This is the basic schematic of the spot welder :
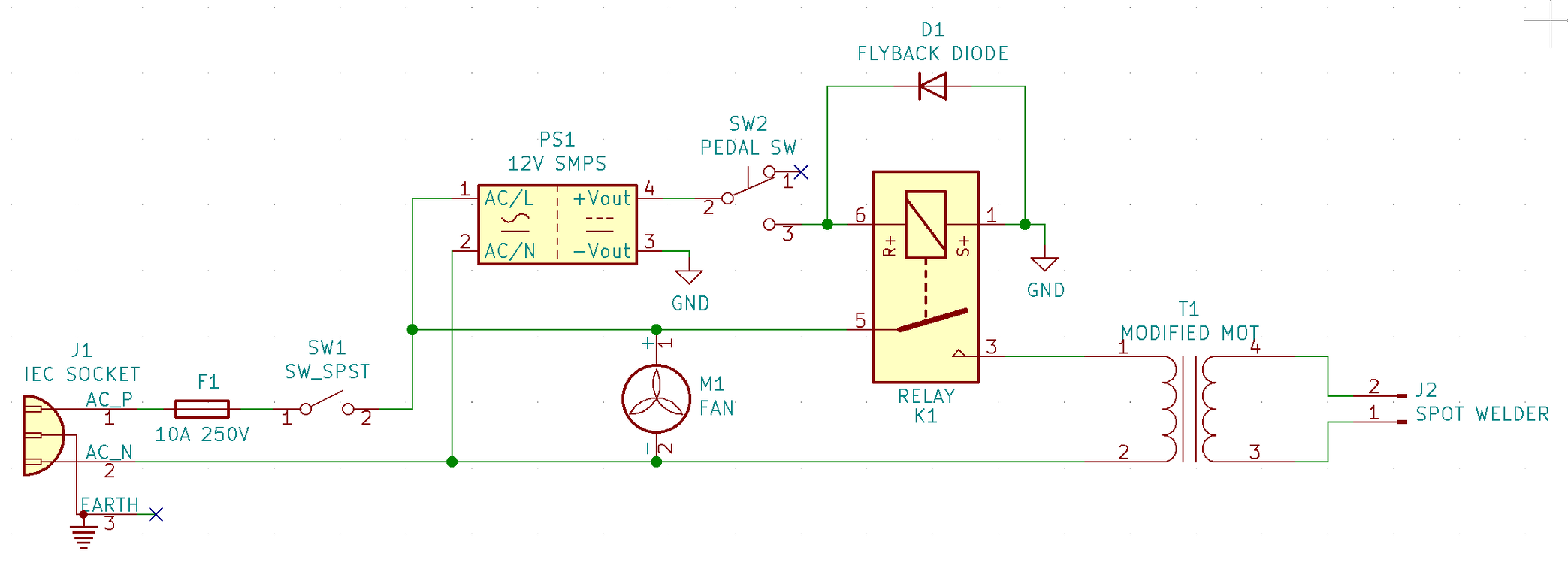
From the microwave oven (MO) I repurposed :
- its cooling fan, 220VAC/50Hz, 18W (REF: HL-YZF6110-A)
- its High Voltage (HV) transformer (REF: W-700S)
- door close switch, 125VDC, 0.6A (REF: SZM-V16)
- relay 12VDC trigger, 250VAC 16A (REF: JD2-1A)
To reduce the end product size when stored or displaced, I decided to use detachable leads. I took a fused IEC socket with power switch from my stock.
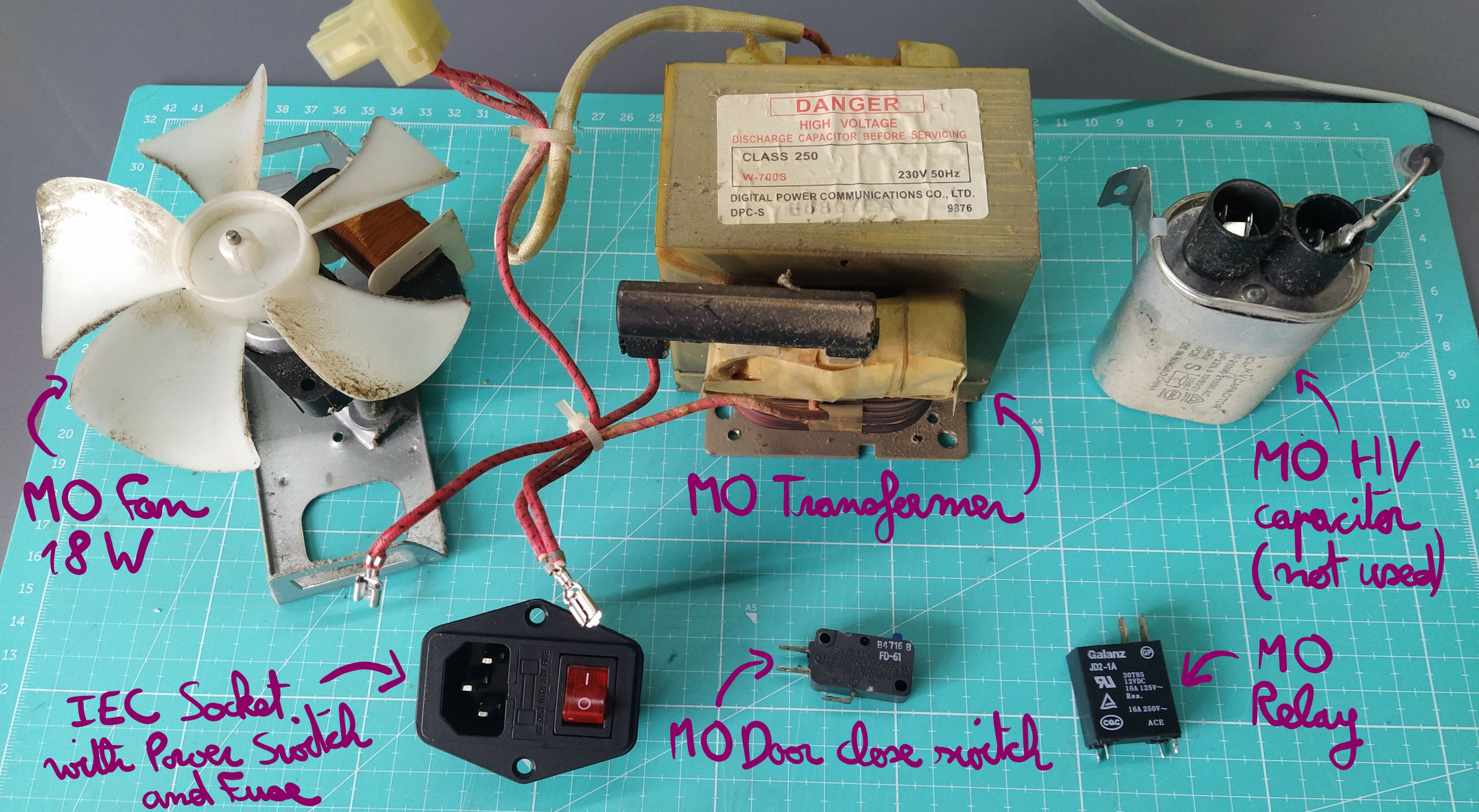
I could directly switch mains voltage with the switch in series to the primary, but I'm not comfortable having 220AC at the tip of my finger. Hence, the use of a small 12V power supply to trigger the relay. I took apart one which was initially powering a router.
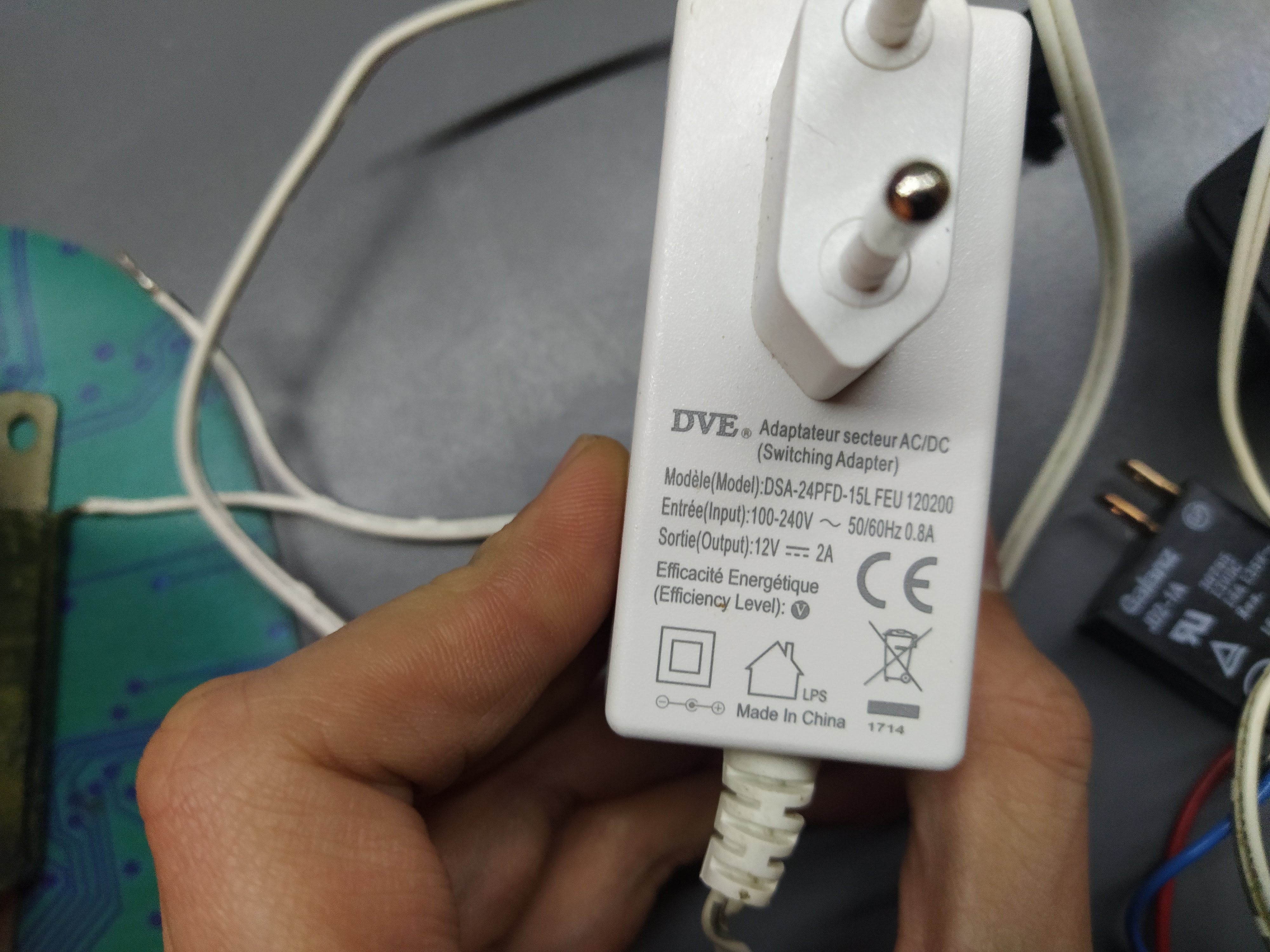
The transformer has to be modified first. In its current state, it is outputting 2kV and little current (few mA). For a spot welder, we need very little voltage and hundreds of amps for the duration of the weld (few ms). We can obtain this output by changing the secondary windings to a few turns of thick gauge wire.
First, we need to get rid of the secondary with the help of a hacksaw :
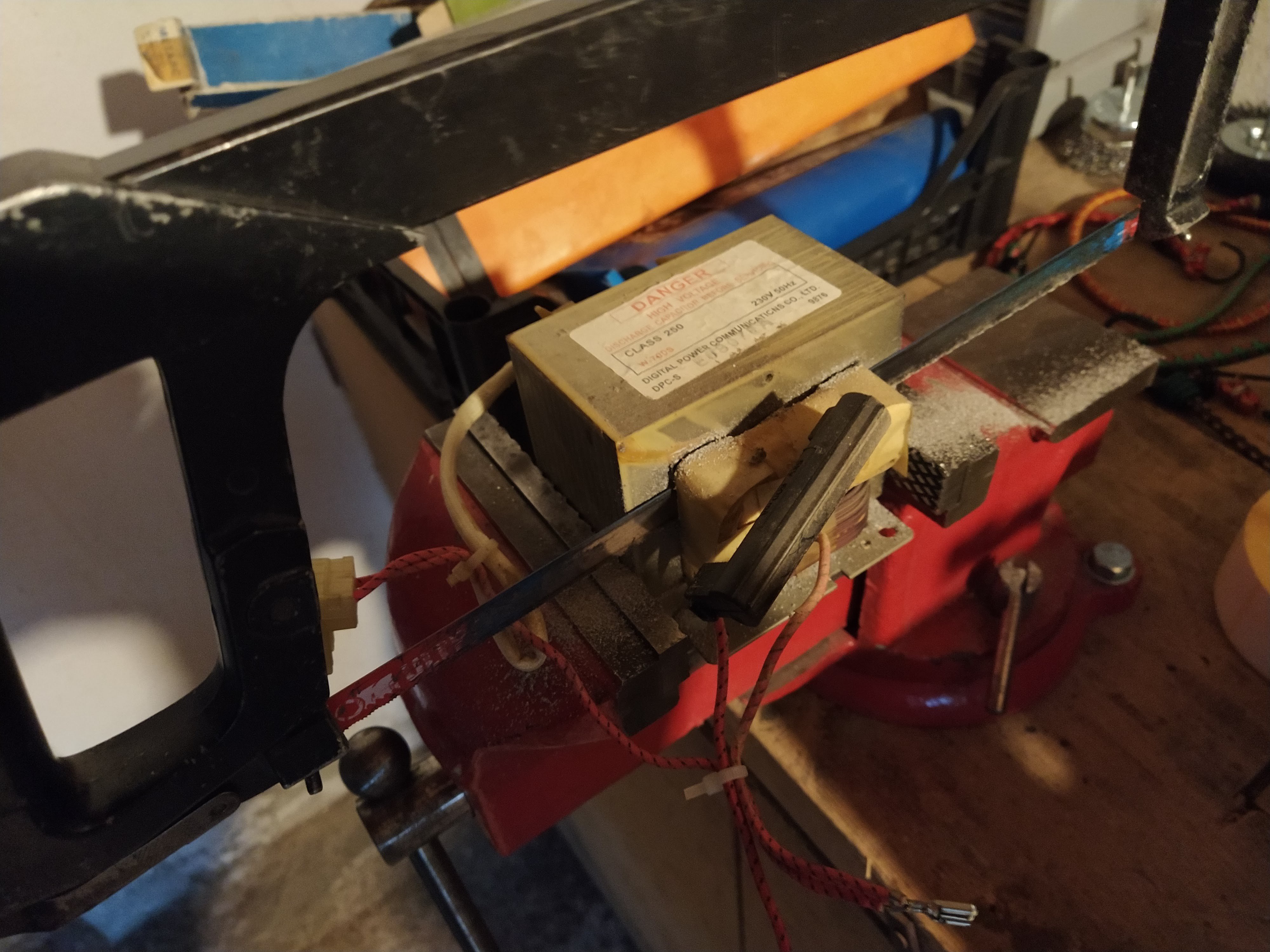
Seems like pure copper was too pricey for the secondary. I guess it's copper coated aluminium wire :

Then I got the rest of the secondary out with a hammer and chisel, pushing it out of the core. What a messy process.
I scrapped part of a 50 mm² wire from an old AC stick welder and wound 2 turns in place of the previous secondary. Such a cable can handle 151 A at constant load. It should be fine for brief 400-ish A peaks.
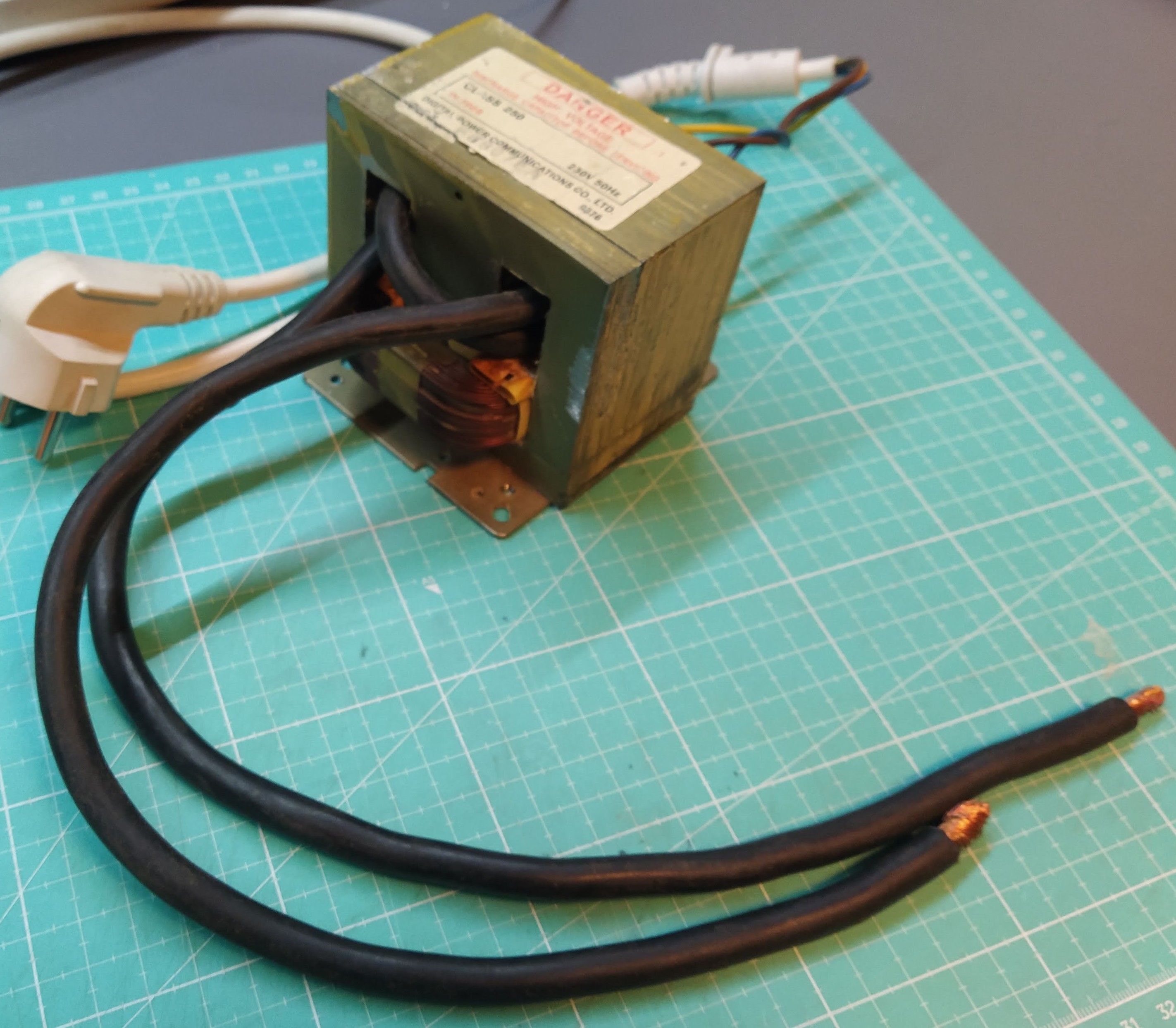
More to come...