I now know that aluminium is unquestionably not suitable for the clamp plate. Why? Well, I tightened Ch6, the black channel, and 3 metres worth of test prints later, I had this superblob from Ch7, the copper channel:
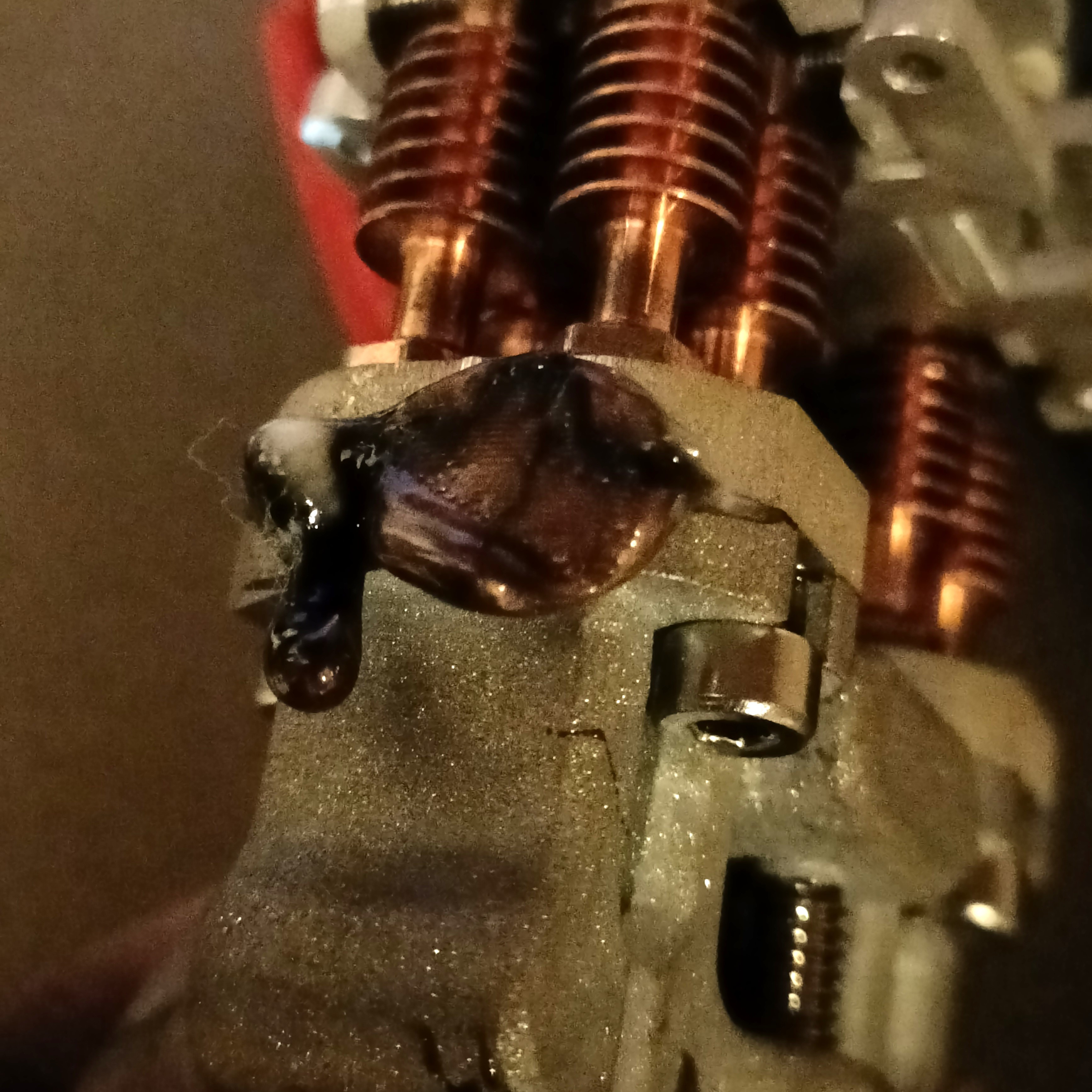
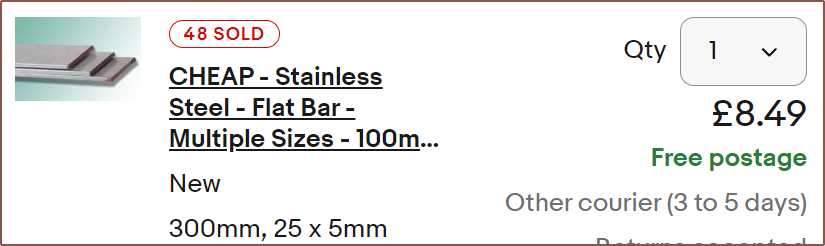
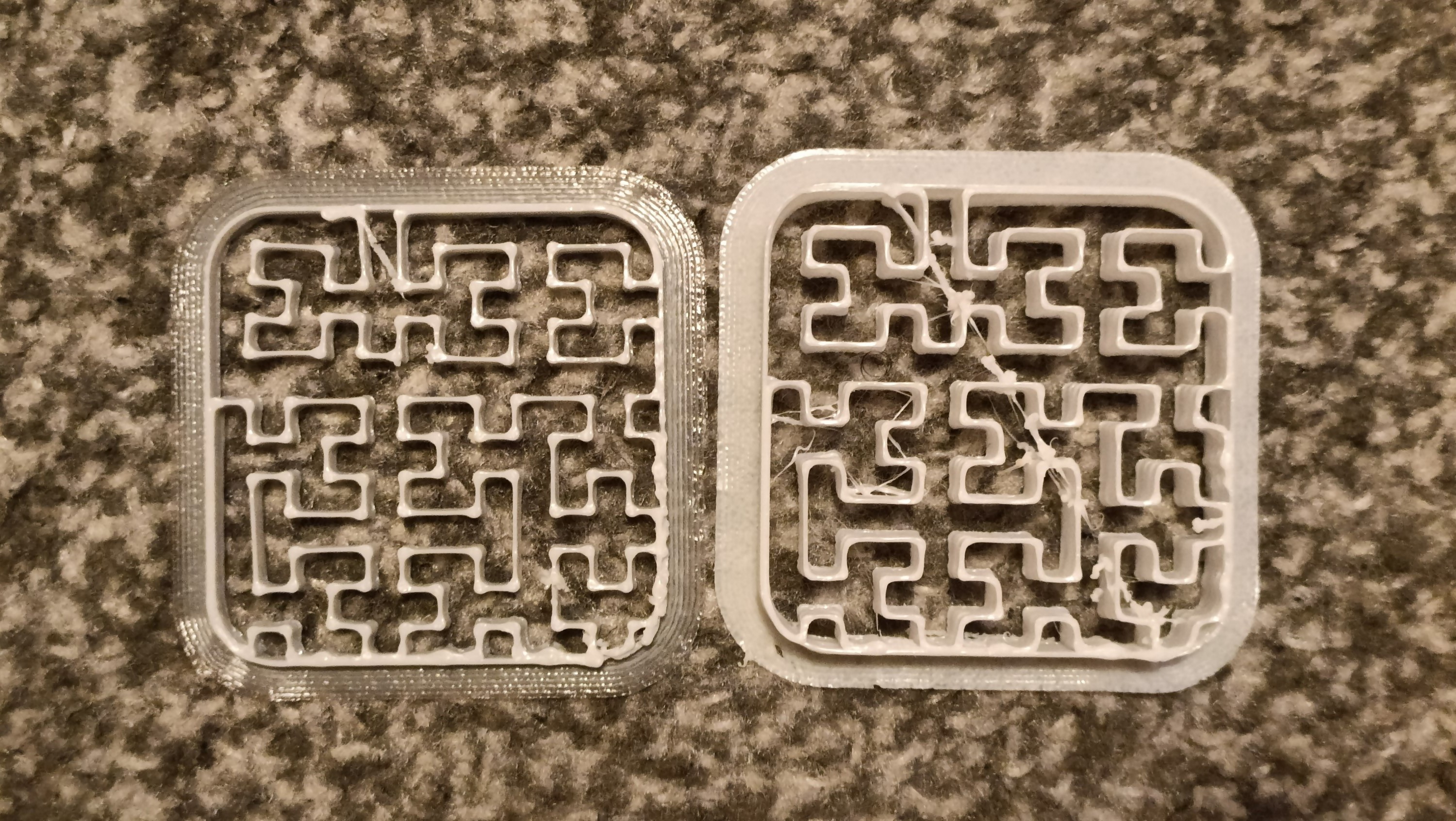
I still need to calibrate M592, since my walls at this speed are 0.48 when they should be 0.68mm. Part of the 30% loss of filament could be attributed to leaks but it's unlikely.
I'd also like to mention that Ch3 clogged when I tried 36mm3/s feedrate, but unblocking was as simple as removing the part cooling fan, allowing 20 seconds for the heatbreak to heat up in the time it took me to send the command to extrude through the channel at 1mm/s. This provides additional evidence that a heater-controlled "valve" will prevent accidental backflow of unloaded channels. It should also mitigate clogs caused by heat creep in unused channels. For consumer-level reliability, it should be paired with a filament sensor so that the valve can only be turned on if the channel is both used and loaded.
Moving on, I wanted to see what my cooling performance was before I tried to redesign the front cover of the coaxial hotend. I set a print for a 1 : 1 mix of White : Black, but accidentally did Black : Copper. In any case, I stopped the print when it was obvious that cooling was inadequate. The only 45-degree overhang that came out good was the one directly in line with the cooling duct:
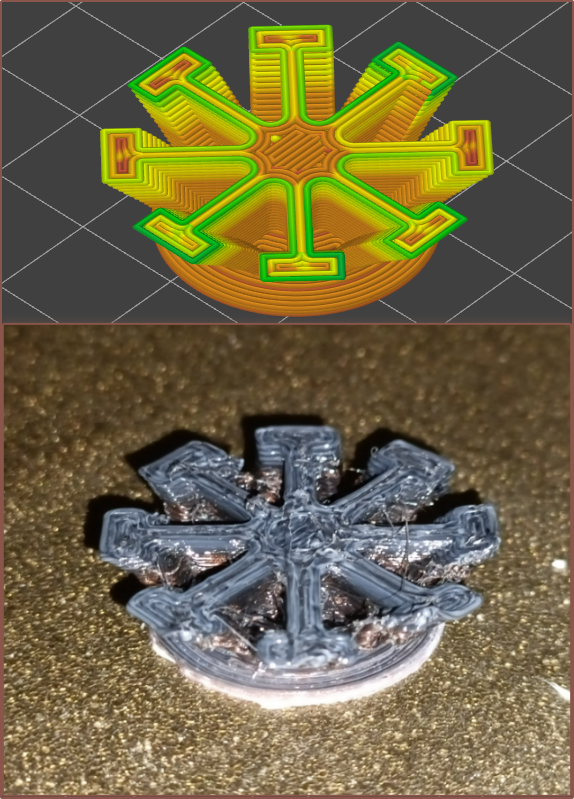
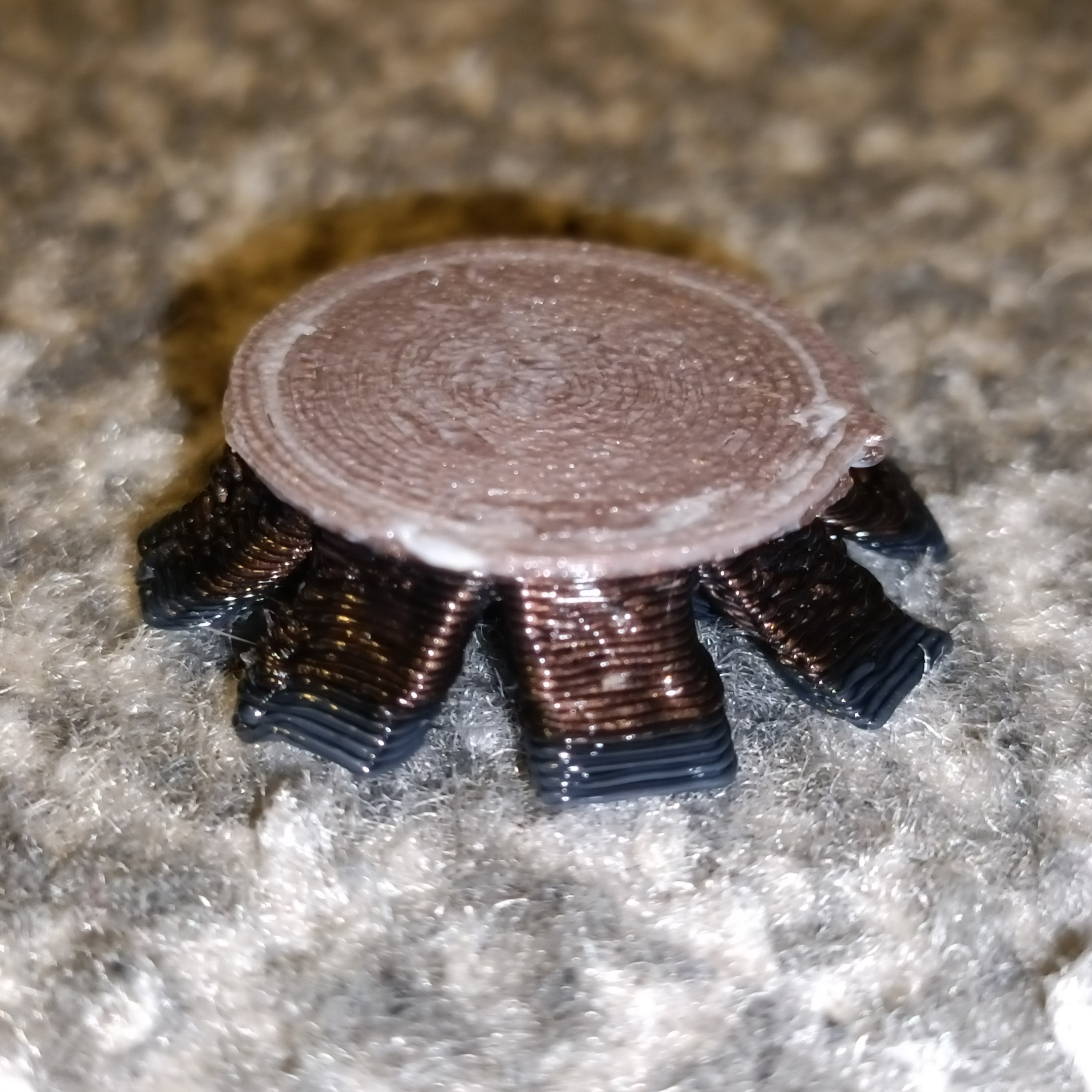
[Dec 30] I just remembered that I printed a temperature tower months ago, and considering the bridging difference between 236C and 218/224C, it's probably not helping that I was running this overhang test at 242C throughout. I'll just use 242C for bed adhesion and 224C for subsequent layers.
Discussions
Become a Hackaday.io Member
Create an account to leave a comment. Already have an account? Log In.