Synthetic Natural Gas (SNG): Through methanation, syngas can be transformed into methane, the primary component of natural gas, enabling its use as a clean-burning fuel. https://patents.google.com/patent/US20120032452A1/en?utm_source=chatgpt.com
Dimethyl Ether (DME): DME, produced from syngas, can serve as a substitute for diesel fuel in compression-ignition engines and as a propellant in aerosol products. Biomass in a petrochemical world - PMC
Hydrogen: Syngas can be processed to produce hydrogen, which is essential for fuel cells and various industrial applications. Gasification: Unleashing the Power of Tomorrow's Energy
Gasoline and Diesel: Through the Fischer–Tropsch synthesis, syngas can be converted into liquid hydrocarbons such as synthetic gasoline and diesel, suitable for internal combustion engines. Biomass in a petrochemical world - PMC
Ethanol and Other Alcohols: Syngas fermentation processes can produce ethanol and other alcohols, which can be used as fuels or chemical feedstocks. Biomass in a petrochemical world - PMC
Jet Fuel: The Fischer–Tropsch process can also produce synthetic jet fuel, which is used in aviation. https://patents.google.com/patent/US20120032452A1/en?utm_source=chatgpt.com
The choice of fuel to produce from syngas depends on factors such as the desired end product, available technology, and economic considerations.”
So:
- 3D model the built-in multi-stage wood chipper in order to turn wood into fuel on the go. This would also be a sawdust converter too.
A few examples: Angle Grinder HACK - Make A Wood Chipper | DIY 🇺🇸 🇬🇧 Plastic powder from old prints with a modified mill TWIN Angle Grinder HACK - Make A Twin Angle Grinder Powered Wood Chipper | DIY Schredder - Drum Chipper Wood crusher/sawdust making machine for big diameter wood logs BROTHER SAWDUST PRODUCE MACHINE KOREA
원스텝 파쇄솔루션 선구자 운타 XR 시리즈 폐기물, 금속류, 타이어 등
Lil Shreddy - Desktop 3D Printed Shredder - (No Supports) by alfiew024 - Thingiverse
easy shredder by dav88 - Thingiverse
Grinder by Gyrobot - Thingiverse
Lil Shreddy V2 - Desktop 3D Printed Shredder - (No Supports) by alfiew024 - Thingiverse
3D-printable shredder by Bribro12 - Thingiverse
recycle failed 3d Print Shredder by stefi01 - Thingiverse
Mini Shredder V9 by jtronics - Thingiverse
Mini Paper and Cardboard Shredder by Artabro - Thingiverse
mini shredder by DIYchen - Thingiverse
shredder - 4 shaft by dav88 - Thingiverse
3D Printed Open Source MultiMaterial UPcycler : SHRED-Buddy3D by venturebit - Thingiverse
Top Funnel for the Fila Maker Compost Shredder by jungleb0y - Thingiverse
Mini shredder loading hopper by GabrieleDaghetta - Thingiverse
3D Printed SHREDDER (Gearbox) by LetsPrintYT - Thingiverse
Auger-based feeder for animals, fish etc using Nema 17 stepper motor by NorthernLayers - Thingiverse
Gyver's cat feeder II screw by PavelNS - Thingiverse
Assemblable Archimedes Screw (or auger) in sections by avoronin - Thingiverse
Automatic fish feeder by Stagermeister - Thingiverse
Automatic Fish Feeder by jerseyguy1996 - Thingiverse
Compost Shredder Outer Gear Covers by daburke369 - Thingiverse
Tupperware Grate Master Shredder Blade Protection by Ratthy - Thingiverse
Spaghetti Shredder by lamabanana - Thingiverse
Replacement SHAFT for Philips Food Processor HR7761 HR7762 by Zivbot - Thingiverse
Actually 3D modelling the wood chipper and screw feeder:
I don’t know why I procrastinate so much to do this part since it is super simple.
(Every ADHD person be like that)
The specifics can be dealt with on a case to case basis, but in essence, I would take a bunch of metal disks, cut the edges with a grinder, weld or lock them in place with bolts and stack them up in a rotational bar.

Like this, the idea is that this would be inside a welded metal box and the wood would be fed from the top to the bottom, continuously grinding everything. You could even use conventional wood saws for that.
The screw feeder could be one of those wood serpentine drillers and that’s it.

(each one is around 10 dollars)
Of course, everything would need to be powered by a strong motor, but I already 3D modelled a bunch of electric motors that could be used.
Of course², you could just do your own thing based on the various wood chippers that I’ve linked above.
The complex part would be the ceramic check valve, but that’s reserved for the Heat exchanger part.
The fuel reformer would be nothing more than a heat-exchanger that can be self-cleaned.
Helium Thermal Engine Generator 3D model:
Well, since the molten carbonate fuel cell idea won’t work since it stops working in the presence of the sulfur contained in the vegetable coal, this is the best option.
This is me from the future and I solved that issue.
Still, maybe I will give this one a try too because it seems quite interesting. Helium turbines are like steam turbines but easier and safer (I think).
Observation:
Cold plasma, or non-thermal plasma, or non-equilibrium plasma is a type of plasma that can be made without melting everything that it touches.
However, since it is full of free electrons and free ions, it can be used as a catalyst for chemical reactions.
Cold Fire You Can Touch - DIY Cold Plasma Torch
The Cold Plasma Wand That Heals (Microjet)⚡
You could (or should) add this to the burner of the helium turbine, which will make it burn more efficiently.
I did want to make the Inside-out combustion turbine, but… Realistically speaking, I don’t see how it could be built with scrap and cheap materials.
- Recapitulating:
Helium turbine generator plants are said to achieve around 50% to 60% efficiency by themselves, with the catch that you need multiple stages in series doing the same thing.
It normally works at 100ºC to 900ºC and at pressures of 20 to 70 atmospheres.
This one is a nuclear reactor plant with a helium-xenon turbine cooler generator. It has an efficiency of 45% working at 1300 Kelvin/1000 ºC at an unspecified pressure ratio.
However, in the PDF it is said:
“Unlike simple gas turbine cycles, where higher pressure ratio yields better fuel efficiency, optimum cycle pressure ratio for regenerative cycles is typically less than 3.5. The preliminary design study looked at compressor pressure ratios ranging from 1.9 to 3.0. The results of this study indicate that a pressure ratio of 2.5 is a good compromise between thermal efficiency and matching the turbomachinery with a direct drive high-speed generator.“
So I’m assuming that it is a pressure of maximum 3 atmospheres? Just like a turbocharger?
No, at page 15 in the PDF it is said that the entire thing is at 1.5 MPa (15 atmospheres), the pressure ratio is how much the pressure is increased (2.5 times) to 3.75 MPa (37.5 atmospheres).
It has a 125kg turbo generator with 60,000 rpm with an output of 370 kilowatts in total, the article says that it is around less than 5% of the total of the power plant. Meaning the entire power plant weighs at least 2500 kilograms.
I would risk saying that 1500 kilograms is at least the radiation shielding of the thing and the generator must be heavy because of the magnetic core of the slots and the permanent magnets… And the radiator…
I’m just coping?
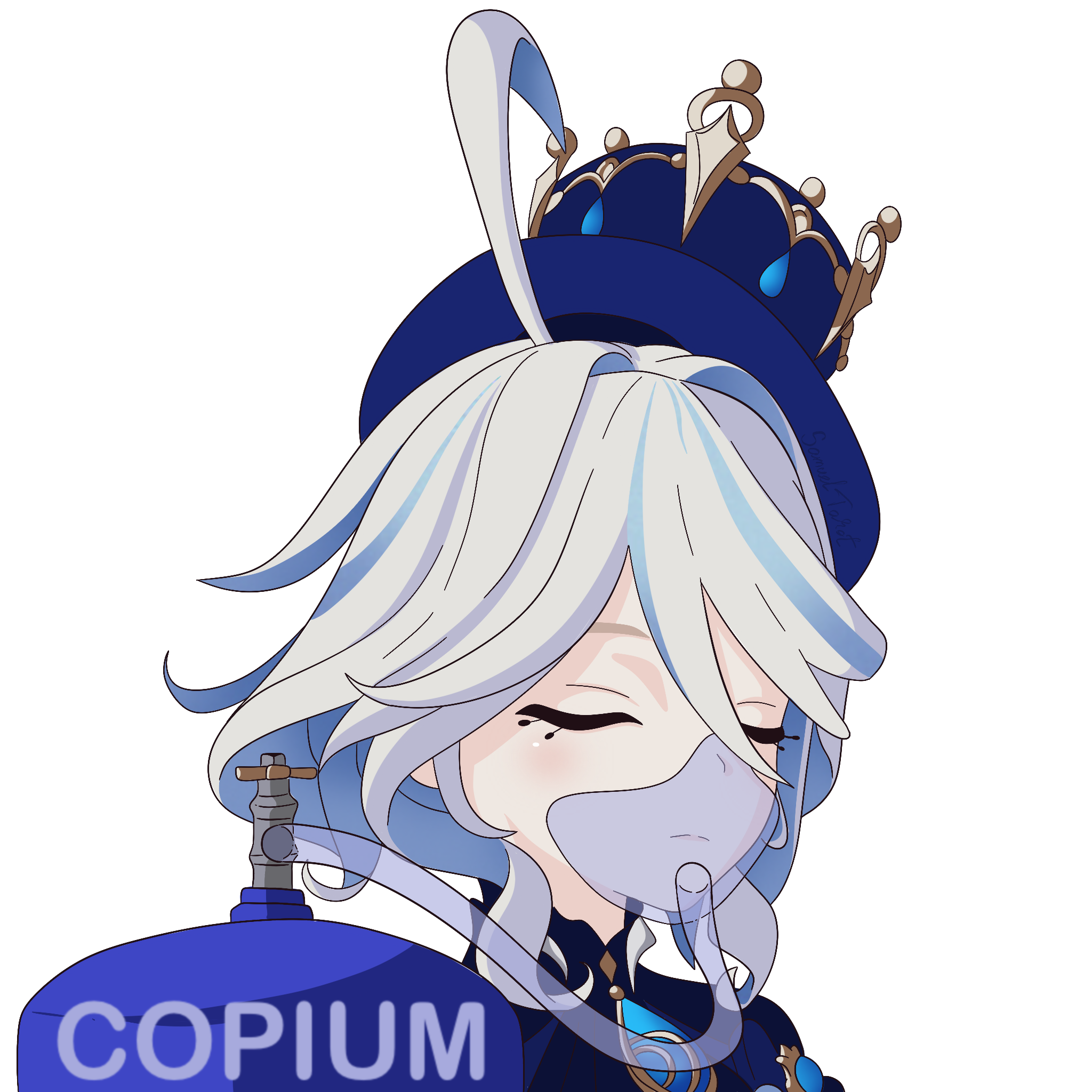
This looks like a turbocharger… The turbine doesn’t seem that big, so does the generator, it is said that it has 0.11m³ of volume.
This would be a 1 meter long cylinder with around 40 cm of thickness.
This isn’t the only helium turbine reactor that exists tho, this is the only one google showed me that has an output energy of 370 kilowatts. Most of the helium turbine power plants are meant for megawatts of power.
A few examples:
- Gas Cooled Fast Reactor
- (PDF) The Energy Multiplier Module (EM 2 ): Status of Conceptual Design
- DESIGN AND DEVELOPMENT OF GTHTR300 X. YAN, K. KUNITOMI, T. NAKATA and S. SHIOZAWA
- https://www.researchgate.net/publication/290549538_Turbulent_Flow_Boundary_Layer_and_Heat_Transfer_Characteristics_for_the_Intermediate_Heat-Exchanger_Simulation_of_a_VHTR
- Structure:
Assuming that the pressure is just ambient pressure, the first idea is to use Aluminum, since it is light, has a good thermal conductivity, it is accessible and can easily be made to be really resistant.
… But the thermal operation of the turbine is 1000ºC, even with the film cooling used on gas turbines, they can only protect up to around 300ºC. And aluminum melts at 700ºC…
Melting Point of Metals & Alloys | Toolbox | AMERICAN ELEMENTS ®
- Aluminum-Iron Alloy Melting Point 1160-1250 °C
There is a difference between Ferroaluminum and Iron aluminide.
Both have more than 20% of aluminum, but Ferroaluminum is used as sacrificial material in steel forgery.
Iron aluminide has tensile strength around 600 MPa at room temperature. But at 600ºC the maximum is 300 MPa, at 700ºC it is around 200 MPa and at 800ºC is just around 100 MPa.
- Aluminum-Nickel Alloy Melting Point 1385 °C
- Brass Melting Point 930 °C
- Aluminum Bronze Alloy C95400 Melting Point 1027 °C
- Copper Nickel Alloy Melting Point 1110-1235ºC
Since the compressor and turbine are so small, I do think it will be possible to add a combined cycle in series.
Essentially, the heat from turbine-1’s exhaust heats up turbine-2’s recuperator/heat-exchanger, which then repeats to turbine 3 and 4 and so on. This may or may not increase the efficiency significantly.
The compressor/turbine are meant for 60,000 RPM, but I’d prefer to use it with at least 10 times less rpm. The document doesn’t specify the diameter of the turbine either, so it is hit or miss while searching for turbochargers.
NOW listing what I need to 3D model:
- 3D model of the compressor and turbine based on turbochargers, if a real one can be bought for casting, or a 3D model can be found online then it won’t be necessary. Turbochargers for cars and the like can achieve 80,000 rpm to 250,000 rpm. It would be better to have a turbocompressor properly made for helium at 1.5 MPa, but I do not have access to such a thing.
- 3D model the stators for higher efficiency airflow.
- Need to 3D model the body of the turbines with the thickness intended for appropriated pressure ratios, based on those fire extinguishers with 2 MPa of pressure.
- Electromagnetic bearings.
- Eddy current couplers, this will allow for turbines to be coupled to compressors through solid metal walls without the need for seals.
- Tubing with appropriate thickness also, but in this case you can buy off the shelf materials, since, although it is a higher pressure for hobbyists, it is somewhat accessible.
- 3D model of the brushless generator with wiring etc.
- Internal cooling tubing both for film cooling of the blades, cooling of the walls, cooling of the components (bearings etc).
- Complex radiators/spiral heat exchangers that use both the heat from the heat source and heat absorbed by the cooling system. I will also make it modular, because there isn’t much difference between a radiator and the heat-exchanger piping for the heat source.
- Insulation layer to keep heat from scaping.
- 3D model of an air blower/turbocharger for the heat source, so it can reach high temperatures. Technically, this will be a turbine engine, and on top of that, it will be a combined cycle of combustion and helium turbine. Like a combined cycle of combustion and steam turbine.
- 3D model of the self-cleaning air filter for the air blower, since it has 0.44kg/s of airflow. Possible examples: Sonic Air Filter Dry Cleaning System Airpel Self Cleaning filter Self-cleaning air filter | Productvideo | Fendt 900/1000 Vario | Fendt Mullet High-Speed Cyclone Dust Collector -- How it works FILTER DENGAN SISTEM VORTEX Machining Coolant Filtration Snapshot Video - Nikuni VDF Hydrocyclone.wmv Dust Collection: Small Changes, Massive Effect! Water-Resistant Vents for Industrial Applications | Design for Mass Production 3D Printing Vibrations-Power-Vehicles-Exhaust-Filter Removal of Particulate Matter Emissions from a Vehicle Using a Self-Powered Triboelectric Filter | ACS Nano (Maybe I could use all of them together in series, lol)
- And finally, 3D model the exhaust of the heat source to go through a recuperator and finally through a catalytic converter to avoid too much pollution.
If you use the helium = steam comparison, then you could use a heat exchanger similar to that of steam for the helium.
And one problem for coal burning into steam engines is that the soot and ashes make a thermal insulating layer, which makes it require more coal, which reduces efficiency.
So a good step would be to add a pyrolysis step with a self-cleaning filter to convert the biomass into syngas for clean burning.
It is said that a condensing boiler is the most efficient design of boilers.
… But I don’t know if it will work with helium, because it is said to be the most efficient because the water in the exhaust/air condensates at the tubing, absorbing heat in the process, then that water is pumped into the steam boiler with the normal reservoir after filtration.
Sooo I would need a heat absorber for the condensed water itself?
Boiler Water and Steam Cycles - Understand the working
These are pretty much what I intended to make, but it also adds bypass valves/tubing for better efficiency.
The most efficient design of gas burners is: (I couldn’t find an specific name)
Efficient Gas Heating of Industrial Furnaces | Thermal Processing Magazine
How to Design Industrial Burners
Energy-efficiency-and-design-in-burners slides (this one uses oscillating combustion with extra air injection for better efficiency)
Swirl stabilized flames are also said to be very efficient, they are also used in gas turbines.
(PDF) Design and Optimization of Combustion Chamber for Gas Turbine Engine
Making the flame go into a cyclone style will also give it more time to exchange heat without increasing the size of the combustion chamber.
Now it is said that the most efficient design of heat exchanger is the plate heat exchanger.
Plate heat exchanger - Wikipedia
Spiral Heat Exchangers Explained
Which Heat Exchanger Is Best? The Three Main Types Explained...
Heat Pipes and Other Heat Transfer Techniques
However, since I do intend on adding a pyrolysis process, powder and other chemicals can be trapped inside of it. So it could be interesting to make it in a conical way so it works like a cyclone filter. Dust Collection: Small Changes, Massive Effect!
I still couldn’t find a turbocompressor for helium. Either 3D model or real product.
In this site you can see the electric centrifugal compressor, which looks pretty conventional. It is also said in the description that it can be used for helium.
And I just remembered that helium can be expensive.
This whole thing may end right here because of that.
I can only find small helium tanks for parties, which costs 400 reais (70 dollars) and the only description it has is “it can fill 30 party balloons”. 😐
Some of the articles that google shows me says that nitrogen and pure air are good candidates to replace it.
According to the articles, you can achieve a maximum 38% of efficiency with either.
Nitrogen turbines that I could find:
Advanced Power Generation Using a Nitrogen Turbine Engine Instead of a Conventional Injection Steam Turbine Engine In this article it says it depends on the design, but that it is around 34.3–300 atmospheres. From 3 to 30 MPa.
Thermal performance analysis of a nuclear heated gas turbine with nitrogen coolant - ScienceDirect
This one says nitrogen turbines have a compression ratio of 5:1 at 9.75 atmospheres and 1100 kelvin/800 ºC.
Welcome to the new Generation IV International Forum's Public Website - Redirection Hub | GIF Portal
This one is a mixture of helium and nitrogen at 850ºC depending on the stage.
This one says the nitrogen system was optimized to 180 atmospheres at 455ºC.
It also talks about regulating the “pinch point” of the reactor to 15ºC.
From google:
“The pinch point is the location in the heat exchanger where the temperature difference between hot and cold fluid is minimum at that location.”
Supposedly, you could also use commercial gas coolants used in conventional freezers and air-conditioners, but they tend to decompose at temperatures between 70ºC to 400ºC depending on the specific coolant.
Supposedly², you could replace helium with these commercial coolants if you reduced the heat input. That is just a matter of “heat density”, the amount of joules/energy used to achieve a flame of 1000ºC in a small space could be used to heat a really big space to 60ºC and power the turbines.
But… That would be a really freaking big combustion chamber and heat exchanger…
300ºC is 3.3 times smaller than 1000ºC, so… Could you perhaps make it work by using a combustion chamber and heat exchanger with 3.3 times more volume or area? Or increasing the pressure 3.3 times?
Depending on the temperature of the stage in question, it could be possible to replace the helium/nitrogen with commercial coolants.
I also couldn’t find a compressor design specific for hydrogen, but in any manner, you could replace the turbo compressor/turbine with reciprocating diaphragm piston, even with pneumatics it can get around 90% efficiency, although I don’t know how factual that can be.
A Guide To Air Compressor Efficiency
It can only achieve 90% with slow movement (meaning bigger pistons = meaning higher weight).
So… How can pneumatic systems only achieve 20% efficiency if this is so great?
Amplifying Piston Force Using Fluid‐Induced Tension in Flexible Materials | Request PDF
This article shows that the pneumatic actuators achieved 80 to 90% efficiency using diaphragm pneumatic pistons.
I would also need to find a material that is flexible and resilient at 1000ºC for the diaphragm compressors/turbines (“turbine” in the sense that the diaphragm will be pushed with the hot nitrogen air, like an stirling engine), since this is the temperature I will have to work with in case I don’t use crazy pressures.
I searched for a few articles listing the tensile strength of metals at high temperature, and in all cases the metals always lose 90% of their tensile strength.
But since this is a reciprocating engine, you could use flexible materials with high temperature insulation to embed the wire mesh, like ceramic fiber glue/paint that can withstand up to 1400ºC.
On top of that, the cooling can still prevent it from overheating while also using the heat loss to move other pistons, just like I was intending with the turbines.
There is also the problem of sourcing the helium.
Maybe you could make a desktop fusor to convert hydrogen into helium.
Like fire, it is easy to make fusion, but hard to produce useful power from it. THat is why we need huge power plants for gas turbines.
Building A Nuclear Star In A Jar (Fusor)
DIY Nuclear Fusion Reactor, FFaaST: Farnsworth Fusor as a Sealed Tube. Part 1: Glassblowing
Making a Desktop Fusion Reactor
Fusor Plasma Dynamics - Star mode, Jet mode, Glow discharge
Home Made Farnsworth Fusor | Hackaday
Chat GPT explained:
“Conclusion: Running a fusor continuously to convert 1 liter of hydrogen into helium would take an impractically long time—around 17 million years—due to the extremely low rate of helium production in typical fusor operations. Therefore, using a fusor as a method for helium production is not feasible.”
oof
Well, ChatGPT assumed that it was a calculation based on the output of desktop fusors that uses 300 watts.
Then it keeps oscillating between 8 billion joules or 8 trillion joules to convert 1 liter of hydrogen into helium with a fusor. lol
Oh, by the way, just like this nitrogen turbine, steam engines have a working temperature based on the pressure they are working on.
Accordingly to ChatGPT (which is not that reliable), if you worked with a steam turbine at around 10 to 20 bar of pressure (like the nitrogen turbine), you would only be able to heat the water to steam around 180ºC.
Although you don’t need a lot of heat to evaporate it, nor a lot of pressure, you would need a crap-ton of steam flow to compensate.
Steam flow/gas flow doesn’t mean you need metric tons of said fluid, only that you would need to recirculate them super fast. And I don’t think that would be energy efficient nor possible to do.
Maybe you could have parallel boilers taking a percentage of the heat of the heat-source, but still, how practical that would be?
I was wondering about making DIY ceramics:
Ultra-high temperature ceramic - Wikipedia
Silicon carbide manufacturing process - GAB Neumann
“Fine silicon particles can be converted to silicon carbide (SiC) by heating in the excess carbon from the organic material. The silica fume, which is a byproduct of producing silicon metal and ferrosilicon alloys, also can be converted to SiC by heating it with graphite at 1500°C (2730°F).”
Production of boron carbide powder by carbothermal synthesis of gel material.
“Boron carbide (B4C) powder has been produced by carbothermal reduction of boric acid–citric acid gel. Initially a gel of boric acid–citric acid is prepared in an oven at 100°C. This gel is pyrolyzed in a high tem- perature furnace over a temperature range of 1000–1800°C.”
Preparation of Titanium Carbide by Carburisation of Titanium Dioxide.
“TiC can be formed by the reaction of solid carbon and titanium dioxide with a high temperature (1700–2000 °C) and long reaction time (10–20 h) [17,18]. The diffusion of carbon is the controlling step in the reaction. Hence, increasing the temperature and time facilitates the formation of carbides [19].”
Even though I can make ceramics in a DIY setup, it doesn’t mean I can make them flexible.
The only way to make flexible ceramics is to either make it a microfiber or a chain.
Flexibility Matters | Flexible Ceramics and Glass | Corning
Method of Ceramic Fiber Manufacturing
How ceramic fiber yarn produced
Can a Dr. Stone Centrifuge Make Cotton Candy and Wires? (maybe you could use a similar process for ceramic fibers)
Basic Carbide - How it's Made (ceramics/carbides need a binder and high compression in order to be made into solid pieces, but I do wonder if you could make foam out of it if you sinter it rapidly without compression)
I was also wondering about the possibility of “vacuum” steam engines.
Heatpipes works by applying vacuum in a tube with a few drops of water:
TLDR: How Heatpipes & Air Coolers Work (w/ animation)
So I was wondering if I did it inside a steam boiler/engine.
The vacuum would be applied first and then the water would be injected after, so it would fill in all of the inside volume.
I asked on quora, reddit and ChatGPT, and all of them said that: although heat pipes are good at transferring heat, it wouldn’t exactly mean that it would convert that heat into mechanical work.
Igloos are great heat insulators and animals too, and I think I should pay attention to them in order to make a better insulating structure for this external combustion engine.
In the case of the igloo, it melts and solidifies over time, dispersing and absorbing heat. I could use a similar thing to the “turbine” expansion chambers, they would be so hot that everything else would act like ice.
Speaking of it, since the expansion chambers/turbine-pistons would be at temperatures ranging from 1000ºC to 2000ºC or more, wouldn’t that mean that conventional materials like steel or glass could be used as flexible materials instead.
They would compose the diaphragm/membranes since they would be flexible, but extremely viscous.
Glass gets less viscous than water at 1800ºC…
yikes…
I guess that is good news for whoever wants to make a Tailless Prince Rupert’s Drop.
List of viscosities - Wikipedia
Everything gets extremely thin at such absurd temperatures, even molten iron only gets 4 times thicker than water at 1800ºC.
Honey has a viscosity of around 14 to 20 times the viscosity of water at room temperature.
I asked ChatGPT:
“Several ceramic materials have melting points within the range of 1500ºC to 1800ºC. Here are some notable examples:
Alumina (Al₂O₃) - Specifically, CeramaAlox™ Ultra Pure alumina has a melting point of approximately 1750ºC. It is known for its high purity (99.95%) and exceptional mechanical and electrical properties [1].
Silicon Carbide (SiC) - This material, particularly in its CeramaSil-C™ form, can withstand temperatures up to 1900ºC. Silicon carbide is recognized for its hardness, strength, and excellent thermal conductivity [1].
Silicon Carbide / Boron Carbide (SiC+B₄C) - Known as DuraShock™, this composite material has a melting point of around 1800ºC and is designed for applications requiring toughness and hardness, such as ballistic protection [1].
Shapal Hi M Soft™ - This machinable aluminum nitride (AlN) ceramic can withstand temperatures up to 1900ºC, offering high mechanical strength and thermal conductivity [1].
Mullite (3Al₂O₃·2SiO₂) - Melts around 1840°C, providing excellent resistance to deformation and creep in the temperature range you specified.
Alumina Silicate melting point – 1,790°C”
This one says that a lot of these materials have a lower melting point.
Actually, forget about it.
I don’t need to have molten materials to use as glue, just getting close to their melting point is enough to make them flexible.
And besides, I don’t exactly need expensive/complex ceramics to make the structure, carbon has a melting point of 3,550 °C.
Also, the tensile strength of Steel keeps approaching 0 MPa the more you get closer to its melting point, while at same time its viscosity starts to approach that of water the more you get past its melting point.


So there is a specific point between 1000ºC and 1490ºC where Steel is neither a strong alloy, nor a viscous material. But since its viscosity can’t be measured properly, doesn’t that mean that it is like a putty?
But that is even the best approach, though?
I mean, assuming that steel is embedded inside ceramic fibers, and it is constantly air cooled on the other side of the cylinder (or through channels), that wouldn’t be much of a problem, no?
Well, like I said in Option 2 for structural materials, you can lower the melting temperature of Alumina (2070ºC) to 950ºC by adding Cryolite as flux.

You could also use DIY heat tiles from shuttles: Making The Most Heat Resistant Material!
On the other hand, at which temperature does nitrogen reacts with carbon?
“At what temperature is carbon nitride formed?
Carbon nitride can be synthesized in a wide range of temperatures (500–650 °C), time (1–10 h) and rate of temperature increase (2–20 °C min−1).”
These same kinds of nitrogen reactions occurs with every type of ceramics.
So you would need to use Helium in the end… Nitrogen can be too reactive at these temperatures.
Maybe this diaphragm piston heat engine can be made in the style of a V engine or a rotary engine…
I would need to add electromagnetic bearings and/or diaphragms on everything possible…
I mean, there are a myriad of different engine configurations:

Learn about every Engine Layout in just one video | V-W-X-U-H Engines

According to ChatGPT, the most efficient one is inline engines. BUT that was said in the context of internal combustion engines, which uses camshafts and timed valves.

Difference Between Oversquare, Undersquare, and Square Motorcycle Engine
This looks more like a general rule of thumb rather than an actual engineering law or something like that.
Let's Settle This. Bore vs Stroke - It's Not That Simple
Long or short stroke is not the same as rod length, by the way:
MIND BOGGLING ENGINE GEOMETRY - Rod Ratio Explained
To Be honest, I was thinking of a high rpm engine with long rods and small bores with small strokes because the engine could be smaller and lighter by having high rpm and low torque. But I don’t know… F1 engines have pistons rotating so fast that they experience 20 g's of acceleration, making them 20 times heavier and experience a proportional force when they go down abruptly.
Well, it wouldn’t be much different than an air-engine, the difference is that the pressure is generated by heat.
This specific design is interesting, because the inlet valve only opens when the piston is high up. But the problem is that since it is a diaphragm air engine, you can’t use the seals to stop the air from running through the exhaust.
Nevermind, he solved that.
But I mean, if you want an absolutely fail-proof way of only releasing the air when the pressure is reduced, then you would need to use camshafts.
You can also use combustion engine designs, tricks and other stuff:


Source: Free STL file hypocycloidal engine cutout ⚙️ ・Template to download and 3D print・Cults
I always wonder why the hell hypocycloidal engines aren’t a thing, since they would solve all the problems related to wall-friction in combustion engines…
This TINY Nissan Engine is More Powerful Than Your Car!
We Found the Lost 40kg, 400bhp Nissan Engine! (It's INCREDIBLE)
This is how Porsche's new SIX-STROKE engine works!
This Tiny Engine Part Changed Everything!
You'll understand everything about Atkinson, Miller and Otto cycle engines after watching this video
SECRETS OF MOTOGP & F1 ENGINE POWER!!! | Pneumatic Valve Spring ( Working Mechanism & History )
FreeValve Isn't a Big Deal. Here's why
The Impossible Engine Speed😳| Explained Ep.28
PatRon: Harmonically Reciprocating Piston Rotary Engine
https://www.pattakon.com/pattakonVVD.htm
https://www.pattakon.com/pattakonHydro.htm
https://www.pattakon.com/pattakonVRA.htm
Why It’s Almost Impossible to Rev to 21,000 RPM
This is a single cylinder F1 engine – 20,000rpm, 300cc, 90bhp!
How Formula 1 Pistons Are Made (I went to the factory)
What If F1 ENGINES Had No Rules?
We Found the Lost 40kg, 400bhp Nissan Engine! (It's INCREDIBLE)
Spain is Living in 2050? Revolutionary 1 Stroke INNengine Analyzed
How Honda's IMPOSSIBLE Engine BROKE MotoGP!
Logic Defying V5 Engine - Honda's RC211V Explained Like Never Before
How the Honda Chimney Engine Works in 3D. 🧠
The Complex Napier Sabre 24 Cylinder "H" Aero Engine Explained Simply
Why the Inline 6 Engine Disappeared From Aviation - History & Technical
The Rise & Fall of the Radial Airplane Engine - History & Technical
Why THIS Engine is DOMINATING in MotoGP
The Unseen Achievement of Honda's Oval Piston Engine - A different perspective on the Honda NR story
How Ducati Made A 1-Cylinder Bike Truly Fast
CROSSPLANE inline 4 EXPLAINED in detail - How the YAMAHA R1 i4 differs from all other INLINE FOURS
Flatplane vs Crossplane - Which Is Best?
The crankshaft stand for centering.
DIY CRANKSHAFT REPAIR (KUNYA) KEY WOODRUFF
How to make an RC engine crankshaft - How to make a crankshaft for a small engine
How I Made a Custom Crankshaft
Millyard Kawasaki S1 Four Cylinder Crankshaft - How its Made - Episode 2
V16: Why Bugatti Stopped Producing the W16 - The Secret & Details Behind the Tourbillon
Deep Dive: Inline 4 vs. V4 vs. Boxer 4 - What's the Difference? Engine Balance Explained in Detail
How This GENIUS Clutch Makes MotoGP Riders FASTER
The Rise & Fall of the Radial Airplane Engine - History & Technical
COMPRESSION RATIO: HOW to CALCULATE, MODIFY and CHOOSE the BEST one - BOOST SCHOOL #10
Why Exhausts Make So Much Power😵| Explained Ep.27
Design and Analysis of a Novel Composited Electromagnetic Linear Actuator
The Ingenious Napier Deltic 2-Stroke Diesel Engine
$5000 Normal Engine vs $10 Million Formula 1 Engine
How These Tiny Engines Make BIG Power
Why These F1 Engines Only Lasted 200 Miles
SECRETS OF MOTOGP & F1 ENGINE POWER!!! | Pneumatic Valve Spring ( Working Mechanism & History )
The Corvette ZR1's Engine Is Absolutely Insane — 1,000+ Horsepower!
Pratt and Whitney R-2800 - America's Indestructible WWII Aircraft Engine
World War 2 Greatest Engine - The Battle Over European Skies Documentary WW2
Rolls Royce Crecy - The Most Advanced Piston Aero Engine Never Made.
How Pratt & Whitney Changed Aviation
How To Build A 4,300hp Aviation 'Wasp Major' In The 1930s?
Napier Sabre - The Ultimate WWII Aircraft Engine - Part 1
Yakovlev M-501 - The BIGGEST Piston Radial Ever Designed
This TINY Nissan Engine is More Powerful Than Your Car!
This Brilliant Engine Makes 1000 HP Without Boost!
Why This Tiny Honda Engine Can Make 1000hp
Why Honda K20/K24 Engines Make Too Much Power😮| Explained Ep.7
HOW TO: MAKE 300 HP, 400 HP & 500 HP WITH PEANUT PORT BBC HEADS (HUMBLE JUNKYARD GEN V 454 )
Pratt and Whitney R-2800 - America's Indestructible WWII Aircraft Engine
Mazda 13B Eccentric Shafts - What Are The Differences.
Triumph T-Plane Engine Explained and Compared with Yamaha's CP3 Crossplane Inline 3 engine
MIND BOGGLING ENGINE GEOMETRY - Rod Ratio Explained
STEEL vs ALUMINUM vs TITANIUM Connecting Rods
one stroke engine (You could make it a one-stroke diaphragm engine, but the shaft should go through all the chambers in order to equalize the pressure and displacement)
Reciprocating Compressor C series - animation | Howden (this can also be applied to the compressor)
I do think that neither option will be viable/possible with the diaphragms at 2000ºC, but you could make the chambers and diaphragms adjacent to the piston.

Like this. You could all have multiple ones to a single shaft.
One thing that people compare between piston and turbine engines is that piston engines have a “shock” or whiplash effect, Since it is always going up and down, changing motion at extreme speeds, it influences the strength and efficiency of the system.
So a rotary engine could supposedly solve that issue.

(I always wondered why these engines were never used in helicopters)
Actually, do I really need a piston, at all?
It is a diaphragm in a rotary engine, the diaphragm/accordion combustion/expansion chambers would eventually contract and expand.
How to make an accordion out of paper. Origami accordion
DIY accordion piston for Stirling engines (origami)
How To Fold Yoshimura Polyhedral Pattern | Paper Cylinder Spring | Paper Lantern #origami #paperfold
Collapsible Paper Tower Helix Decagon
Hexagonal Bellows Fold or Accordion Fold. (Card Folding Tutorial).
Car engine science: Ignition timing, emissions, mixture
RBR - Radial Bi Rotary Balanced Piston Combustion Engine
New Split Cycle Engine Concept: The Doyle Rotary Engine
Bentley BR1 Assembly Movie (HD)
Radial vs. Rotary | AIRCRAFT ENGINES | Plane Savers S2-E6
This Engine is Not What You Think... Le Rhone 9C - YouTube
How it works: Radial vs Rotary Aircraft Engine #plan #airplane #engineering - YouTube
ROTARY ENGINES: HOLD THE CRANK, SPIN THE REST | Simanaitis Says
(PDF) The Rotary Aero Engine from 1908 to 1918

(I think this could be interesting to add) Source: (PDF) The Mixture Formation Process In The Radial Engine
Design of Connecting Rod || step by step procedure || technical classes || learn and grow
The issue is: how to feed the fuel air and cooling channel in a self-contained helium piston engine?
It is a f*cking external combustion engine, you don’t need to feed the fuel inside of it. I’m stupid…
Wait a minute… Since I’m going to use diaphragms, pistons and a cascade system, this is nothing more than a thermoacoustic generator.
I mean, even if I don’t use acoustic resonance, it would work just like an overcomplicated Stirling Engine. And that is essentially what a thermoacoustic engine is.
Cascading the system (aka make multiple engines in séries) would increase the efficiency tô around 45% to 50%, which is the efficiency of a cascading cooler. And a cooler is the reverse of a thermal engine.

This is a stirling engine, but instead of having a cold and hot side, the air is expelled.

Similar things are used for free piston powered turbine engines.
At this point I’m starting to wonder why not just convert this into a conventional internal combustion engine.
Well, to begin with:
An internal combustion engine that uses high temperature and lean burn would be extremely propense to knock-up, aka detonation instead of combustion.
Maybe using the idea of the Omega 1/StarFire engine could work, although I’m not so sure about it since it is clearly a scam.
The H2 Starfire Engine Explained

Omega Engine - a closer look - Part 1
Omega Engine - a closer look - Part 2
Although we all know it is a scam, you could make it work by adding multiple “tooths” like a gearbox.
You could make the “teeth” round, so they seal against each other mechanically instead of relying on the clearance of the walls.

Not to mention that you could in fact make multiple rotors in a single engine, like a planetary gearbox.
… Of course, assuming it will work, you would need membranes/diaphragms extending very farther from the disk, so the air doesn’t escape during compression. And then that introduces the problem of how the membranes/diaphragms would even survive under high centrifugal forces.
There is also the issue of fuel injection, but it would be actually possible to do so if the center wheel-gear is fixed while the rest is rotating.

Like in a planetary gearbox where you can keep any of the three elements fixed in place, or the other gifs, whatever they are.
But then you introduce the problem that separating the exhaust gas from the incoming air would be impossible since you can’t isolate the air flow like in a conventional engine.
Actually, I think I’m wrong.
For example:

Assuming that each gear tooth is a diaphragm combustion chamber, you don’t need to keep the fuel and air insertion moving with the entire structure.
But it would still be impossible to filtrate the exhaust gases.
The only idea I had was either to have a bunch of suction tubes at the sides of the stator gears in order to capture the exhaust gases.
Actually, I had another idea: the diaphragm of each combustion-chamber in the gear teeth would actually be isolated from the external gear.

Where normally the gear teeth would engage, the air bubble would be compressed, and once it combusts, it would expand again, pushing the gear. Thus, the exhaust gases could also be extracted with a valve in the stator gear (just like in the gif).
But… Just like in the reciprocating piston engine, the diaphragm would always be pushed up and down, requiring really strong diaphragms.
Actually, do you even need the gear teeth at this point? You could use a simple wheel and it would still work just fine.
The more I watch these videos and read the articles, the more I’m sure I won’t be able to make a reliable piston engine. Turbine engines are mechanically “simpler”, but require super alloys and complex aerodynamics.
But can I really make something actually useful tho? I’m not even an engineer…
Airflow through an Axial Compressor
Is THIS Really The Future of Jet Engines?!
What Exactly is a Mixed-Flow Turbomachine?
All in One: A/R, Compressor Maps, Turbo Lag, Surge, Twin Scroll, VGT, Wastegate +more
Appreciating The Beauty of Jet Engines by Juxtaposing Them Against Piston Engines
Jet Engine Evolution - From Turbojets to Turbofans
So You Want to Design a Jet Engine
Cautionary Tales from the Jet Shop
J79 - Turbine Engines: A Closer Look
Discussions
Become a Hackaday.io Member
Create an account to leave a comment. Already have an account? Log In.