraulic cylinders, right?
They have more of less the same structure (without the threads and the like), so I could at least use it as a starting point...?
In any manner:
3 times extra strength for every consecutive actuator:
- Biceps/Arm = 3 tons
- Shoulders: 3 ton x 3 Extra force = 9 tons
- Torso: 9 tons x 3 extra force = 27 tons
- Legs: 27 tons x 3 extra force = 81 tons
Now that I separated every consecutive actuator, I think I see the issue... I did say that this leads to exponentional growth, which is absolutely insane...
2 times extra strength for every consecutive actuator:
- Biceps/Arm = 3 tons
- Shoulders: 3 ton x 2 Extra force = 6 tons
- Torso: 6 tons x 2 extra force = 18 tons
- Legs: 18 tons x 2 extra force = 36 tons
Well, I could only find a 30 ton hydraulic cylinder, and it is CHONKY.
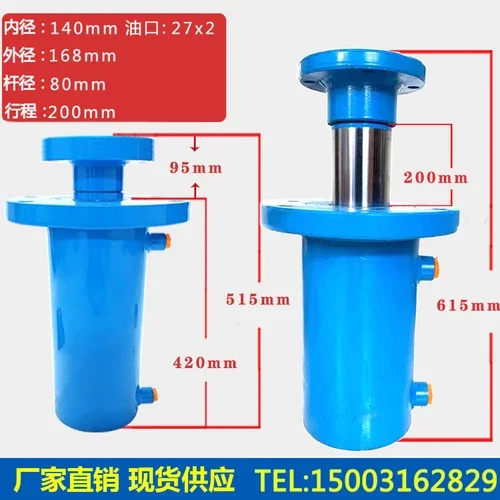
I don't understand Mandarin (or Cantonese), so I don't know exactly which is the diameter of the rod and the diameter of the bore.
(Forget it, I found another link were it is in english)
It has 80mm of rod diameter and 140mm of bore (inner diameter) and a outer diameter of 168mm.
It is meant to work maximum 300 meters per second (somehow) and maximum 30 MPa of pressure, which reaches the 40 ton mark, at 30 MPa its pulling side reached 30 tons.
And since the rod will be sticking out in both sides, then it would be 30 tons for both sides.
It would need 827.3070 Liters per minute of fluid flow, and I'm supposed to ad 6 of these for each leg.
I won't even waste my time calculating this one, lol.
At least I now know how THICCC the screw actuator would need to be.
1.5 times extra strength for every consecutive actuator:
Now this one, the 10 ton hydraullic cylinder has 63mm of rod diameter, 100mm of bore diameter and 110mm of outer diameter.

It has maximum 7 ton of pulling force, so you know the drill, I will make the inner diameter a little bigger for the sake of reaching 10 ton. 110mm of inner diameter in this case.
It would also need 509.6085 liters per minute of fluid flow, or 3000 liters of fluid flow in total counting the stewart platform.
I can't go around making 4 different cylinders for each output force, so let's see how much fluid flow each would need:
- Biceps/Arm: 3 tons = 500 LPM but with a pressure limiter for 5 MPa
- Shoulders: 3 ton x 1.5 Extra force = 4.5 tons = 500 LPM pressure limiter at 7 MPa x 6 = 3000 LPM
- Torso: 4.5 tons x 1.5 extra force = 6.75 tons = 500 LPM pressure limiter at 10 MPa x 6 = 3000 LPM
- Legs: 6.75 tons x 1.5 extra force = 10.125 tons 500 LPM with no pressure limiter also 3000 LPM
- To supply one side of the mech at full speed: 9500 LPM.
- I would "only" need 90 hydraulic pumps with 100 LPM of output flow.
- Which would need around 585 horsepower in total.
- Not great, not terrible.
The 10 ton hydraulic cylinder weights around 15kg by the way, so 1+6+6+6 = 19 x 2 sidez = 38x15 = 570kg in total for the hydraulic cylinders alone.
1.5 times extra strength for every consecutive actuator:
Now calculating with the proper hydraulic cylinder sizing:
3 ton hydraulic cylinder: 50mm of inner diameter, 28mm of rod, 300mm of stroke, 16 MPa = 107 LPM.
5 ton hydraulic cylinder: 63mm, 35mm, 300mm, 16 MPa = 170 LPM.
6 ton hydraulic cylinder: (I couldn't find one, so I will use the force of a 8 ton) 80mm bore, 50mm rod, 300mm stroke, 16 MPa = 245 LPM.
10 ton hydraulic cylinder: 100mm of bore diameter, 63mm of rod diameter, 300mm of stroke 16 MPa = 500 LPM.
- Biceps/Arm: 3 tons = 107 LPM
- Shoulders: 3 ton x 1.5 Extra force = 4.5 tons = 170 LPM x 6 = 1020 LPM.
- Torso: 4.5 tons x 1.5 extra force = 6.75 tons = 245 LPM x 6 = 1470 LPM
- Legs: 6.75 tons x 1.5 extra force = 10.125 tons 500 LPM x 6 = 3000 LPM
- To supply one side at full speed: 5597 LPM
- I would "only" need 55 hydraulic pumps.
- Which would need around 357.5 horsepower in total.
1.2 times extra strength for every consecutive actuator:
- Biceps/Arm: 3 tons = 107 LPM
- Shoulders: 3 ton x 1.2 Extra force = 3.6 tons = 107 LPM x 6 = 1020 LPM.
- Torso: 3.6 tons x 1.2 extra force = 4.32 tons = 245 LPM x 6 = 1470 LPM
- Legs: 4.32 tons x 1.2 extra force = 5.18 tons = 245 LPM x 6 = 1470 LPM
- To supply one side at full speed = 4067 LPM
- Which would need around 260 Horsepower in total.
In any manner, this would show how much the screw actuator would also weight and how much energy it would need.
Although, it would be 7 times lighter if made with the all PE composite + graphene.
Tomorrow I will try to make a 3D model of the screw actuator with the dimensions into consideration.
Well, guess what? The scroll in my mouse stopped working, now I need to wait until the new one arrives at my house.
Dang it, the project log is already reaching maximum limit of characters.
But before I create a new one to post the screw actuator design: to calculate the linear speed and force into horsepower, and it seems like in order to lift 3000kg at a linear speed of 1.33 meters per second, I would need around 1000 watts (1.33 horsepower) accordingly to chatGPT, which is probably wrong...
So maybe I misscalculated some things on the previous actuators?
Nope, it is 81 kilowatts for 1000kg of force, ChatGPT was indeed incorret.
Also, this would make it simpler for the screw actuators or even for hoist actuators.
Out of curiosity, energy consumption with the extra force:
- 81 + ((81x3)x6) + ((81x3x3)x6) + ((81x3x3x3)x6) = 19,035 kilowatts = 25,380 horsepower.
- 81 + ((81x2)x6) + ((81x2x2)x6) + ((81x2x2x2)x6) = 6,885 kilowatts = 9180 horsepower.
- 81 + ((81x1.5)x6) + ((81x1.5x1.5)x6) + ((81x1.5x1.5x1.5)x6) = 3,543.75 kilowatts = 4725 horsepower.
- 81 + (81x1.2)x6) + ((81x1.2x1.2)x6) + ((81x1.2x1.2x1.2)x6) = 2203.848 kilowatts = 2938.464 horsepower.
Well, I definitely misscalculated something in the hydraulic cylinders, because it should be way above the values I got.
Off-topic:
One thing I forgot to talk about more in depth was the plasma jet engines.
Although I talked about them more like a conventional turbine engine, with compressor, combustor and turbine parts, you could also use them as a Tip-jet rotor.
Basically, it is a type of propulsion system in which the rotor/propeller/blades are hollow and air is injected into them, the centrifugal forces compresses the air further and at the tips of the rotor there is the combustion chamber that generates thrust.

The thing is: since it is a type of propulsion system that doesn't need a combustion chamber and a turbine to work the same way as a conventional turbine engine, you could, maybe, use it in a plastic plasma jet engine, only using the ceramic/metal parts at the tips.
Like this one.

Source: https://www.sciencedirect.com/science/article/pii/S1000936119302213
Maybe this could be useful to replace the 300+ kilowatt electric brushless motor, or it could even be used for a pneumatic McKibben muscle.
Adiabatic Combustion Engine:
SPEAKING of adiabatics...
There are a type of engine called "adiabatic engine", it is said to have around 50% to 60% of fuel efficiency.
Source: https://www.sae.org/publications/technical-papers/content/830314/
You "just" need to make all of the components out of insulating ceramics and then run it super mega hot so the energy loss to heat is minimal.

It can also be done by doing a very high compression very fast, when I was searching for the most efficient combustion engines in the planet, ship engines were always the first to appear, and those had meter long compression. But I don't know how I would avoid fuel detonation with an engine at 1200ºC
Discussions
Become a Hackaday.io Member
Create an account to leave a comment. Already have an account? Log In.
Festo recently made a video about a "bio-hydrogen" battery that uses a special bacteria culture that converts hydrogen to and from a liquid that is easier to store: https://youtu.be/2Y_bqzlobw8?si=D6990lcVTBX_1T01&t=49
Are you sure? yes | no
Looking at the weight and quantity of hydraulic oil, and the pump... yikes, that's a lot of weight and energy needed to move that around for hydraulic muscles, sounds expensive too.
Have you considered Hydrogen Peroxide steam generators for pneumatics? consider this
https://www.youtube.com/watch?v=VesprTcNIdo
https://www.youtube.com/watch?v=A1H2mFEsbNk
Obviously these are open generators and not constrained to tanks, not that they have to though, maybe a design similar to a tube boiler or flash boiler could suffice to generate the pressure needed to move the muscles. (but instead of "boiling" it passes the peroxide through the catalyst)
These steam generators work with 12% (or more) peroxide, which is household grade, the catalyst might be more difficult but it is not consumed in the reaction. and of course you do not need any pump/engine to generate this pressure, perhaps a small one to pump the peroxide in and a couple of valves.
Of course, i am unsure if this could meet your demand of lifting 1 ton, but it's an idea :^)
Are you sure? yes | no
That is a cool idea actually, the only problem is that I would need a very big steam tank to store all the pressurized steam.
But I saw one article where they use a reversible fuel cell to separate water into hydrogen and oxygen gas on demand.
https://www.semanticscholar.org/paper/Soft-Polymer-Electrolyte-Fuel-Cell-Tube-Realizing-Nabae-Kodaira/e23633c26983e613c647139e917760feb9b52bb6
In the article they use a fuel cell for every muscle, but you could have a central fuel cell for that.
Are you sure? yes | no
The 7MPA muscle paper is available here: https://www.fujipress.jp/ijat/au/ijate000600040482/
Are you sure? yes | no
THank you <3
Are you sure? yes | no