The project log 87 got so long that I had to split it into project log 88 and 89, sorry for that, lol.
Manufacturing The Mech parts:
I still need to make the 3D model, calculate weight and all that stuff, but I just want to get this out of the way first.
Obviously, I will run into more details when I actually start building, linking all the proper tutorials that I followed, precise steps that I took and the like (yes, on the details I say this is more of a guide, but being frank, this way I will be forced to actually organize my stuff, lol).
For the Coils of stator, bearings and couplings:
- Find a soda can for aluminum scrap.
- Triturate all of it, take out the paint, clean it up as much as possible.
- Take the proper weight of aluminum welding rods 4043 and 2024, fluxes etc.
- Make the microwave kiln with sodium silicate and silicon carbide.
- Use the same materials to make an aluminum wire extruder (first I thought of doing that idea of pouring paraffin wax in sand for a wire mold, but that would take too long.
- Purify the aluminum scrap as much as possible, taking out dirt, humidity and the like (I don’t want an aluminum steam explosion in my face).
- Buy all the safety equipment for forging aluminum (I want to DIY everything, but molten metal is risky).
- Make a pile of dirt sacks around the kiln and the extruder for extra safety.
- Heat both the kiln and the extruder so there isn’t a thermal shock explosion.
- Make the process of manufacturing aluminum wire at a safe distance.
- Then use a cheap Carbide Wire DrawPlate to smooth out any imperfections on the surface.
- Anodize the aluminum wire for insulation, just like enameled wire, it will serve for protection and avoid short-circuits.
- Make the aluminum coils into the desired shapes using 3D printed molds and the like.
- Heat treats the aluminum coils in an artificial aging process for hours or days.
- Infuse the coils with a mixture of polymer (such as HDPE) composite with thermal paste for heat dissipation (DIY or not) and a thermochromic paint (DIY or not if possible) in order to make the visualization of heat easier.
- You can add a ferrite polymer composite core or not to the center of these coils for a slightly better magnet field.
- Position the wired coils into the stator’s molds, connect them with the 3 phase correctly (check and recheck multiple times, any mistakes will be hard to correct) and inject the mold with structural polymer for stator completion.
- Then I would use good insulating materials around the motor housing to avoid frost build up.
- That also applies to bearings, couplings, servos etc.
I was thinking of making the mold using glass panels, they are made with incredible tolerances (in the micrometer range) and thus, the rotors would also have those tolerances if made with the same surface.
The space between the coils, magnets and the like would be dependent on the precision of the mold, which on another hand, would be limited by the method of fabrication.
I was thinking of using resin 3D printing (in this case, hire a 3D printing business for this specific case).
But in hindsight, I feel that it would be unnecessarily troublesome, I could do it with laser printed plastic schematics with measurements glued to a glass and align the parts with it.
I was even thinking of using an DIY light/shadow projector, the bigger the projected shadow/light, the higher the precision. But you would need a lot of space for that.
For the permanent magnet rotors:
- Find and/or buy Alnico/Neodymium magnet powder or turn Alnico/Neodymium magnets into powder. Do that in some oil because neodymium is highly reactive with oxygen.
- Mix it with a 95% magnet powder to 5% polymer composite, just like the coils, the polymer, thermal paste and thermochromic paint. Some magnets can survive from up to hundreds of degrees celsius, but not the plastic.
- Do that under a strong magnetic field, so the particles will align properly during injection and curing.
- Use a magnetizer to turn these magnets into permanent magnets.
- Position the magnets into the rotor's molds (check and recheck multiple times, any mistakes will be hard to correct) and inject the mold with structural polymer for rotor completion.
- Then I would use good insulating materials around the motor housing to avoid frost build up.
- That also applies to bearings, couplings, servos etc.
A halbach array is an interesting manner of increasing the magnetic field strength of a permanent magnet rotor and the like, even with the possibility of building personalized magnets, I don’t think it is worth the trouble.
For the Assembly:
I still didn’t 3D model it, but I was thinking of separating the motor and the hydraulic pump in two separated chambers, and both would be coupled together with an electromagnetic clutch.
There are many types of electromagnetic clutches out there, but, depending on how easier it is to calculate, predict and build, I would use eddy current clutches and/or bearings. The rotor would have an induction coil for wireless power transmission to power its electromagnets for its contactless electromagnetic bearings and clutches mechanisms, then the pump would have either an aluminum plate for the eddy current formation or an DC current electromagnet with a full bridge rectifier to follow the electric motor.
Either way, both would be floating in their respective chambers, the electric motor being cooled by its -70ºC coolant and the pump cooled by the water it is pumping.
For a clutch or a bearing to work, they need a power that can resist the forces they are receiving, which would be really powerful. 10 pieces of 1000 volts 20 amps cost 50 reais (10 dollars), so depending on the importance of the piece in question, I could make an AC to DC conversion using a full-bridge rectifier for the system.
For the Cooling System:
Well, it ends up that I won’t need to cool down aluminum wires to -70ºC as explained in the 3D modeling section.
Observation: Although the system doesn’t use flammable products, it is still extremely dangerous to touch a liquid at -70ºC (imagine being splashed by it).
This, of course, is just to make Aluminum as conductive/resistive as copper while being as light a possible. If -70ºC is too much (and I do believe it is too much), you should increase the size/weight by 1.54 times in order to compensate for the resistivity at ambient temperature.
When I actually 3D model everything and calculate its weight, I will decide whether or not I should mix the aluminum coils with copper and use a conventional freezer cooler (-17ºC).
Just like I linked before, I would use the pulse tube cryocooler system built by Hyperspace Pirate’s channel.
However, since I don’t have access to the same copper tubing he uses (because it is expensive and a little hard to mess with), I will be using the equivalent sizing and tubing made using plastic parts mixed with thermal paste for heat exchange, either for cooling or dispersing heat.
I would actually attempt to make a radial piston system also driven by the motor and/or hydraulic pump, either with an electromagnetic or physical clutch/coupling.
This time, however, I wouldn’t care much about maximum efficiency, as long as it performs really well, I don’t care that much.
If there is more than one electric motor chamber, the coolant will be pumped through insulated hoses around the body of the mech.
The heat exchanger would be an hybrid of liquid cooled that would be pumped through a radiator with a pump integrated on the electric motor itself and a section for stacked peltier cooling. The peltier plates would be only used during highly demanding moments for super fast cooling at the cost of efficiency, in fact, you can cool things to about -40ºC to -50ºC using stacked peltier plates in a very compact and light manner.
But that can change if I ever find a better way of getting rid of the heat generated by the system in a way that is faster, like having a bigger mass of coolant.
The cooling system will also be used to cool down the electronic parts.
About Liquid Metal Magnetohydrodynamic Generator (LMMHDG): Not Practical, back to Molten Carbonate Fuel Cell.
Since last project, I was in doubt on how to make it an efficient and inductive system, but a good way of doing it would be to attach a flipping valve at the end of the air blower that switches between two vacuum ejectors-gas chamber hybrids.
This way the liquid would go back and forth, creating an inducting current on the coils.
One thing that concerns me is that the fuel and oxygen would eventually contaminate the molten metals since it would constantly be at 700ºC, I would need a really non-reactive metal.
Well, it seems like I either find a way of this working or I need to change back to Molten Carbonate Fuel Cells.
Because no metal would stay non-oxided with oxygen being blown into it while molten. ChatGPT suggested platinum, gold and silver however.
Other chatgpt suggestion:
“At temperatures between 400°C and 700°C, some materials, including certain molten salts and carbonates, can be conductive and molten. Here are a few examples:
Conductive Molten Carbonates:
Sodium Carbonate (Na₂CO₃):
Melting Point: ~851°C
State at 400°C to 700°C: Solid (but molten above 851°C)
Conductivity: In its molten state, sodium carbonate is ionic and conductive. However, it is not molten within the 400°C to 700°C range.
Potassium Carbonate (K₂CO₃):
Melting Point: ~891°C
State at 400°C to 700°C: Solid (but molten above 891°C)
Conductivity: Similar to sodium carbonate, it is conductive when molten but remains solid in your specified temperature range.
Lithium Carbonate (Li₂CO₃):
Melting Point: ~723°C
State at 400°C to 700°C: Close to its melting point; it may begin to melt near 700°C.
Conductivity: When molten, lithium carbonate is conductive due to its ionic nature.”
Ironic that I would rely on fricking carbonates to escape from the molten carbonate fuel cell.
It also suggested adding other materials to the molten thing in order to make it more conductive, such as Silicon Carbide, Tin Oxide and Indium Oxide.
Well, this presents another problem.
On the molten carbonate fuel cell you don’t care too much if the carbonates are actually in liquid state, you just need them to be ionically conductive.
But here, with the LMMHDG, you actually need materials to be in liquid state.
But then you would need temperatures ranging from 700ºC to 1600ºC.
When I think of a high temperature binder material, I think of sodium silicate. But it melts at 1000ºC, even binders for ceramic fibers only survive until 1200ºC.
I was thinking of even using the manufacturing technique of NASA's thermal tiles of fused silica fibers, but they can only survive until 1200ºC also.
Which binding materials could survive temperatures up to 1600ºC?
At this point isn't it better to just make a turbine engine using these insane materials?
ChatGPT suggested calcium aluminate cement and phosphate binders, I couldn’t find either to buy, but I found a tutorial on how to make a phosphate.
The maximum refractory cement I found was 1400ºC…
I did find plates that can easily reach 1600ºC or more, but the problem is that I need to make something in a customized shape and size that will contain molten metal.
You know what? Screw it, I will just add a thermometer to start cooling the whole structure at 1300ºC.
However, the more I stop talking about it, the more I think the molten carbonate fuel cell seems more attractive… I just started to wonder about using liquid metal magnetohydrodynamic generators because the molten fuel cell has a maximum efficiency of 50% and slow power spikes on demand.
I’m assuming that all of this trouble will allow the LMMHDG to achieve efficiencies over 70% or even more. All of that because of this blasted article:
https://www.mdpi.com/2071-1050/15/16/12619
But according to other sources, the maximum efficiency achieved using the carnot cycle is 60%.
Then how can the system reach 70% of efficiency?
There is the Brayton Cycle, the Rankine Cycle and the Carnot Cycle, one consecutively more efficient than the other 40% and 45%. Although the Carnot is a hypothetical thermal engine, it only calculates the maximum amount of efficiency achievable without any kind of losses.
So, since I was thinking of using something similar to a turbine engine, but using the liquid metal, it would be safe to assume that at the best possible performance, I would still only reach 40% with this system.
Even a Rankine-Brayton Combined Cycle (and other types of combined cycles) can still only reach a maximum 60% of efficiency.
That, of course, is the upper limit of thermal engines, like piston engines, gas turbine engines, steam engines etc. So these values may not apply to other types of energy generation, like hydro-electrical turbines and Fuel Cells.
Now that I think about that, since I can make a hydraulic pump/actuator 95% efficient using the diaphragm piston thingie, then why wouldn’t that work with combustion engines?
Of course, you would need a really temperature resistant material for that, but I mean… If the combustion chamber is a good insulator for a high temperature combustion chamber, the piston rod has almost no friction, it has a heat exchanger and a regenerator… That would be the closest possible engine to a Carnot Engine.
Of course, that would be a stretch, especially because the Carnot Engine is the more efficient the higher the difference between the cold and the hot part. Which you would have a hard limit to maximum 1000ºC for flexible things.
Wouldn’t that be just a Stirling Engine tho?
Since the maximum efficiency of Stirling Engines is 40%, then maybe you could surpass that limit if you had a vacuum ejector turbine engine. The combustion chamber would take both microwave, fuel and high pressure air, the combustion channel would make even more heat and thus, even more air flux, creating a vacuum. You could add electric turbines to the system, which would both rotate the compressors and the electric generators.
The incoming air would be both used on the coolers, on the heat-exchange/regenerator and as the air supply for the combustion.
I feel like I already talked about this on this project before…
It also got me wondering: would you be able to make an electromagnetic field around the turbine blades to protect against the plasma generated?
This also got me wondering:
Thermoelectric Generators (TEG) have low efficiency (<10%), but by stacking multiple layers, the heat generated by the heat source and the electrical resistivity (that would also turn into heat) would eventually be converted into electricity with enough layers, no? Wouldn’t that increase efficiency?
Edit: Accordingly to this article, kinda yes, kinda no. They only achieved 15%.
I couldn’t find any paper that explored this possibility, so I'm probably wrong. Especially if you take into consideration that the bigger the heat difference between the hot part and the cold part, the higher the efficiency/performance of the system.
If the system is completely solid, wouldn’t that mean that the difference in heat between the cold and hot parts is so minuscule that no energy would be produced?
The only way I could think that this could be somewhat “solved” would be to have as many many cooling and heat systems as possible to maintain the difference between each layer as practical as possible, even if that means diverting heat from the heat source to more distant layers in order to increase their heat difference.
Making a solid 3D system like that already makes a knot on my brain tho…
I said that, but I was thinking of it more like a “river” with two parallel “liquids” with different temperatures, the more the “rivers” flow, the more equal the temperature starts getting. When equilibrium is reached (aka both sides have the same temperature) the two “rivers” separate, what was the hot one goes back into the heat source and what was the cooler one goes to the outside for dissipating its heat. Then both “rivers” unite again until equilibrium is reached again, repeating the process.
You could literally have “rivers” doing that with liquids in insulated tubes, or you could have solid materials spiraling around the heat and cooling sources.
Or am I just thinking too much? You could get the same result with a spiral style cooling system, where the inner wall is hotter than the outer side of the wall because the heat source already distributes its heat to the cooling flow.
Kinda like Joule-Thompson cooling and/or cascade cooling, but on the reverse.
If Hyperspace Pirate is correct, then this system has 0.1% of efficiency, because this is just a reverse heat engine, just like the carnot cycle. And the most efficient type of heat engine is the Pulse Tube Cooler or Stirling Heat Engine, with an efficiency of 40%.
Huh, the carnot cycle is useful both for heating and cooling… hm
See? That is why I like to write down everything about my thought process. I learn a bunch just thinking about why certain things work or don’t work (even though they are obvious things for everyone with 2 working brain cells, not my case).
That may also explain why the idea of a vacuum ejector-turbine hybrid may not work: you can’t use the same working system to cool down systems.
… But that is even accurate, tho? Turbo Compressors are a thing, and they are part of the Carnot Cycle.
About Molten Carbonate Fuel Cells:
Embarrassingly, only now I saw the comments made by latinflavorxd on my project logs about fuel cells (damn, it took me 1 entire year to answer him, sorry for that).
He suggested using methane to reform into hydrogen gas to feed into a Solid Oxide Fuel Cell. Solid Oxide Fuel Cells are really hard to DIY and really expensive to buy, as far as I could search on the subject, of course. About the hydrogen since it is 20% hydrogen by weight, but unfortunately, reforming or using any solid hydride storage of hydrogen gas with anything below 40% of hydrogen per weight is really not viable (as far as I could actually calculate).
As I answered him, I also thought of using the hydrogen and carbon released from the Methane reforming to react in an hydrogen alkaline fuel cell and in a carbon molten carbonate fuel cell.
I would get 31 megajoules per kg of liquid methane (around 2.3 liters), and since Methane is 55 megajoules per kilogram, that would make the whole system have an efficiency of 56%.
Of course, assuming the carbon fuel cell will take the carbon released from the reforming process and the plasmatron reforming wouldn't require too much energy, which I'm not very confident that it would work.
Taking into consideration the difficulty of storing methane (in a DIY method), reforming it and consuming it, I don't think this would be much practical in a DIY system. But it could be really interesting in other scenarios.
By the way the materials used to make solid oxide fuel cells:
“The main materials used in the different components of a solid oxide fuel cell (SOFC) are:
Electrolyte: Yttria-stabilized zirconia (YSZ) is the most commonly used electrolyte material in SOFCs. It is a solid oxide material that conducts negative oxygen ions from the cathode to the anode. [1][2]
Cathode: Strontium-doped lanthanum manganite (LSM) or a composite of LSM and YSZ is typically used as the cathode material. The cathode is responsible for the reduction of oxygen into oxygen ions. [1]
Anode: Nickel-YSZ cermets (a composite of nickel and YSZ) are the most common anode material. The anode must be porous to allow fuel flow and must conduct both electrons and ions. It is also often the structural support layer. [1][2][3]
Interconnect: Metallic alloys such as chromium-based alloys or lanthanum strontium manganite (LSM) are used as the interconnect material. The interconnect provides electrical connection between the individual cells in an SOFC stack. [2]
Sealant: Glass-ceramic or glass-based materials are typically used as sealants to prevent gas leakage between the different components of the SOFC. [2]
https://www.sciencedirect.com/science/article/abs/pii/S0955221901001200
https://www.fuelcellstore.com/fuel-cell-components/sofc-materials
https://en.wikipedia.org/wiki/Solid_oxide_fuel_cell”
Off-topic:
I just want to get this thing out of my brain.
I don’t remember if I talked about this before, but essentially, if you heat copper acetate or copper formate, it turns into pure copper and liberates flammable gasses (which you can carefully burn in a chimney), formaldehyde gas (which you can neutralize with hydrogen peroxide aka oxygenated water) and a little bit of copper vapor (which you definitely need to vent through activated carbon).
These reactions can be used to make metallic copper mirrors, which are good at reflecting infrared light.
(the same goes to silver acetate)
Also, quite useless thing, but I was thinking: if you use that idea of using really powerful incandescent filament for light bulbs on the kilowatt range to make an infrared emitter “melter”, maybe you could make an energy blade of some sorts.
The idea would be to use reflective articulated tubes (like I said in the previous project log) like optical fibers and direct the output in some edge or knuckle style weapon in order to make a heat blade/power gauntlet.
Some materials are invisible in the infrared spectrum while opaque in the visible light, like potassium chloride (KCL) and sodium chloride (table salt), so that is what you could make the tip out of (but both melt around 700-800ºC). But if you mix it with sodium silicate… Maybe it would be able to last longer.
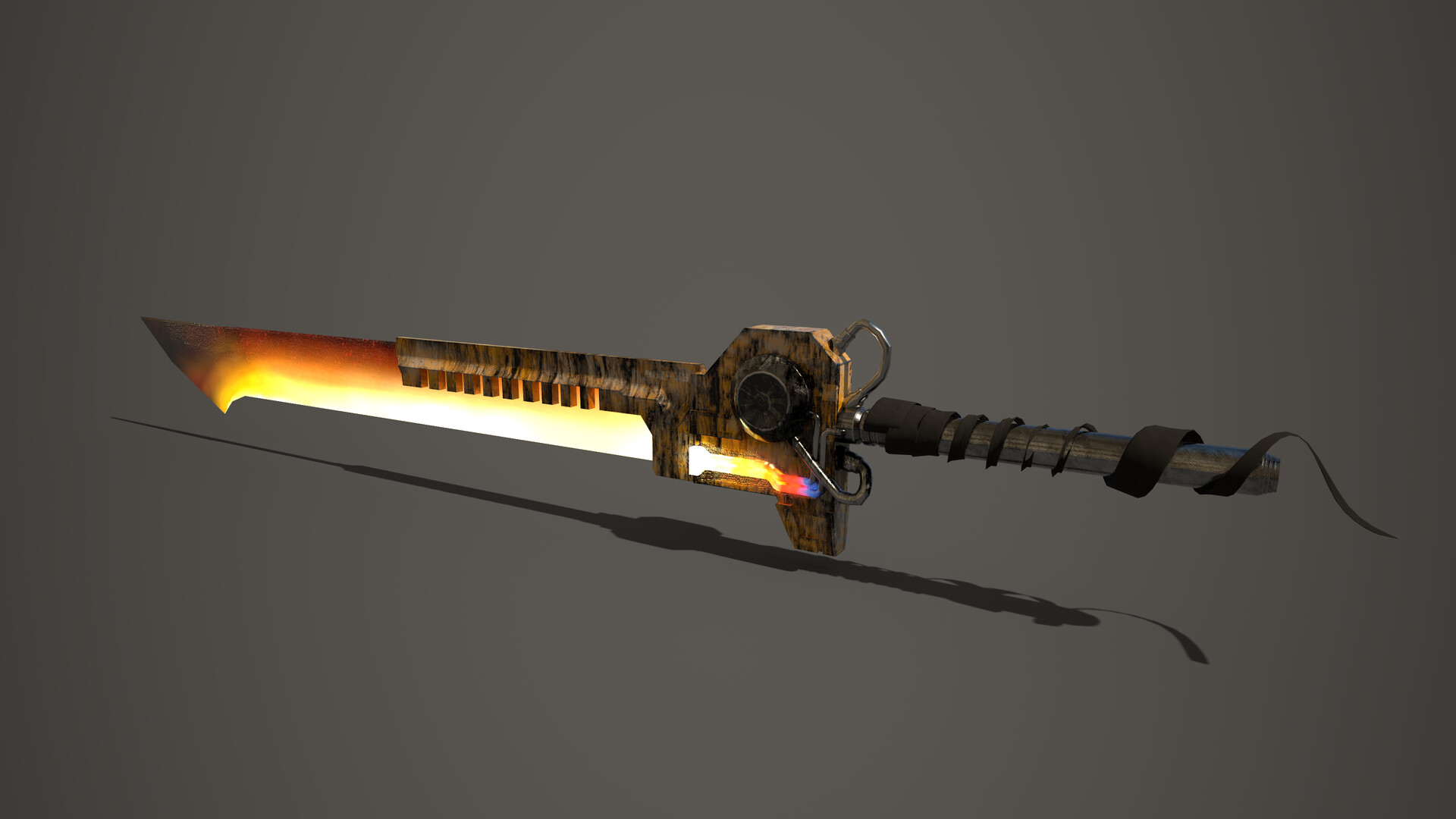

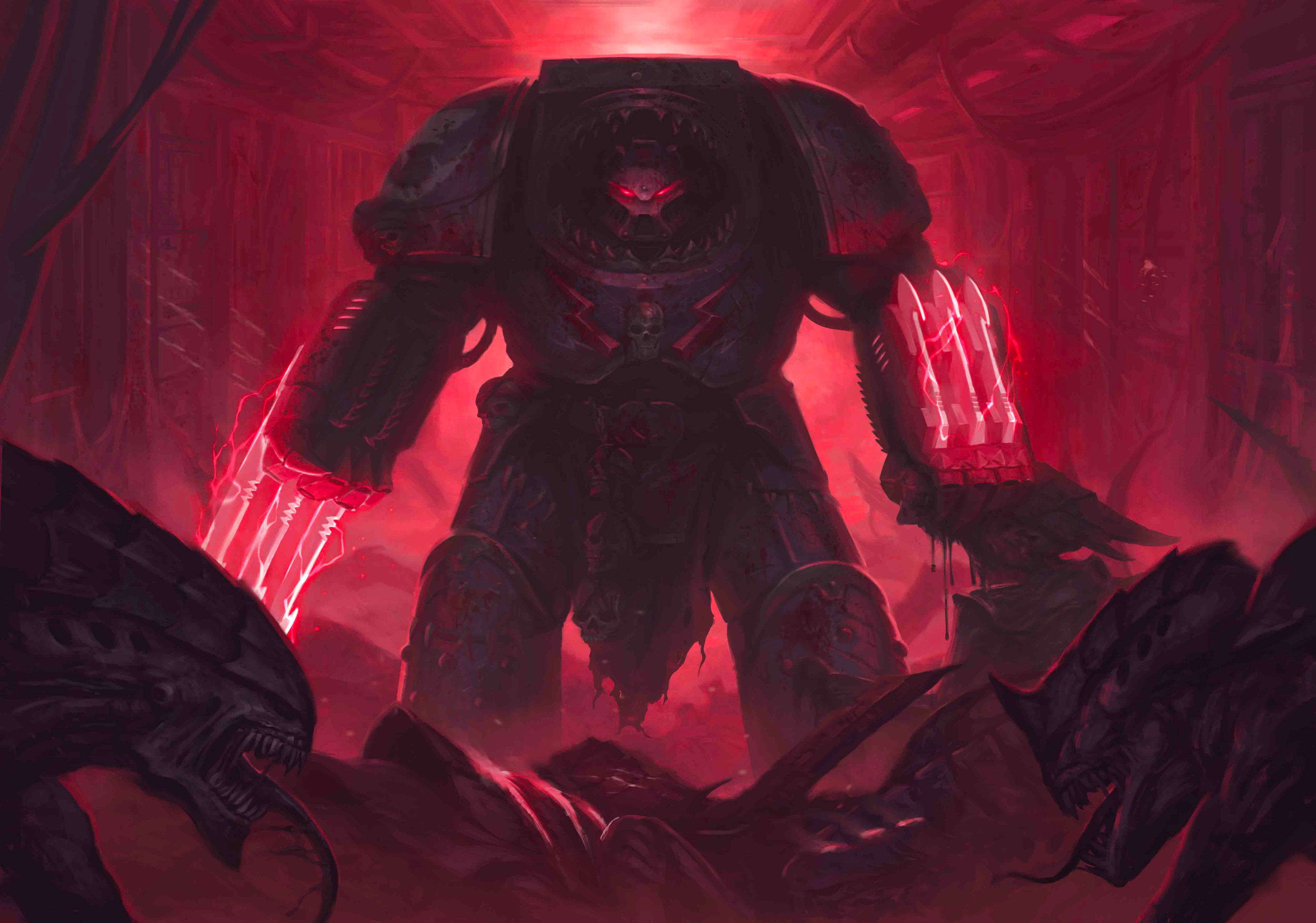
Completely useless to anything in real life, but so cool tho…
I just don’t know if you would need to make it a pulsed infrared emitter (like the laser) or a continuous infrared emitter. If you need to make it a pulsed one, you need to make the filament as thin/resistive as possible, so the pulses can have enough time to emit infrared radiation. If it is continuous, maybe you would need a really thick incandescent filament?
Oh, by the way, about the laser thruster:
I still don’t know how much energy it would require for a given amount of thrust, but maybe the Kinetic energy calculator would help?
If you accelerate, let’s say, 1000kg at the same speed of the gravity (9,807 m/s²), you would need around 50,000 joules of energy. Even though gravity is measured in acceleration, not speed.
So I guess that’s the amount of energy per second required to keep something into the air? Since the speed is measured in meters per second…?
ChatGPT agrees with me, but I’m not very confident about it anyway…
On the Wikipedia article about ablative laser propulsion it has 5000 seconds of specific impulse, then I asked GPT to calculate with this information. It said it would either need 35 megajoules or 240 megajoules.
Poe on Quora answered:
“To calculate the energy required to provide 500 lbs of thrust on an aircraft, we can use the relationship between thrust, fuel flow rate, and the energy content of the fuel.
Assuming the aircraft is using a hydrogen-oxygen rocket engine, the energy required can be calculated as follows:
Thrust (F) = 500 lbs
Specific Impulse (I_sp) for a hydrogen-oxygen rocket engine is typically around 450 seconds.
The relationship between thrust, mass flow rate (m_dot), and specific impulse is:
F = m_dot * I_sp * g_0
where g_0 is the acceleration due to gravity (9.81 m/s²)
Rearranging this equation, we can solve for the mass flow rate:
m_dot = F / (I_sp * g_0)
m_dot = 500 lbs / (450 s * 9.81 m/s²)
m_dot = 0.1136 kg/s
The energy content of hydrogen is approximately 141.8 MJ/kg.
The energy required per second to provide 500 lbs of thrust is:
Energy = m_dot * Energy content of hydrogen
Energy = 0.1136 kg/s * 141.8 MJ/kg
Energy = 16.1 MJ/s”
Therefore, it takes approximately 16.1 megajoules (MJ) of energy per second to provide 500 lbs of thrust on an aircraft using a hydrogen-oxygen rocket engine.”
If you replace the 500 lbs by 2200 lbs (1000kg) and the specific impulse with 5000 seconds it gives 6.3 MJ/s.
Of course, that is assuming the energy density of said laser is the same as liquid hydrogen (141.8), but I don’t quite know what should be the energy density of an infrared laser made using incandescent filaments. 😐
Besides, is this equation even correct? If I use something with 1000 MJ/kg, the consumption only increases.
So how the hell do I calculate how much energy I would need for 1000kg of thrust using a pulsed laser thruster similar to a pulsejet?
In any manner, the whole idea of the laser guns and laser thrusters is that before every “shot” of infrared emission, a tunnel of ionized air will be made using a Nd:glass donut tube. After that, the infrared light will be emitted through this ionized tunnel at its target, like an optical fiber.
But that gave me the idea of using it as an energy shield instead.
You would make the ion optical tunnel in the shape you want, in this example, a cone, and then the infrared light would be emitted inside of it. Reflecting until its energy is dispersed as heated plasma, then you repeat the process billions of times per second.
The only shape that I could think of realistically making was a cone/pyramid shape, unfortunately, I couldn’t think of a way of making an ion tunnel using lasers with a more convenient shape, like an actual shield of some sorts.
On top of that, it would also need to be really, really precise on its timing, or else all the infrared light (and visible light) would be emitted in every direction instead of being fully absorbed by the plasma bubble.
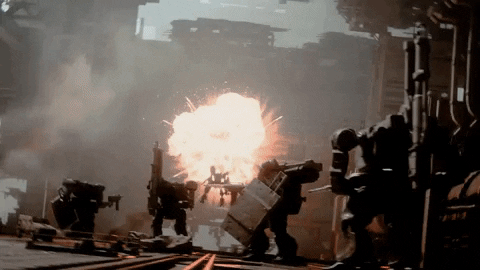
There is also the possibility of making the laser curve using the thermal lensing effect, but I really don’t know how that would work in such a short path (neither in a long path, lol).
You can bend a laser’s path using a gradient of sugar content on water, I just don’t know how you would do that in the middle of the air using the heat gradient of a laser.
I asked this on quora, but people keep ignoring the gradient part and straight up saying “that is just a trick, you can’t bend a laser outside of a black hole”, and I can only judge in silence.

Discussions
Become a Hackaday.io Member
Create an account to leave a comment. Already have an account? Log In.