Electrical Arc Comparison - High Voltage Jacobs Ladder Discharge 28KV Different Currents
Maybe you could make the electric discharge move in the direction you want if you apply a magnetic field at 90º angle to the discharge length.
There is also the vortex discharge thingie, but I never saw anything about using it for propulsion:

How Does a Plasma Vortex Work?
Electric Arcs in a Magnetic Field | Magnetic Games
Plasma Vortex in Magnetic Field - Electric Lightning within a Magnetic Field - Physics Experience
Plasma Vortex in a Magnetic Field | Magnetic Games
At best, I found this kickstarter:
Plasma Jet Electric Thrusters for Spacecraft

This is a plasma accelerator, essentially a plasma railgun. However, as the guys stated, it can only work in a single pulse, thus the necessity for funding to make it make more pulses.
And honestly, I don’t know if they implied this has a projectile or not, because a lot of the plasma railgun articles I find focuses on using plasma as the armature/rails instead of the accelerating matter itself.
Firing the Lorentz Plasma Cannon (You can kinda do that, if the current is strong enough, it will compress the plasma itself, creating a plasma filament wire)
(PDF) Development of Micro-Particles Accelerator with Pulse Formation
This is one of the few exceptions, and I’m not even sure if it would work.
It does look like the dense plasma focus apparatus, though…
Dense plasma focus - Wikipedia
Numerical simulation of plasma flows in curved coaxial ducts with longitudinal magnetic field
[PDF] A contoured gap coaxial plasma gun with injected plasma armature. | Semantic Scholar
Air Force SBIR Phase I: Pulsed Plasmoid Propulsion System for Agile and Resilient Spacecraft
Dynamic formation of stable current-driven plasma jets | Scientific Reports
Development of a high energy pulsed plasma simulator for the study of liquid lithium trenches
MHD Centripetal Melter - Fusor Forums
On the impact of the plasma jet energy on the product of plasmadynamic synthesis in the Si-C system
Modeling of thermalization phenomena in coaxial plasma accelerators
Dynamic formation of stable current-driven plasma jets | Scientific Reports
Hall Current Plasma Accelerator
ATON-Thruster Plasma Accelerator
Plasma propulsion for rocket engine using ion thruster
The Deadly Coilgun/Railgun Hybrid You've Never Heard Of (Helical Railguns) (yes, this one again, but you could use the tesla coils to create the magnetic field that will accelerate the discharge)
Plasma Gun Design, Particle Ion Beam Weapon SciPhi 08
Design and optimization of a high thrust density air-breathing pulsed plasma thruster array | Journal of Electric Propulsion This one produced 21 millinewtons of thrust for every 9 joules with a frequency of 20 hertz and 21 millinewtons per kilowatt.
It is said in the article:
“Unlike many EP thruster experiments, no gas feedthrough was incorporated into the thruster. The TAMU PPT is passively filled relying on the ambient pressure inside of the vacuum chamber. This method may need to be adjusted in future experiments depending on the thruster installation method onboard a spacecraft. For example, if the thruster is relying on onboard propellant or the high-speed flow in front of the spacecraft a gas feedthrough would better model these circumstances than the current passive refill system.”
9806.65 millinewtons = 1 kilograms 9806.65 millinewtons / 28 millinewtons = 350.2 9 Joules x 350.2 = 3,152.1 joules per pulse for 1 kilogram 3,152.1 joules per pulse x 20 pulses per second = 63,042.75 joules 63,042.75 joules x 60 seconds x 60 minutes = 22,6953,900 Joules 22,6953,900 Joules = 84.5 horsepower hour = 63,406.2 watt hour for 1 kilogram of thrust
I mean, you “just” use 63,042.75 joules per second… You could have some quick boosts armored core style.
63,042.75 x 5000kg of thrust = 315,213,750 joules.
Also, another question:
At 35 kilometers of altitude the pressure is 0.00682831 and the temperature is -34ºC. Assuming I'm using this thruster at sea level, how would pressure influence the thrust generated?
The breakdown voltage of air is 3 kv/mm while vacuum is 30 kv/mm…
The pressure difference would be around 150 times at sea level, would that result in 150 times more thrust?
Theoretical and Experimental Analysis for an Air-Breathing Pulsed Plasma Thruster
“A theoretical model and laboratory results are used to demonstrate that specific thrust values of > 350 mN/kW can be generated by the system at desired altitudes of ~ 25 km.”
Oh well, you would more or less reduce the energy cost of 300 megajoules for 5 tons thrust to 30 megajoules to 5 tons of thrust.
And the pressure it worked with was 0.05 bars, instead of the 0.006 bars of the previous thruster.

Investigation of a Pulsed Plasma Thruster for Atmospheric Applications
“Specific thrust measurements of 470 mN/kW were obtained using the pendulum based thrust stand.”
Electrohydrodynamic Thrust for In-Atmosphere Propulsion
Electroaerodynamic Thruster Performance as a Function of Altitude and Flight Speed
An Investigation of Ionic Wind Propulsion - NASA Technical Reports Server (NTRS)
“A pin array was found to be optimum. Parametric experiments, and theory, showed that the thrust per unit power could be raised from early values of 5 N/kW to values approaching 50 N/kW, but only by lowering the thrust produced, and raising the voltage applied.”
Design and testing of a laboratory setup for EHD propulsion studies
“ A thrust-to-power ratio as high as approximately 100 N kW−1 was obtained.”

As I believed, the increase in voltage increases the performance and efficiency of the ionocraft.
5000 kg = 50,000 Newtons = 500,000 watts for 5000kg of thrust 500,000 joules (per second) for 5000kg of thrust.
… But I find it ironic how the simple, flimsy ionocraft thruster just outperformed all of the crazy suggestions I’ve made and the highly complex ones I found…
Wait… Now I’m wondering how reliable that article is. I couldn’t find a single article with a similar output of thrust…
“100 N kW−1”
100^-1 = 0.01
huh… Is this correct?
Metre per second squared - Wikipedia
“Newton's second law states that force equals mass multiplied by acceleration. The unit of force is the newton (N), and mass has the SI unit kilogram (kg). One newton equals one kilogram metre per second squared. Therefore, the unit metre per second squared is equivalent to newton per kilogram, N·kg−1, or N/kg.”
In any manner, if I really want to make a crapton of thrust, I better find a way of making this thing way studier than it already is…
Now I’m wondering how I could scale this up… How much thrust per area? How much thrust per kilogram?
ChatGPT:
“Ionocrafts, or electrohydrodynamic (EHD) thrusters, generate thrust by ionizing air and accelerating the ions using electric fields. Achieving high thrust-to-weight and thrust-to-area ratios in these devices is a significant engineering challenge, but recent research has made notable progress.
Thrust-to-Weight Ratio
Miniaturization has been a key strategy in enhancing the thrust-to-weight ratio of ionocrafts. Smaller devices benefit from favorable scaling laws, leading to improved performance metrics. For instance, researchers at the University of California, Berkeley, developed a millimeter-scale ionocraft with a relatively high thrust-to-weight ratio compared to other pico air vehicles. This advancement is attributed to the reduced size and mass of the device, which enhances its overall efficiency.
The Ionocraft: Flying Microrobots With No Moving Parts
Additionally, studies have indicated that decreasing the scale of thrusters can lead to increased thrust-to-weight ratios and reduced operating voltages required to achieve desired drift field strengths. This suggests that further miniaturization could continue to improve performance.
Thrust-to-Area Ratio
The thrust-to-area ratio is influenced by factors such as electrode design, operating voltage, and ionization efficiency. Optimizing these parameters can lead to higher thrust densities. For example, an experimental investigation into ionic wind propulsion reported a maximum measured thrust of about 0.45 N with a flow area of roughly 0.1 m², resulting in a thrust-to-area ratio of approximately 4.5 N/m². Their optimum thrust-to-power ratio was 21 N/kW.
An Investigation of Ionic Wind Propulsion “
Supposedly, increasing the distance between the electrodes increases overall efficiency.
I also wondered how to increase the arc discharge length:
ChatGPT:
“Introducing intermediate electrodes between the anode and cathode can indeed extend the overall distance of an electrical discharge arc. Each pair of adjacent electrodes forms its own gap, and the breakdown voltage for each gap depends on the product of the gas pressure and the gap distance, as described by Paschen's Law.
To increase the arc discharge distance in air from 30 cm to 1 meter while maintaining an applied voltage of 1 megavolt (MV), you can introduce intermediate electrodes to divide the total gap into smaller segments. This approach leverages Paschen's Law, which relates the breakdown voltage to the product of gas pressure (p) and gap distance (d).
Paschen's Law Overview:
Paschen's Law is expressed as:

(When I copy paste scientific equations, it gets all messed up in the google document, so I’m just copy-pasting the printscreen)
Calculating the Number of Segments:
Given an applied voltage of 1 MV and a desired total gap of 1 meter, we can determine the optimal number of segments (n) by ensuring each segment operates below its breakdown voltage.
Determine the Breakdown Voltage per Segment:
The breakdown voltage for air at standard atmospheric pressure is approximately 30 kV/cm.
Calculate the Maximum Gap per Segment:
To maintain a safe margin, let's assume each segment should not exceed 25 kV.
Maximum gap per segment = 25kV / 30kV/cm = 0.833cm
Determine the Number of Segments:
n = Total distance / Maximum gap per segment = 100cm / 0.833cm ≈ 120
Implementation:
By introducing approximately 120 intermediate electrodes, each spaced about 0.833 cm apart, you can extend the arc discharge distance to 1 meter under an applied voltage of 1 MV. This configuration ensures that each individual gap remains below its breakdown voltage, facilitating a controlled and sustained discharge path.
Considerations:
Electrode thickness: While specific thickness values can vary based on several factors, a practical approach is to use electrodes with a thickness ranging from 1 mm to 5 mm. This range typically provides a balance between mechanical robustness and effective thermal management for high-voltage applications.
Precision: Accurate spacing and alignment of electrodes are crucial to prevent unintended discharges.
Insulation: Proper insulation between segments is necessary to maintain the integrity of the system.
Environmental Factors: Variations in pressure, temperature, and humidity can affect breakdown voltages and should be accounted for in the design.
By carefully designing the electrode configuration based on Paschen's Law, you can achieve the desired increase in arc discharge distance while operating within the constraints of the applied voltage.”
Maybe you could use a low power cold plasma source to make the air even more conductive, which would allow for bigger distances, no?
But in order for the cold plasma generator to work it would need an already existing air flow, meaning that I would need to make a moving part to make the non-moving part propulsion system to work. Or at least to start working…
Arc Discharge System for Micromachining of Helical Fiber - PMC (I think this one is very, very interesting)
Effect of electrode configuration on plasma spatial distribution and gas temperature in multi-arc plasma generator with three pairs of electrodes (this one as well)
I mean, I was thinking of doing something like that turbineless jet engine that I suggested in the Helium Thermal Engine Generator. But without moving it (like an Archimedean Spiral?).

The ionic wind thrusters electrodes would be placed at the top and at the bottom of the engine, using the intermediate electrodes (and or cold plasma generators) I mentioned in order to increase the travel distance of the arc discharge.
🔶🔶🔶🔶
(I will write these orange squares to keep track of parts where I’m procrastinating, so I finish them already)
Cryogenic liquid air electrothermal propulsion:
With that aside: Maybe it would be interesting to cool down air until it becomes liquid and then use an electrothermal rocket.
Making Liquid Nitrogen with my Homemade Cryocooler
According to the ideal rocket equation calculator, I would need 5 kilograms of liquid of air (assuming 1000 seconds of specific impulse) to accelerate 500 kg of mass to 300 km/h.
Tsiolkovsky Rocket Equation Calculator • Model Rockets • Online Unit Converters
According to the specific heat calculator, I would need 1,118,260 (1.2 megajoules) in order to convert 5 kg (5 liters more or less) of liquid air at -196ºC (70ºK) to 25ºC (room temperature).
I’d assume that this is the same exact amount of energy to convert room temperature air into liquid air, although either heating or cooling it down would have different efficiencies, and thus, different consumptions of energy.
Electrothermal rockets are around 90% efficient, while cryocoolers are below 20% to around 10%. Depending on the type.
This says that even laser thermal rockets achieve a specific impulse of 800 seconds, not 1000.
So the de facto result is:
7845 m/s of effective exhaust velocity
… Which gives the same result of 5 kilograms of initial mass 😐
What is the pressure required inside the chamber anyway?
ChatGPT:
“In thermal rocket engines, the pressure within the expansion chamber—commonly referred to as the combustion chamber or pressure vessel—varies based on the engine's design and type.
Chemical Rocket Engines:
- Liquid Propellant Engines: These engines typically operate at chamber pressures ranging from 10 to 20 megapascals (MPa). For instance, the SpaceX Raptor engine has achieved chamber pressures up to 30 MPa. SpaceX Raptor - Wikipedia
- Solid Rocket Motors: Chamber pressures in solid rocket motors are generally lower, often between 3 to 7 MPa, depending on the specific design and application. Solid Rocket Motor Upgrade - Wikipedia
Nuclear Thermal Rocket Engines:
- The NERVA (Nuclear Engine for Rocket Vehicle Application) XE engine, a prominent example of nuclear thermal propulsion, operated at a chamber pressure of approximately 3.86 MPa. NERVA - Wikipedia
These pressures are critical for determining the engine's thrust and efficiency. Higher chamber pressures can enhance performance but require more robust materials and advanced cooling techniques to withstand the increased thermal and mechanical stresses.”
So the thermal laser rocket already has a similar specific impulse to that of nuclear rockets…
I was wondering, however, how much the specific impulse would increase if you increased the pressure inside of it to 30 MPa…
Taking into consideration that at 8.1 MPa gaseous hydrogen and gaseous oxygen rocket has 158 seconds of specific impulse and the liquid hydrogen and liquid oxygen rocket has 450 seconds of ISP at 30 MPa:
30/8.1 = 3.7 450/158 = 2.84
So I would more or less triple the specific impulse…?
And thus, according to the rocket equation calculator, I would need 1.8kg of cryogenic propellant.
Also, I was playing around with the numbers and I noticed that every time I tripled the pressure, thus, the specific impulse (ISP x 10 = effective exhaust velocity), the amount of mass required to accelerate the rocket was cut by half.
Observation:
The name is ideal rocket equation, in reality it would be lower. The raptor engine reached 380 seconds of ISP.
By the way, you can reduce it to -150ºC instead by increasing pressure to around 20 to 30 bars.
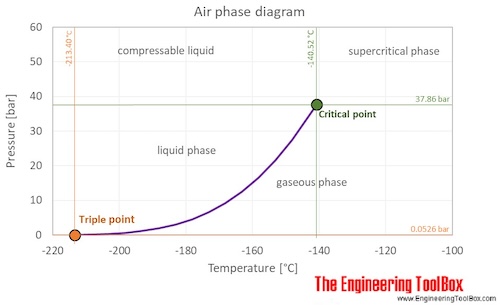
Source: Air - Thermophysical Properties
So, how would I store cryogenic fluid at -196ºC anyway? (overshooting for safety)
ChatGPT:
“To effectively insulate a cryogenic tank storing ambient air cooled to -196°C (the boiling point of liquid nitrogen), it's essential to minimize heat transfer through conduction, convection, and radiation. The following materials and methods are commonly used in cryogenic insulation:
Multi-Layer Insulation (MLI): MLI consists of multiple layers of thin, reflective materials separated by spacers. This design significantly reduces heat transfer by radiation. MLI is widely used in spacecraft and cryogenic applications due to its high thermal performance and compactness.
Vacuum Insulation: Creating a vacuum between the inner and outer walls of the tank can significantly reduce heat transfer by conduction and convection. This method is commonly used in vacuum-insulated evaporators and other cryogenic storage vessels.
Reflective Foils and Papers: Reflective foils, such as aluminum, combined with insulating papers, are used in multi-layer insulation systems to reflect thermal radiation. This combination is effective in reducing heat gain in cryogenic vessels.
YOUR GUIDE TO CRYOGENIC INSULATION”
“At extremely low temperatures, such as -196°C (77 K), Styrofoam (expanded polystyrene) and other plastics exhibit significant changes in their mechanical properties.
Styrofoam at -196°C:
Styrofoam is a thermoplastic polymer composed of polystyrene, which is known to become brittle at low temperatures. At -196°C, Styrofoam would undergo a transition from its typical flexible state to a brittle one, making it susceptible to cracking or shattering under stress. This behavior is due to the reduction in molecular mobility at such low temperatures, leading to a loss of ductility.
Low Temperature Properties of Polymers
Behavior of Other Plastics at -196°C:
The response of plastics to low temperatures varies depending on their chemical structure and molecular composition:
Polyethylene (PE): PE becomes brittle at temperatures below -184°C (-120°F).
Polypropylene (PP): PP exhibits brittleness at temperatures below -190°C (-310°F).
Acrylonitrile Butadiene Styrene (ABS): ABS becomes brittle at temperatures below -184°C (-300°F).
Nylon: Nylon exhibits brittleness at temperatures below -184°C (-300°F).
Polytetrafluoroethylene (PTFE): PTFE remains relatively stable at low temperatures but can become brittle below -275°F (-170°C).
In general, most plastics transition from a ductile to a brittle state as temperatures decrease, with the specific transition temperature varying based on the polymer type. This transition is characterized by a decrease in molecular mobility, leading to reduced flexibility and increased susceptibility to fracture under stress.
Low Temperature Properties of Polymers “
Also, remember that I posted earlier a NASA document showing that epoxy composite materials retain their strengths next to absolute 0 (-273ºC).
Testing Tensile and Shear Epoxy Strength at Cryogenic Temperatures
Cryogenic Impact on Carbon Fiber-Reinforced Epoxy Composites for Hydrogen Storage Vessels
Aluminum also survives at these temperatures, apparently:
Influence of Cryogenic Temperatures on the Mechanical Properties and Microstructure of 2195-T8 Alloy
Cryogenic Deformation Behaviour of Aluminium Alloy 6061-T6 | Metals and Materials International
Glass and ceramics also (seems to) stay okay at such temperatures.
Although I don’t like making these pressure vessels, you have to make them as such.
After all, once you start heating them up, they will expand and go somewhere. Preferably out of the rocket nozzle.
There is also the possibility of the nitrogen and oxygen reacting into a combustion due to their high concentrations.
Water hydrolysis Propulsion:
… Ooooor I could simply take water (from the humidity in the air) and use electrolysis to separate it into oxygen and hydrogen, then make propulsion out of it. 😐
ROCKET that LITERALLY BURNS WATER as FUEL
DIY Atmospheric Water Generator! - Produces/Extracts Distilled Water from the air! - DIY distiller
Drinking Water From Thin Air?! How To Harvest Moisture With A Dehumidifier
Well, I just can’t find the specific impulse of oxygen and hydrogen gas. I can only find their specific impulse in liquid form…
Performance verification of a laboratory scale hydrogen/oxygen combustion chamber (it achieved a specific impulse of 158 seconds at pressure or 8100 kPa [81 bars] at a flow of 22g/s of hydrogen and 65g/s for oxygen with a thrust of 137 newtons [13 kg])
Gaseous Hydrogen/Oxygen Injector Performance Characterization
VERY LOW THRUST GASEOUS OXYGEN-HYDROGEN ROCKET ENGINE IGNITION TECHNOLOGY (325 seconds of specific impulse at 517 kN/m² [5.17 bars] producing 1 newton of thrust)
Accordingly to this specific impulse calculator, that would result in 1549.5 m/s of effective exhaust velocity.
Again, inputting 500 kg of final mass on the ideal rocket engine calculator, it got 27 kilograms of initial mass.
So, this one needs 27 kilograms of water converted into hydrogen and oxygen, but the liquid air propulsion needs just 5 kg?
I know why: https://en.wikipedia.org/wiki/Specific_impulse
The specific impulse of liquid oxygen + liquid hydrogen is just 450 seconds, while its effective exhaust velocity is 4,400 m/s.
And like I said in the previous section, it needs around 30 MPa of pressure.
Almost half of the thermal laser propulsion… So I’m just reducing what is already low…
I asked ChatGPT:
Me:
“I don't understand, normally it is said that these thermal rockets (resistorjet, microwave thermal rocket, arcjet, laser thermal rocket etc) are really low thrust with high efficiency/specific impulse, but how can they produce low thrust?
For example, if you calculate the amount of joules required to heat and expand and generate thrust, it gives a certain amount of joules that you could supply instantly with a capacitor bank.
Still, all of these examples use several kilowatts of power for little to no thrust over long periods.”
ChatGPT answered:
“useless garbage”
In essence, it keeps seeing that nuclear thermal rockets have better thrust because they are nuclear, even if I say I will supply the proper power in joules.
But in reality, nuclear thermal rockets also suffer from the same problem.
It was just saying it has higher specific impulse and higher thrust because I assumed it was the case and it doesn’t dare to correct me.
Engine List 1 - Atomic Rockets
It says the amount of watts they consume, but not the duration, thus, not the amount of joules required.
The Orion Project aka pulsed nuclear detonation propulsion system has both high impulse and high thrust because it is a detonation aka explosion.
Project Orion (nuclear propulsion) - Wikipedia
“The Orion concept offered both high thrust and high specific impulse, or propellant efficiency: 2,000 pulse units (Isp) under the original design and an Isp of perhaps 4,000 to 6,000 seconds according to the Air Force plan, with a later 1968 fusion bomb proposal by Dyson potentially increasing this to more than 75,000 Isp, enabling velocities of 10,000 km/sec.”
But technically speaking, a rocket is a continuously detonated bomb…
How the hell do I make sure I get the propulsion and efficiency that I desire with the minimal mass usage possible?
However, kinetic energy is calculated as “mass x velocity”, then how do I make sure that the amount of thrust is properly generated?
Example, a tank round’s gunpowder has around 10 megajoules of energy per kilogram, while weighing around 10 to 20kg. Thus having a total of 100 to 200 megajoules in energy in total. It has 30 tons of recoil and its round (such as that tungsten dart) has around 10 megajoules of kinetic energy.
Then why can’t I make a thermal rocket booster like this?
Wikipedia says that the pressure inside the barrel is around 500 to 700 MPa.
So, 100 or 200 mJ / 30 tons of recoil = 3.3 to 6.6 megajoules of energy required for every 1000 kg of thrust, thus requiring 16 to 33 megajoules of energy for 5 tons of thrust to move a mass of 500kg to 300 km/h.
But tank cannons have 30% of efficiency in transferring the energy to the round and the rest is either lost or spent pushing the barrel with the recoil of 30 tons, no?
Taking into consideration the calculation of the tank ammunition, it would need 2 to 4 kilograms of gunpowder with 10 Megajoule per kilogram of energy density.
And if you notice, it has a similar amount of mass to what the liquid air thermal rocket calculation I found before.
Thus, I’m assuming I would require around 16 to 33 megajoules of input energy in the thermal rocket in order to generate 5000 kg of thrust in bursts/detonations just like the tank. Maybe like a rotating detonation engine.
Since the tank barrel has 500 to 700 MPa of pressure, you would need 16 to 23 parallel pressure tanks with 30 MPa of internal pressure releasing 5 kg/liters of liquid air in order to keep the equivalent mass flow. (I think)
I asked again:
“To achieve the same thrust of 5 tons (approximately 49,033 Newtons) with a cold gas thruster operating at a lower pressure of 30 MPa, you'll need to adjust the mass flow rate of the propellant accordingly.
Thrust Equation:
The thrust (𝐹) produced by a cold gas thruster is given by:
F=m˙ * ve
where:
m˙ is the mass flow rate of the propellant (kg/s)
ve is the exhaust velocity of the propellant (m/s)
Exhaust Velocity and Pressure Relationship:
The exhaust velocity ( 𝑣 𝑒 v e ) is influenced by the chamber pressure ( 𝑃 𝑐 P c ) and can be approximated for an ideal gas expanding isentropically through a nozzle:

where:
γ is the specific heat ratio of the gas
R is the universal gas constant
Tc is the chamber temperature (K)
M is the molar mass of the gas
Pe is the exit pressure (Pa)
Pc is the chamber pressure (Pa)
Assuming the exit pressure ( 𝑃 𝑒 P e ) is much lower than the chamber pressure ( 𝑃 𝑐 P c ), the term ( 𝑃 𝑒 𝑃 𝑐 ) 𝛾 − 1 𝛾 ( P c P e ) γ γ−1 becomes negligible, simplifying the equation to:

This shows that 𝑣 𝑒 v e is proportional to the square root of the chamber temperature ( 𝑇 𝑐 T c ).
Mass Flow Rate Adjustment:
Given that the thrust is directly proportional to both the mass flow rate and the exhaust velocity, and assuming the exhaust velocity decreases with the square root of the pressure drop (since temperature and pressure are related in an ideal gas), reducing the pressure from 500-700 MPa to 30 MPa would decrease the exhaust velocity. To maintain the same thrust, the mass flow rate must increase proportionally.
If the original system uses 5 kilograms of liquid gas to produce 5 tons of thrust at 500-700 MPa, and you're reducing the pressure to 30 MPa (which is approximately 1/20th of the original pressure), the exhaust velocity would decrease by a factor of about √20 (since 𝑣 𝑒 ∝ 𝑃 𝑐 v e ∝ √P c ). Therefore, to maintain the same thrust, the mass flow rate would need to increase by the same factor, √20 , which is approximately 4.47.
Thus, you'd need approximately 4.47 times more propellant:
5kg×4.47≈22.35kg
Therefore, you'd require approximately 22.35 kilograms of liquid gas at 30 MPa to achieve the same 5-ton thrust.
Note: This is a simplified estimation. In practice, factors such as nozzle design, gas properties, and thermodynamic efficiencies would influence the exact amount of propellant required.”
This is a similar value to that of the hydrolysis rocket…
(btw, chatgpt said that the tank gun would have 50 seconds of specific impulse based on gunpowder rockets)
That assumes that 70% of the energy is transferred to the barrel recoil, since around 30% of the energy of the gunpowder is transferred to the projectile.
Even if it was 90% or more (95%), it would still require some substantial amount of joules. Around 10 to 25 megajoules (1 megajoule = 1,000,000 joules).
Since I couldn’t find a way of designing and calculating it, I asked for already existing rocket engines so I can copy:
“Liquid rocket engines with thrusts ranging from 1,000 kgf to 5,000 kgf (approximately 9.8 kN to 49 kN) are commonly used in various aerospace applications, including upper-stage propulsion and spacecraft maneuvering. Below are some examples of such engines, along with their key specifications:
S5.80: A liquid pressure-fed rocket engine developed by the Soviet Union (now Russia) for spacecraft propulsion. It burns unsymmetrical dimethylhydrazine (UDMH) and nitrogen tetroxide (N2O4) with an oxidizer-to-fuel ratio of 1.85. The engine generates a vacuum thrust of 2.95 kN, with a chamber pressure of 0.88 MPa. It has a specific impulse of 302 seconds in vacuum and a dry weight of 310 kg. The engine is 1.2 m in length and 2.1 m in diameter. S5.80 - Wikipedia
RD-843: A one-chamber, multi-start pressurized fuel feed rocket engine developed by the Yuzhny Mashinbuilding Plant. It produces a vacuum thrust of 250 kgf and has a specific impulse of 315.5 seconds. The engine weighs approximately 15.93 kg and is designed for multiple restarts during flight. Liquid rocket engine RD-843 – Production Association Yuzhny Mashinbuilding Plant
L75: Developed by the Instituto de Aeronáutica e Espaço (IAE) in Brazil, the L75 engine is designed to provide 75 kN (approximately 7,650 kgf) of nominal thrust in vacuum. It operates with a mixture ratio between 1.50 and 1.95 and has a combustion chamber pressure ranging from 5 to 7 MPa. The engine uses liquid oxygen (LOx) and ethanol as propellants. Development Status of L75: A Brazilian Liquid Propellant Rocket Engine
Laika: An experimental sounding rocket developed by the Michigan Aeronautical Science Association (MASA). It employs a liquid bipropellant engine using nitrous oxide and 95% ethanol. The engine produces a nominal thrust of 3,780 N (approximately 385 kgf) and has a specific impulse of 215 seconds. The total vehicle mass is 96 lbs (approximately 43.5 kg). Laika Liquid Bipropellant Rocket | MASA - Taking Michigan to Space
RD-171: A powerful liquid-fuel rocket engine with four combustion chambers, each producing 1,000 kN of thrust, totaling 4,000 kN. It operates at a chamber pressure of 24.52 MPa and has a specific impulse of 338 seconds in vacuum. The engine's dimensions are 2.5 meters in length and 1.5 meters in diameter, with a dry weight of 9,750 kg. RD-170 - Wikipedia
RL10: A liquid-fuel cryogenic rocket engine that burns liquid hydrogen and liquid oxygen. Modern versions produce up to 110 kN of thrust in vacuum. The engine operates at a chamber pressure of approximately 1.5 MPa and has a specific impulse ranging from 373 to 453 seconds in vacuum. Its mass is approximately 131 kg. RL10 - Wikipedia
Rocketdyne LR101: A regeneratively cooled engine using liquid oxygen (LOX) and kerosene, producing around 4,450 N (1,000 lbf) of thrust. It operates at a chamber pressure of approximately 2.8 MPa and has a specific impulse (Iₛₚ) of about 249 seconds at sea level. The engine's dimensions are a chamber diameter of 69.3 mm, a throat diameter of 41.3 mm, and a nozzle exit diameter of 93.3 mm. Its dry weight is approximately 45 kg. 1000lb Thrust LOX-Kerosene Rocket Design
Rocketdyne H-1: Thrust: 2,200 lbf (9.8 kN) Combustion Chamber Pressure: 633 psi (4.4 MPa) Specific Impulse: 289 s Mass Flow: 2,092 US gallons/min (132 L/s) of RP-1; 3,330 US gallons/min (210 L/s) of LOX Size and Weight: Inboard Engine: 1,830 lb (830 kg) dry weight Outboard Engine: 2,100 lb (950 kg) dry weight Usage: Used in clusters of eight on the first stages of the Saturn I and Saturn IB rockets. Rocketdyne H-1 - Wikipedia
Rocketdyne F-1: Regarding the liquid fuel rocket engines used in the Apollo missions that sent humans to the Moon, the primary engine was the Rocketdyne F-1. This engine powered the first stage of the Saturn V rocket, providing the necessary thrust to launch the Apollo spacecraft toward the Moon.
For a more detailed overview of the Saturn V rocket engines, you might find the following video informative:
An Overview of the Saturn V Rocket Engines
The idea is that I could search for these engines and find 3D models online, scale them up to the propulsion and pressure that I need and then make the necessary modifications.
Dunno how well that would work, but better than take a PHD on rocket science just to make a 3D model of a mech, lol.
PulseJet Propulsion:
A possible and practical approach is the use of pulsejets.
They are simple, light and practical and work with any kind of fuel, but are extremely inefficient. 5% maximum, everything being lost as heat and sound.
Maybe you could increase the efficiency if you used both the fuel and the air as coolants (like in a rocket engine), an air compressor, thermal insulating materials, ideal fuel to air ratios and perfect timing for the detonations.

Sources: Enhanced heat transfer and flow topology of hydrogen regenerative-cooling channels with novel X-shape ribs - ScienceDirect Liquid Rocket Engines - Ultramet
Besides, you can make them in whatever shape you want (as long as the shapes are properly designed for sonic resonance, just like in the 2 stroke engines).

Valveless | Home Made Jet & Pulsejet Engine
Crazy Rocketman testing really big 400 pound thrust Pulsejet engine! This guy has a website where he sells his blueprints for pulsejet engines, although I don’t have money to buy them… lol
Crazy Rocketman: Test running the "Super Dragon" 450 pound thrust Pulsejet Jet engine.
New Rocketman show starting 2017 900lb thrust twin Pulsejet engine .
Maddoxjets.com: 900 pound thrust Pulsejet engine.
Cylindrical Tesla Valve Pulse Jet Engine (3D Printed)
Full Throttle Test: Did we Push a Pulse Jet Engine to its Limits?!
Experimental research on a rotary-valved air-breathing pulse detonation engine
WE USED AN AUGMENTER ON OUR PULSE JET!
This is in a Different Class Than a Raptor Engine! (Supposedly, if you stack pulsejets in a circular pattern and synchronize their firing sequence, you can make a rotating detonation engine, but I don’t know how well it would work since you are using the inefficient pulsejet)
Svarthålet Racing - Assembly of valve grid for pulse jet
I was also wondering about mixing this with the idea of the turbineless jet engine, in which the entire compressor is a closed screw which I talked about in the Helium Thermal Engine section.
Essentially starting rotation and then the proper combustion chamber maintaining propulsion.

Helical Blade Turbineless Gas Jet Engine
Real life force/energy-fields:
Skip to the end of this section because the actual energy shield talk starts around there.
Before I talk about my idea, let’s talk about energy shields in real life:
US20170097212A1 - Electric reactive armour - Google Patents
US9897418B2 - Electric reactive armour - Google Patents
How Electromagnetic Armor Vaporizes RPGs
Electromagnetic Reactive Armour
They are described like a capacitor bank, but they are called electromagnetic…
The Genius Behind The First Force Field
Not exactly bullet melting, but it is really cool nonetheless.
FORCE FIELDS: How Close are We?
How Close Are We to Building Force Fields?
There is an anti-missile system in tanks that works kinda like a force-field.
The idea is that two conducted plates, one negative and other positive are separated by an insulating layer (the armor), once a missile or projectile pierces the two plates, the system is connected through the projectile. Vaporizing it before it can damage the tank.
Is there a way of doing the electrode connection through projectile wire wirelessly?
Without physical plates?
I genuinely don’t know, but if you find a solution, you can make force fields a reality.
The only idea I had that might work for every type of projectile (and work passively) would be:
(I’m no engineer and none of this might work)
To use electrostatic sensor antennas linked to an “energy emitter” array.
In essence, the electrostatic antennas would make an electrostatic field in which it would detect changes in the field, so even if the projectile is non-conductive or non-magnetic, the antennas would detect a change. That change would passively open the mosfets (or a similar conductive gate) connecting the capacitors to the “energy emitters” in that region and direction, emitting enough energy to vaporize the projectile.
In this hypothetical scenario I’m assuming that the field would be tuned to react to projectiles flying at specific speeds and on top of that, filter out all the noise (only god knows how hard that would be). I’m also assuming that conventional electromagnetic fields/radars wouldn’t detect non-conductive materials.
The “energy emitter” would be anything that can emit enough energy to vaporize the projectile.
For example:
- Lasers that directly target the projectile.
- Infrared Photon emitters (like incandescent light bulbs).
- Electro Lasers: multiple laser induced plasma channels are created in the direction of the projectile, once the projectile disrupts the channels, they will pass thousands of joules worth of electricity through the projectile. Working like electric arc furnaces.
- A mix of the three, a laser induced plasma channel in the shape of a cone is formed and the infrared photon emitter does its thing. The plasma would (probably, maybe) work like a mirror of the infrared light, focusing all of its heat in the projectile.
Well, in my quest to find a way of making energy bubbles in order to make a real life energy field I came to two ideas that seem kinda realistic to try.
If you make it out of solid materials, it will eventually look like swiss cheese and not work anymore, but you can't make it with pure energy because the laws of physics aren't that convenient.
So I thought on these two ideas:
- Ultrasonic waves would keep conductive spheres floating around the object you want to protect. Researchers create a sonic tractor beam with loudspeakers
- Literally making unpoppable soap bubbles around the object. UNPOPPABLE BUBBLE SOLUTION (hold bubbles without bursting)
In both cases the outside would be negatively charged and the inside would be positively charged.
But in the case of the sonic tractor beam, I don't think it would work, since the spheres would just keep rotating.
Well, I asked around if these ideas would have any possibility of working, and the few people that cared to consider them said it simply wouldn’t work.
And being honest, I agree with them.
The only solution would be to actually keep the discardable wire mesh panels as the electrodes.
Since you could simply make the system useless by using non-conductive projectiles, the discharge of energy should occur at the place where the plates are pierced, based on the size of the projectile, not when the projectile itself completes the system.
Also, I would add points of emission for the incandescent filament/infrared photon emitter, the discharge would power up the infrared emitter, melting the projectile with the emitted heat.
… Bruh, I just reinvented ERA. 😐

But the unpoppable bubbles are really cool, I do wonder if they could be useful for composite materials and the like.
Extracting Strawberry DNA to make Massive Bubbles
The bubbles are harder to pop because of the molecular spaghetti that some polymers are.
Wouldn’t that be just like a fiber composite?
Making micro to nano fibers is really hard, but that could help the strength of composites, no?
… Or maybe I’m wrong, there are micro to nano sized needles.
Anyway, I used a Specific Heat Calculator and then used the weight of various different projectiles ranging from 9mm to 120mm armor piercing fin-stabilized discarding sabot (APFSDS) tank rounds assuming everything is made out of tungsten (melting point around 3500ºC) and an efficiency of heat transfer around 10%.
So:
- 9mm weighs around 10 grams = 4,500 joules x 10% efficiency of energy transfer = 45,000 joules to melt it.
- Caliber 5.56 mm (common assault rifle caliber) weighs around 4 grams = 1800 joules x 10% efficiency = 18,000 joules to melt it.
- 50 .cal BMG weighs around 50 grams = 22,800 joules x 10% efficiency = 228,000 joules to melt it.
- 30×173mm caliber (A-10 warthog bullet) weighs around 500 grams = 228,000 joules x 10% efficiency = 2,280,000 joules to melt it.
- APFSDS M829A3 (120mm) weighs around 25kg = 12,000,000 joules x 10% efficiency = 120,000,000 joules are required to melt it.
Well, this is a defense system for all projectiles, explosives or kinetic, like armor-piercing rounds.
But if we are speaking solely on explosive rounds, why does no one ever use net guns, pellet shotgun shells or even metal umbrellas of some sort?

It wouldn’t have the range and precision of a phalanx system, but it sure would be cheap.
Actual energy shield:
Since there is non-thermal plasma, one could make a cold-plasma layer around an object, you can make some kind of real life energy shield that could activate (turn into thermal plasma) when needed. I tried to find plasma shells, plasma layers, plasma blankets, but nothing like a sphere around an object.
But how would you detect the presence of an object?
I mean… You can use plasma both as a speaker and a microphone by detecting the disturbances in plasma.
Plasma Arc Microphones – Digilent Blog
ChatGPT:
“Yes, plasma arcs can be utilized as sensors to detect objects passing through them and determine their position. This capability stems from the plasma's sensitivity to disturbances in its properties, such as voltage, current, and impedance, when an object interacts with it.
In plasma arc welding and cutting processes, monitoring systems detect changes in arc characteristics to maintain optimal operation. For instance, variations in arc voltage are used to control the torch height, ensuring consistent cutting quality. When an object or material disrupts the plasma arc, it alters the electrical properties, which can be measured to infer the object's presence and position.
Additionally, in plasma chambers used for material processing, arc detection apparatuses monitor voltage and current ratios to identify disturbances. These systems can detect rapid changes indicative of an object interacting with the plasma, allowing for real-time adjustments to the process.“
Sources it listed:
Plasma arc cutting torch tracking control - J. Wang, K. Kusumoto, K. Nezu, 2001
US9170295B2 - Method and apparatus for detecting arc in plasma chamber - Google Patents
A switching arc plasma measurement experimental system using a magnetic sensor array
Use of the Plasma Spectrum RMS Signal for Arc-Welding Diagnostics
Discussions
Become a Hackaday.io Member
Create an account to leave a comment. Already have an account? Log In.